Thank you for dropping by for a read and a catch up as here in the UK we plunged into a month of stormy weather and freezing temperatures that made life far from ideal for painting the underside of our jet hydroplane Longbow but more about that later within this update.
Emily Digweed, Digital Marketing Coordinator for one of our sponsors Wessex Resins has commenced writing some articles about Longbow for Epoxycraft magazine and the first in the series is now available to read online from the following link:
https://epoxycraft.com/projects/building-the-longbow-hydroplane-part-1/
We were hoping to report this month about how our good friend Dave Warby and his team had got on with development runs of their jet hydroplane Spirit Of Australia II. Unfortunately the program of tests had to be postponed over in Australia due to stormy weather there and Dave says the tests have therefore been rescheduled for December, so fingers crossed the weather is more favourable then in allowing the tests to go ahead.
Another good friend of ours, Steve Holter did an excellent talk at Brooklands this month to accompany his book on the subject of the jet hydroplane Crusader and his investigation into what he concludes are the number of reasons as to why the craft came to grief on Loch Ness in 1952. A link to Steve’s talk is as follows:
This month we were contacted by a television production company who are considering a documentary upon current outright air, land and water speed record contenders to which we said it was premature to be featuring Longbow so we suggested they approach Dave Warby for the water speed record element. However during that conversation it became apparent that as the person was a layman in such matters there was some confusion as to what they perceived a hydroplane is and what some of the challenges of going quick upon water are, compared to the land speed record for cars and motorcycles.
At the same time and perhaps as a result of Steve’s talk mentioned above we also noted comments upon social media comparing the largely wooden structure of Crusader with the all metal construction of Bluebird K7. We have skirted around these points before in previous updates so perhaps it is worth now going into greater detail of both hydroplane design and construction over a series of diary updates.
So what is a hydroplane? In essence it is a boat that when running at speed is supported by more than simple buoyancy with the hull largely out of the water as it skims along running upon the craft’s planing surfaces. Why would you want the boat up and out of the water when running at speed? Well depending upon altitude water is around 800 times more dense than air so that is quite a difference and in case you cannot get your head around the size of that magnitude, then the next time you are at a swimming pool try in a depth you can stand up in the water running from one side to the other through the water. Now compare that to how much time and effort it takes compared to doing it on land. Accordingly if we can get most of a boat’s hull up and out of the water we can go quicker for less power compared to trying to plough through it.
Whilst both Crusader and Bluebird K7 were specifically designed as jet hydroplanes their format compared to each other was radically different. In the case of Crusader she had a large diameter centrifugal flow jet engine that inherently made the thrust line above the surface of the water high compared to the much smaller diameter axial flow compressor of Bluebird K7. The difference between axial flow and centrifugal flow jet engines having been discussed in previous updates for Longbow.
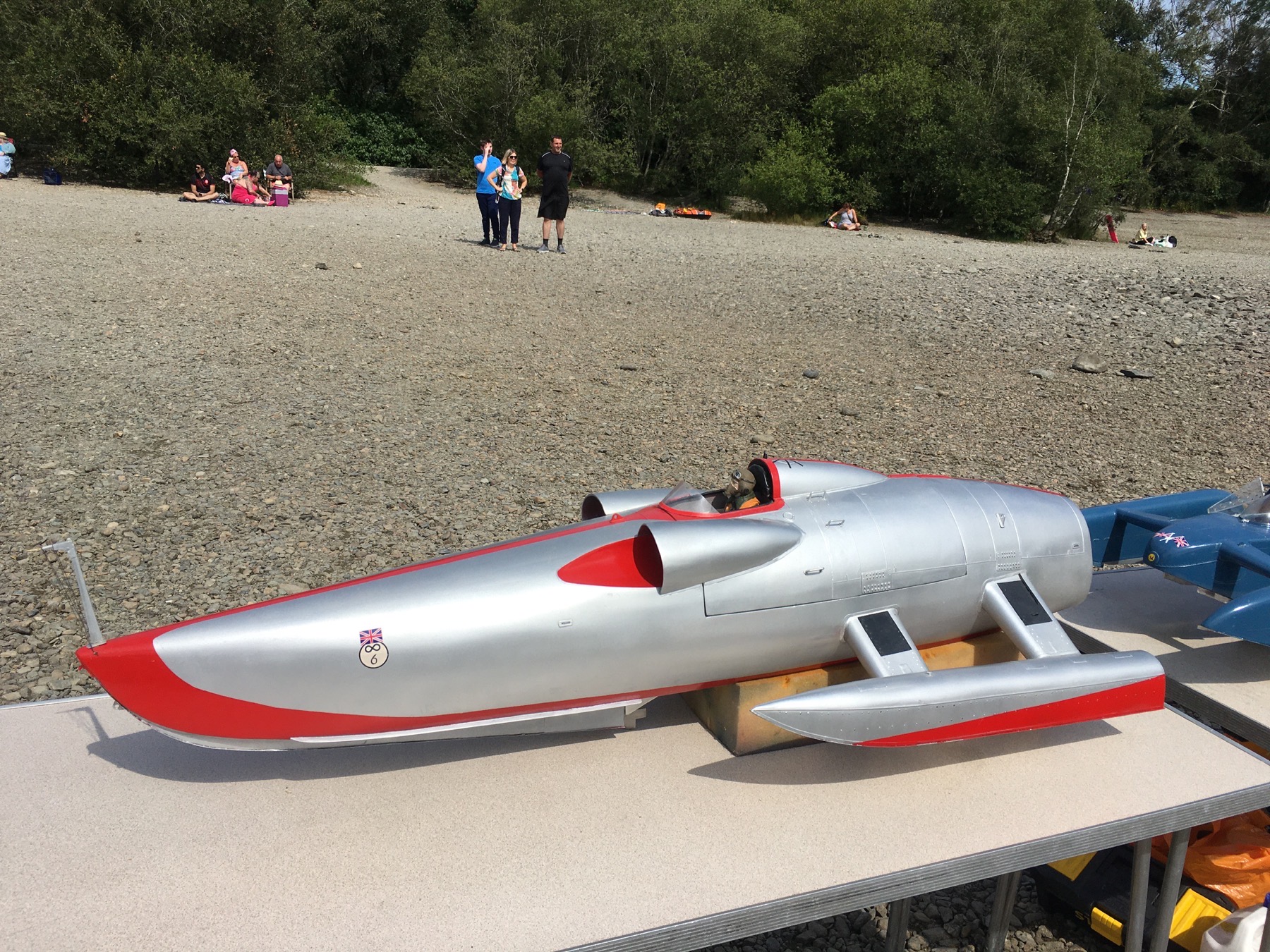
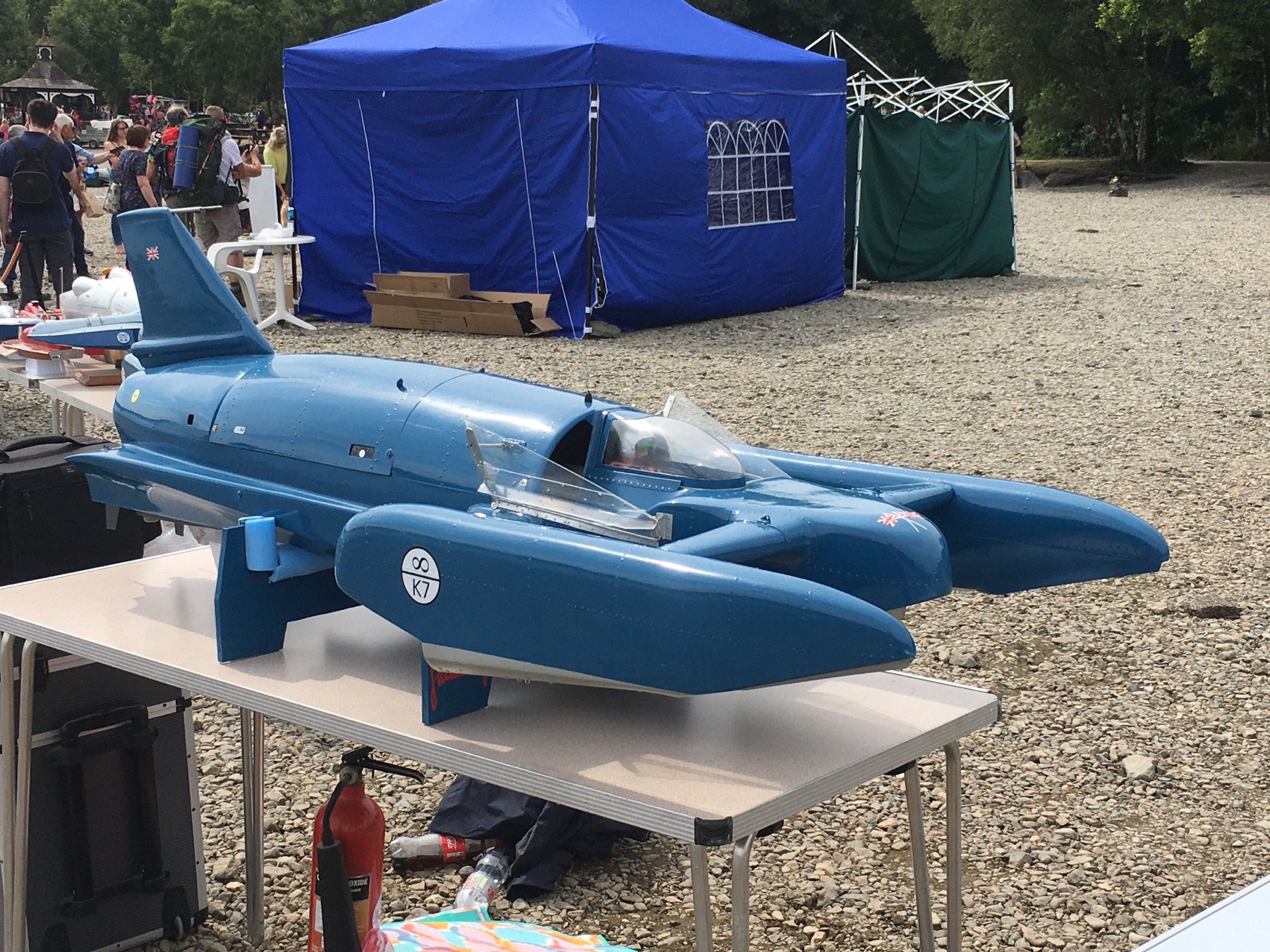
Both Crusader and Bluebird K7 were designed to run at speed on three planing shoes but in the case of Crusader two of those planing shoes were on outriggers to either side at the back of the boat and one beneath the front, whilst with Bluebird K7 two planing shoes were at the front on outriggers either side of the boat whilst, a third planing shoe was beneath the rear of the hull.
Another difference between the two craft is the location of the rudder. In the case of Bluebird K7 the rudder is located at the rear of the boat whilst with Crusader it was directly behind and attached to the single planing shoe at the front of the boat.
Neither craft had a composite safety capsule for the driver. Crusader only had one crash and that was fatal, Bluebird K7 only had one crash and that too was fatal so in both cases the fact that one was built from metal and one was built from wood made no difference to the outcome when an accident occurred.
If you watch the talk by Steve in the link given above you will note that failure of the front metal planing shoe to Crusader was occurring prior to the crash due in part to the lack of wood that was designed to be present beneath the front shoe being omitted in the build process.
Both Crusader and Bluebird K7 are outrigger hydroplanes. That is to say two of the planing shoes are on arms that span out from the main hull on either side of the craft. These outrigger type hydroplanes are not designed to tunnel / trap air beneath them which makes them somewhat separate in design from hydroplanes that do just that. When comparing the ride of the outrigger hulls to a tunnel / air trapping hull would you rather sit in a wheelbarrow with no suspension being run over a ploughed field, or be taken across that same field in a hovercraft that traps a cushion of air beneath it?
If you were to look at the percentage of hydroplanes built from the 1950’s to present day, be they of small capacity outboard propeller, all the way through to the Unlimited Class and compared how many of those were outrigger designs to those that tunnelled / trapped air beneath their hulls, you would find only a handful have ever been of such outrigger configuration and none of those outrigger designs have been very successful at circuit racing.
Whilst even a shopping trolley can be made to plane on the surface of the water if you tow it behind a boat quick enough, it is not unreasonable to conclude that by evolving design and real world out on the water experience there is a reason air trapping / tunnel boats have been the norm in hydroplane racing over decades and not the outriggers.
When we look at the current Outright World Water Speed Record of 317mph held by Ken Warby MBE at 317mph in his jet hydroplane Spirit of Australia that craft was built in wood and it is an air trapping type hydroplane. When we look at the previous record holder of 285mph with the jet hydroplane Hustler we also see that the craft was also wooden hull of an air trapping design.
It would appear that there is a false perception held by some that wood is an unsuitable material for building a jet hydroplane to undertake a straight line record of being the fastest boat in the world. However the above facts show this not to be the case. Furthermore 2.5 ton wooden air trapping Unlimited Class hydroplanes with massive V12 aero engines circuit raced against each other in very rough water for decades. In the 10th century Vikings sailed 1000 miles across the ocean in wooden boats to Greenland. All kinds of wooden boats and ships are still being built to endure mountainous waves today. The Mosquito aircraft largely built of wood flew a top speed of 437mph.
When we look at the straight line water speed record the craft are individually designed, running upon calm water. Here we want to view any structural issues that may occur and undertake alterations to the hull that may be required as a result of on the water development.
Composite construction of course has its uses and we will incorporate it in many parts of the craft such as the driver capsule, air intakes for the jet engines, etc. However composite construction for an entire hull of this size would be at comparatively massively more cost than wood. Defects if they do occur to a composite hull are not particularly easy to detect and accordingly sudden catastrophic failure of composite material can be the only point you find out it was actually happening.
Changes to a one piece fully composite hull are also not easy to make. We would have to build a timber hull as a buck in order to form the composite construction from it and bear in mind this is a one off build. That is to say it is not like we are going into business selling multiple copies of the craft. Neither are we under the time pressures that say a circuit racing hydroplane team are to replace damaged elements with off the shelf parts for the next race.
When you start to factor all of these issues in then an air trapping / tunnel wooden hull with composite safety driver cockpit combination begins to look increasingly attractive.
An air trapping / tunnel hydroplane is capable of high speed because we are in effect flying the boat over the surface of the water whilst remaining just about in contact with it by only a few square inches on each planing shoe and the rudder / any other appendage such as a fixed fin (to aid directional stability) being immersed in the water.
So how do we fly the boat? We design the hull like a wing with the ceiling of the tunnel to the craft being the underside of the wing and the upper deck forming the topside as we run it in what is termed ‘ground effect’ which is a little misleading as in our case we are obviously running it over water. As the hull acts like a wing as we travel along it will create lift so the hull is not only supported by the hydrodynamic planing surfaces of its shoes, it is also supported by aerodynamic lift. The bigger the surface area of the tunnel the more lift we are going to get.
The amount of lift is not only effected by the total surface area of the tunnel, it is also effected by the aspect ratio which is the width of the tunnel divided by its length. A short wide tunnel generally speaking will give you more lift than a narrow long one. Hence why say a glider has wings that have a considerable span (side to side), compared to their width (front to back). However if we get too much lift and have no means of correcting it, the craft will blow over.
We need enough thrust to overcome the total amount of drag for the speeds we are aiming at and the forces acting about the centre of gravity of the boat must balance out if we are going to be able to run straight and true without pitching up and blowing over, or nose diving into the lake. As we consume fuel the boat will get lighter and that might alter its balance, the water and wind conditions constantly change, which in turn can alter the angle at which our hull acting as a wing is running. That in turn will alter the amount of lift generated and alter the forces around the centre of gravity. Remember all of this is as the craft is travelling at high speed so it can ruin your day in the blink of an eye. It is therefore something of a delicate balancing act.
We will delve further into this balancing act in future updates as that is probably enough for you to scratch your head over for now.
Back with the build of Longbow as the temperatures plummeted Steve Buckle of our sponsor Sealey Tools sent us some replacement infra red heater bulbs for the workshop.
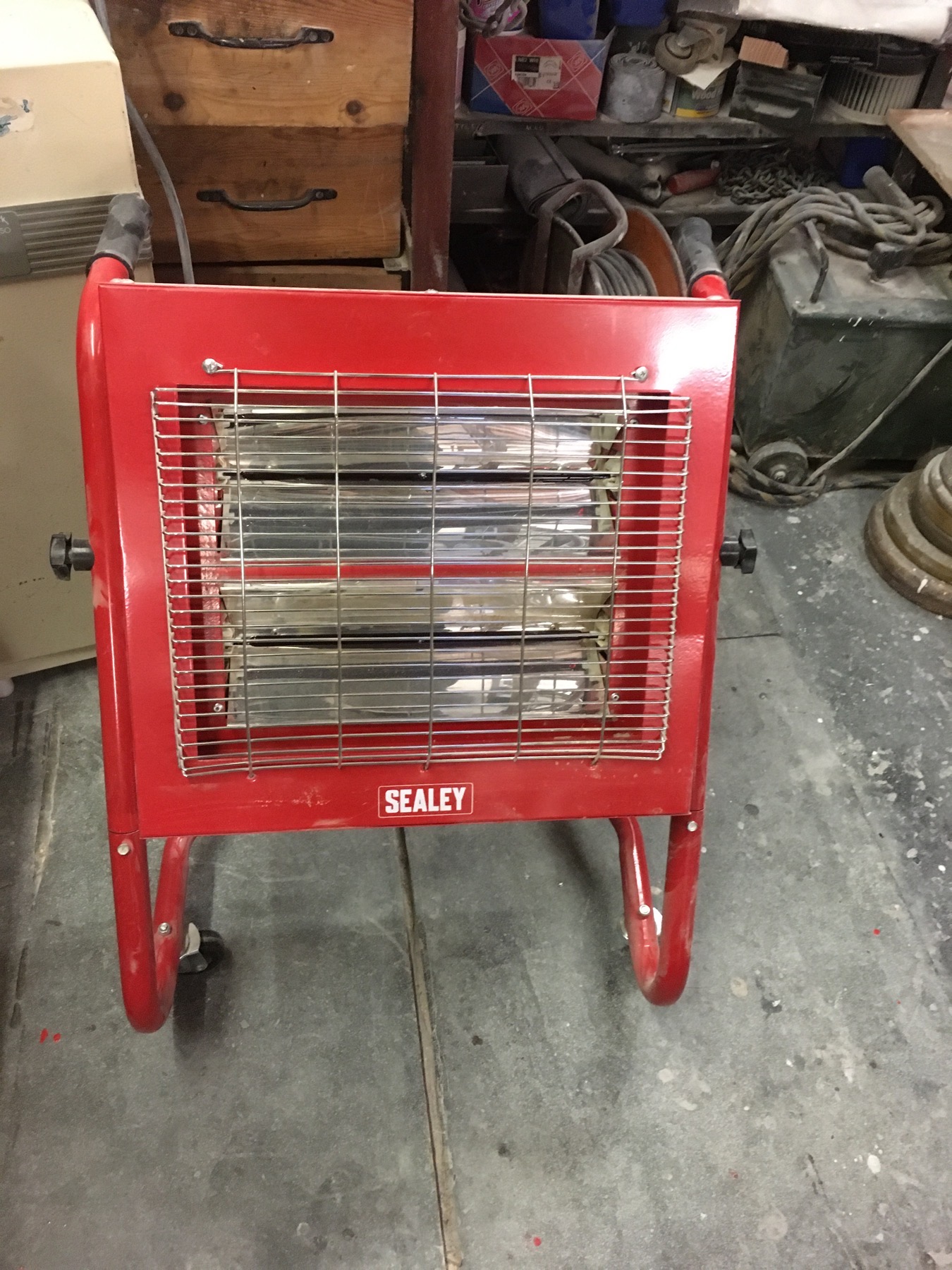
I also had to go cap in hand to Darren Spinage at our sponsor Trend for a part replacement on our new vacuum dust extractor for sanding the hull after I dozily damaged it pulling it around the hull so a big thank you to Darren for promptly getting us back up and running.
Three coats of our sponsor International Paints with their Perfection Pro primer along with sanding the hull between each coat turned the hull and myself a lovely shade of grey.
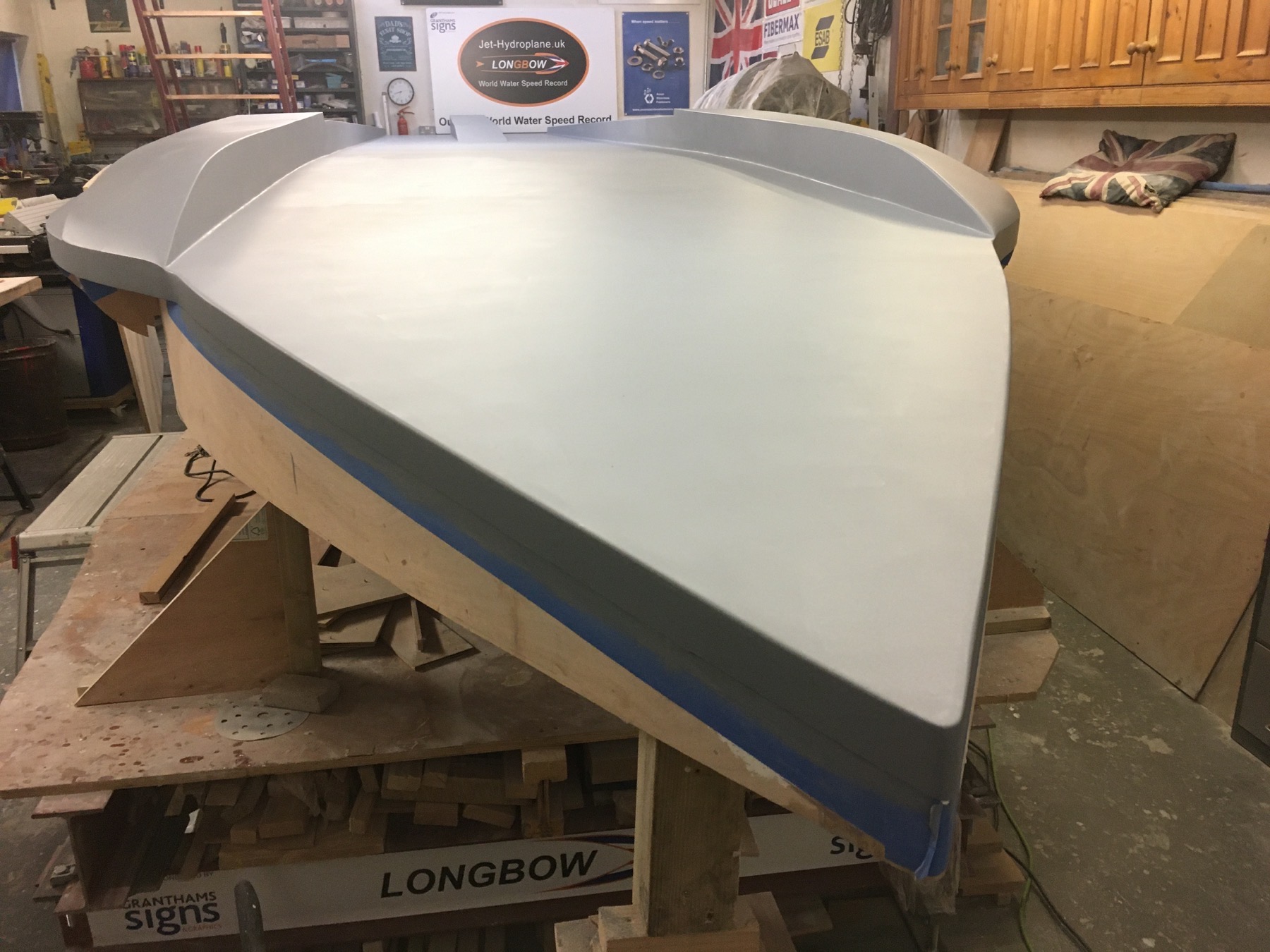
Then four coats of Perfection Pro undercoat sanding between each coat and we were back to white again.
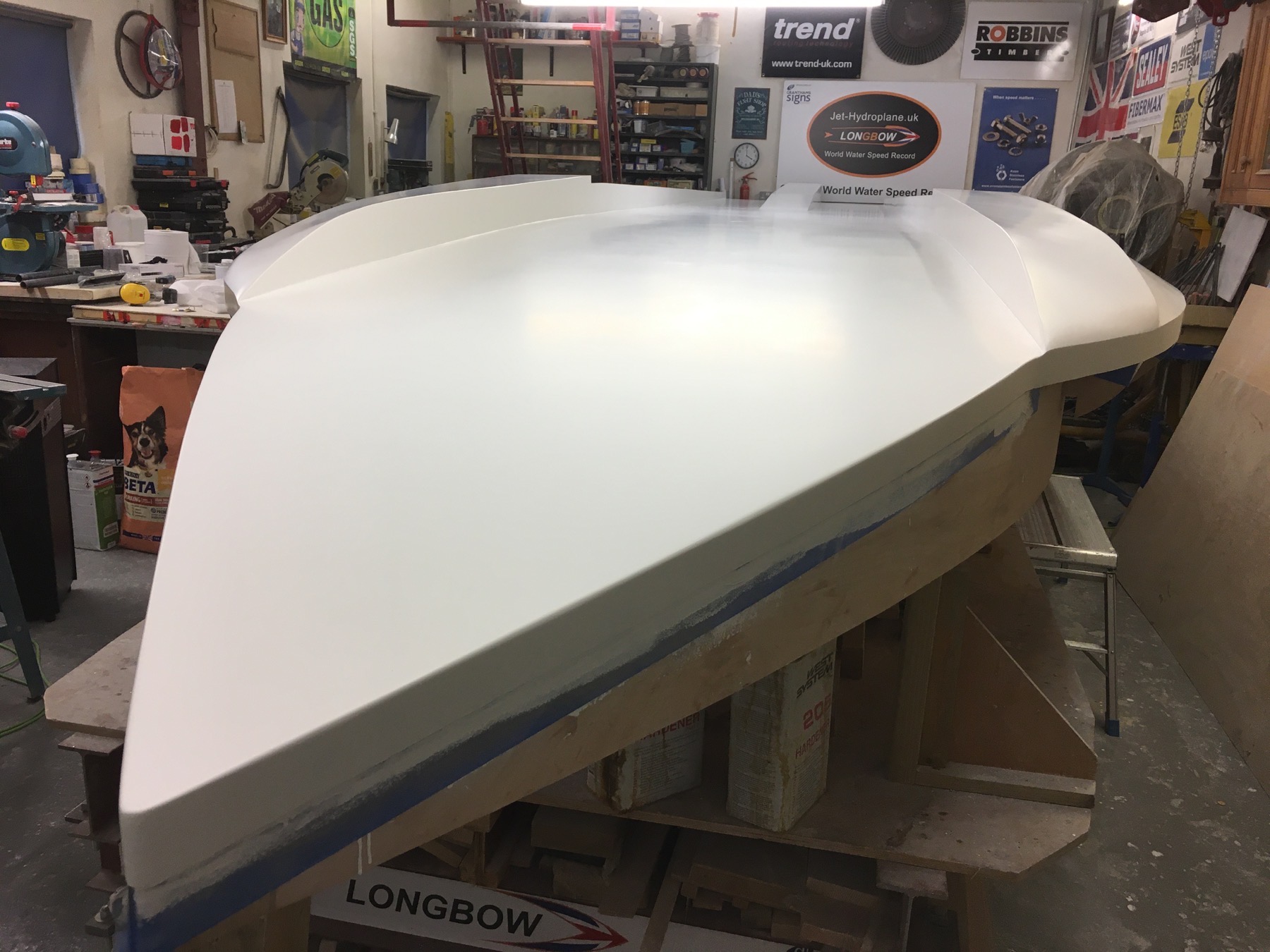
Having stripped the masking tape off and renewed it we then ready for the colour coats to begin and at time of writing here is the first one going on.
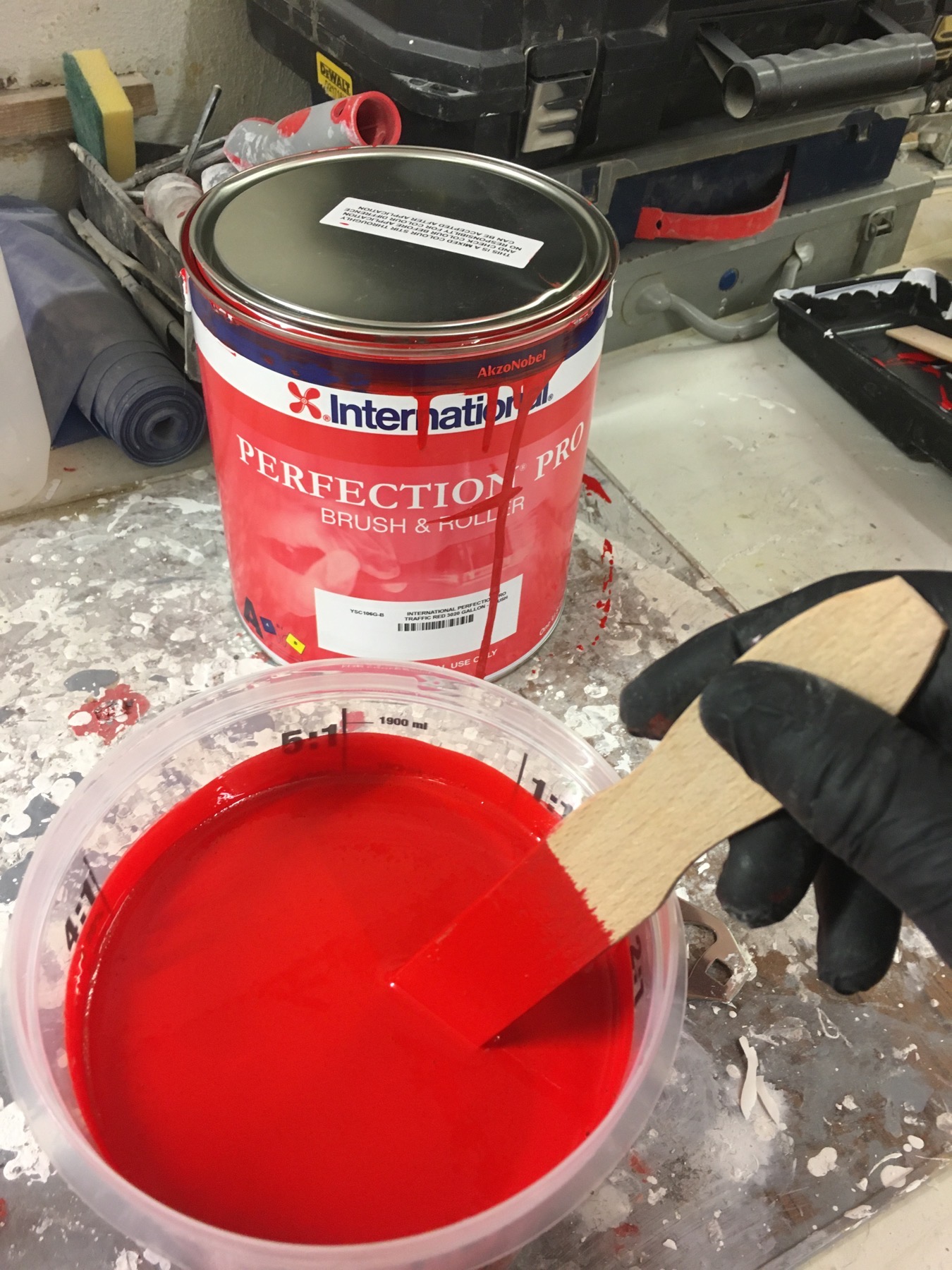
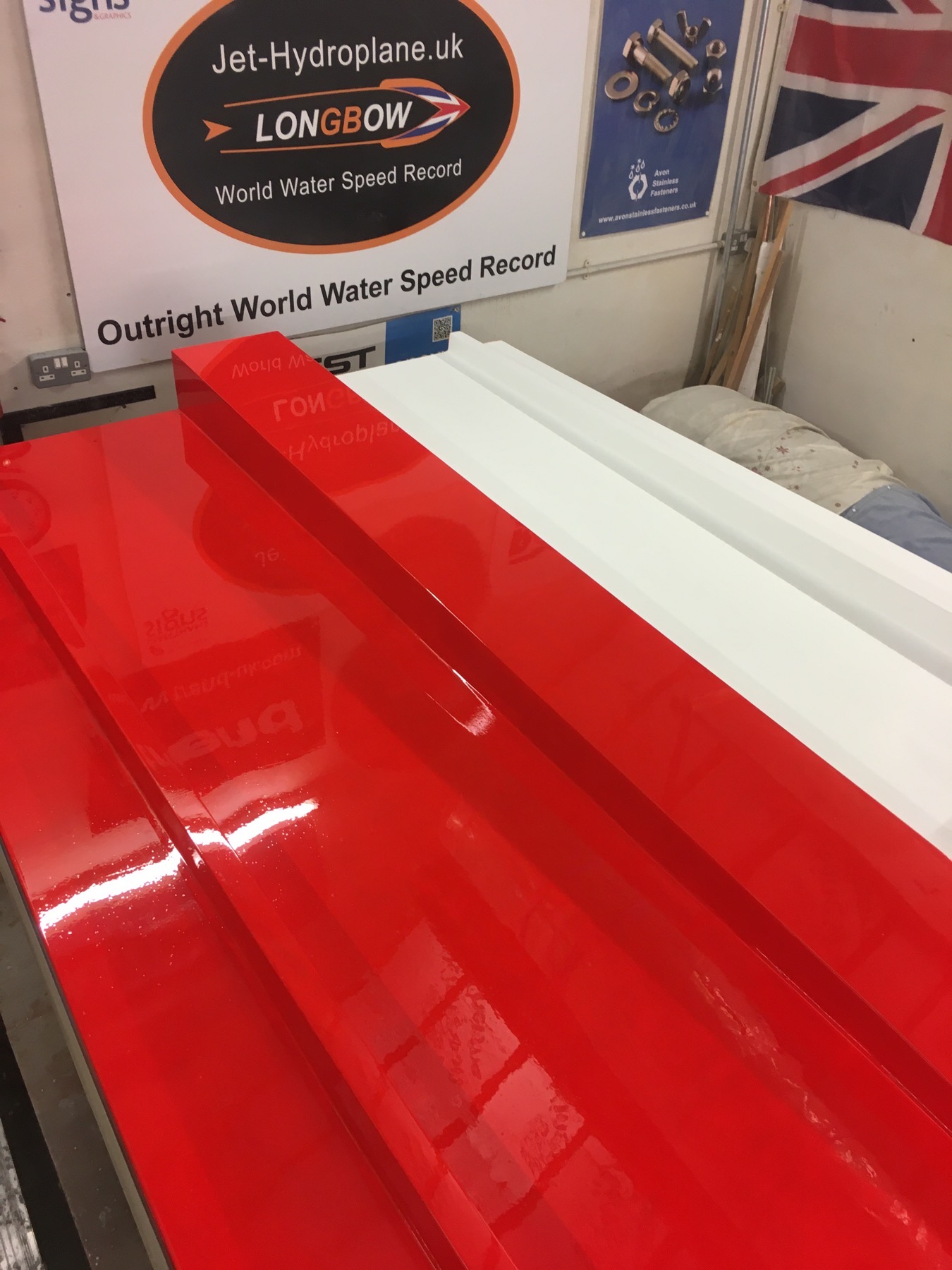
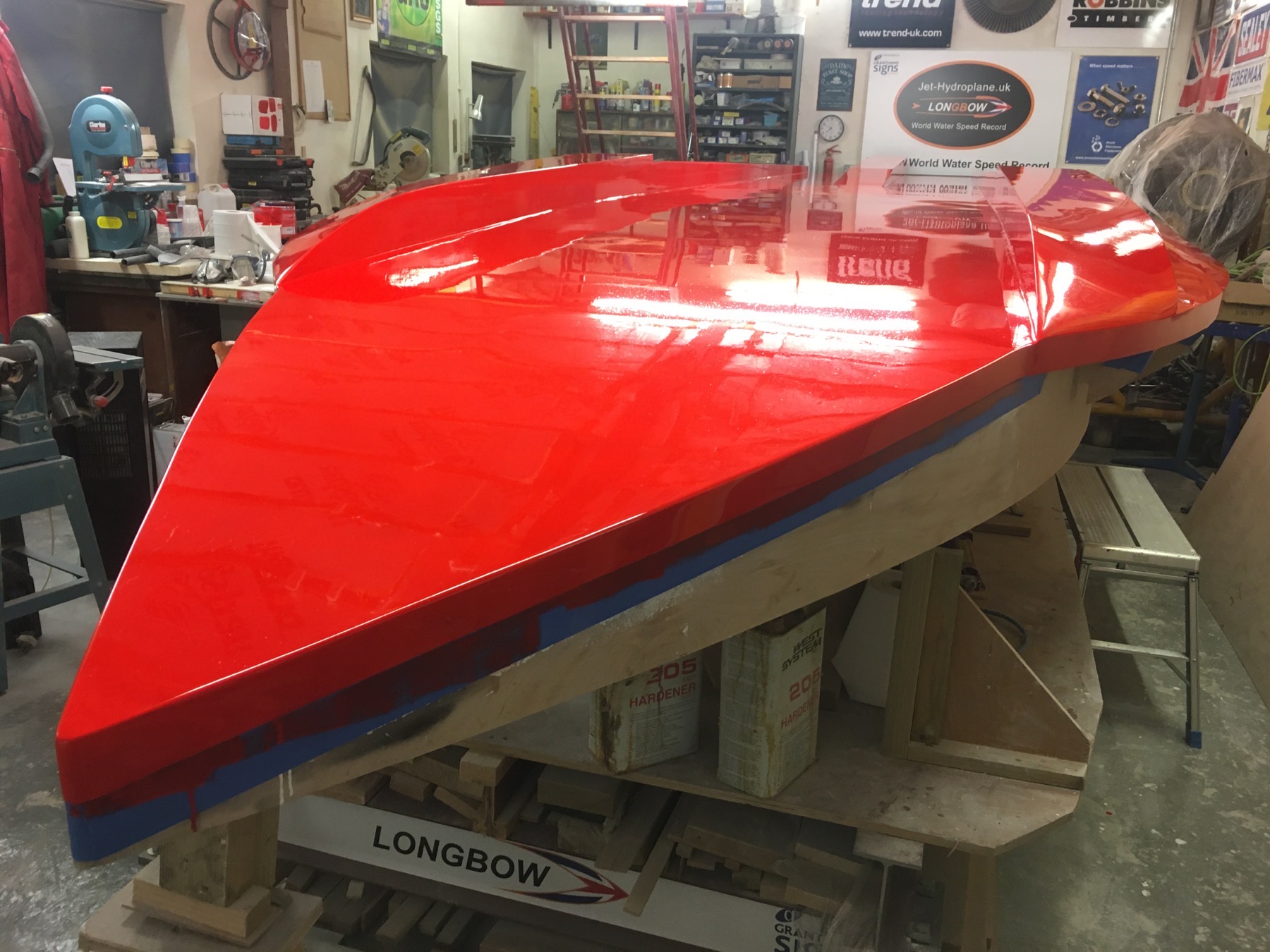
I hope you like the colour bearing in mind it is only the first coat so the white undercoat is still bleeding through to some degree. All I have to do now is sand the hull between a further two or three more coats to get a uniform colour of depth and reduce the amount of dust floating around during painting that gave too many inclusions in this first coat. For the colour coats I will have to wait 48-72 hours to harden enough to be able to sand between each coat and then once the last coat is completed leave it for a fortnight to fully harden off before I can think about turning the hull over.
Thank you for dropping by to read this little update and hopefully I will have some more paint and news on Longbow by the next update towards the end of December.