They do say timing is everything. In our case it was somewhat fortunate that we had timed the epoxy coating of the inside of our jet hydroplane, Longbow’s hull, out in the glorious warm sunshine of last month; as the weather here in the U.K. this month has definitely descended into the colder, wet, windy autumnal season. As a result it was now time to put on a jumper and with a hot brew settle into our next job on the list of building the boat.
So for this month that has meant permanently fixing into place the marine grade woodwork supplied by our sponsor Robbins Timber that makes up the rear of the sponsons and also likewise to fix into place the upper longitudinal battens that form the framework that will support the top decking of the sponsons. As always in the monthly updates of building our jet hydroplane Longbow we give thanks to our product sponsors who so very generously supply material for the build in return for the marketing platform the venture represents. Without them our project simply wouldn’t happen and this could not be better illustrated than by the following little tale.
Just as I was about to do some surface preparation air tool sanding with my old faithful air compressor, it decided to start playing up but I was loath to scrap it after all these years if there could be any hope of being able to sort the issue out. Even though it was not a Sealey compressor, Steve Buckle of our sponsor Sealey Tools came to our rescue with both technical advice and an appropriate replacement part that put new life into the old workhorse. This is just so typical of the tremendous support both Steve and Sealey have given to us throughout the project.
The timberwork for the sponsons is fixed into place using WEST SYSTEM Epoxy kindly supplied by our superb sponsor Wessex Resins & Adhesives. As the timber sections have to be clamped and held into place whilst the epoxy cures, we use a combination of Sealey ‘F’ clamps and marine grade stainless steel screws, with the screws left in place to become a permanent fixture of the craft. A big thank you to our friend and sponsor Frank Canfield, MD of Avon Stainless Steel Fasteners for keeping us stocked up with screws this month.
So with all that terrific support from our sponsors my wife Gill and myself set about the task of fixing all this carefully shaped woodwork into place. In this instance we split the task into putting together the bulk of the rear sponson first, then once that was achieved we could then fix the curved longitudinal sponson battens that would tie everything into place. The following photo shows the bulk of the rear sponson fixed into place as the first stage of the works were completed.
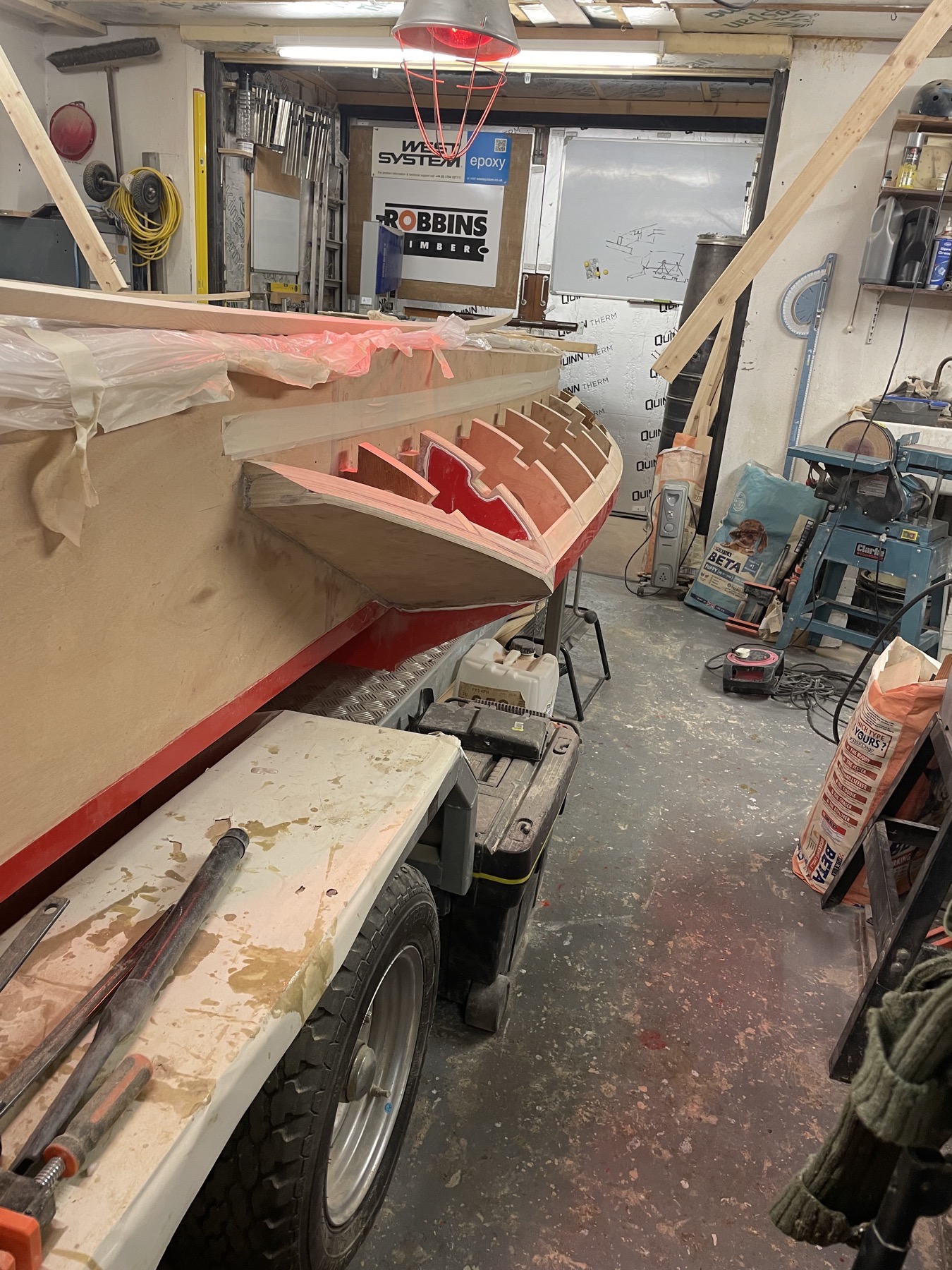
Methodically Gill was measuring and mixing each cup of epoxy for the allotted time on the clock, then pouring it into dispensing trays for me to use as I buzzed around the hull with an array of brushes, spreaders, spatulas, clamps, stainless steel screws and drivers. It wasn’t until 1.30am that we would see the job of fixing the longitudinal sponson battens completed and we could then clean down the tooling, set the workshop alarms and retire to bed.
Although you can remove the temporary fixing clamps sooner, I like to leave them in place for a couple of days before doing so, especially as we go into the colder seasons given the cure of epoxy is in part temperature related. So after a couple of nights away from the boat I gently teased the clamps off the areas of work and could then clean the wood down, thankful that my old compressor was back on form to make the job somewhat easier.
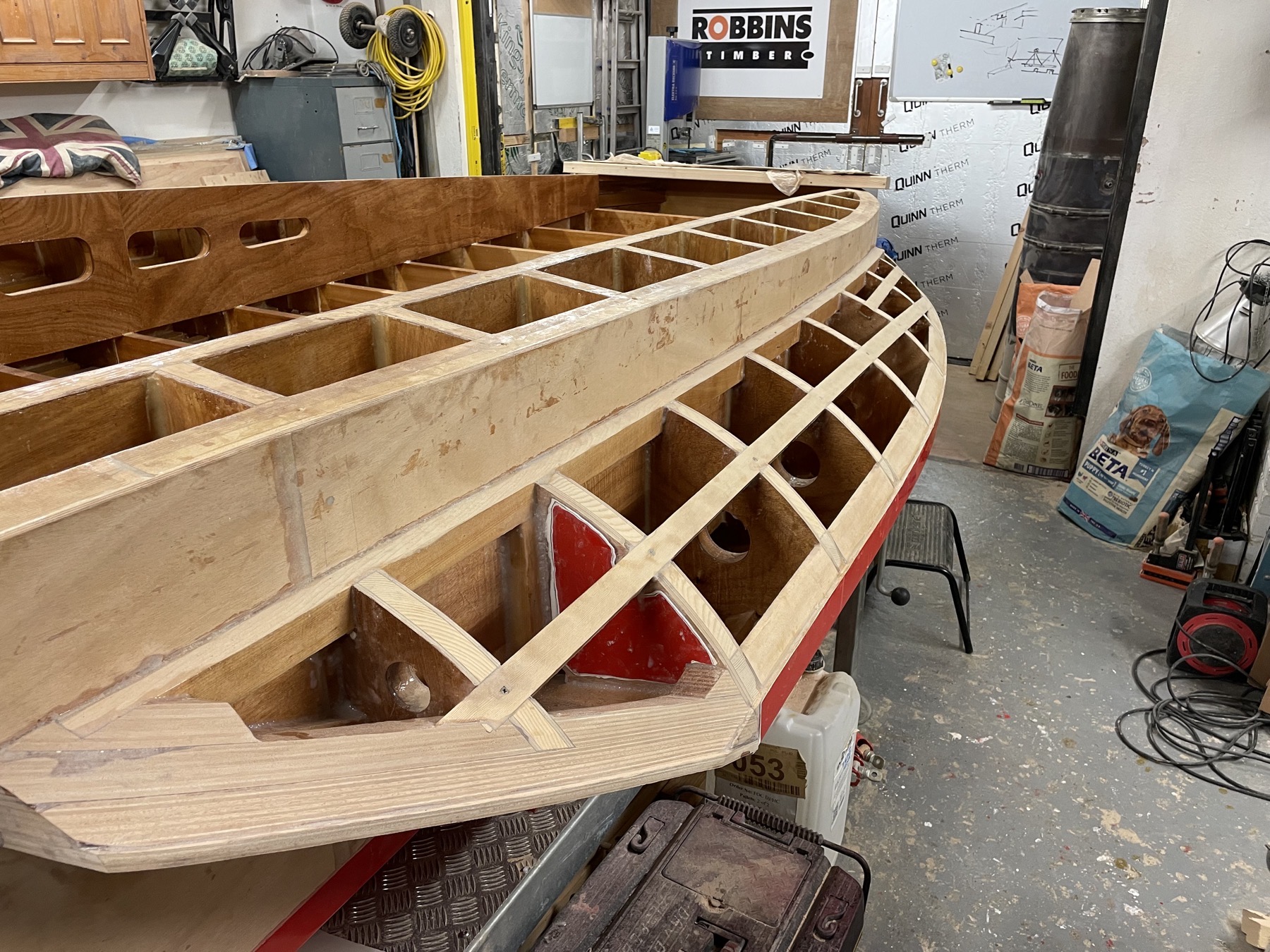
After that task was complete we could have carried straight on with the next job on the list which is forming the top decks of the sponsons. However I was also mindful that the weather was only going to become worse as we move into the colder wetter seasons, plus some of my trusted family helpers were committed to jetting off shortly on their holidays. This being the case the chances of a fine weather weekend between now and Christmas that also coincided with folk being around to lend a hand upon a dry weather weekend were quickly diminishing.
And why did I want the boat pulling back out of the workshop you may ask? Well because it was now time to get on with the exciting bit of trial fitting Longbow’s twin jet engines!
So grabbing hold of my newly acquired son-in-law Kieran and my two lads, Rob and Tom, we set about fitting the bolts to secure Longbow’s engine cradle into the hull and put together the lifting rig specially made by our sponsor Britlift for Longbow’s jet engines.
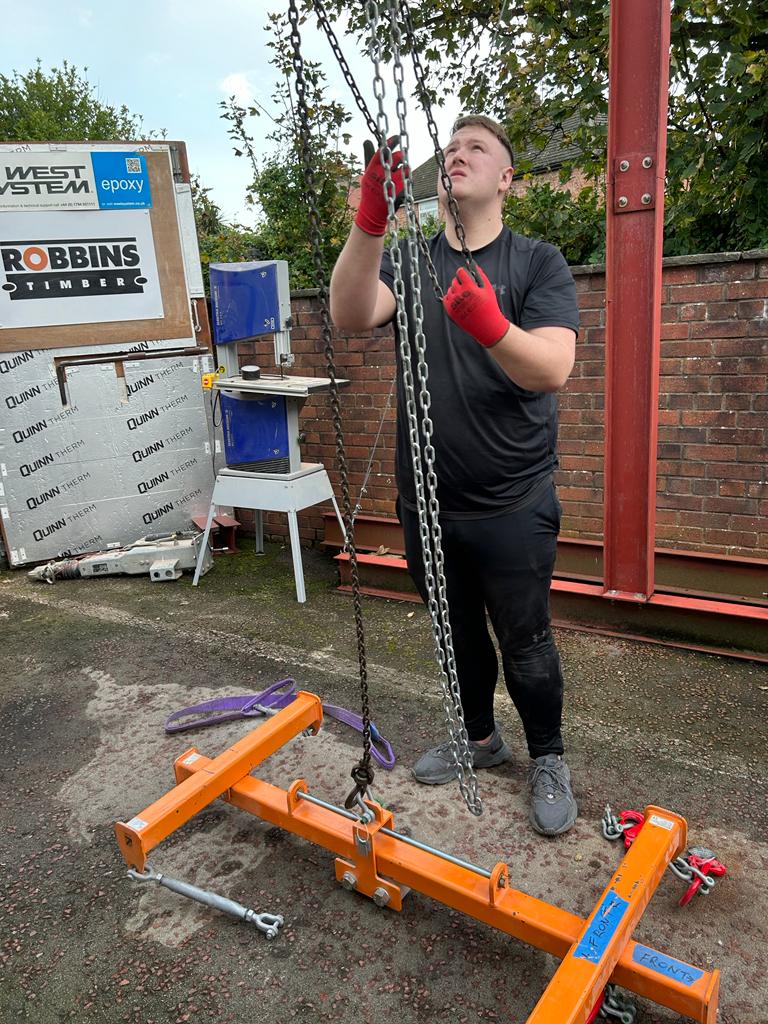
We then brought one of the Viper jet engines out of storage and hoisted it up into the air before pulling Longbow out on her purpose made trailer so she was directly underneath the engine. Rob was in charge of the block and tackle as he gently lowered the first engine into position until it married with the trunnion mounts of the engine cradle in the hull.
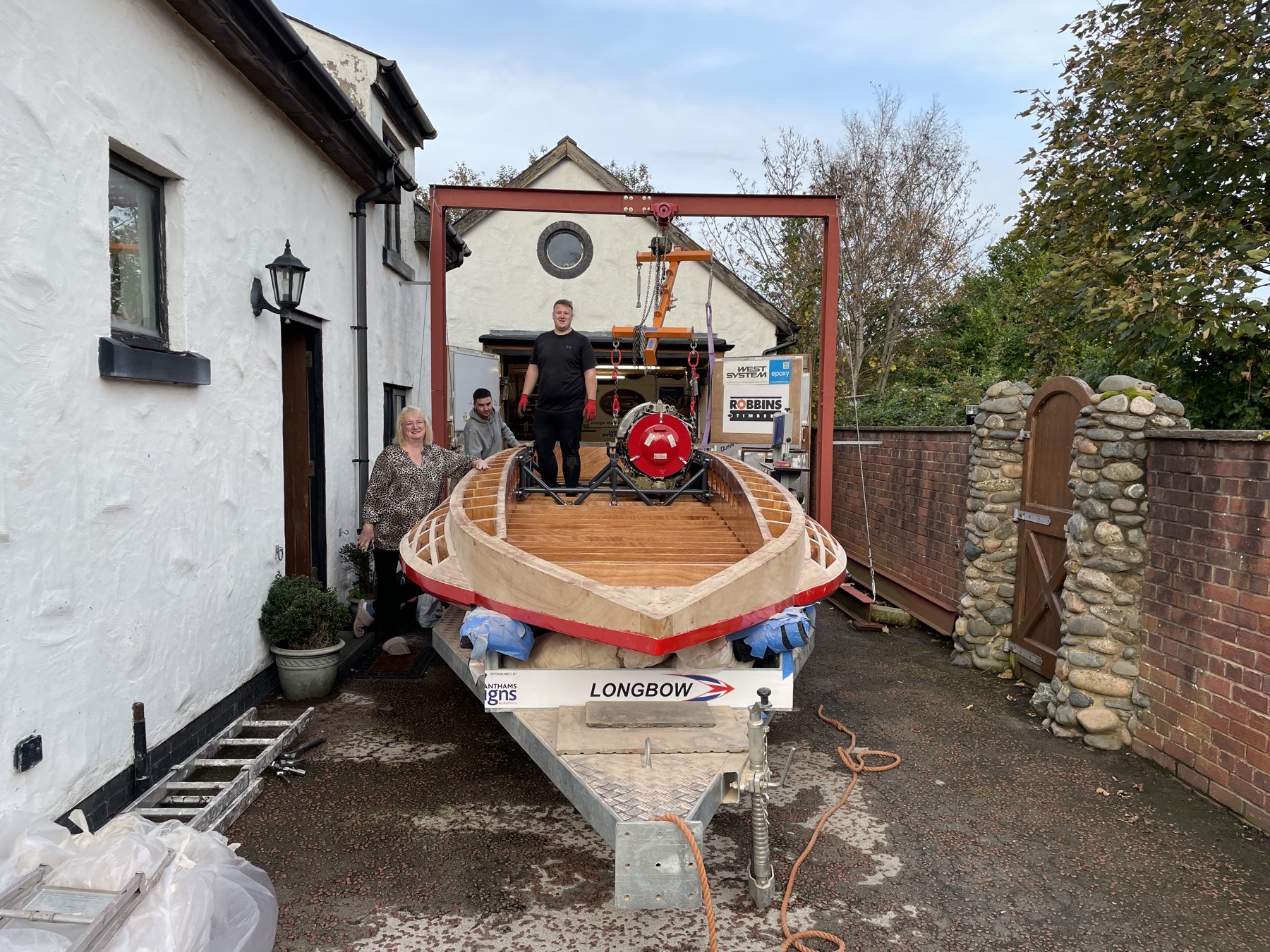
In order to fit the second engine into Longbow’s hull we then had to move the boat out of the way, move the beam trolley, block and tackle along with lifting rig to the other side and then bring the second jet engine out of storage and hoist that one up into the air. After that was done we could then push Longbow on her trailer to beneath the lifting rig and Rob could then lower the block and tackle to position the second jet engine into place.
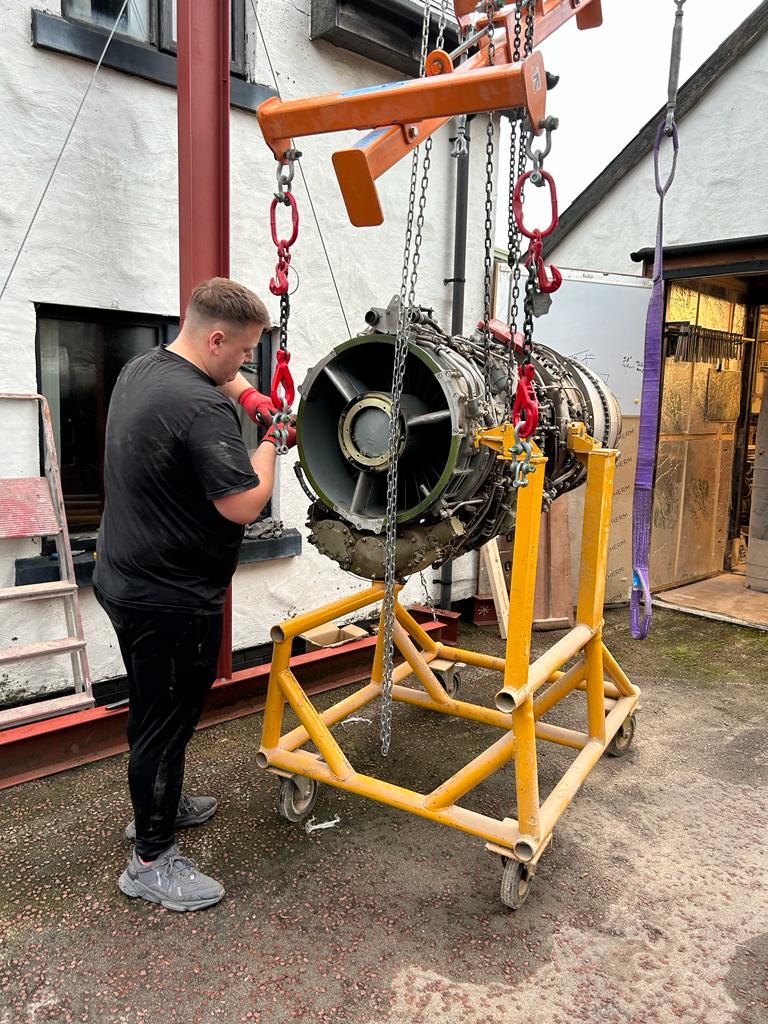
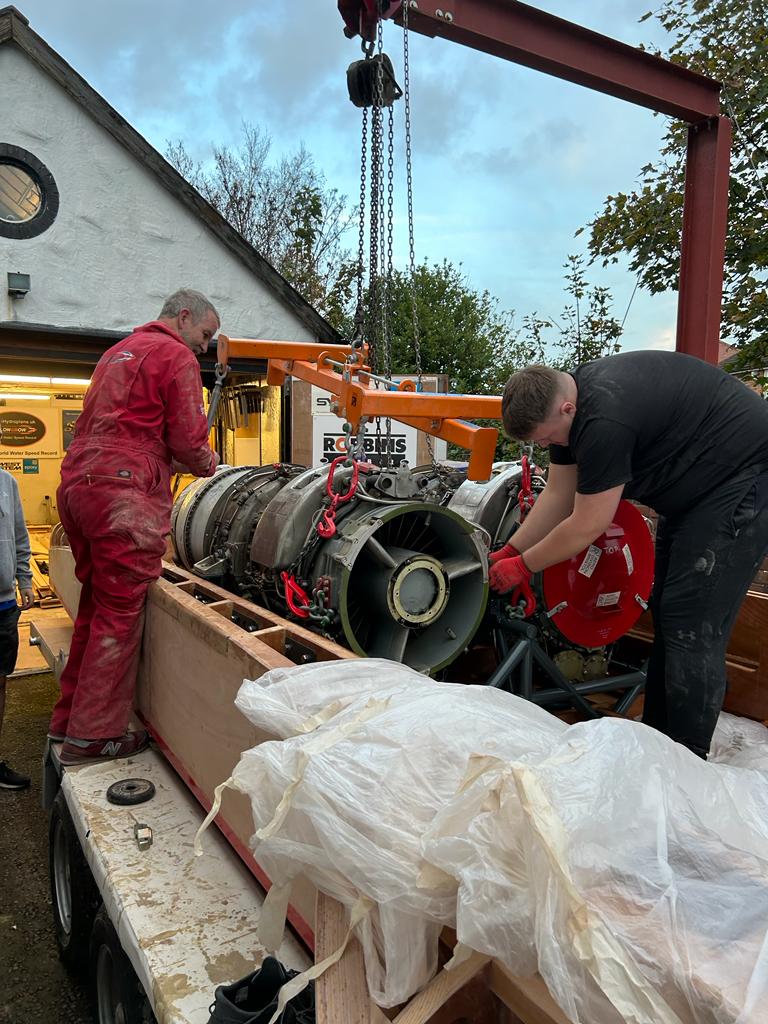
Just as it had all gone so smoothly the first drops of rain began falling. It hadn’t been forecast to rain but such is life and so we had to quickly sheet over the hull and get her pushed back into the workshop with her feeling just a bit heavier now the engines were thankfully installed than when we had previously dragged her out.
The following day I could fit the nose cones to the front of each of Longbow’s jet engines in the hull. These engine nose cones as you may recall from our previous update were polished by our metalwork guru Steve Charlesworth and they really look the part now they are fitted into place.
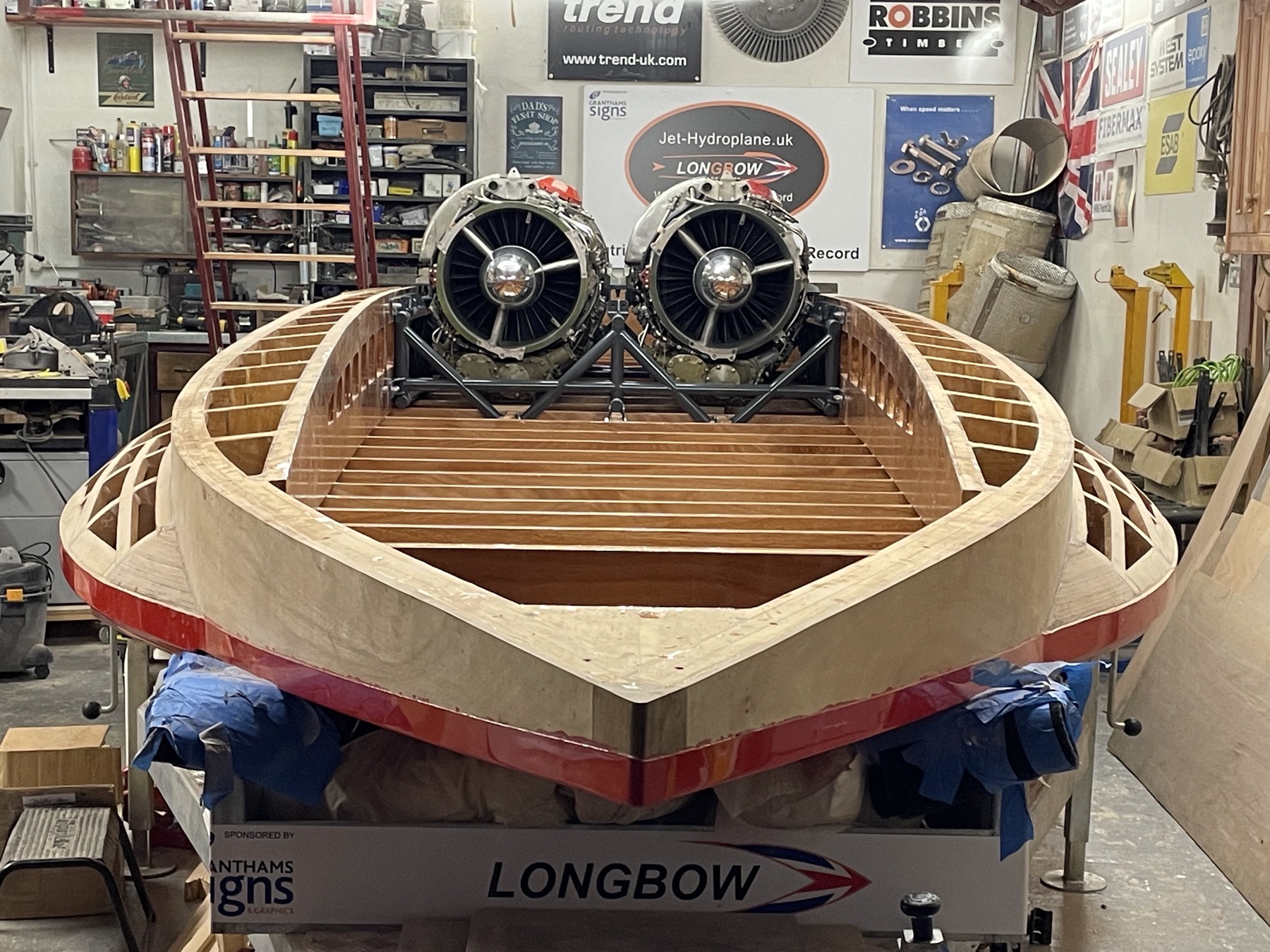
With the engines installed I can now start getting my head around cutting into the transom of Longbow to accommodate the twin jet pipes that will to some degree protrude out the rear of the boat. In addition with the sponson frames now complete, I can now start to make a template for making the top decks of those sponsons.
In the meantime our good friend Dave Warby and his team down in Australia are making preparations for a return visit to Blowering Dam with their jet hydroplane Spirit of Australia II next month. The craft continues to be fine tuned working towards Dave making an attempt upon his late father’s World Water Speed Record to make SOAII the fastest boat in the world.
Albeit at much slower speeds it was a fantastic achievement to see over 30 students from Princeton University in the USA and their driver John Peeters along with various sponsors all working together to set a 400 volt electric powered water speed record at just over 114mph with their hydroplane called Big Bird. The record was sanctioned by the American Powerboat Association (APBA) which is reportedly the oldest sanctioning body in the world for water speed records. Advisor to the project was J.W. Myers a very experienced and talented unlimited hydroplane driver who some of you may recall came over to Coniston Water back in 2012, to drive the U-11 Peters & May unlimited hydroplane to set a class record of just over 175mph in 2012.
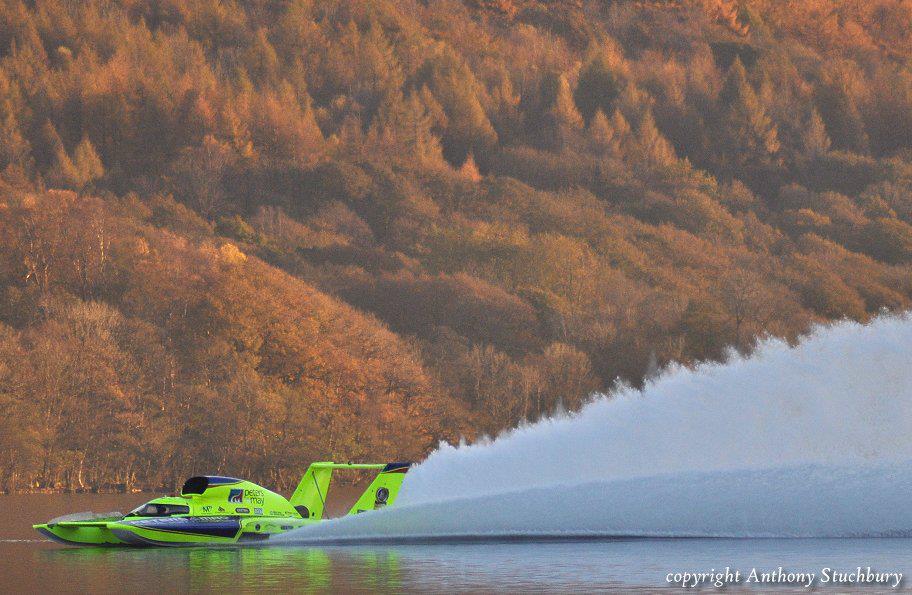
This year the 51st annual Powerboat Records Week at Coniston Water is taking place from 30th October to the 3rd of November and this being with the youngest competitor Tate Mantripp from Suffolk being only nine years old! Although the weather at this years event is unfortunately not the best and the number of competitors taking part this time around appears to be somewhat modest, we wish everyone taking part and supporting the event every success.
So that’s it for this month folks, if you have not done so already please take a moment to like our Facebook page and drop by towards the end of next month for the next update on progress as we build our jet hydroplane Longbow to run and develop upon lakes and lochs within the U.K.