Following on from last month I did say that I would post a photo of my youngest daughter Jenny, my little Princess, marrying the love of her life Kieran, so here is one of myself as proud father walking her down the aisle on the big day:
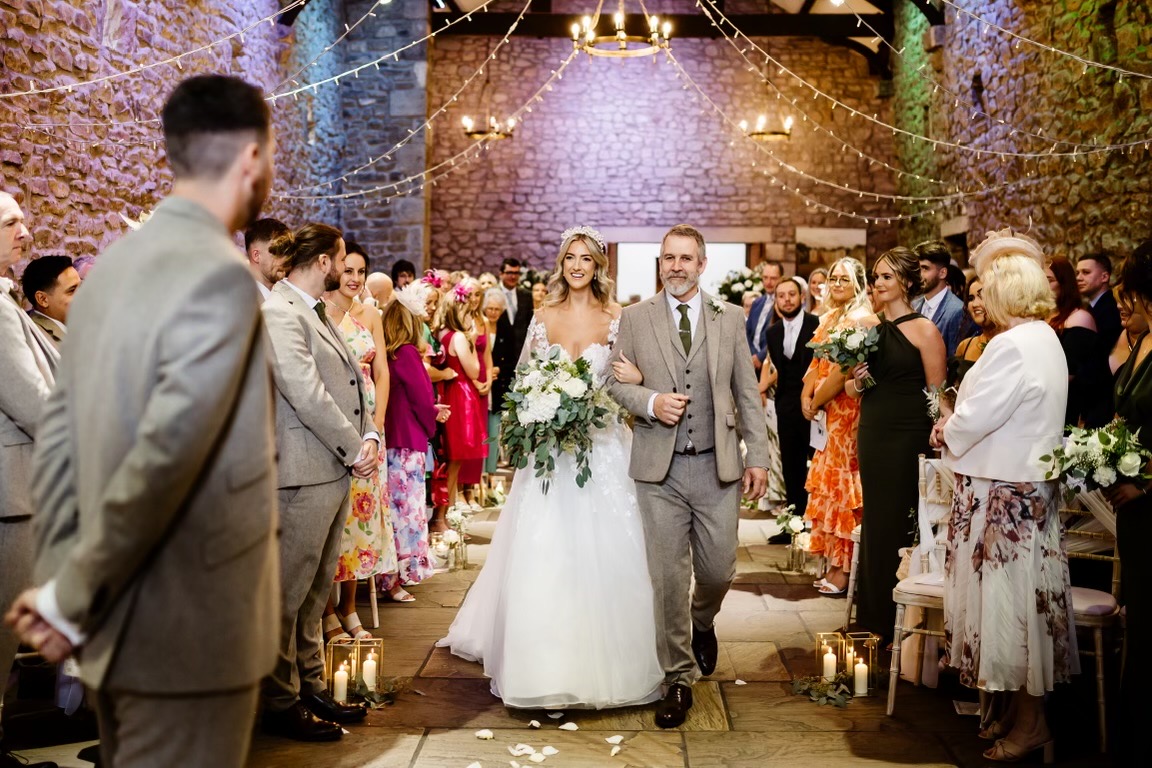
In the period following the wedding and at the time with the weather still being relatively warm and sunny, it was an ideal window of opportunity to get a few folk together in order to epoxy the inside of the hull of our jet hydroplane Longbow. The main purpose of this task being to both waterproof inside the hull and also to provide some degree of additional strength to the hull. The product of choice we would use for this critical task is the brilliant WEST SYSTEM EPOXY where their 105 Resin is mixed with their 207 Special Clear Hardener that does not turn cloudy or produce amine blush, all supplied by our great sponsor of the project, Wessex Resins & Adhesives Ltd.
As the workshop has sanding dust floating about in the air from the ongoing works on the boat I was mindful that this would settle and stick upon the epoxy as it cured if we tried to do the task in there. Accordingly it was better to pull the boat out onto the driveway taking her away from that issue. Then to blow all the dust off her and vacuum her out in the open air so we could then apply the epoxy there, which I knew would be a little bit more tricky than at first might appear.
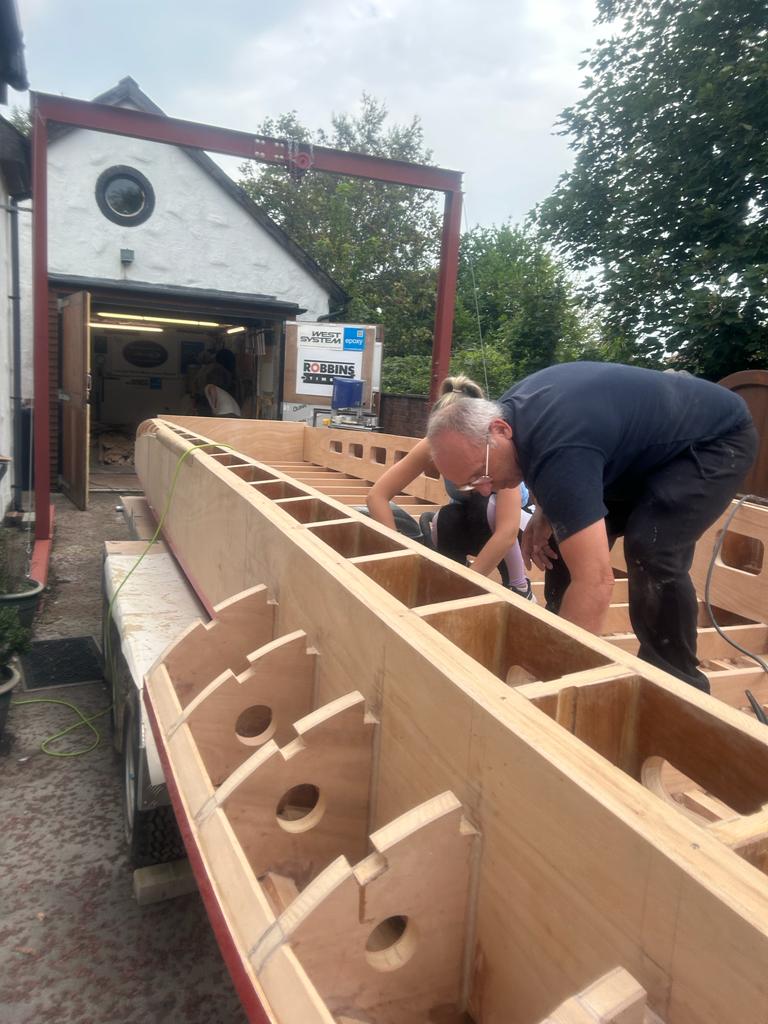
In simple terms we needed to apply at least three coats of the epoxy inside the hull but to do that in a process where we applied the following coats before the earlier coats had fully cured, so there would be a chemical bond between the coats of epoxy, with at the very least all of it to be done on the same day.
Of note I am aware that some people when undertaking this task will thin the first coat of epoxy down using a solvent but this is not recommended by the manufacturer for the following reasons. Thinned epoxy has less resistance to moisture penetration making the hull more prone to decay. Also thinned epoxy soaking into the wood results in the outer layer of solvent flashing off upon the surface but trapping some of the solvent within the timber thereby having an adverse effect upon the cross linking of the epoxy matrix and also an adverse effect upon the epoxy bonding to the wood itself. As a result there is less strength with thinned epoxy than you would otherwise have using pure epoxy in accordance with the manufacturer’s instructions.
So with all of that in mind we had Gill and Steve dispensing the resin and hardener to the correct ratios followed by stirring them together for at least two minutes to ensure a thorough mix.
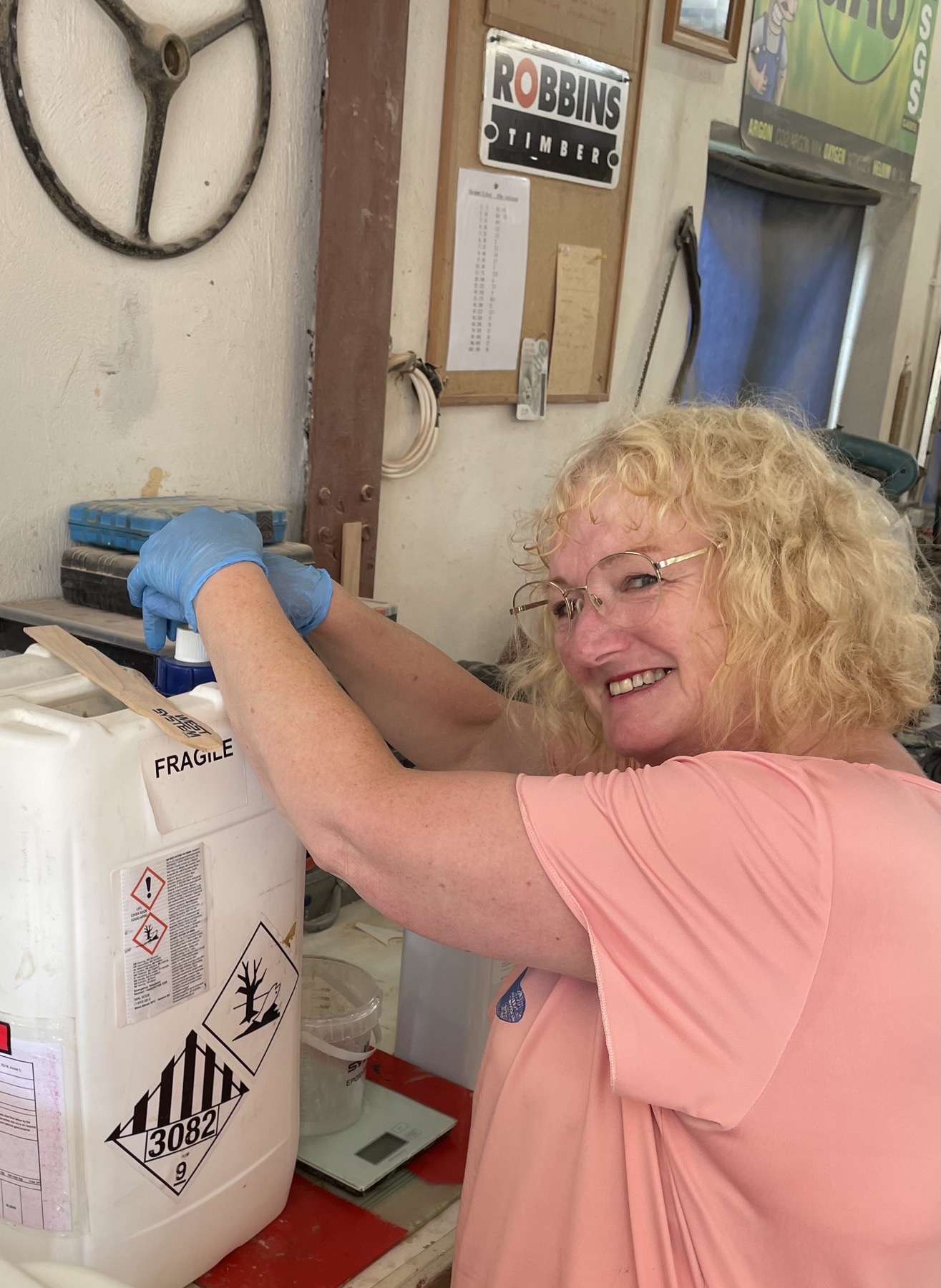
Once ready they poured the mixture into several paint trays for the rest of us to apply the epoxy inside the hull. The trays spread the surface area of the mixture extending its usable working time compared to it quickly cooking when left as a large volume in the mixing pot. A good tip is to line the paint trays with foil so you can replace that with new with each refill of epoxy and not have part cured epoxy in the tray as the day rolls along. Disposable gloves, paint brushes, spreaders and rollers are also the order of the day for the task in hand.
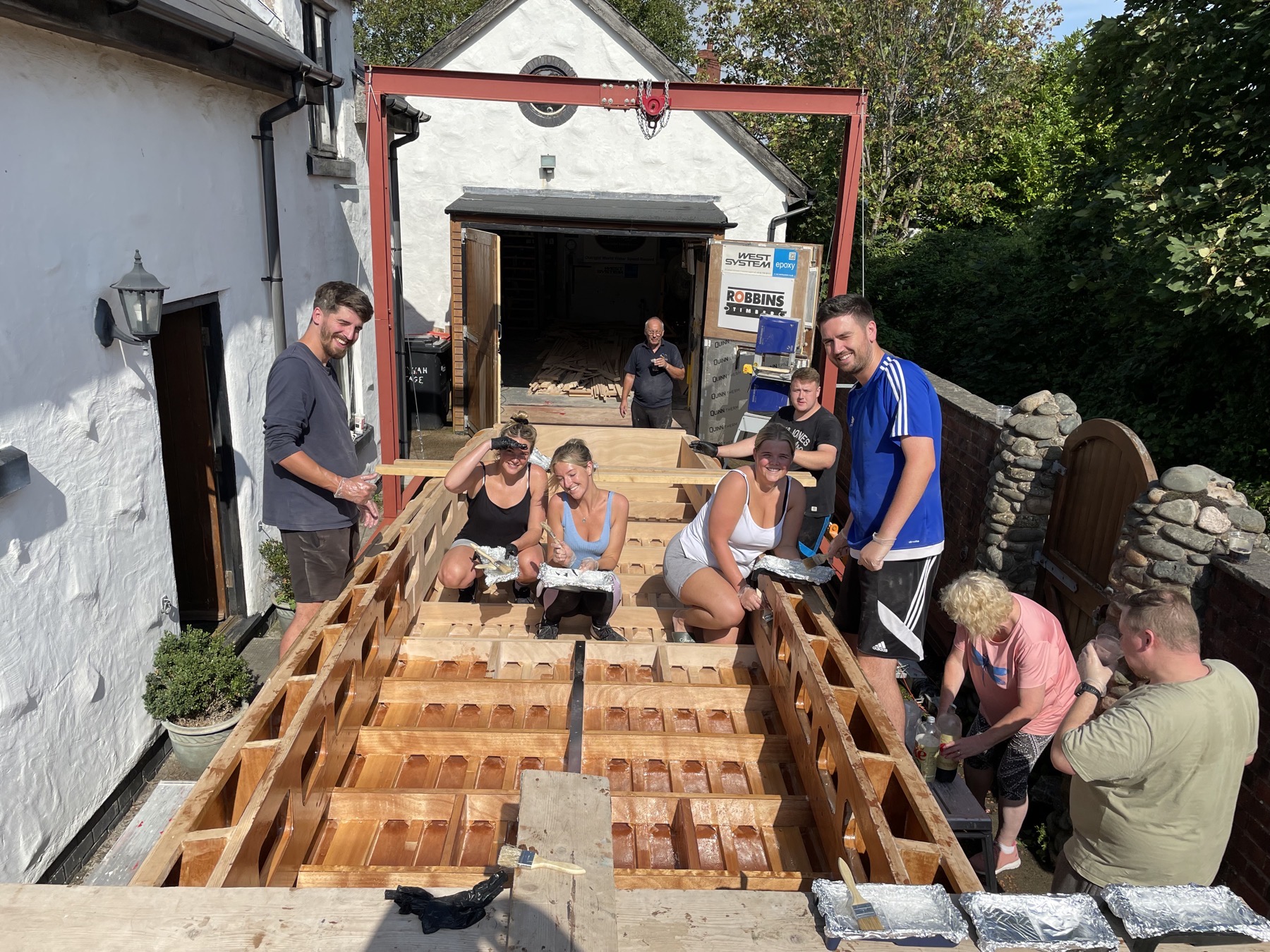
Inside the hull of Longbow is a complex series of battens, frames, stringers, semi closed voids, drainage channels, etc, so some areas are awkward to reach and whilst it is easy to see where you have been with the first coat of epoxy, the following coats all being clear, result in you having to have a good memory of where you have and have not applied further coats. So being methodical, with each person having their own area to do as they worked along the boat applying the epoxy coats was a good system of ensuring proper application.
Scaffold planks and a ladder section with crawl boards allowed folk to apply the epoxy in the middle of the hull that would have been difficult to reach from the sides trying to lean over.
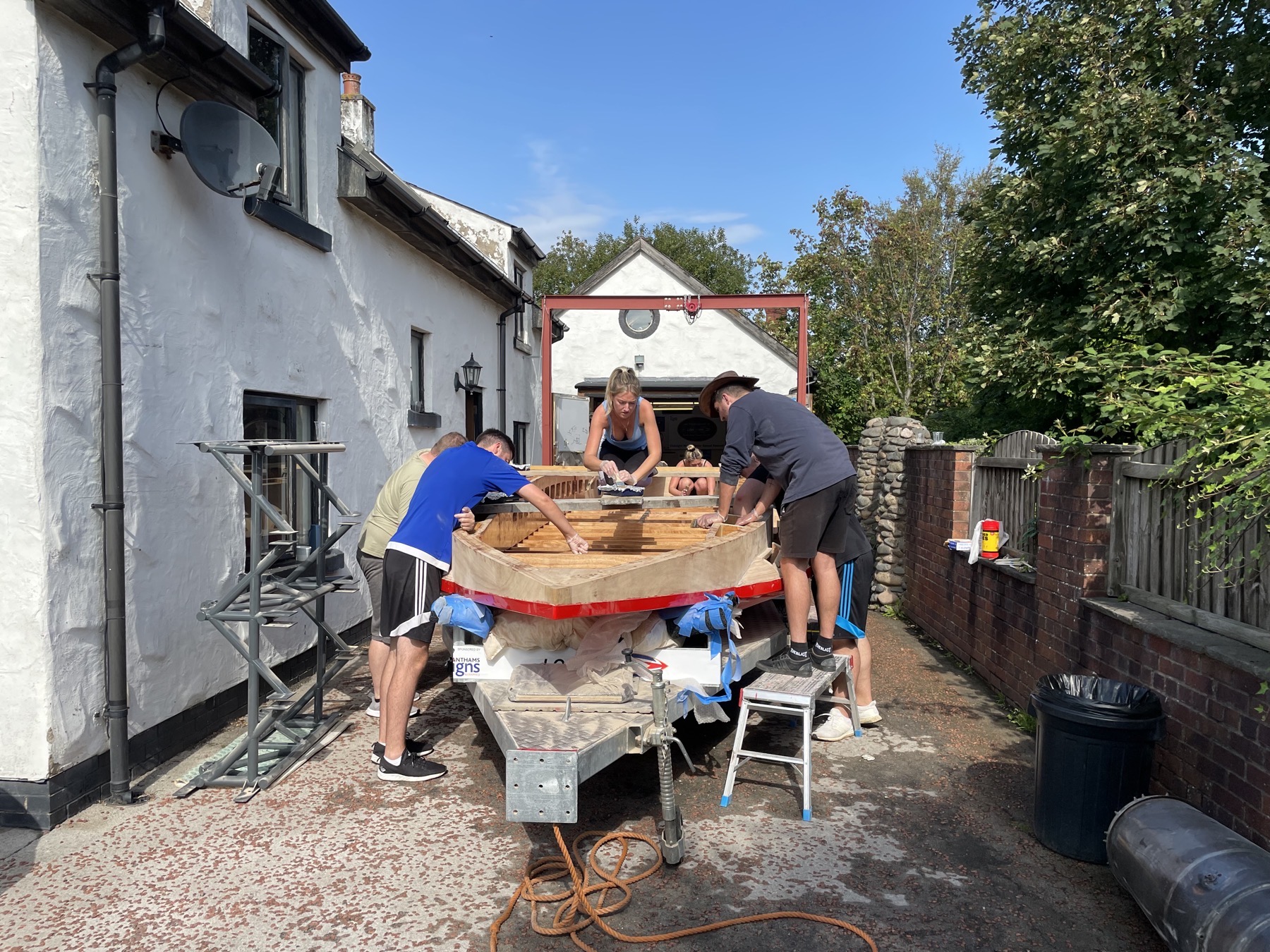
There was a little bit of out-gassing from the wood during the process which is where the air within the timber expands and tries to escape from the surface of the wood forming bubbles beneath the epoxy as it cures. The reason for this being as the epoxy cures it is an exothermic chemical reaction, that is to say it gives off heat and added to that heat was us doing the task outside on such a glorious hot sunny day. However the out-gassing from the wood was easily addressed by the sun moving off the driveway later in the day and returning the hull into the cooler workshop upon completion of the works.
Everybody worked really well together to get the job done and we had just the right amount of friends and family on the task to make it a fun event with a big relief on my part that it all went so very well along with well deserved drinks all round at the finish. A big thank you to Hamish Cook at Wessex Resins & Adhesives for his great advice upon how to tackle the job and to Steve, Jenny, Kieran, Robert, Caitlyn, David, Ellie, Gary, Tom and my good lady Gill for all coming together to help out on the day.
With woodwork still ongoing to the rear of the sponsons we sheeted over the top of the hull to keep the majority of the sanding dust out of there.
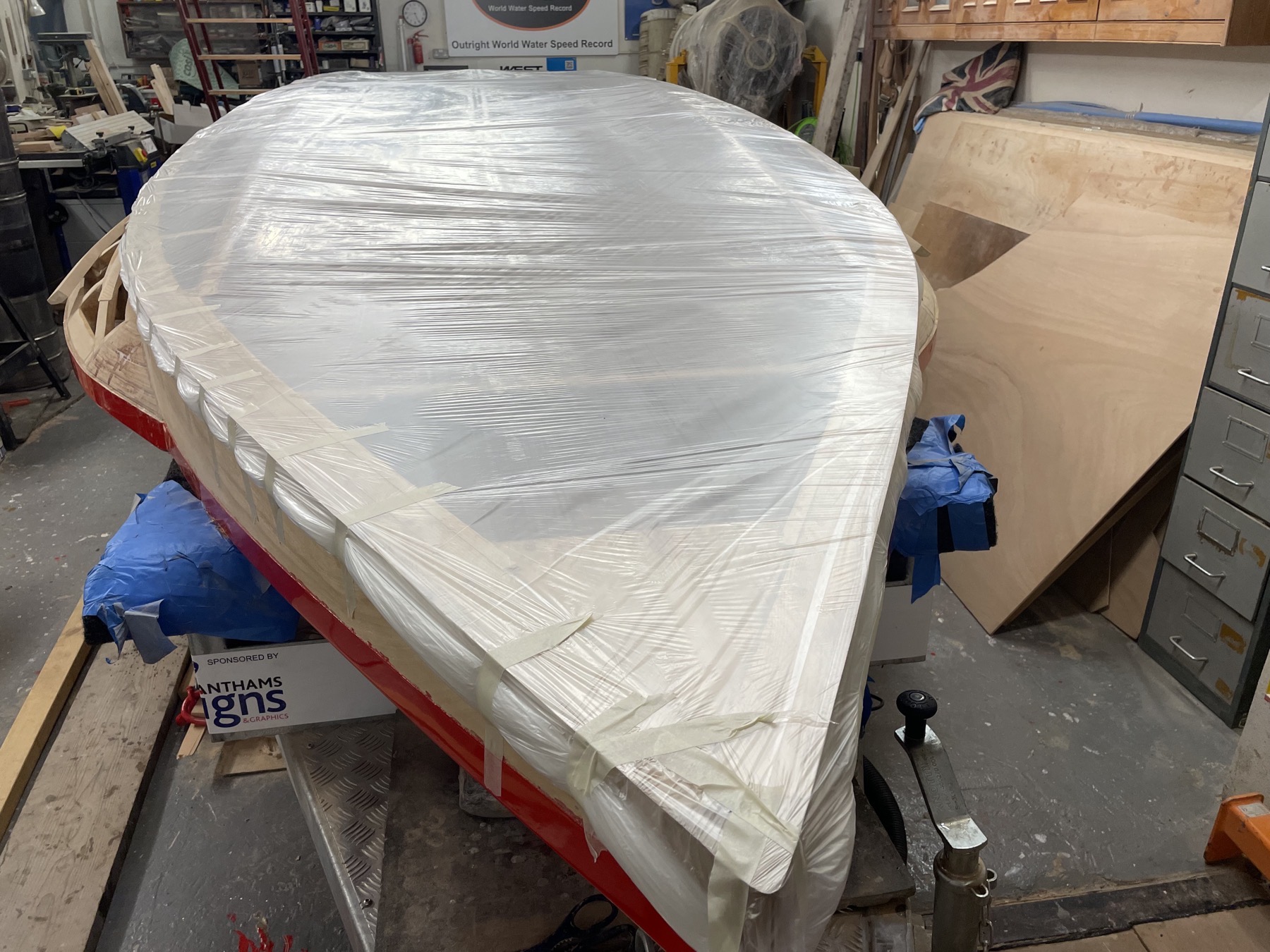
After leaving the epoxy to fully cure, a couple of days later my two boys Tom and Robert were roped into helping me lift the jet engine cradle back into the hull.
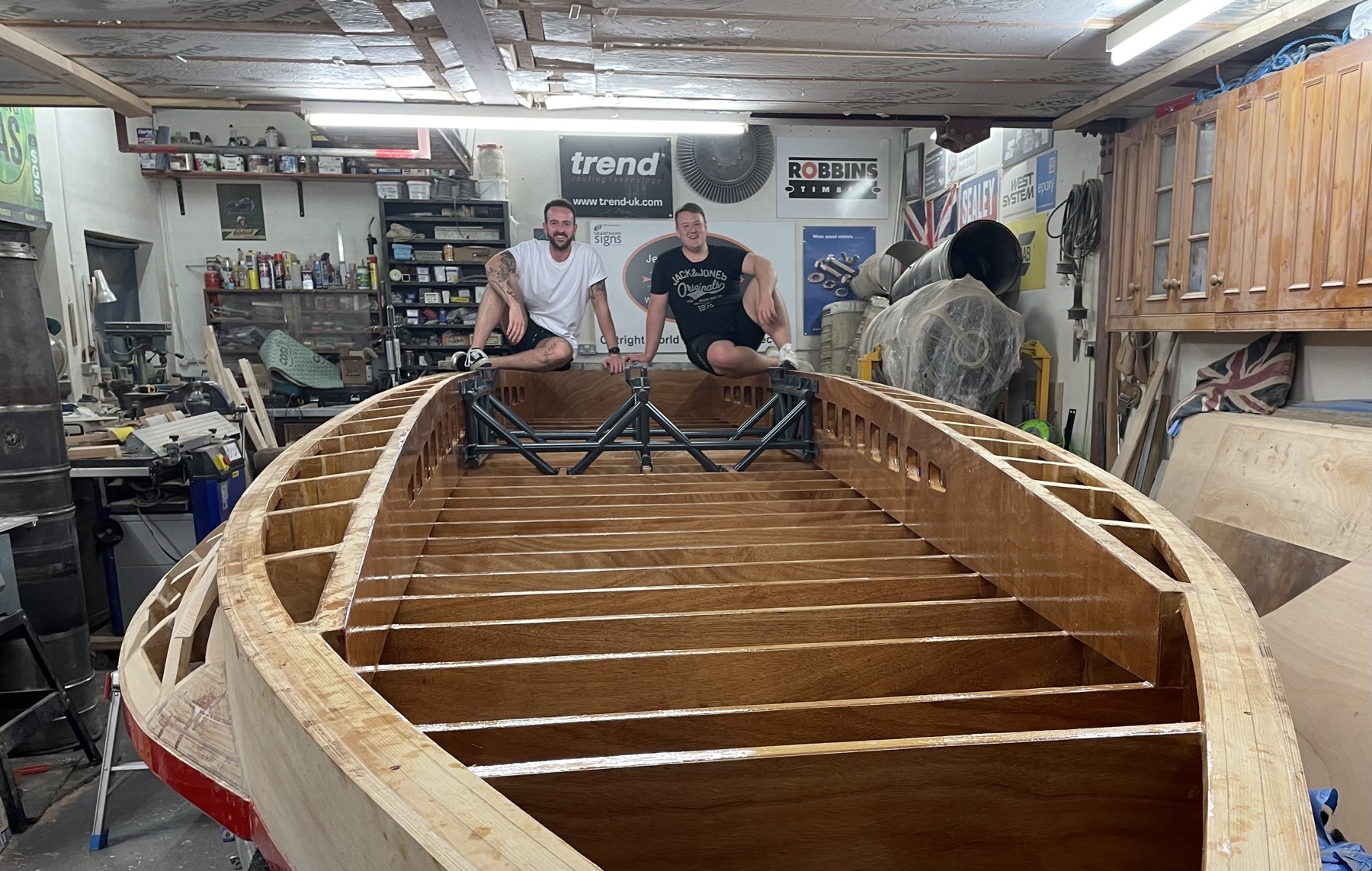
Back with working upon the rear of the sponsons using the marine wood kindly supplied by our sponsor Robbins Timber, having got much of the shaping done to one of the rear sponsons upon one side of the hull, I could then mirror all of that to do the rear sponson on the other side of the hull. As I mentioned in last month’s update there is a lot of work in this detail that perhaps is not so readily apparent from the photos. However this little collection of what I can only describe as being like Jenga blocks all interlocks together quite nicely so it was quite satisfying to spend the time and effort to get the detail to work. Steve Buckle of our great sponsor Sealey Tools very kindly kept us well stocked up with their excellent 50mm sanding pads and disks for this task:
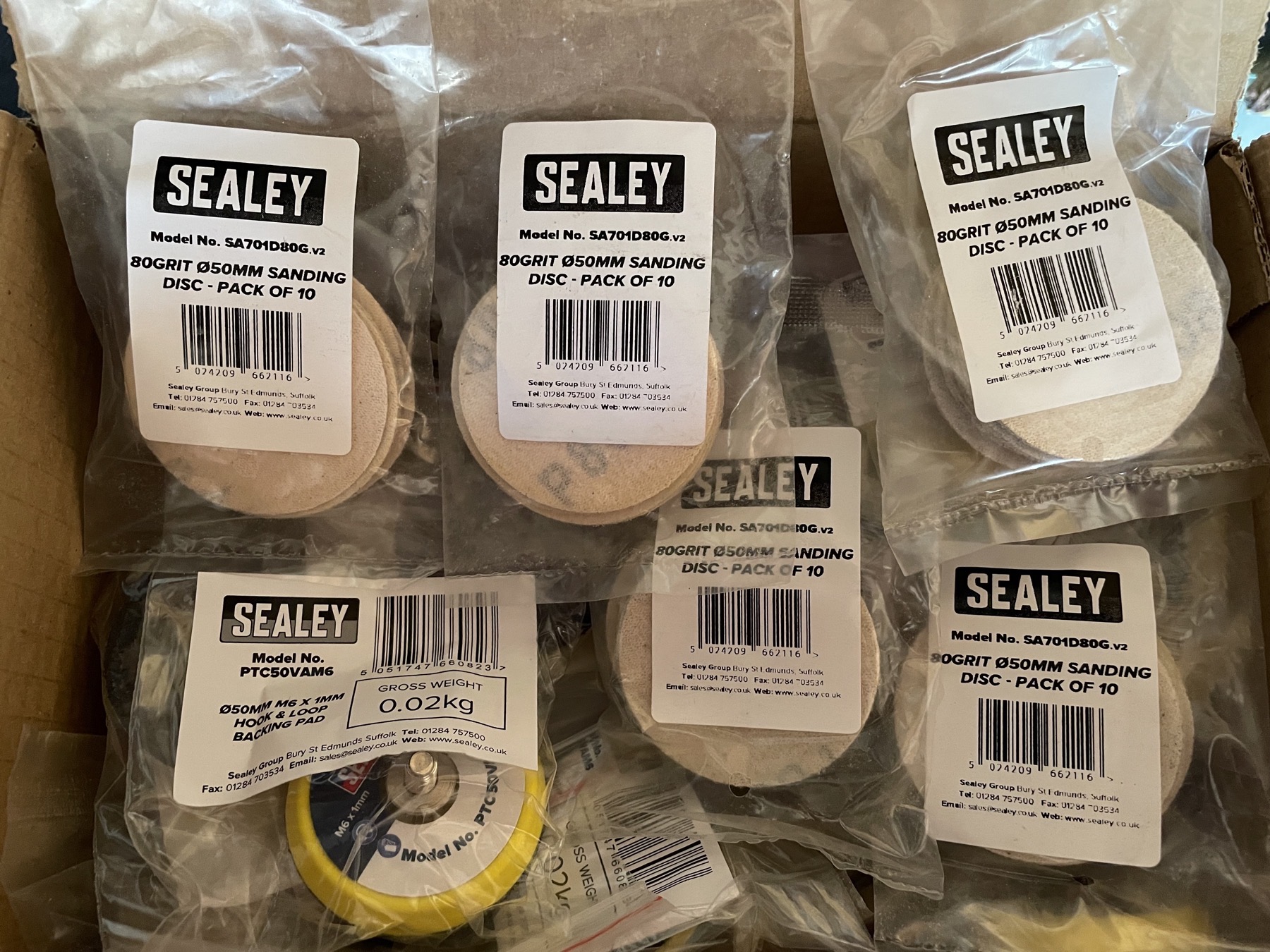
A little bit more sanding and shaping over the following days to of the rear sponsons should see us to a point where we are ready to apply the WEST SYSTEM EPOXY that will see all of this structure permanently fixed and bonded into place.
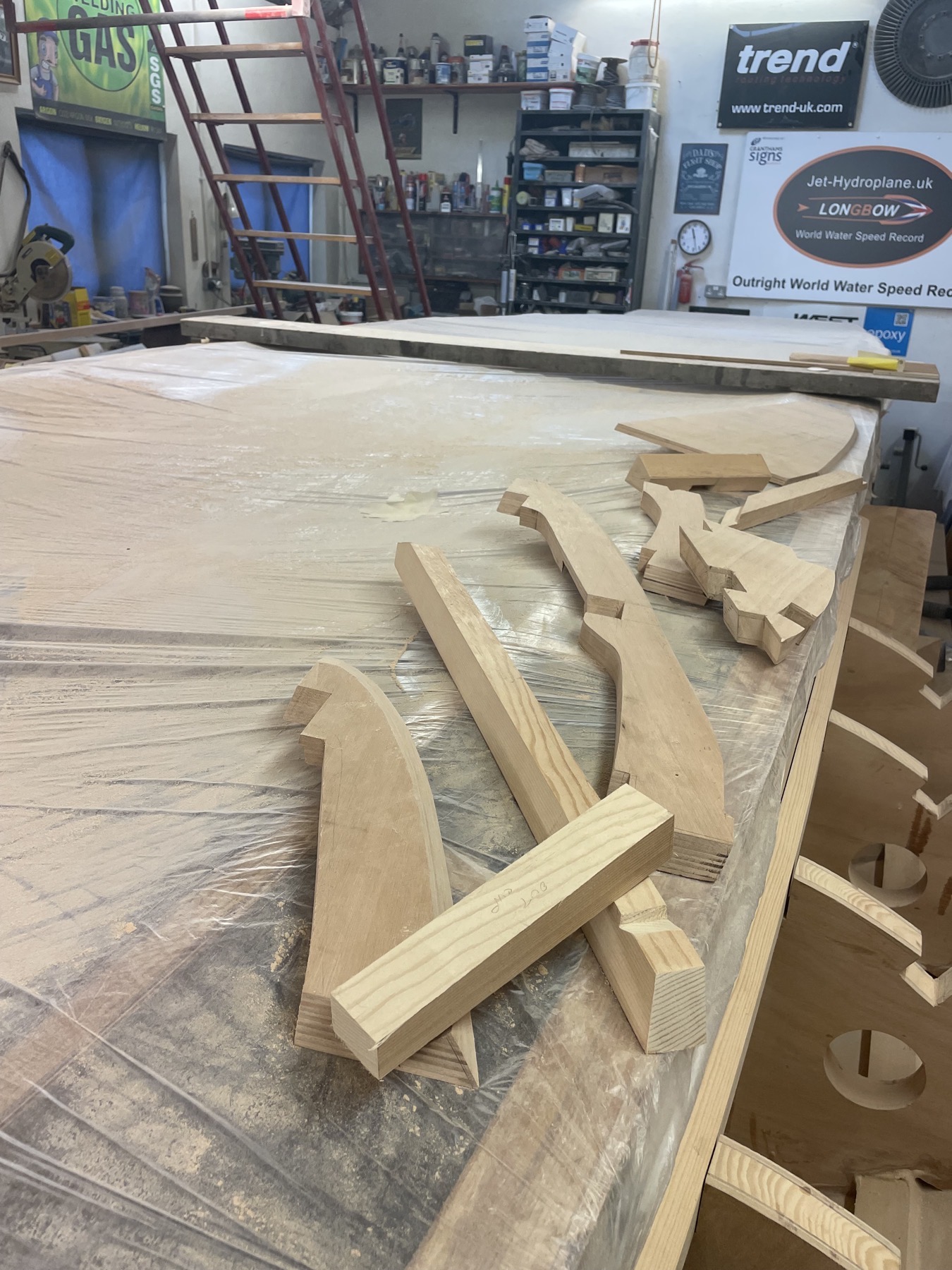
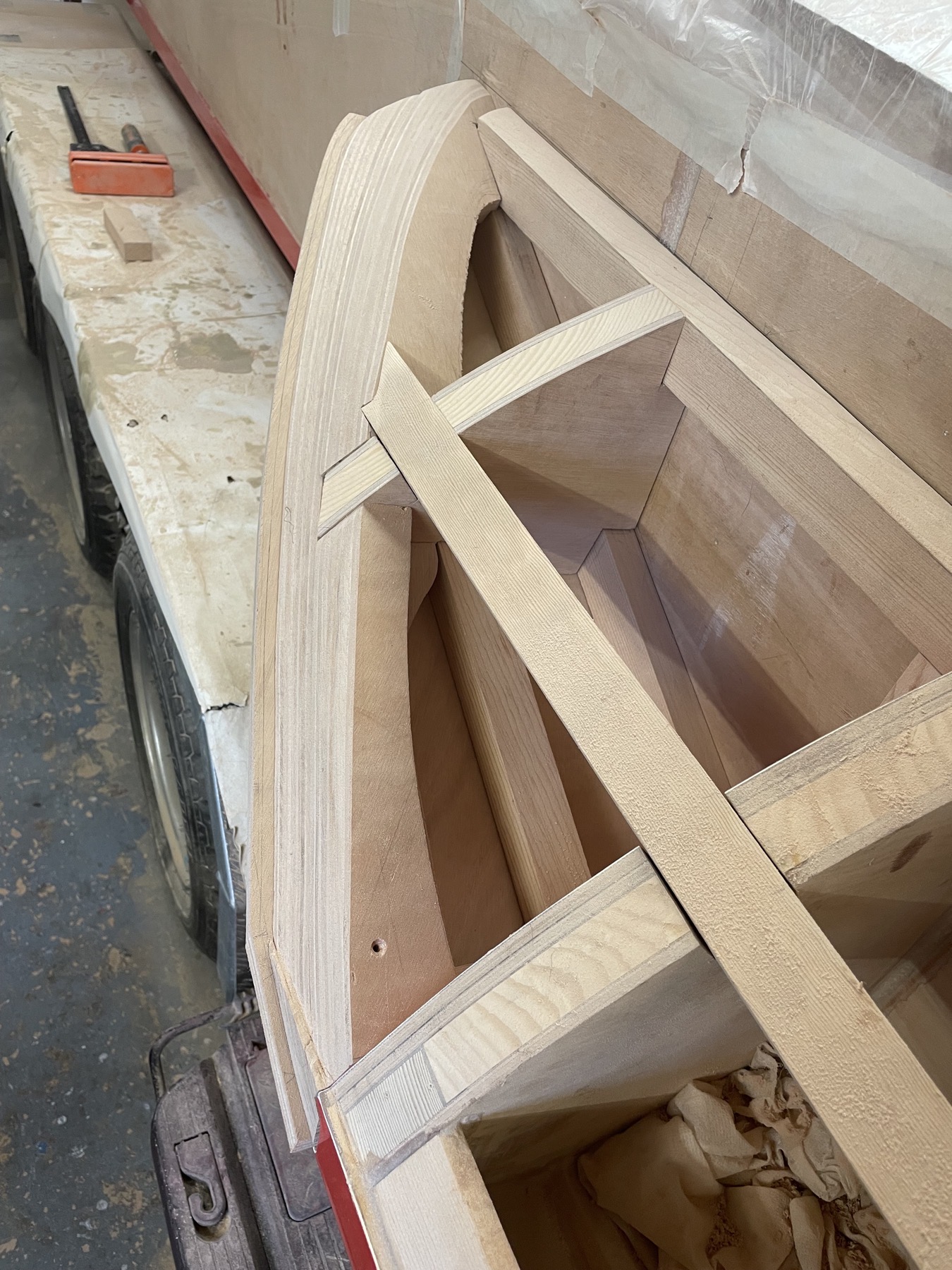
Moving on from wood to metalwork my great pal and master craftsman Steve Charlesworth last time he had visited us, had eyed up the alloy intake spinners, sometimes referred to as a ‘bullet’ shaped nose cones that will be bolted to the front centre of each of the twin jet engines that will power Longbow. The function of the spinner to the jet engine (that you will appreciate are normally for use within aircraft) is to reduce any unfortunate bird impact damage to the engines, reduce ice build up, along with assisting with streamlining airflow into the front of the engine.
In our case the version of Viper jet engine that we were using from the military BAC Strikemaster aircraft was not designed to have a spinner on the front of that engine when fitted as a single engine for that aeroplane, being located against a bulkhead in the airframe directly behind the cockpit. However in a different version of the Viper jet engine there are spinners bolted to the front of those engines for example upon the twin jet engines fixed via pylons to the rear each side of the HD / HS / British Aerospace 125 aircraft.
With us using twin Viper jet engines in Longbow we ideally wanted spinners to the front of both jet engines and fortunately for us the engine manufacturer has provided fixing points for spinners to be fitted to the front of our version of the Viper engines when required.
However sourcing the correct spinners was no easy task as the engines are no longer in production, people who have spinners attached to their Viper engines usually want to keep them with the engine and it’s not like you can pop down to Halfords and get another over the counter. Anyway we did eventually manage to source three Viper spinners, one from the USA and two in the UK. The one we got from the USA was in reasonable condition but with the other two there was one with a dint in the nose whilst the other had some degree of surface corrosion.
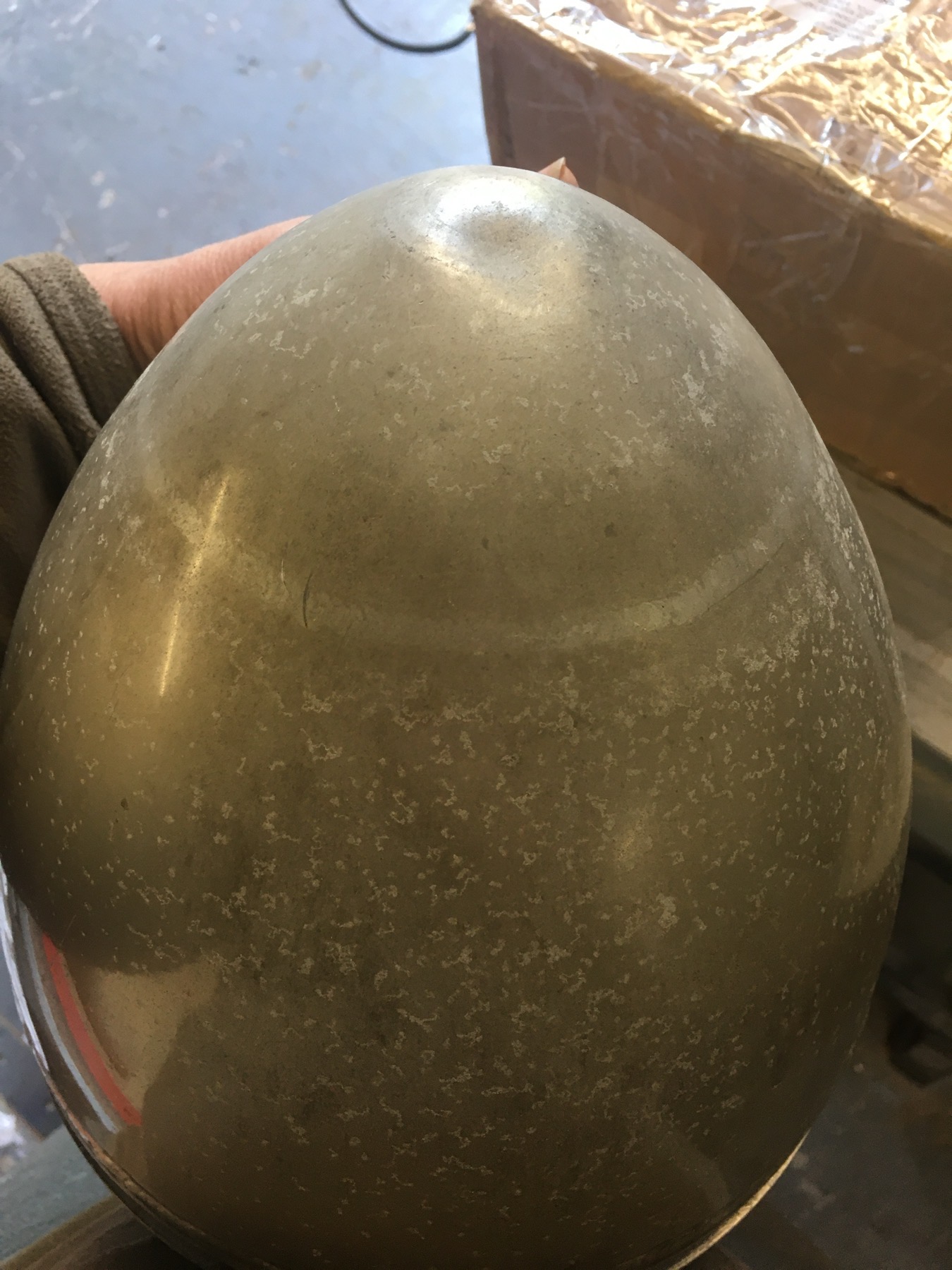
All three spinners are constructed in such a way that there is an inner and outer layer of alloy to the bullet shape with a small void between the layers, as well as a welded base plate and bulkheads along their length that prevents access internally.
The spinner with surface corrosion we decided to use as a spare with Steve on a mission to make good the corroded areas with his superb welding skills. However before he could do that we needed to know what type of aluminium alloy we were dealing with in order to marry the correct replacement sheet material and TIG rods to the defective areas.
Steve cut out a section of the spinner and sent it off to Paul Critchley, Technical Manager for Workshops & Engineering, at University of Central Lancashire, who very kindly had their analytical suite examine the material.
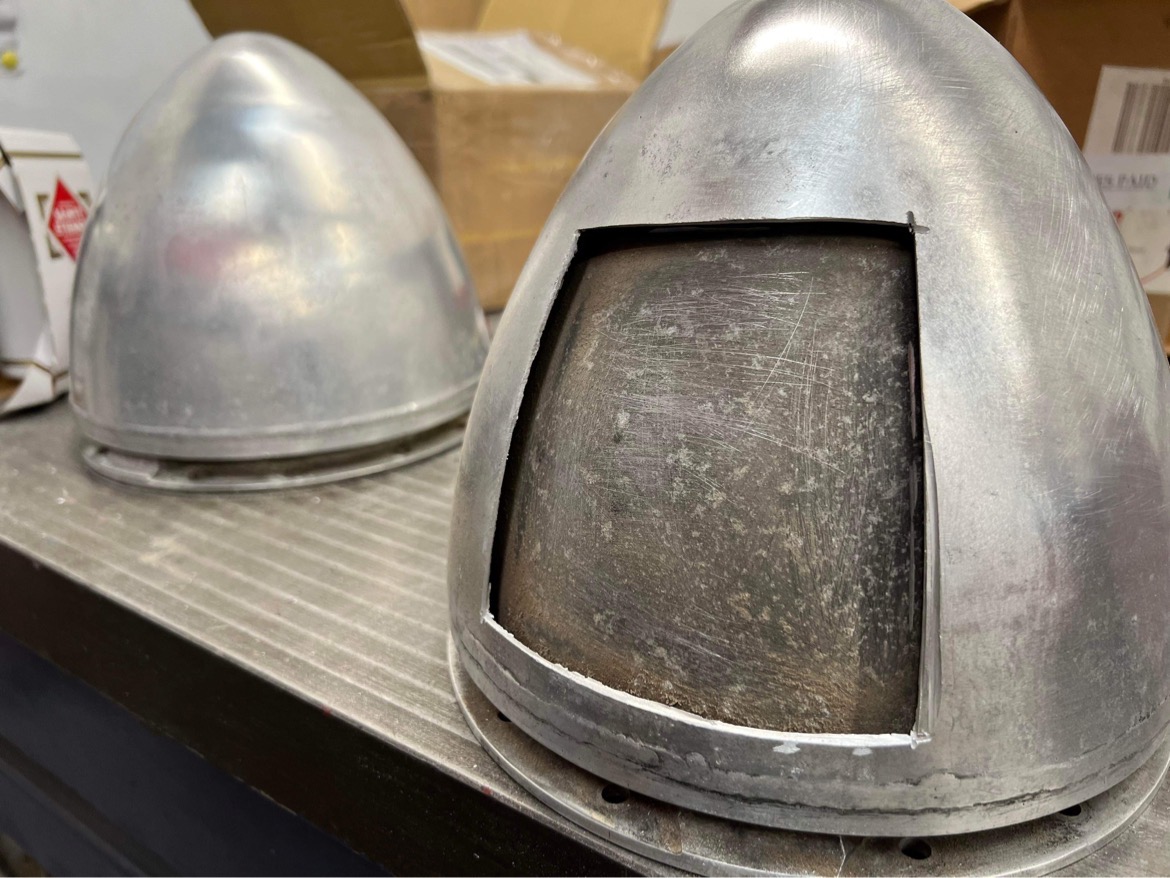
The results were the material contains only 70% aluminium with other elements such as but not limited to magnesium being present but noticeably no manganese or chromium. Hopefully from this information we will be able to source suitable TIG rods and replacement material.
Rather peculiarly for some reason two of the spinners had their outer bullet shape fabricated from several pieces of curved metal welded together whilst the other one appears to have been ‘spun’ on a lathe in one piece. If you have never seen metal spinning on a lathe before, the following video gives an example of the mesmerising process:
Of the two spinners that we are going to use upon the jet engines within Longbow, Steve skilfully worked his magic to remove the dint in the nose of one of them – don’t ask me how he managed to do that without getting inside it the clever devil. He then treated both spinners to some tender loving care with him polishing them up. The results compared to how they originally looked, I think you will agree, are to say the least spectacular and I cannot wait to bolt them into place on each of the jet engines once fitted in the boat.
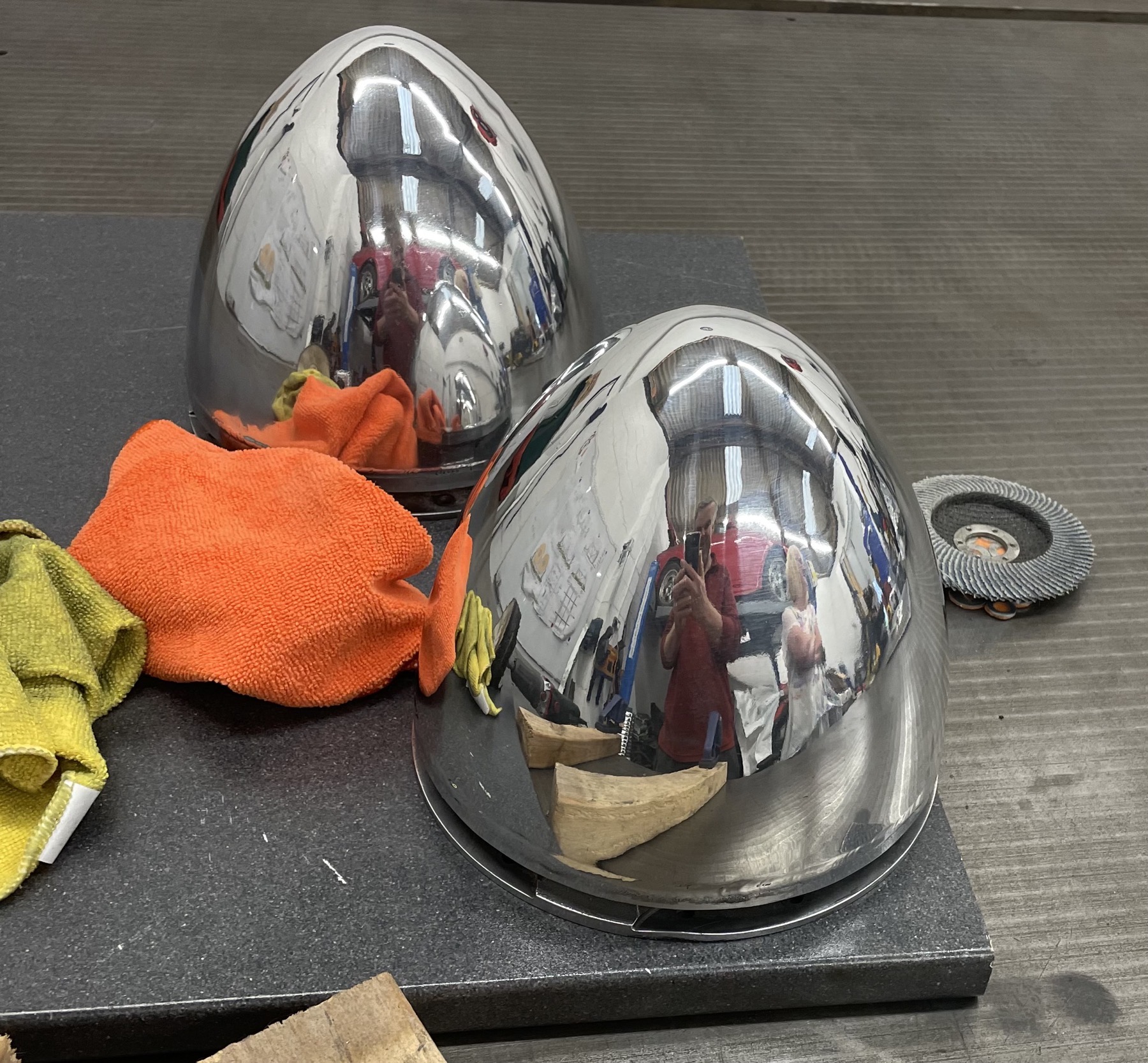
Whilst all of that was going on our driver for Longbow Flight Lieutenant David-John (DJ) Gibbs of the RAF was entertaining the vast crowds who had come to his home town of Southport to see the Airshow and in particular DJ doing his amazing acrobatic display upon behalf of the RAF. Of note DJ has logged over 6,000 hours of piloting 50 different types of aircraft and is Officer Commanding Tutor Standards Flight, where he and his team ensure that all Tutor Qualified Flying Instructors are teaching at the expected standards. The following photo credit to Wartog shows DJ in action at the airshow:
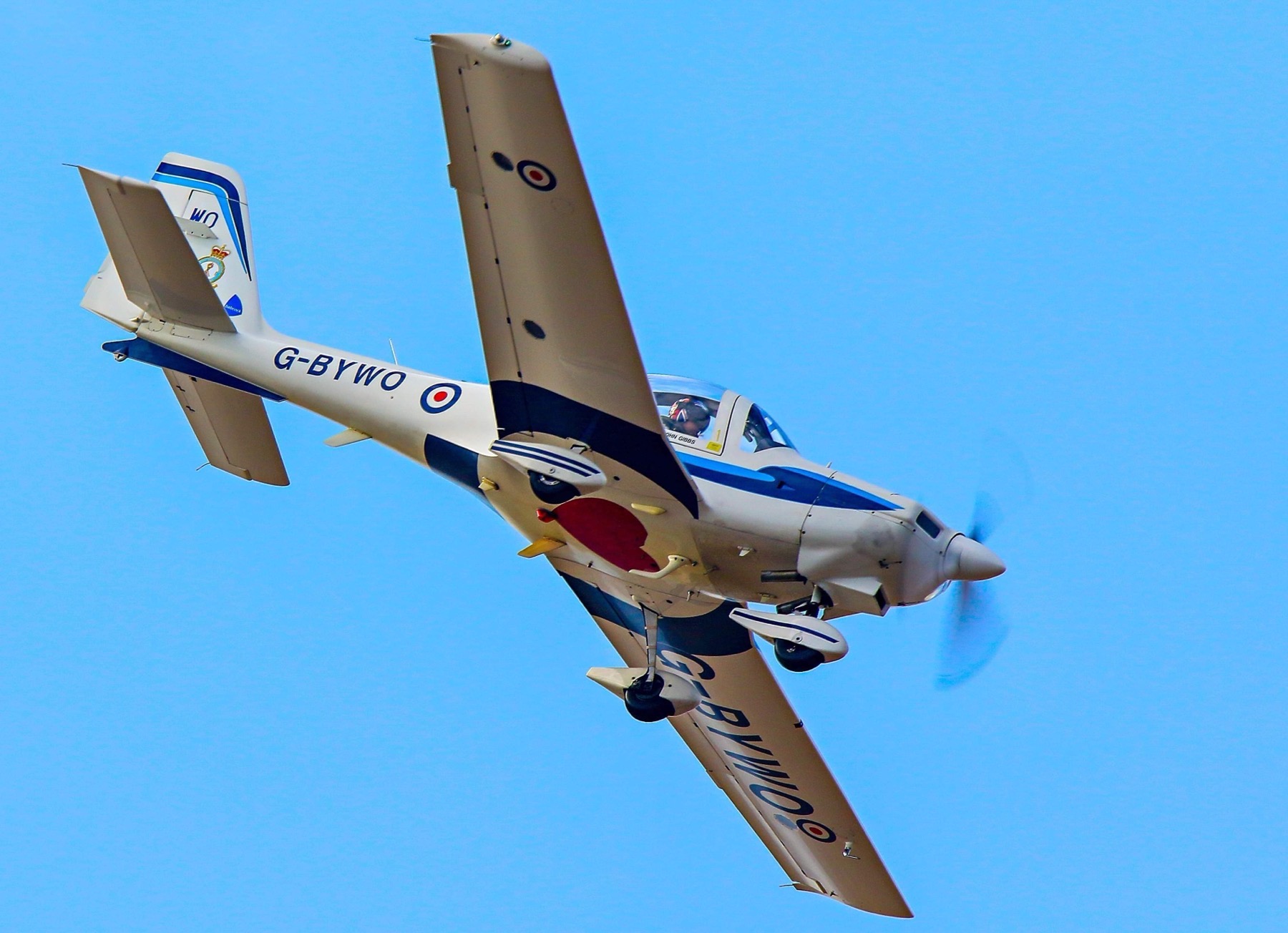
Closing this month’s blog is an update upon our good friend Dave Warby’s latest development runs of his jet hydroplane Spirit of Australia 2 at Blowering Dam, NSW, Australia; as he prepares to make an attempt upon the Outright World Water Speed Record – fastest boat in the world – set by his late father Ken Warby MBE at 317mph in 1978.
Dave and his team set up camp for the weekend at the Dam and despite rain and strong winds they managed to get out onto the water during the Saturday for literally some ‘shake down’ runs with ‘white horses’ of waves proving what a strong hull SOA2 is as she rode over the surf at an incredible speed for the terrible conditions of the day at around 185mph. The next day brought somewhat better weather but still far from ideal conditions. Dave and his team made the boat ready and everyone got to their stations as crowds watched from the shoreline, the Orpheus 803 jet engine that powers the craft bursting into life for an incredible sight and sound experience.
Team cameraman Jeff Barnett who provides the brilliant photographs herein tells me that he is fortunate to see the boat running from all angles especially from the air as he flies overhead during the runs and he can tell Dave is getting quicker by how fast SOA2 now leaves the plane behind. On his best run of the day despite the less than ideal weather conditions Dave managed an amazing 265mph and says he could not be more happy with how the boat is now set up and handling.
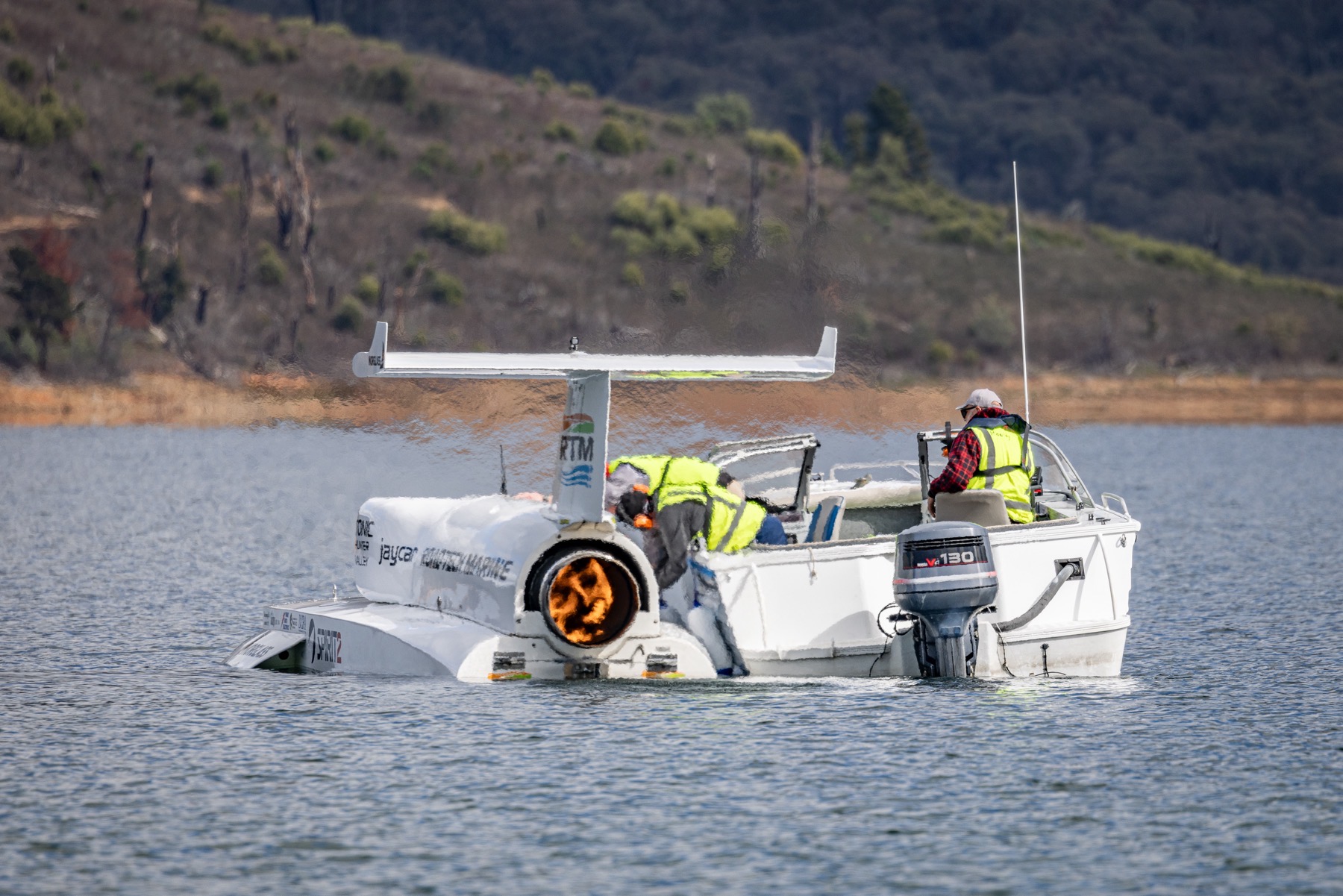
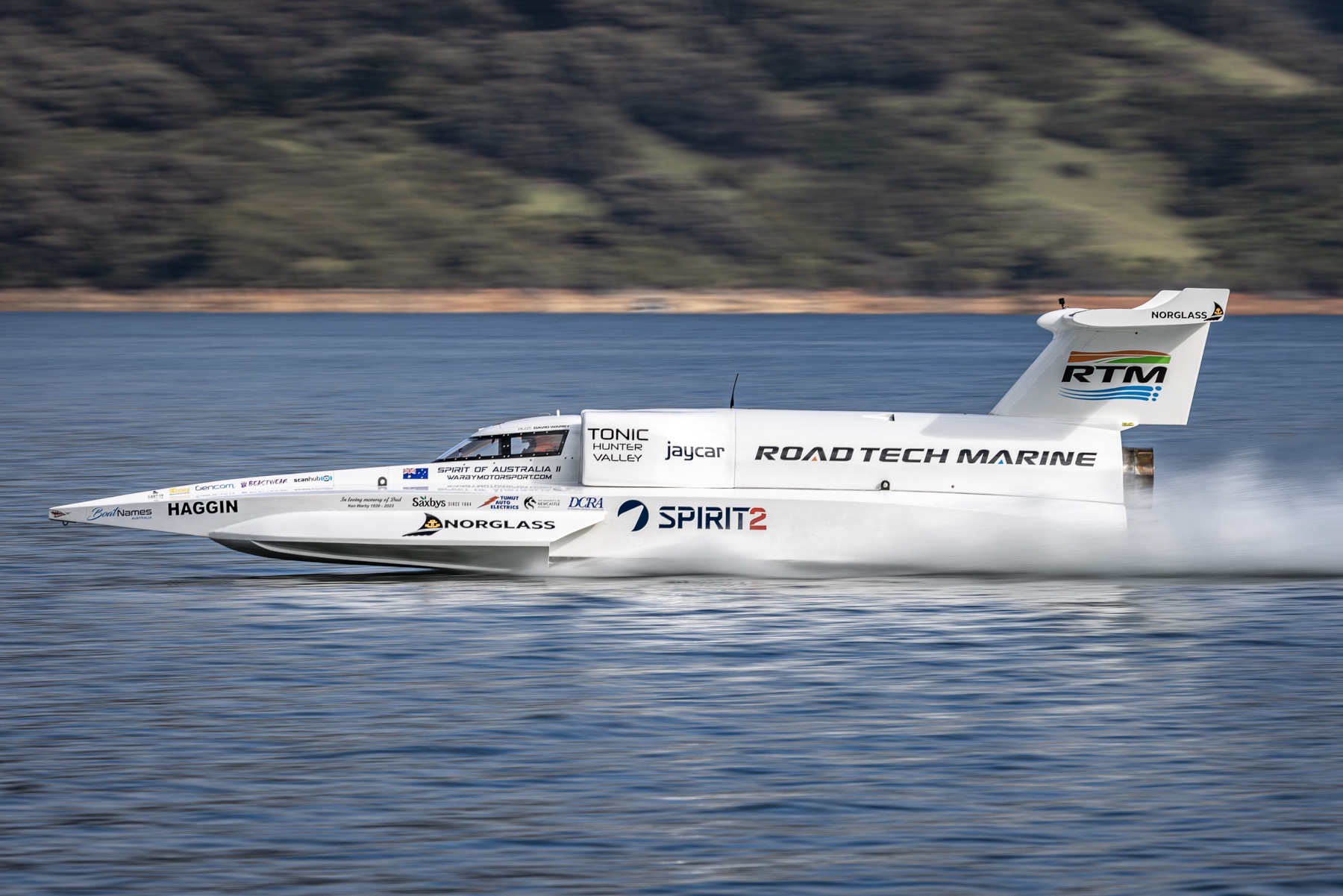
If you want to see a master class upon how to run and develop a jet hydroplane in a competent and safe manner within a public setting, then look no further than Warby Motorsport. Be under no doubt that we are so very blessed to have Dave and his team guiding us along with our little venture and with what lies in front of us for the times ahead. Dave says his next outing with SOA2 is scheduled for November and we will report back in due course upon how he gets on then with hopefully better weather.
So that’s it for this month folks, if you have not done so already please take a moment to like our Facebook page and drop by towards the end of next month for the next update on progress as we build our jet hydroplane Longbow to run and develop upon lakes and lochs within the U.K.