As it is trick or treat this month I am always a little guarded as we approach Halloween when one of my children asks me to close my eyes as they have got something for me. However on this occasion it turned out to be treats they had taken delivery of, signed as being all the way from Australia. Upon opening the parcel I shouted ‘wow fantastic’ which prompted them to roll their eyes, walking away no doubt disappointed it wasn’t their latest Amazon clothes delivery.
My treats from half way around the world were actually two 50m rolls of Dynel fabric, courtesy of Damien Bensley, the General Manager of Colan Australia who are a sponsor of our jet hydroplane Longbow.
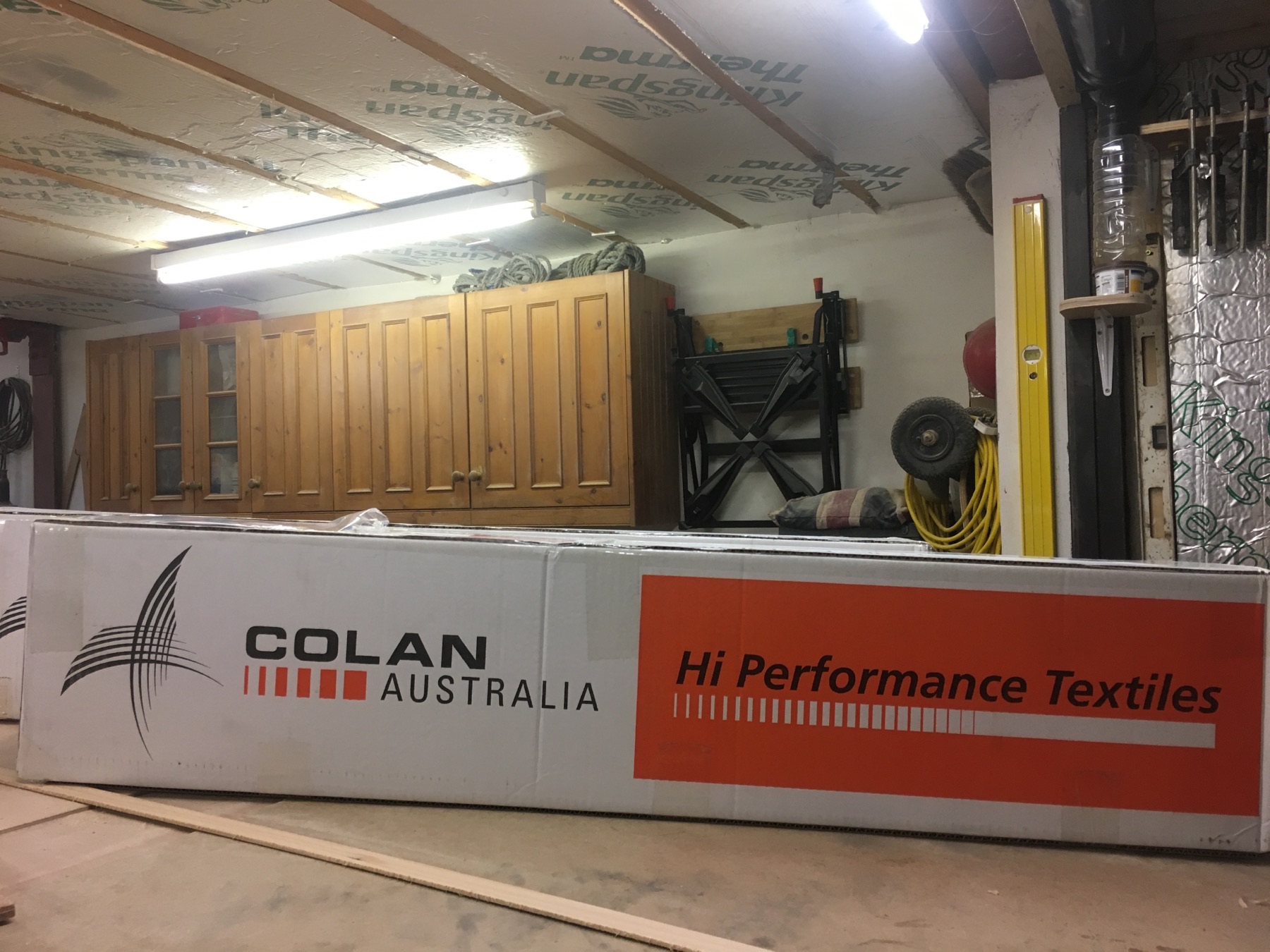
Dynel is a woven polyester cloth that has a long history of use in boat building where laminates to hulls require a high impact resistance combined with the requirement to withstand abrasion. Dynel was used on the hull of the current Outright World Water Speed Record holder Ken Warby’s jet hydroplane Spirit of Australia so we know it is a proven product for our application. Our only problem was getting hold of it since Dynel is not manufactured or stocked within the UK or indeed Europe but it is made and readily available in both Australia and the USA. Following the paper trail of where we could get it led us to the door of Colan Australia; so a very big thank you to them for supporting the building of Longbow from the other side of the world and sending us more than enough Dynel to do the job.
Whilst we are mentioning the land down under, I spoke with our good friend Dave Warby in Australia and Dave says the current COVID position there is that they have been given the green light to undertake further testing of their jet hydroplane Spirit of Australia II at Blowering Dam in a few days time! This is terrific news and will give Dave the first chance to run his boat with the addition of the T tail to see what difference that makes to the handling and he tells me the weather is currently forecast to be good, so happy days all round.
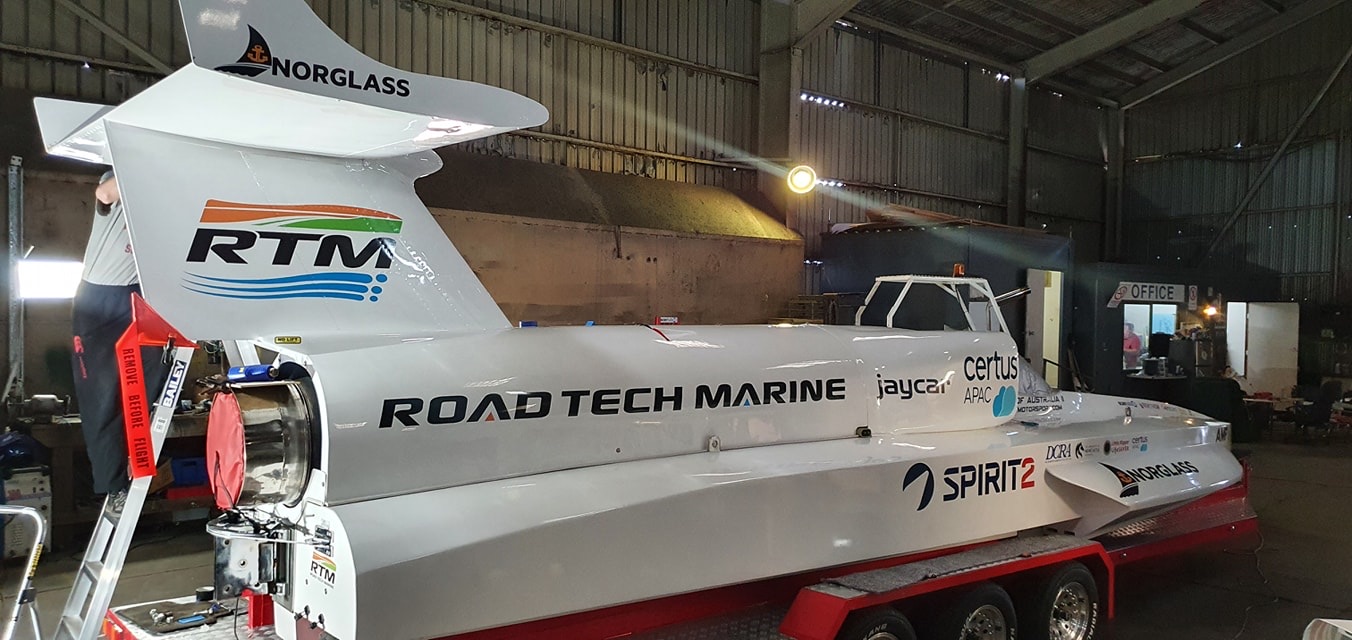
As always we wish Dave and his team every success out on the water with their latest round of tests but especially so on this occasion after their past frustration of being previously put on hold to run on the water due to the pandemic situation. We will of course report back in next month’s update as to how they get on but I cannot wait to see them back in action and as always showing to the world how a jet hydroplane should be professionally and safely run.
Back here with Longbow and our sponsor WEC Group in Darwen were able to take delivery of the steel and aluminium from our brilliant material supplier and sponsor John W. Laycock in Keighley. A really big thank you goes out to their MD Mark Sugden for organising the material to be pre cut to various sizes and its timely transport to WEC on our behalf. This material being for the fabrication of the trailer for Longbow that the craft will spend most of its life sat upon when not out on the water so it has to be right.
The fabrication of the trailer at WEC is being undertaken by their apprentices under the guidance of Kris Mercer and I have to say that I am absolutely bowled over by what a fantastic job they are all making of it, as can be seen by the following photographs.
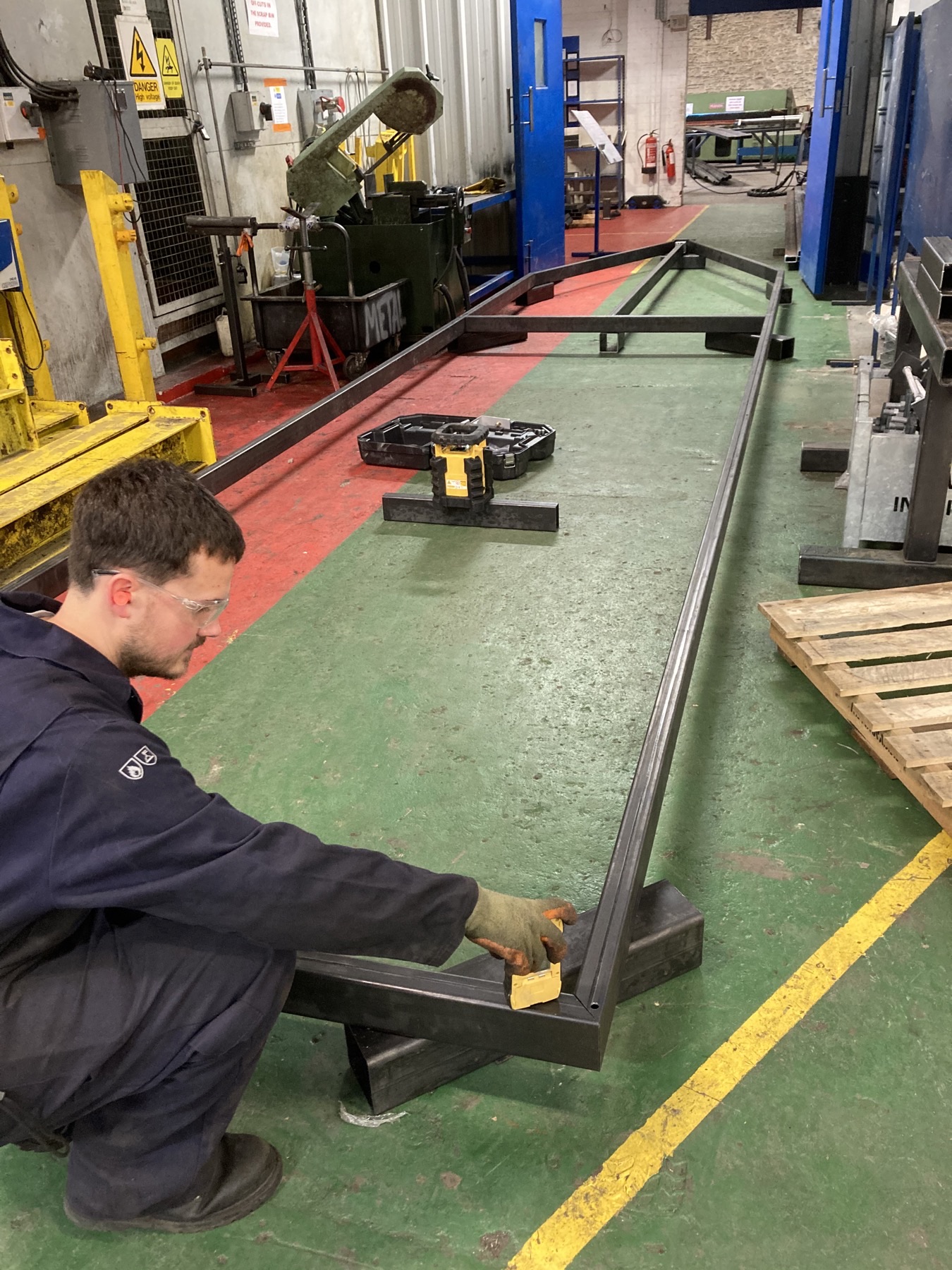

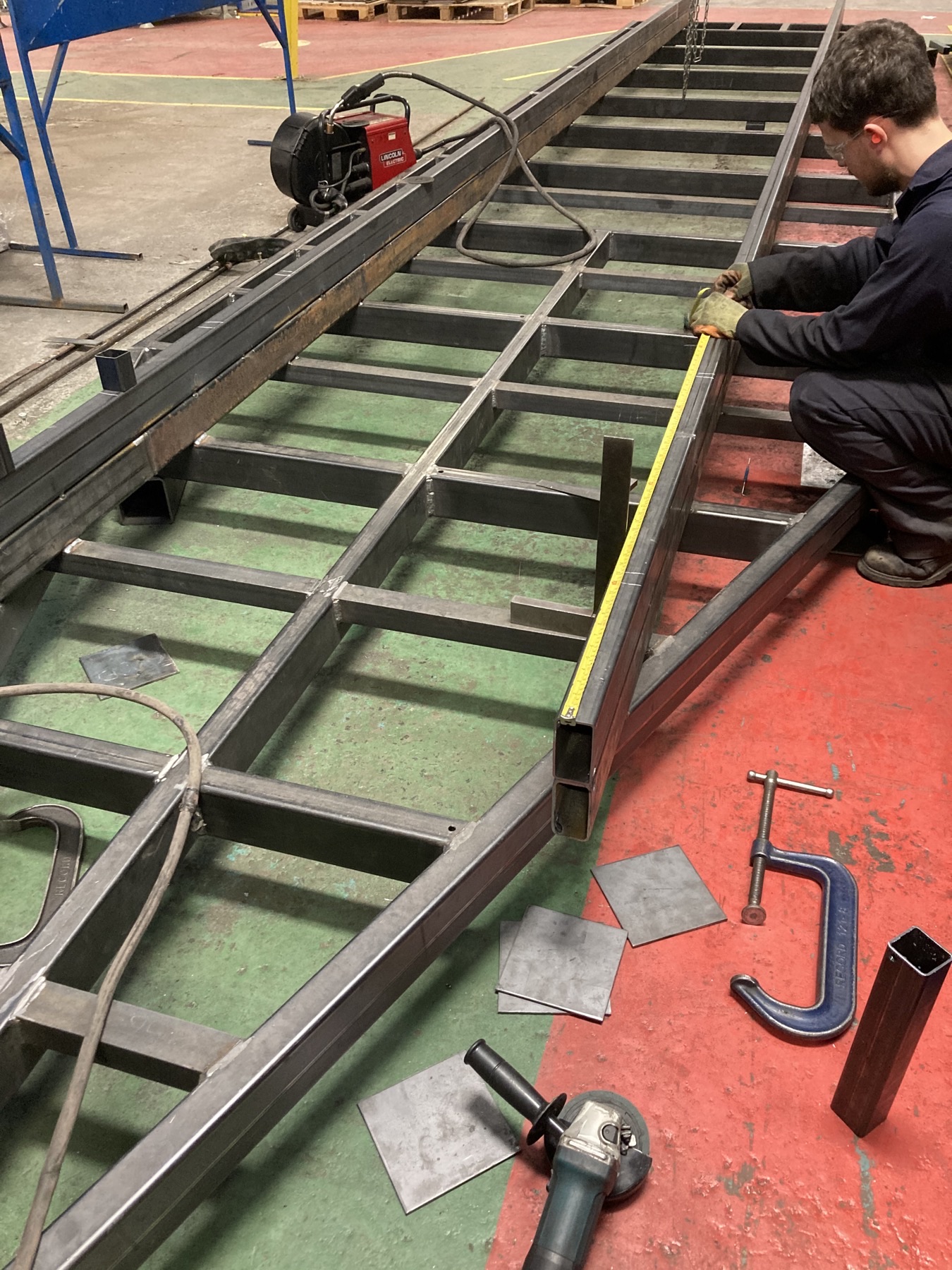
I am also amazed at how quickly the build of the trailer is coming along and I will show you more of the trailer construction at WEC in the next month’s diary update.
Here within my own cottage workshop, those who have been following the venture may recall that in last month’s update, whilst I said that the sponson shape at that stage of the build could then be seen; I also wrote that there was still a considerable amount of work to do in shaping this critical area of the hull before the plywood running surfaces could be fitted.
When running at speed the hydroplane is skimming along the surface of the water with only the rear few square inches at the rear of each planing shoe making contact with the H2O, in order to reduce hydrodynamic drag to a bare minimum. The rest of the sponsons and rear planing shoe are therefore interacting with the air at high velocity. With such a situation it should be obvious that the aim is to match the left and right sponsons in weight, shape and angles or the craft will want to veer off course giving the driver extra workload with steering corrections. With this in mind the time and effort spent on sanding, planing and shaping this sponson timber framework I knew would pay dividends prior to fitting of the plywood running surfaces over it.
Whilst to a layperson it might not look much, there is an awful lot going on when forming the shape of these sponsons. The sponson frames are set upon the rising surface of the bow that is also diminishing in width at the same time. Then on to that the sponsons are increasing in width from front to rear and every sponson frame has a different planing angle and differing chine (inclined side) angle. Add to that the outer and inner runners that are following those sponson frames whilst twisting like a corkscrew at the same time and you may begin to appreciate that it is quite a three dimensional puzzle to bring everything into line of where you want it to be.
The following photo shows me working on the sponsons with a variety of hand tools as it is not really the place for diving in with power tools and you can draw it out as much as you like but it comes down to constant measuring shaving and sanding and getting it too look right. There is for me considerable satisfaction from just taking my time and using a well sharpened plane of my grandfather’s as I try to emulate the skill and craftsmanship that he showed to me as a young lad in his workshop so many years ago.
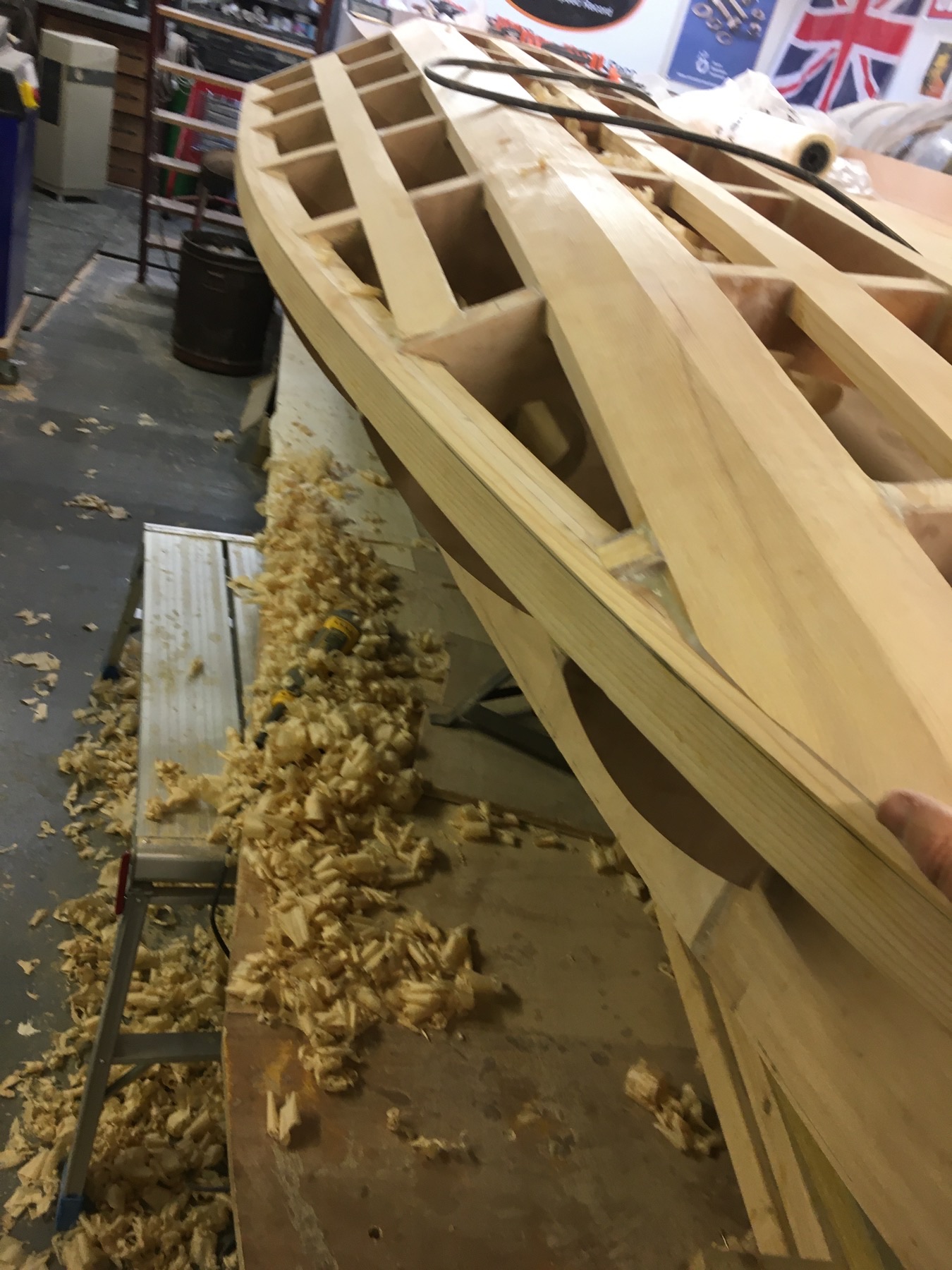
On the front of the sponson I had to infill the tapered step where it joins the bow of the craft using layers of marine plywood from our sponsor Robbins Timber, then shape this into a curved solid block. This area acts as a buttress taking the brunt of the hydrodynamic loads to the front of the sponsons as the craft comes out of its displacement stage, with increasing speed to get on to the plane and then again when the craft decelerates at the end of a run, to the point that it comes off the plane back down into the displacement stage once more.
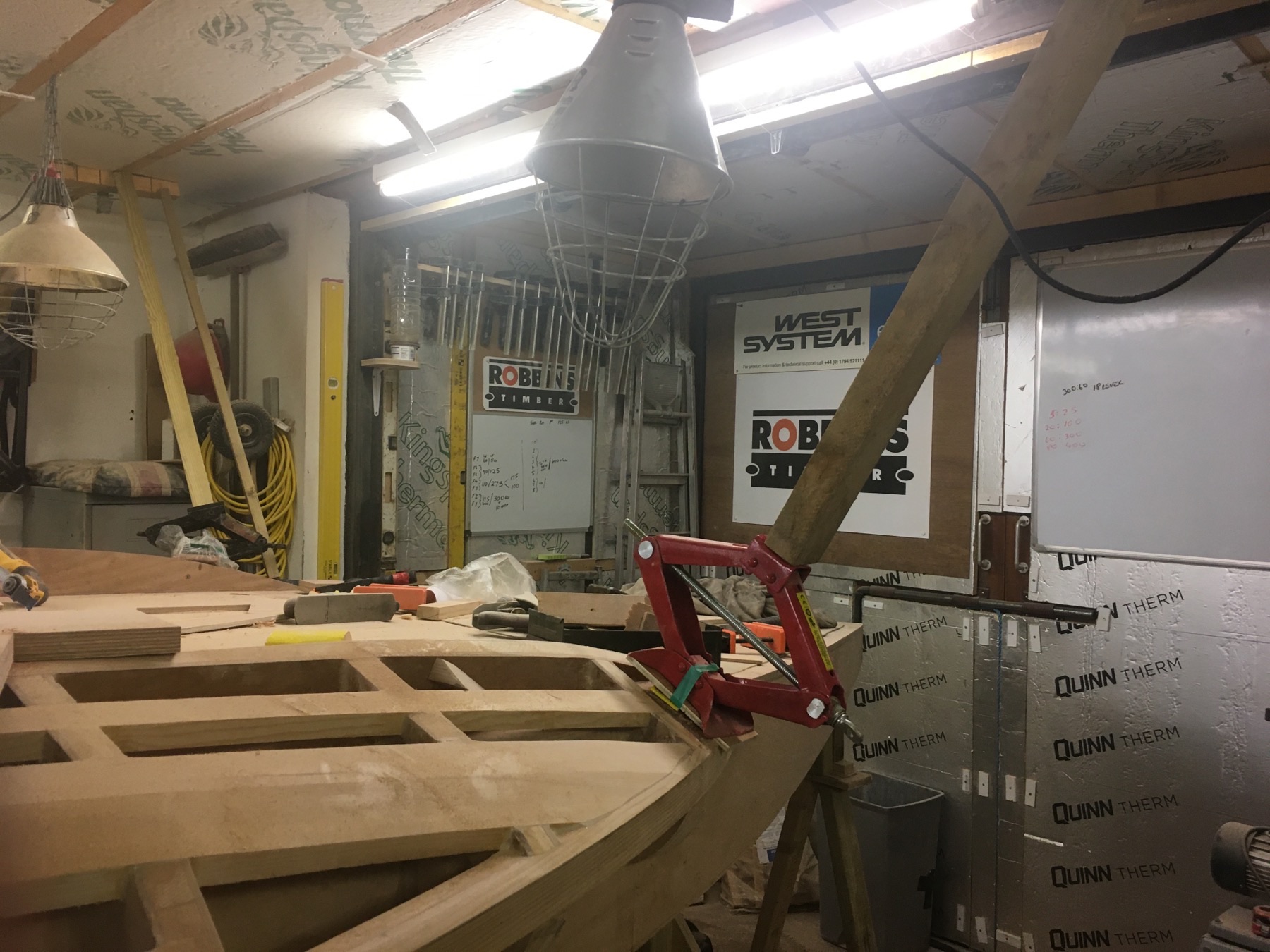
To the rear of the sponsons it was then time to shape and fit the closure sheet of plywood over the end grain of the timber runners to the sponsons using the WEST SYSTEM Epoxy supplied by our fantastic sponsor Wessex Resins through our good friend and Area Sales manager Colin Fletcher. As always the Sealey clamps and Raptor composite nails doing a fantastic job of holding everything in place whilst the epoxy cured.
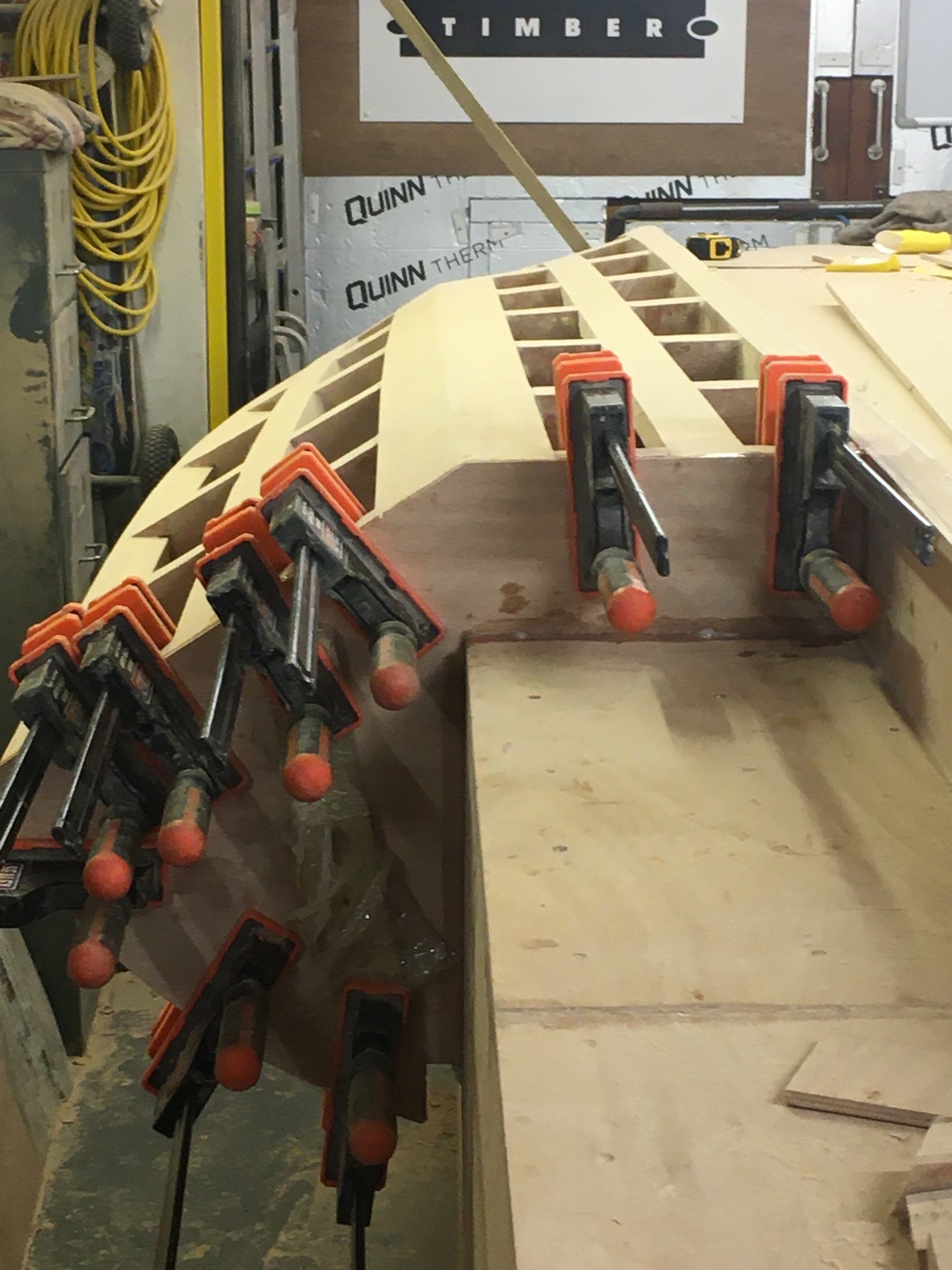
Next on the list of things to do was to widen the surface area of the outer rail to the chines of the sponsons to increase the adhesion contact area of the plywood and epoxy that will follow as running surfaces. This required several sections of the Robbins supplied timber to be cut and shaped to match the adjacent frames on each of the two sponsons and once I was happy with them, again I fixed them into position using the WEST SYSTEM Epoxy.

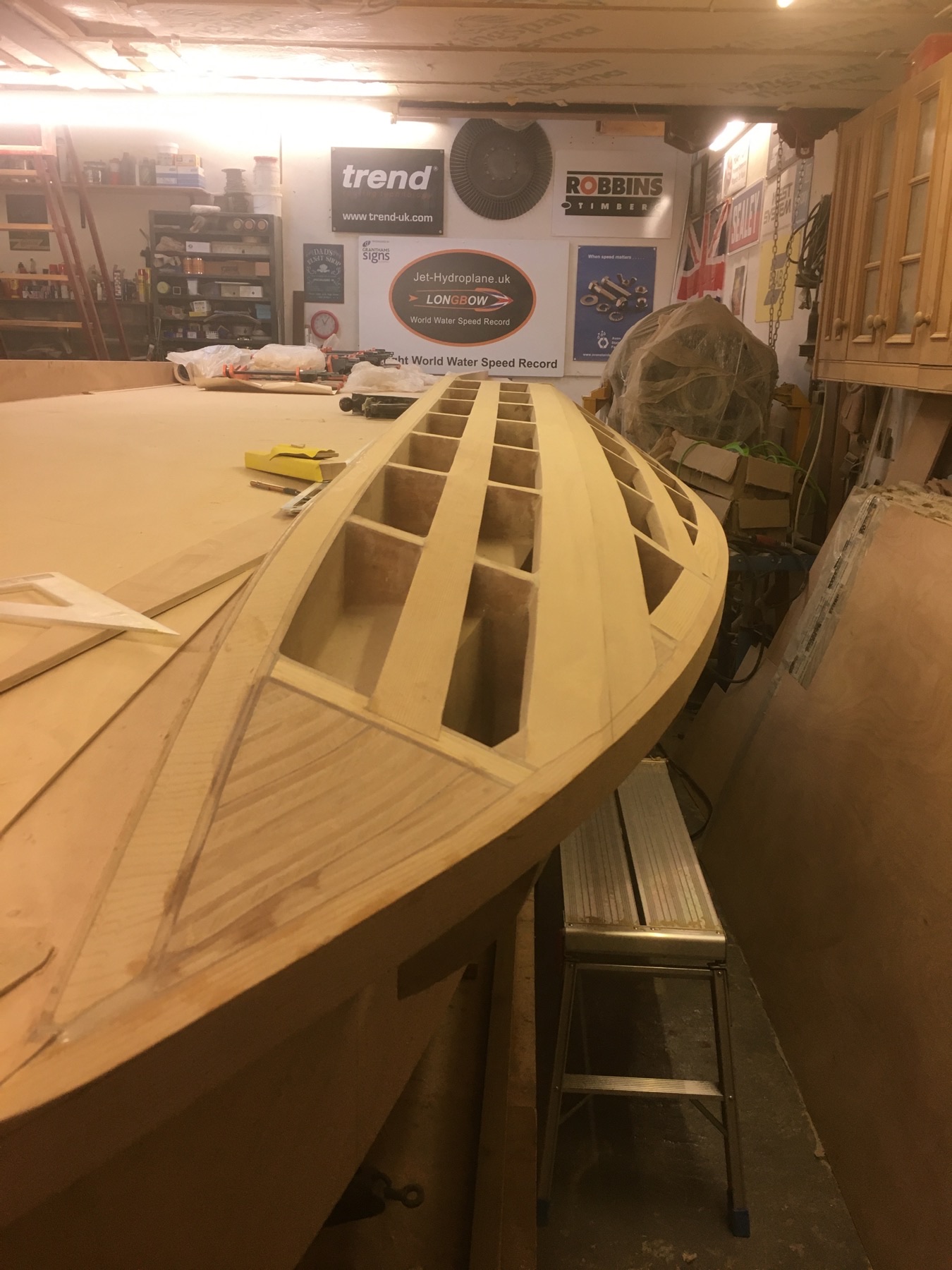
After that task was completed it was time to form the drainage pathways, or as I am told some folk call them, ‘limber holes’ to the sponson frames in order to allow any water (be that penetrating or condensate), that may occur between each sponson frame, a route by which it can be drained out via threaded sealed plugs as yet to be fitted on the rear of the last of each sponson frame.
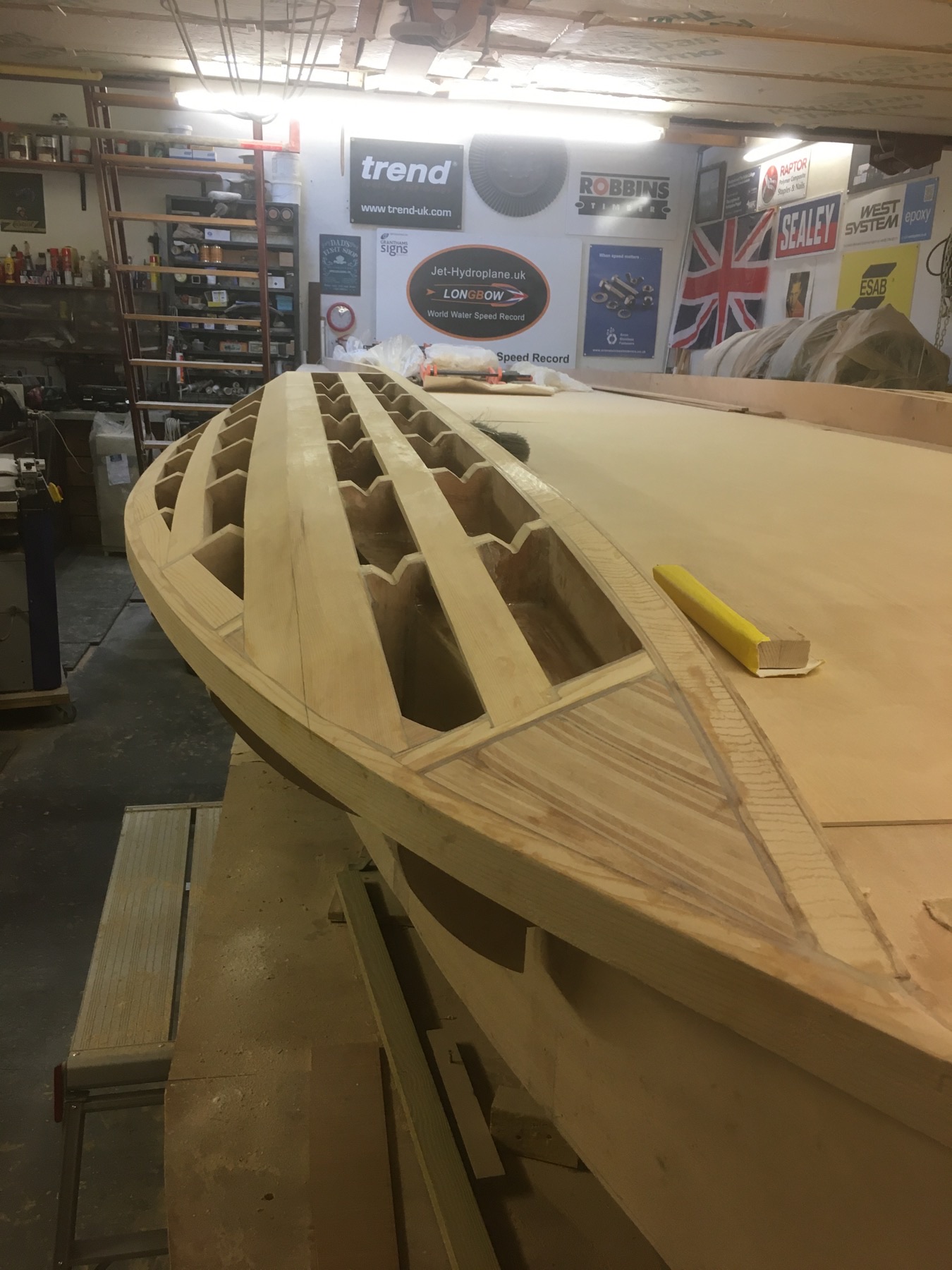
I hope from the above you will now begin to appreciate what I meant at the end of last month’s update when I said that at the time, there was still quite a bit of work to do before the plywood running surfaces to the sponsons could be fitted. However after the time spent on them since then I am now pretty much at the point where I can move on to the next stage of the build.
Away from the build it was sad news this month to be told that a lifelong friend of the family, Dave Chamberlain had lost his battle with cancer. He leaves behind many crazy happy memories for all that new him, a retired highly skilled engineer and thoroughly decent bloke who will be sorely missed. It was strange to say the least having to watch his funeral in Ireland via a live stream on the internet due to the COVID restrictions, so a proper wake like only the Irish can do is fully booked for a time when it is safe to all get together. As a tribute to the great man, the following photo shows Dave next to the Bluebird jet hydroplane replica K777 that I spent over four years working upon and he was so over the moon to see when I took him to visit a while back.
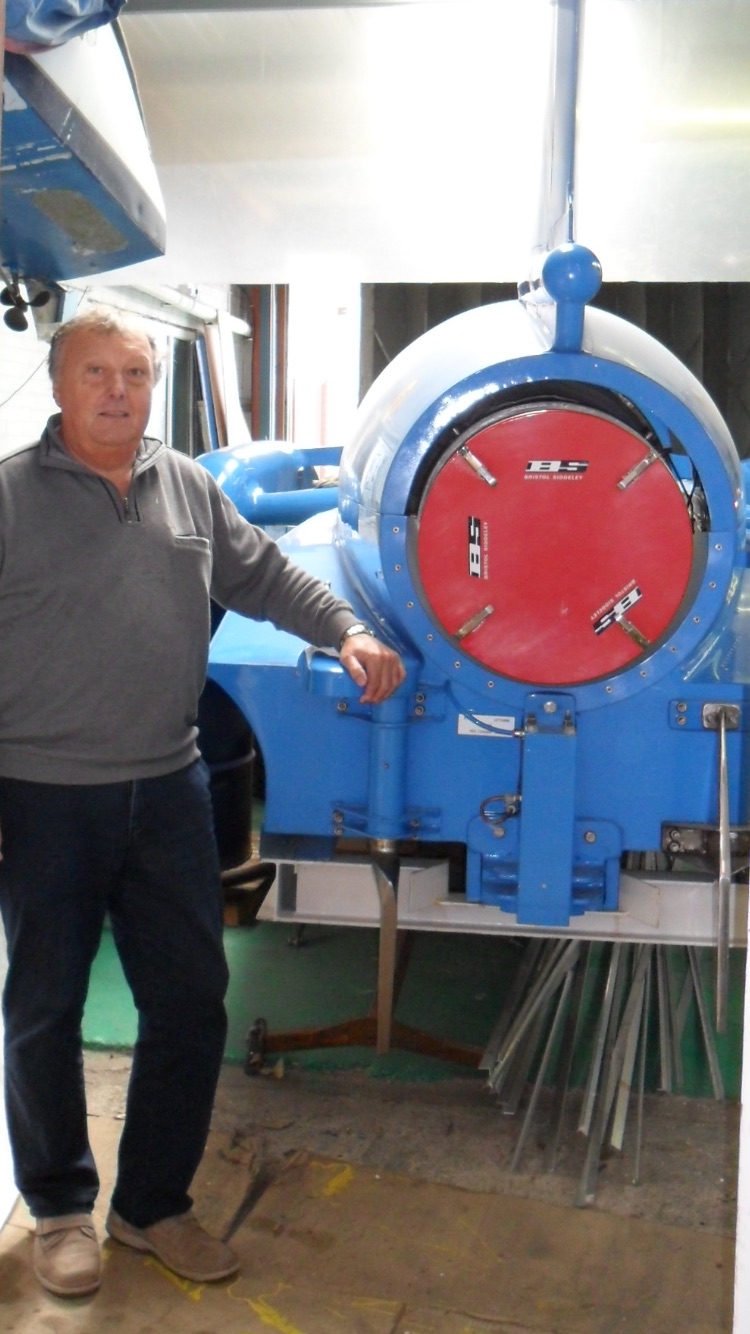
On a happier note and for everyone to go ‘aw how cute’ to, is one of our standard poodles called Elsa has had pups this month so here is a photo of them just after birth with all of their new homes already spoken for.
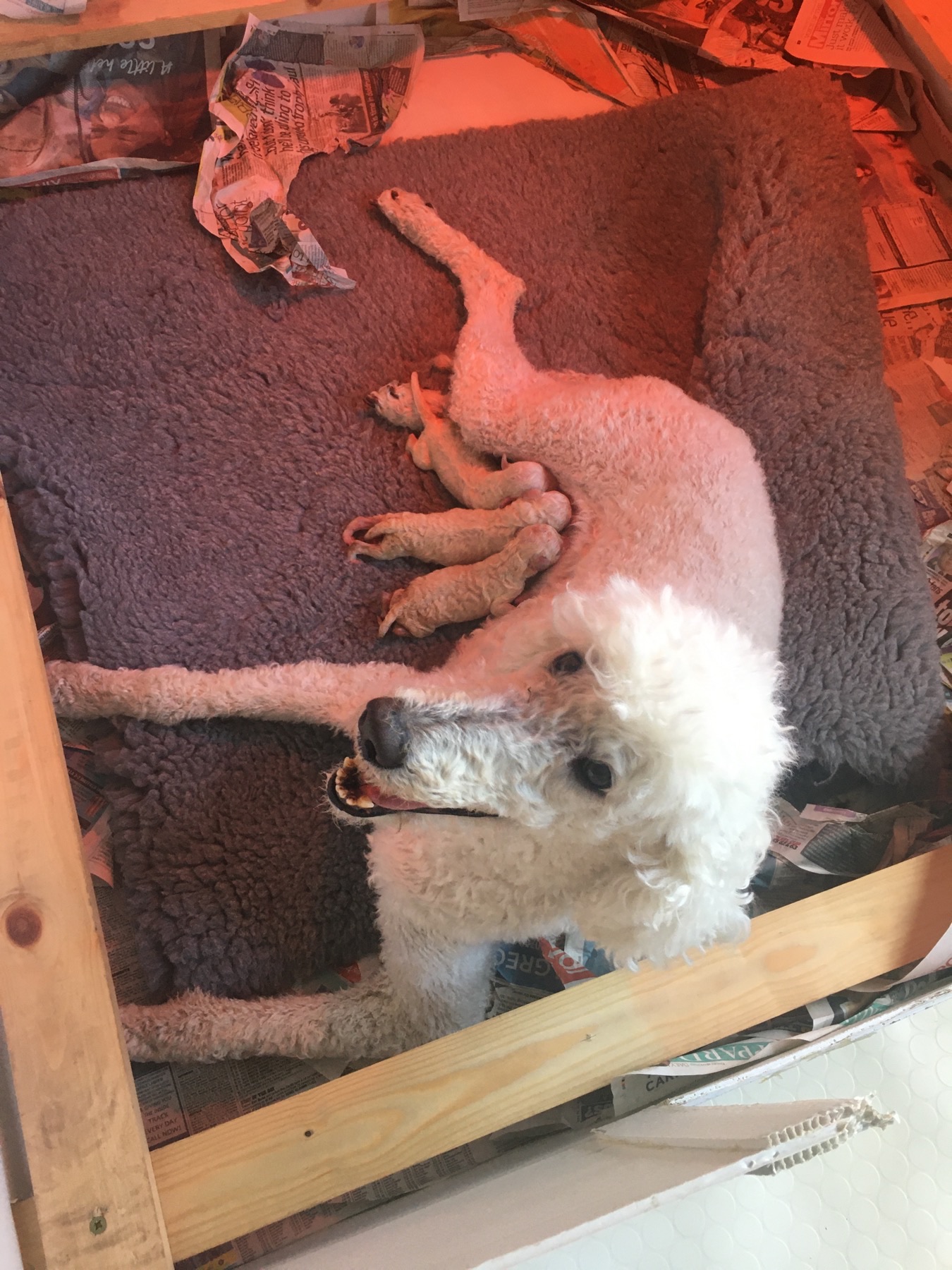
That’s it for this month folks, thank you for dropping by for a catch up with our little venture and if I have not bored you too much, then please tune in next month to see how things are getting along. If you have not done so already please like the jet-hydroplane Facebook page to keep in touch and stay as safe as you can in these most challenging of times.