It appears that I must be doing something right as the fact I didn’t publish an April update due to an injured hand brought a lot of well wishes from those following our little venture which was both humbling and very much appreciated.
So last month saw me walk into an operating theatre at Spire private hospital with the surgeon all gowned up with anaesthetic and scalpel at the ready, only for them to ask what had I been doing as self treatment for this troublesome pyogenic granuloma, they were about to whip off appeared to them to be in the early stages of resolving.
Well folks as we all know YouTube has a video for everything these days so low and behold there was a clip of a doctor on there recommending a novel treatment of granulomas by taping a cap full of salt over the top of them 24/7 with daily refills to sort the thing out within a month. As luck would have it the surgeon I was seeing at Spire knew the doctor in the video and said let’s hold off on the surgery and see how the salt treatment pans out which was very good of them as private surgery is not the cheapest day out. If it failed to resolve then he would set up another surgery date.
A family friend who is a dermatologist said I was wasting my time with home remedy as did my sister who is a nurse but sure enough rubbing salt daily into an open wound as it turns out can sometimes be a good thing as far as granulomas are concerned and it has now thankfully completely healed so we are back in business. For those of a gruesome nature here is a before and after shot to put you off your dinner for sure.
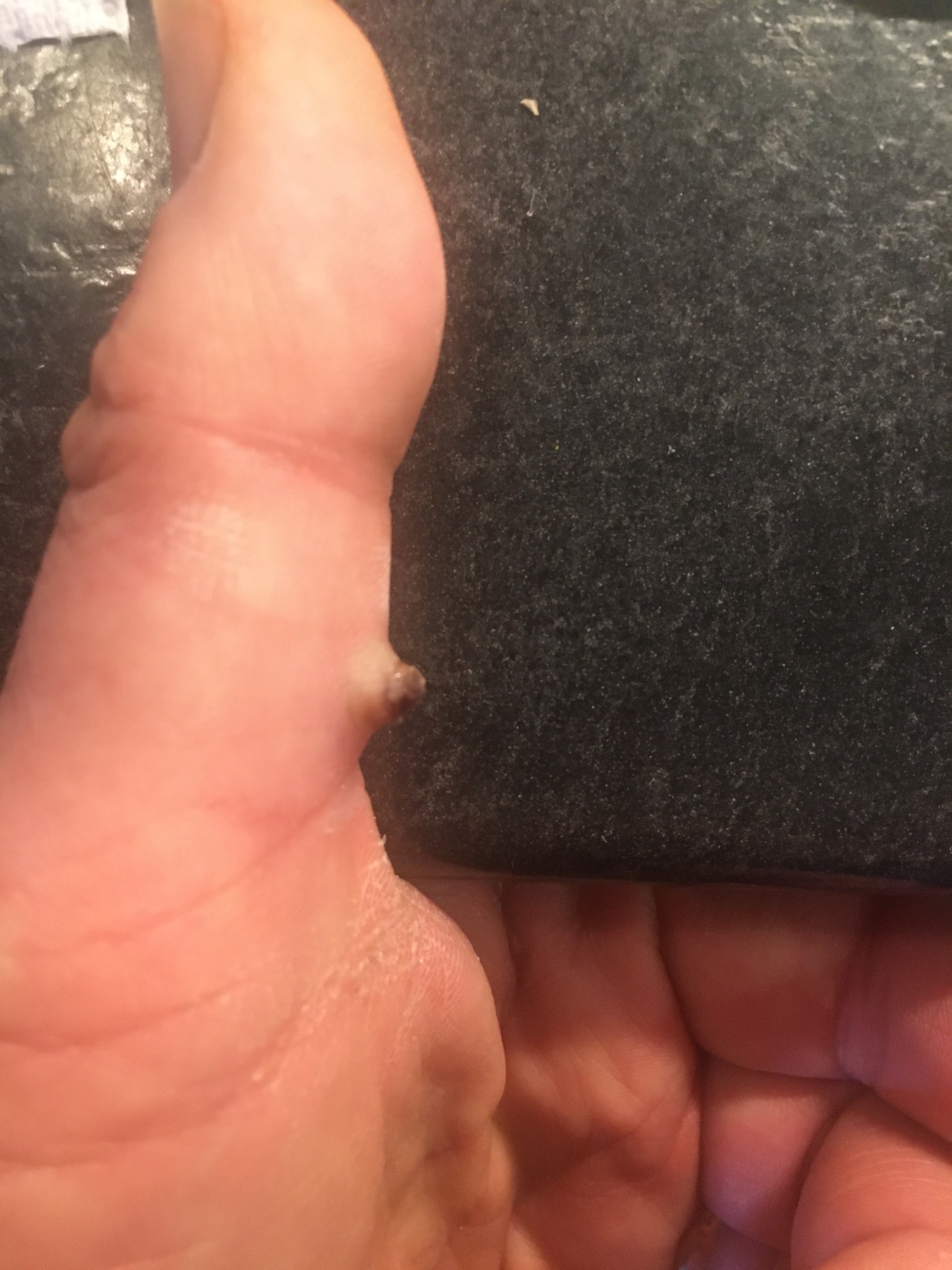
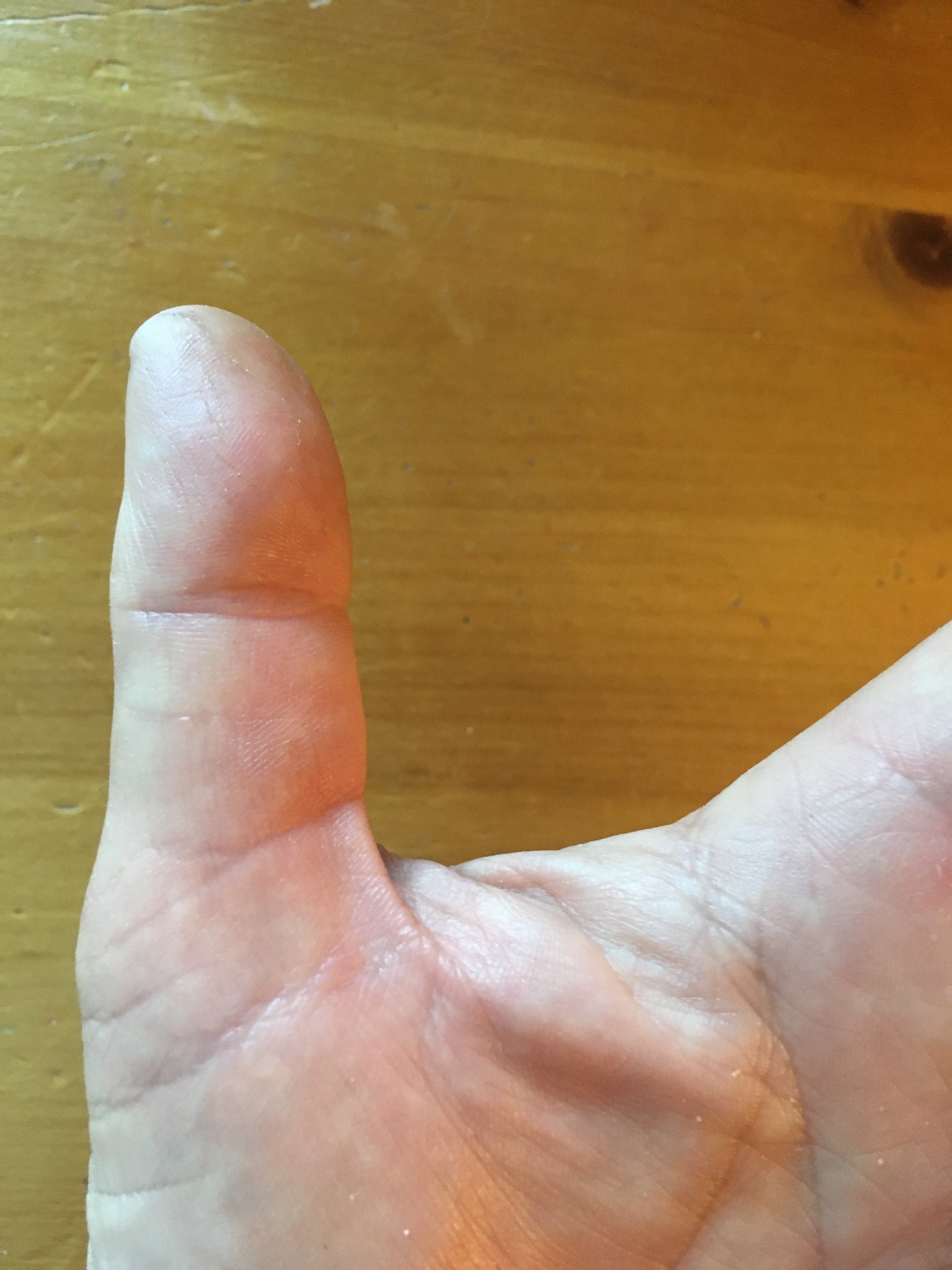
Anyway back to jet hydroplanes and this month saw our good friend Dave Warby and his team take their boat Spirit of Australia II back to Blowering Dam in Australia to continue their program of testing for their attempt at the Outright World Water Speed Record (fastest boat in the world) of 317mph. Dave and his team had undertaken a couple of changes to the boat since their last outing and were keen to see how these alterations translated into the handling of their jet hydroplane at high speed.
Unfortunately the weather was against them at this latest outing with strong side winds and periods of rainfall dogging their weekend at the dam. Nevertheless Dave managed to get a run of the craft at around 200mph and whilst it may have looked fast and steady from the shoreline he said the boat and himself were getting such a battering in the rough conditions that it would have been reckless to press on to higher speeds. Fingers crossed that their next visit to the dam will be under much calmer conditions to give them the feedback they need from the changes they have made to run the boat safely at higher speeds.
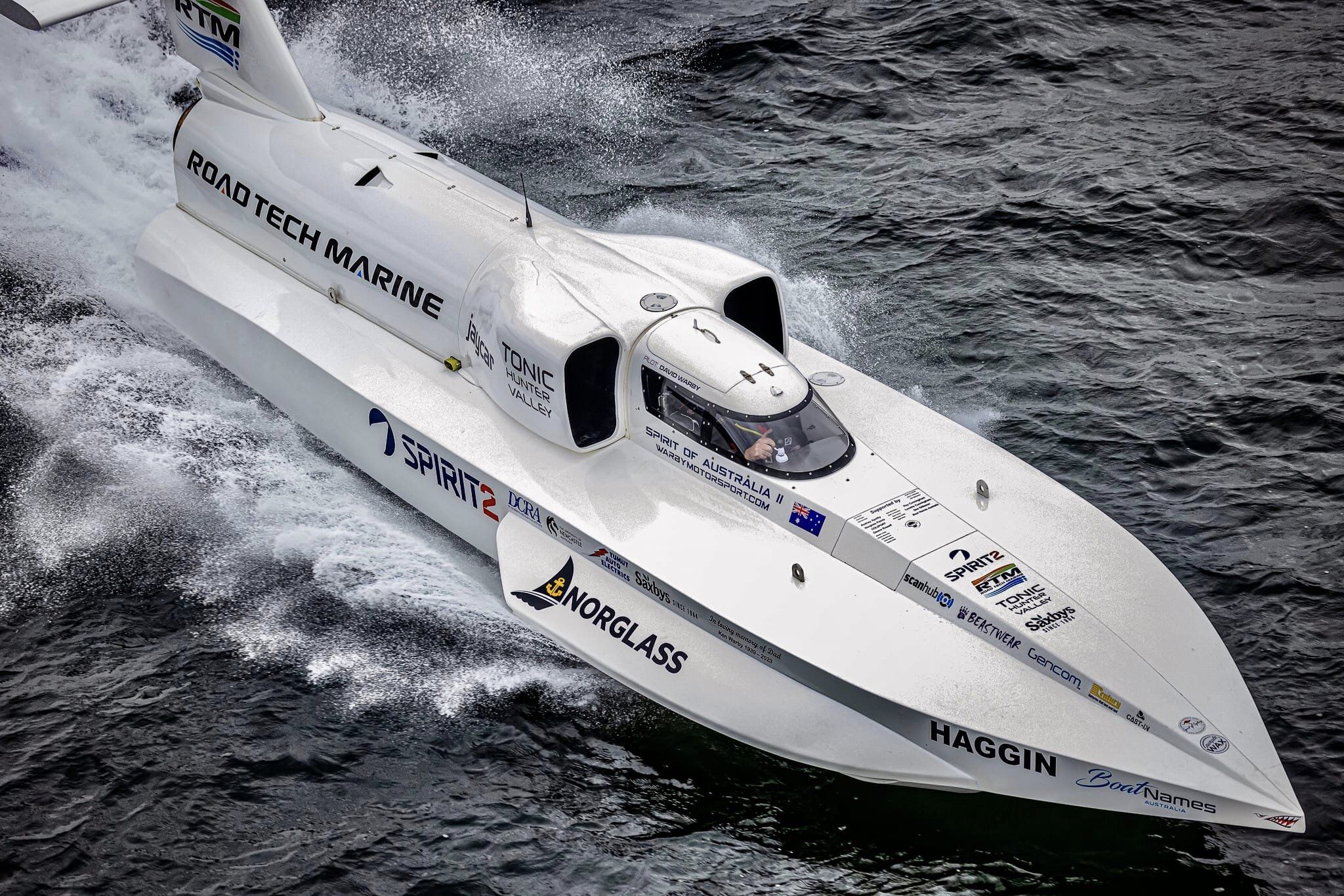
So back with Longbow and we had left off at our last update with the steel tubes for her engine cradle dropped loosely into the hull between the two main curved laminated timber stringers that form the backbone to the craft. The next job was to weld a series of metal brackets to those steel tubes of which every bracket was a different size / profile because the stringers are curved and from those brackets weld longitudinal steel plates to which we could then bolt the cradle onto the timber stringers with matching backing back plates.
The only way to do all that was with the metal engine cradle actually in position in the hull itself which was going to be awkward, uncomfortable and requiring some very skilful TIG welding indeed. Luckily for us we have our great pal Steve Charlesworth coded expert welder and TVR mad petrol-head who we are so very grateful for his commitment to getting Longbow built and running.
Steve came over and put in a 12 hour shift of TIG welding using our sponsor ESAB’s superb machinery and many thanks to our sponsor Allan Holly of SGS Gases for keeping us supplied with shielding gas for Steve to use whilst welding as the build continues.
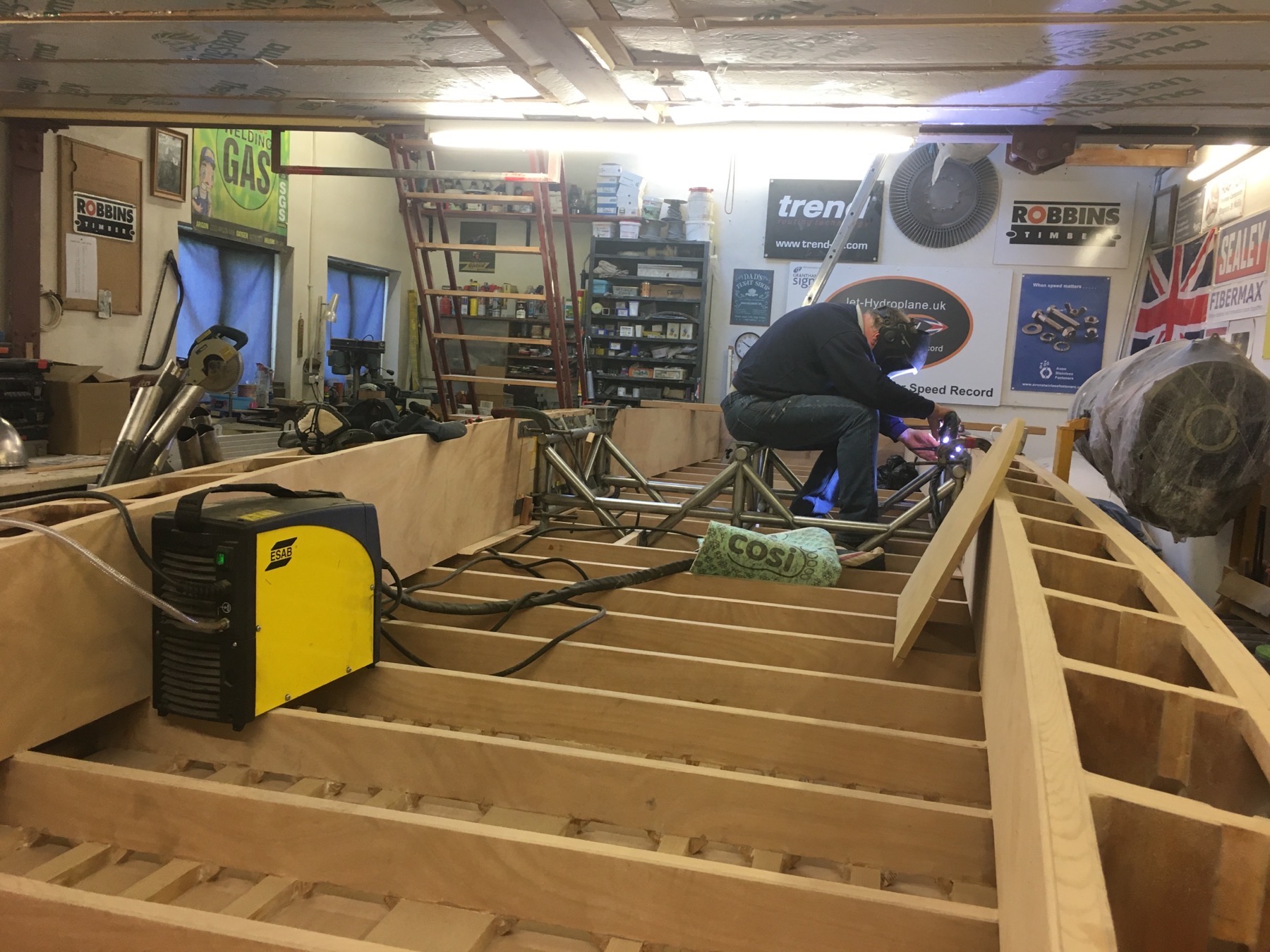
For my part in the meantime I used our sponsor Wessex Resin’s WEST SYSTEM Epoxy to laminate into place some very thin marine plywood packing from our sponsor Robbins Timber and then it was time to drill the steel base plates at the bottom of the engine cradle to receive the bolts. Our sponsor Sealey Tools supplying the cobalt (not the cheaper less effective cobalt dipped) drill bits for the task combined with cutting drill paste.
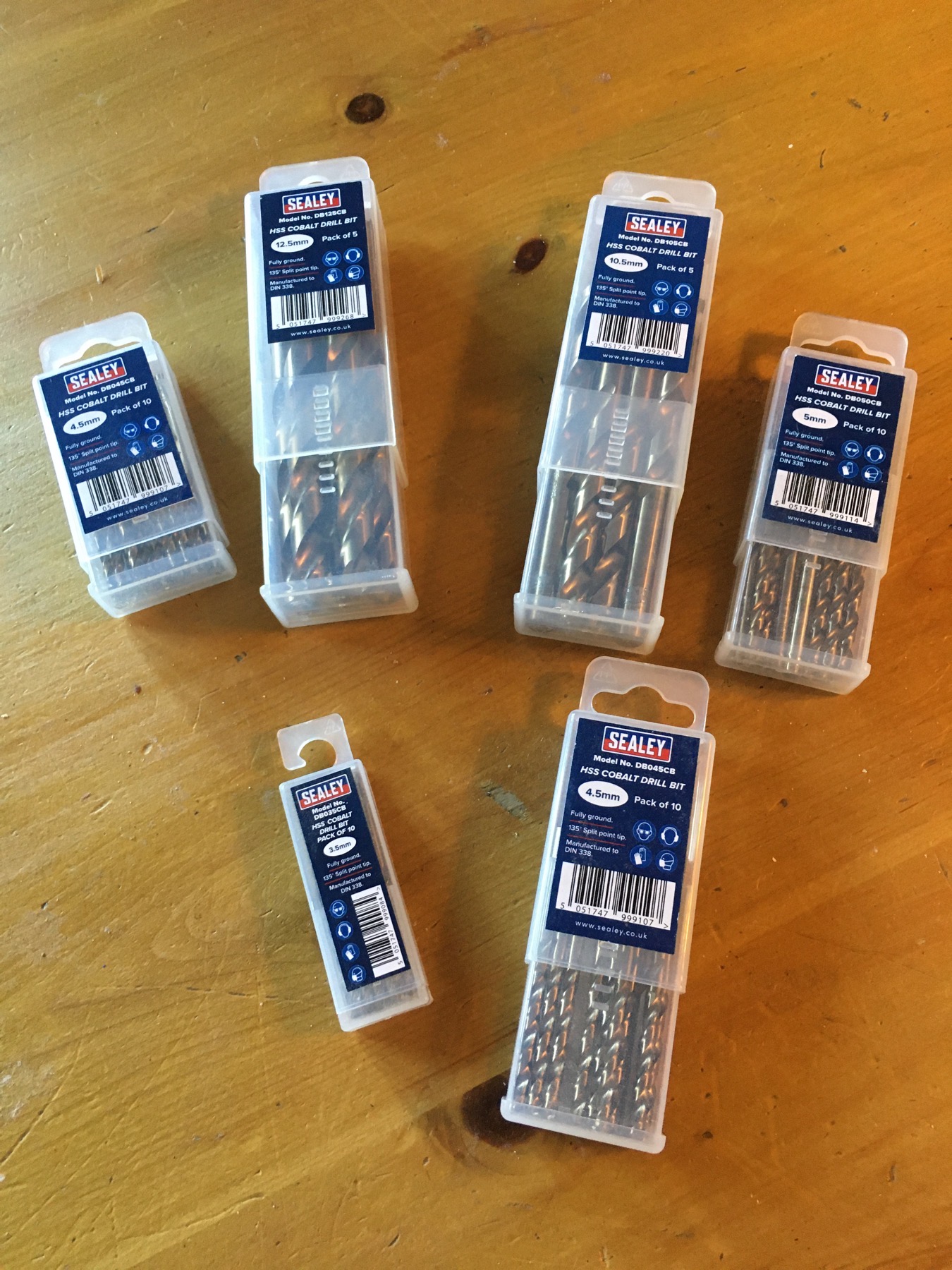
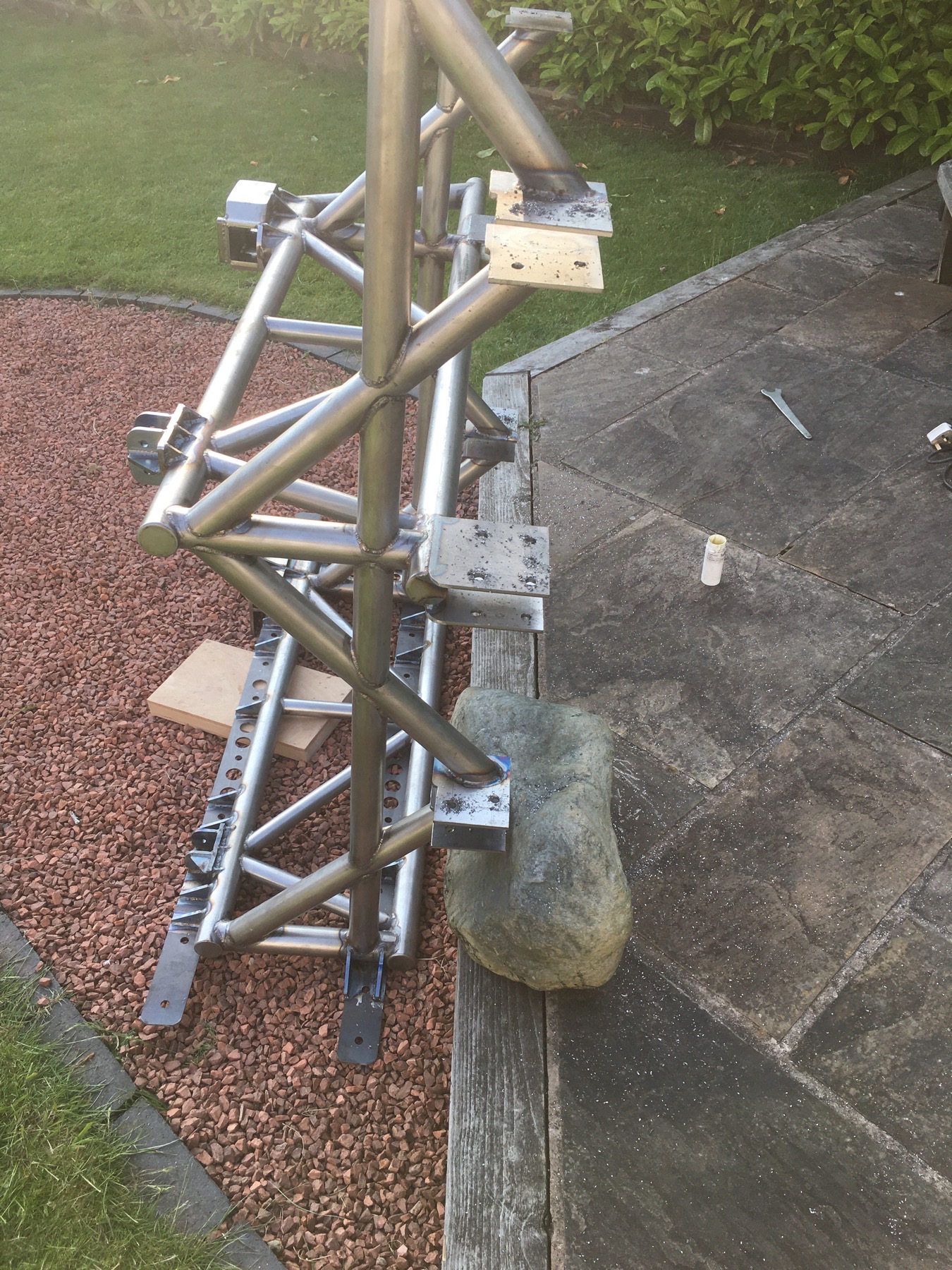
After the engine cradle was drilled we offered the cradle back into the hull of Longbow, made sure the cradle was level and then drilled into the laminated timber stringers and into the laminated timber noggins in the bottom of the hull previously fixed into place with WEST SYSTEM Epoxy.
Following on from that our sponsor Frank Canfield of Avon Stainless Steel Fasteners very kindly sent us a full set of bolts, castle nuts, washers and split pins to fix the engine cradle into place. There are a good few bolts involved and Henry our Standard Poodle stud dog was on hand in the role of foreman to ensure that only a couple of threads were showing for neatness.
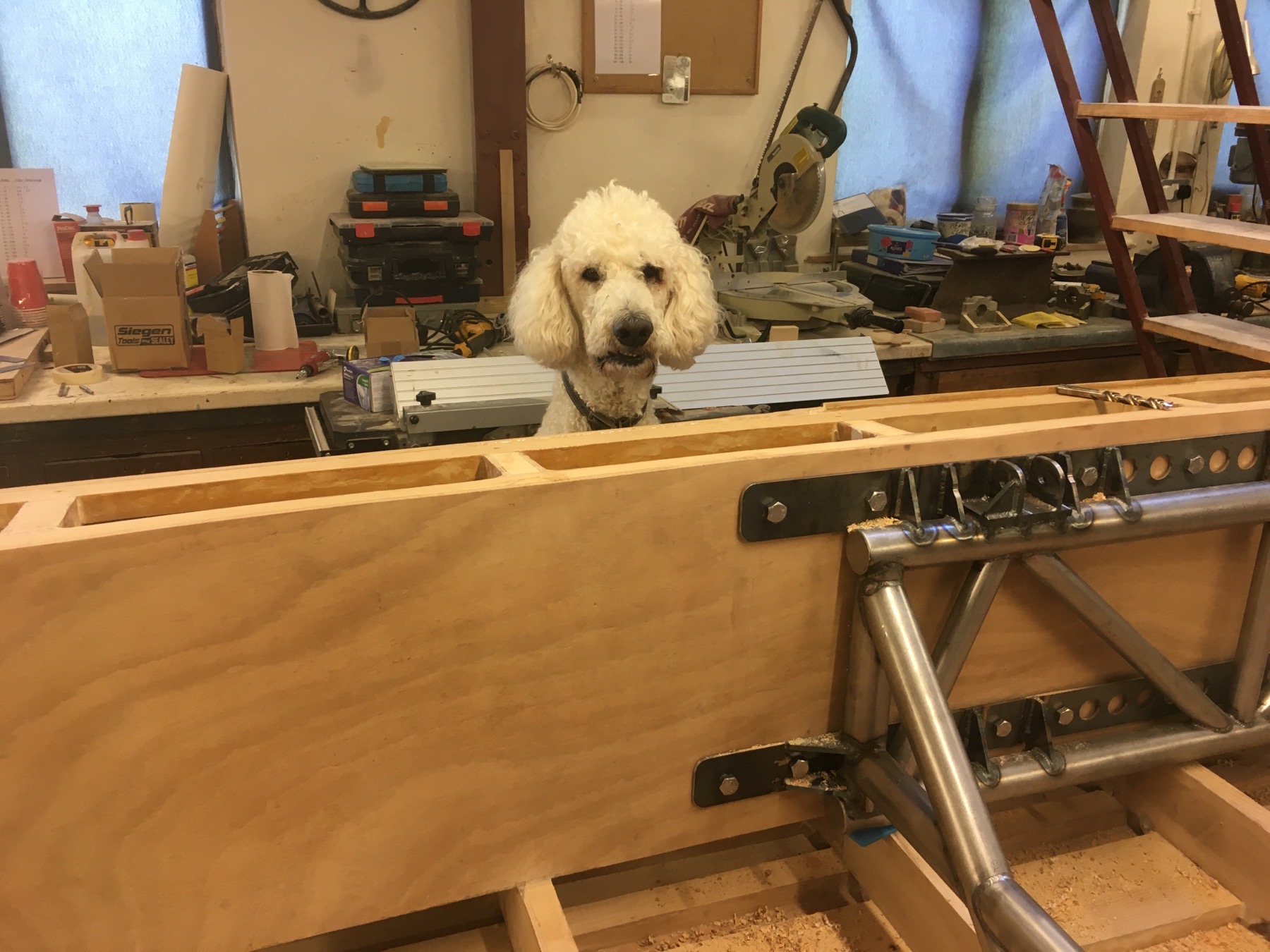
With all of that then done and with the sun shining it was time to see if one of our Rolls Royce Viper 535 jet engines would actually fit within one side of the jet engine cradle. This meant first carting one of the engines out of storage and winching it up into the air using the custom built Viper engine lifting rig from our sponsor Britlift.
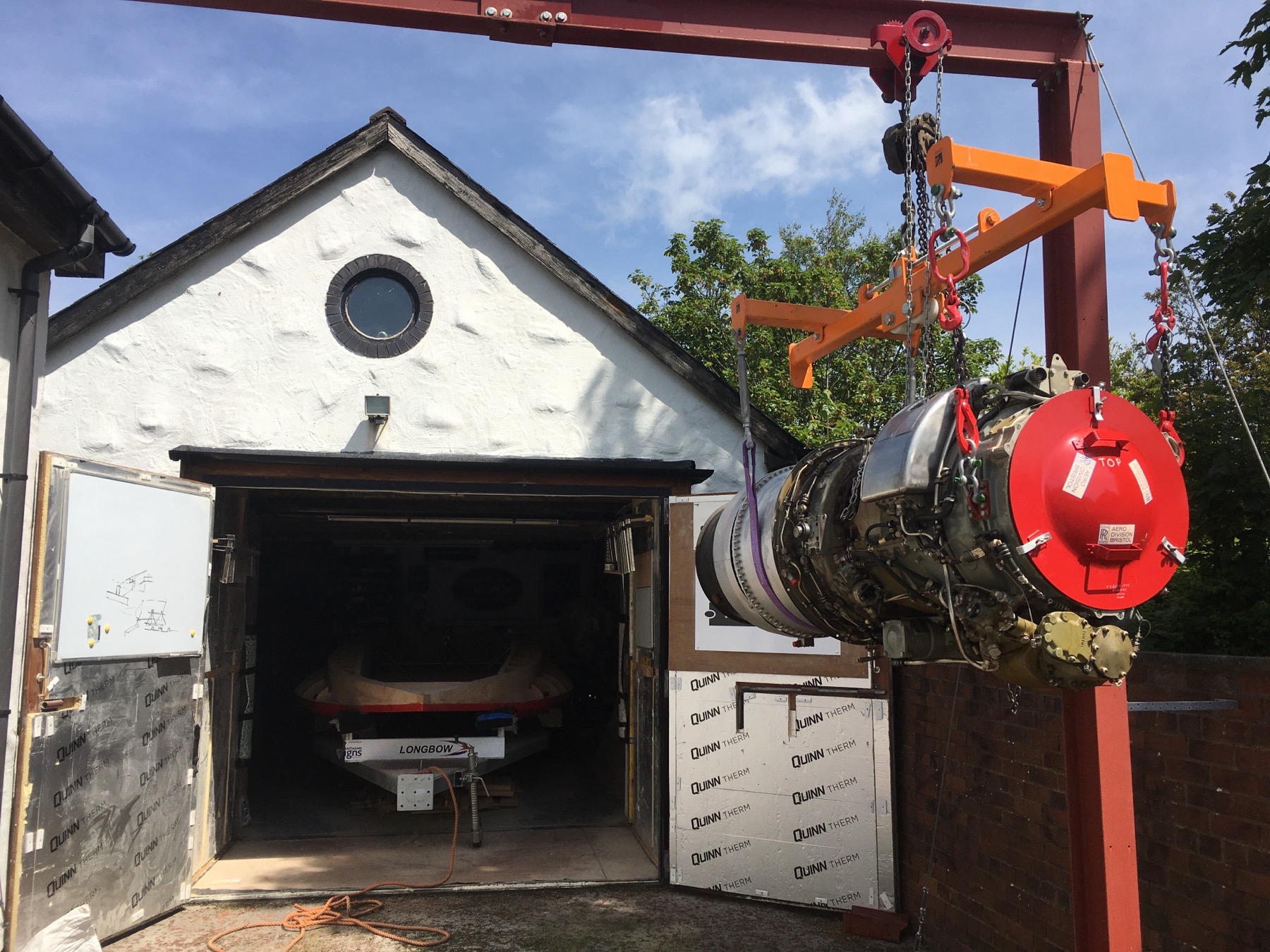
My two sons Robert and Tom along with my future son-in-law, Kieran did a fantastic job of carefully manoeuvring Longbow on her purpose built trailer out of the workshop to underneath the engine lifting frame and then began gently lowering the engine into the cradle that Steve had spent so much time and effort fabricating for us.
I had previously bolted into place the central engine trunnion mounting so that was the fixed point from which everything else had to fit into place but I could only pray that all my measurements had been correct and the trunnion on the other side of the engine would land in the right spot; plus the engine itself would actually fit into the cradle. If it didn’t Steve wouldn’t be happy having to chop and change his fabrication and I would have received a roasting from the lads to say the least.
So with my heart in mouth and fingers definitely crossed the lads gently lowered and guided the engine further down into the cradle until it was fully seated. So did it fit? Your damn right it fit and all that time and effort spent measuring and checking the figures then re-measuring of the engine in its transport stand had paid off. So you can imagine my wife Gill saying the sheer look of relief of everything fitting as it should was written all over my face.
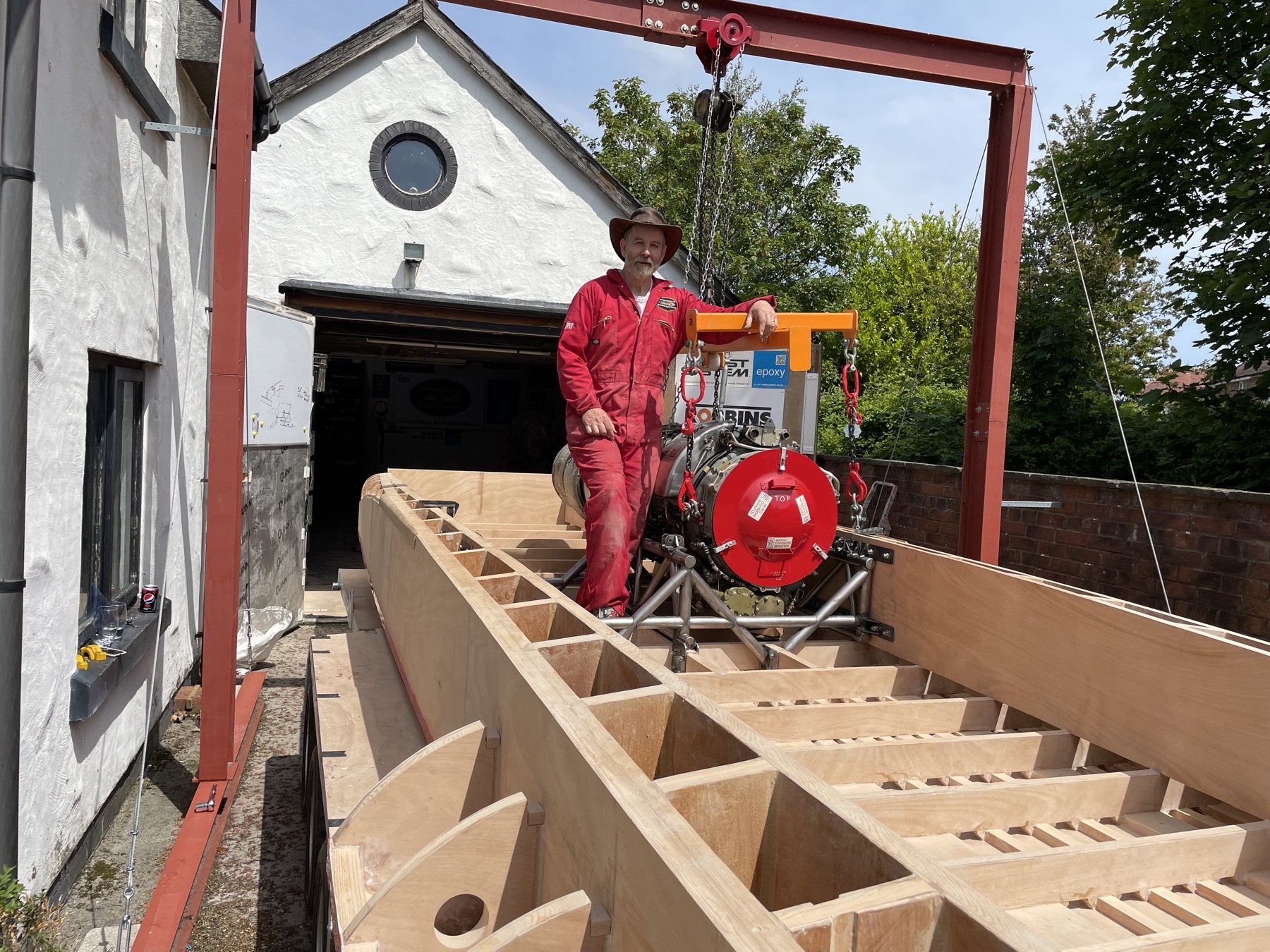
With the main engine sat upon its trunnion mounts in the frame we could then clamp on the intermediate jet pipe section from the Strikemaster aircraft and do a family photo.
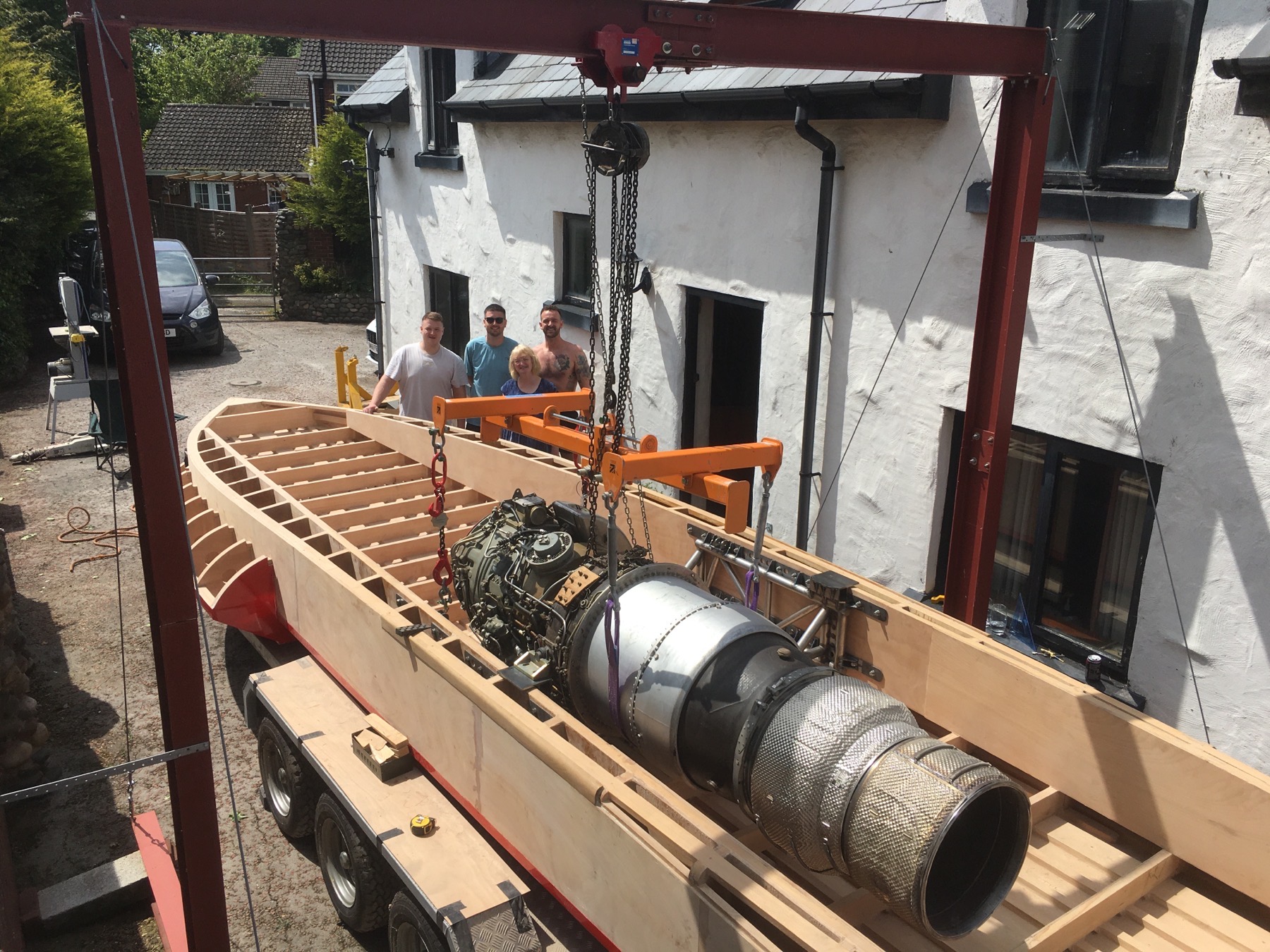
With that in place we could then measure the remaining length of jet pipe from the aircraft that we would need to cut down and Steve to weld so it terminates at the end of the boat at the point that we desire.
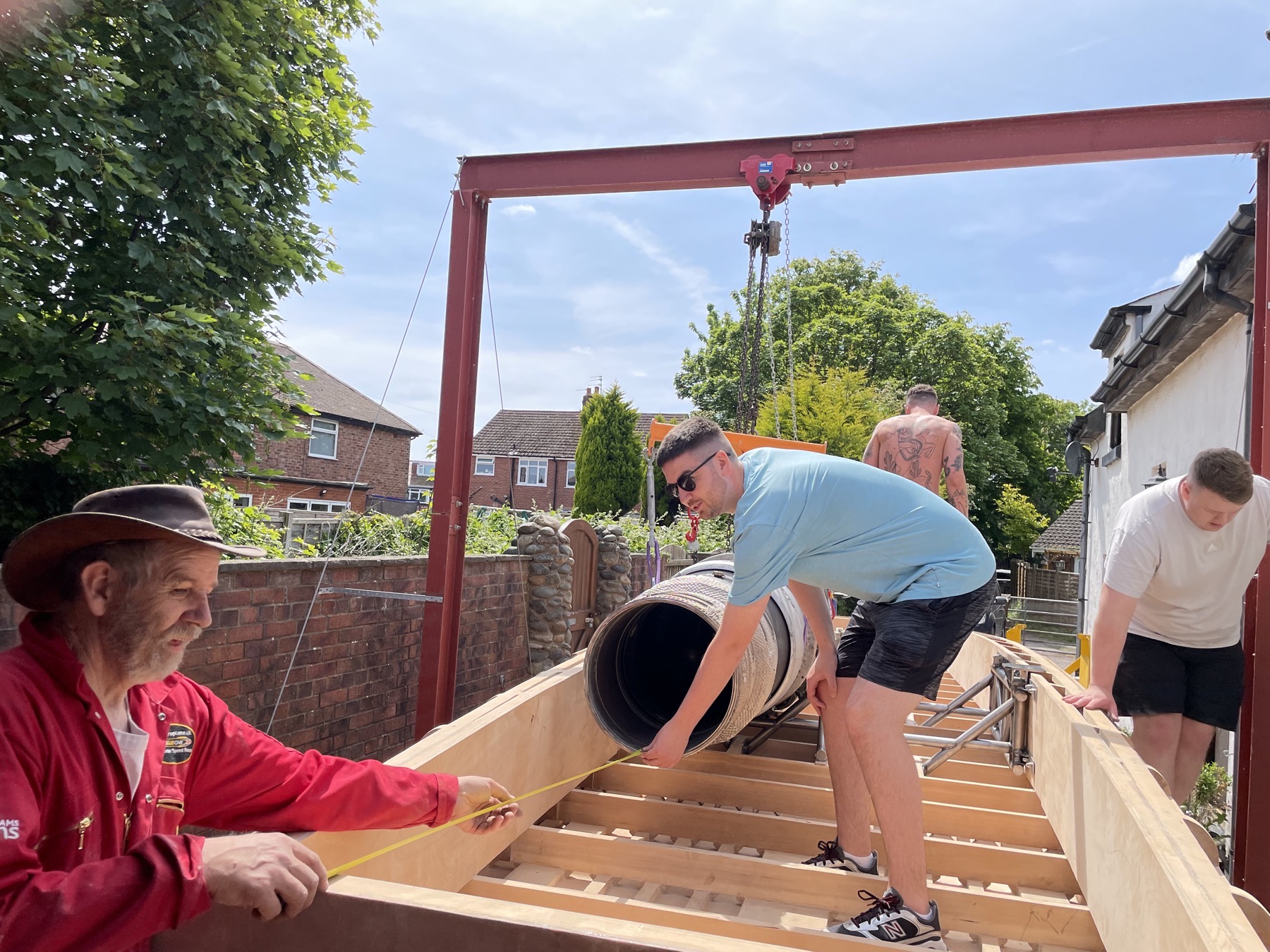
Meanwhile at the front of the engine we could now measure the length of turnbuckle required to make the connection from the engine cradle to the mounting point on the engine which in turn dictates the angle of thrust of the engine.
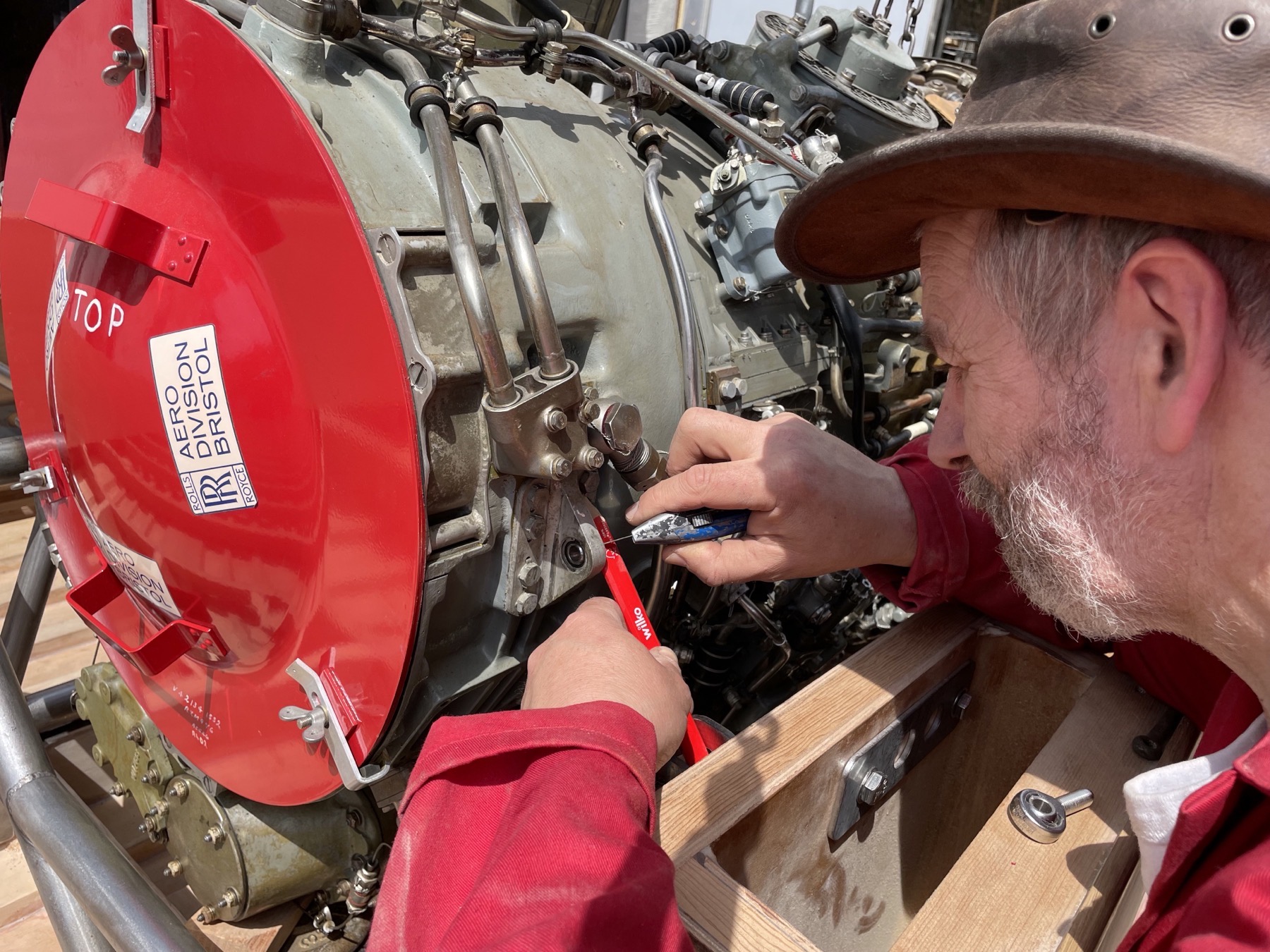
With all the measurements taken the lads were enjoying the sunshine along with plenty of banter before it was time to take the engine back out of the frame and return it to storage along with pushing Longbow back into the workshop.
Next on the to do list is painting the engine cradle now we know the engines will fit into them correctly as intended. I had thought about powder coating the frame and I know there are different types of powder coating but my experience of them all over many years is that powder coating often cracks and you get corrosion going on underneath the coating hidden from view. Also if you need to say weld in another bracket or drill another hole to the frame, or scratch the frame in the times ahead then it is difficult to make good the powder coating finish whichever type has been applied.
For all of these reasons it is better in my view to revert back to a standard spray applied vehicle paint of a type that is resistant to jet fuel and has anti-corrosion properties rather than powder coating. This being the case our paint for the cradle has been generously supplied by our sponsor HMG Paints of Manchester with special thanks to Tony O’Connor, Graciene Ikin and John Fenton for their superb ongoing technical advice and ongoing product support.
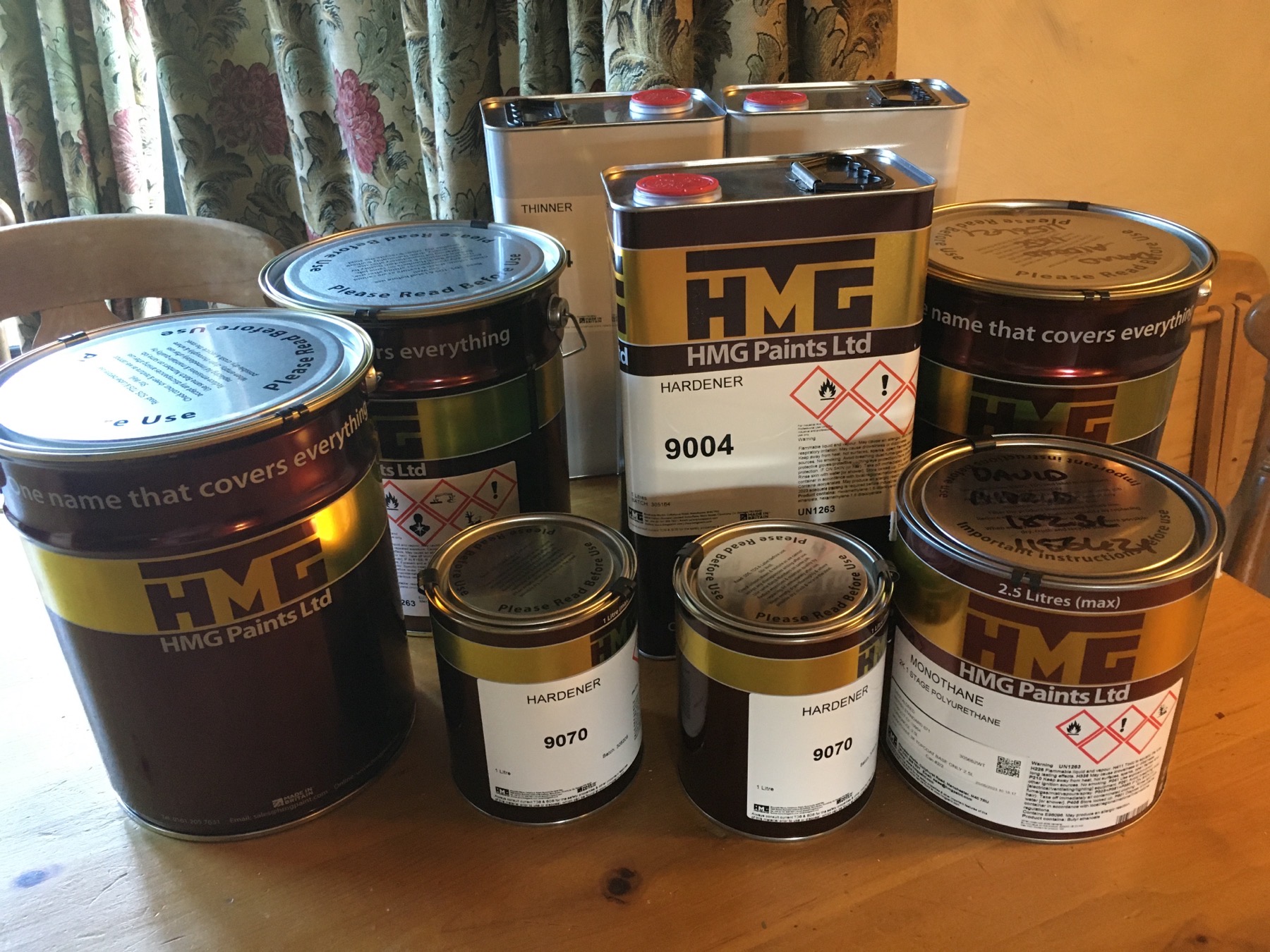
Blackpool & The Fylde College local to us who are one of our education partners had previously said they would spray paint the cradle for us but with their paint lecturer on long term sick with no indication of a return date, the task has fallen back to ourselves. Thankfully Steve Buckle Purchasing Director at our sponsor Sealey Tools came to our rescue by way of sending us their fantastic Premier HVLP (High Volume Low Pressure) gravity feed spray gun with a range of nozzle / needle sizes, along with their Premier HVLP touch up spray gun, in-line water trap / filter and on-gun air pressure regulator / gauge.
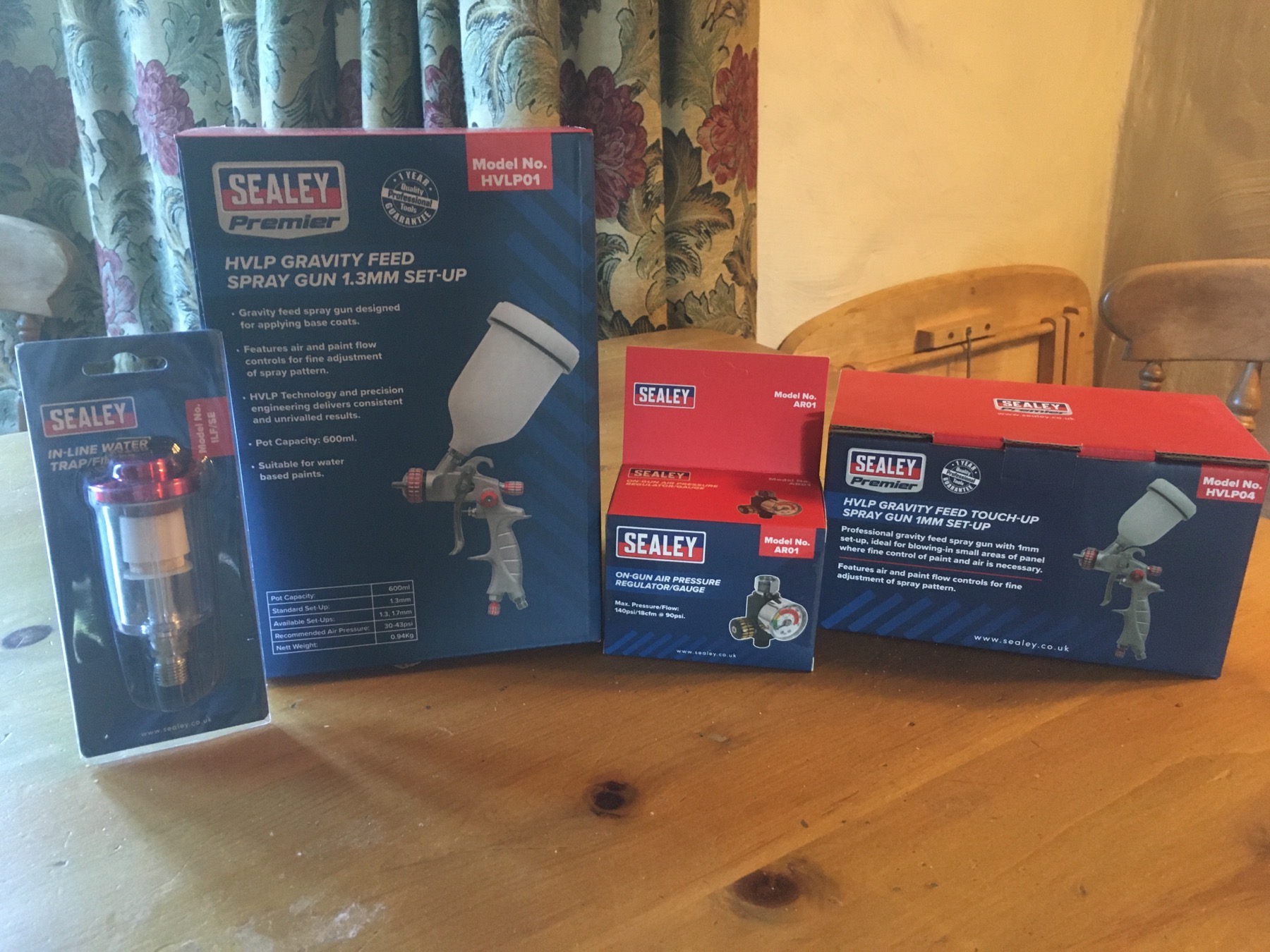
Steve and Sealey have been supporting us from the outset and I really cannot thank them enough for all that they do for us in making the venture happen with their superb equipment that gets some very hard use in the workshop but never fails to impress with its quality and performance.
Well that is all for this month’s update folks. Now my hand is sorted it is great to be back on with the build and we cannot wait to have both of Longbow’s jet engines fitted into the hull shortly. Thank you once again for all your good wishes and terrific support in making our little venture happen. If you have not done so already please like our Facebook page and drop by towards the end of next month for the next update on progress as we build our jet hydroplane Longbow to run and develop on lakes and lochs in the U.K.