We begin this month’s update with the exciting news that David-John Gibbs (who is the nominated driver for our jet hydroplane Longbow), has been selected by the RAF for this year’s Grob aircraft tutor display team. So our congratulations to DJ and please give him a wave or say hello if you see him on the display circuit this year:
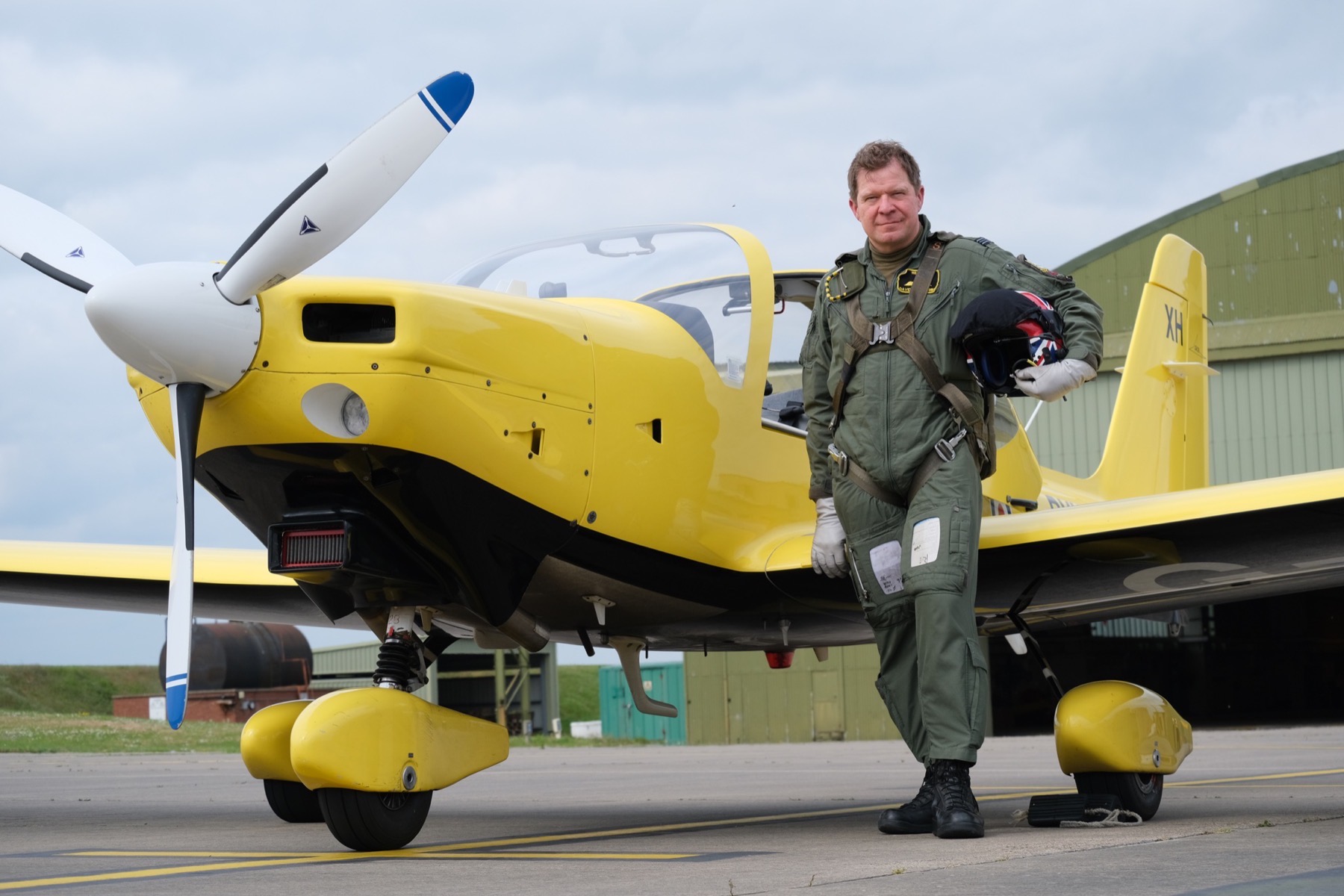
On a separate note as a parent when thinking of how many children to have, may I suggest trying to strike a balance between enough to help you out with tasks when you may need them in later life and how much time you are going to have spend at each of their homes when they fly the nest doing jobs for them in return.
When I built the cottage we live in my four children consequently grew up in the comforting knowledge that a pleading face that only a child can give their parent would be enough to have their dad doing any job they could think of at their homes. The upshot being this month I found myself fitting a kitchen plus integral appliances in one of my daughter’s and her fiancé’s house, which in turn prompted one of my sons having me fit an integral dishwasher and hanging up all manner of pictures, shelves and mirrors at the home of him and his girlfriend. Little did they know that this time and effort their dad was putting in to keeping them all happy was building up my leverage to ask them later in the month to help their old man out with our jet hydroplane project, Longbow.
With Longbow’s hull now the right way up and managing last month to generally clean the inside of her hull out of epoxy drips, she is now ready for fitting out of her twin Rolls Royce Viper 535 jet engines derived from the military BAC Strikemaster aircraft.
We therefore need to fabricate a metal cradle within the hull of Longbow to support her twin jet engines. In order to draw that cradle up to have it fabricated I wanted to take some measurements from one of the transport stands for those engines with preferably the engine removed. That in turn prompted me to think about how could I lift an engine out of its stand and at some point be able to put it into the hull of Longbow when there wasn’t enough height in the workshop for the lifting equipment to do that in the area of the mezzanine floor.
One of our sponsors Jack Sealey Ltd do a wonderful gantry ideal for most garage workshop engine lifts:
https://www.sealey.co.uk/product/5637198511/1tonne-portable-adjustable-gantry-crane
Unfortunately in our case it was just not wide enough to span the hull of Longbow on her trailer so I was going to have to make one of a suitable size. Fortunately we had some surplus steel beams from the grillage we had used to build Longbow upon prior to placing her on her trailer, so rather than scrap them it was time to do a bit of upcycling.
As any gantry we made would only be erected on a temporary basis I needed it to be in a form that would break down into relatively short lengths that could then be stored away when not in use. That being the case the first job was to cut the long heavy steel beams down into more manageable sections that I could then bolt together with various plates to form the gantry.
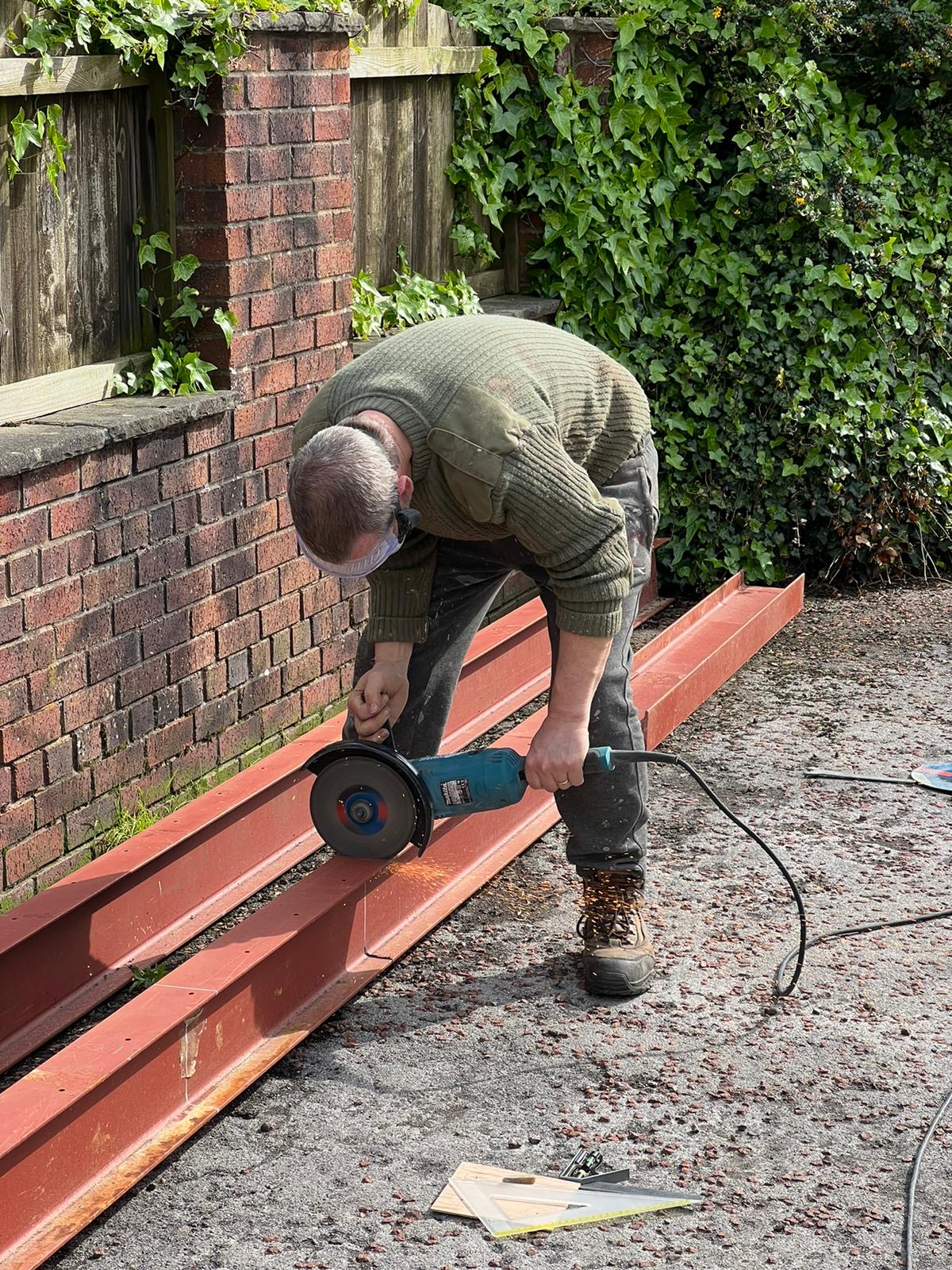
My good friend Howard Bryan who heads the Blackpool Thunder Car Club, put me in touch with one of their members, Steve Charlesworth who is a highly qualified fabrication welder of many years experience and Steve kindly offered to come over to our workshop to weld on some metal plates for the stanchions of the gantry we wanted to make. The following video shows Steve as he TIG (Tungsten Inert Gas) welded using our sponsor ESAB’s fantastic 240V AC/DC machine and our sponsor SGS gases providing the necessary shielding inert gas.
Steve Buckle Marketing Director of our sponsor Sealey very kindly sent us plenty of drill bits to aid with the fabrication process.
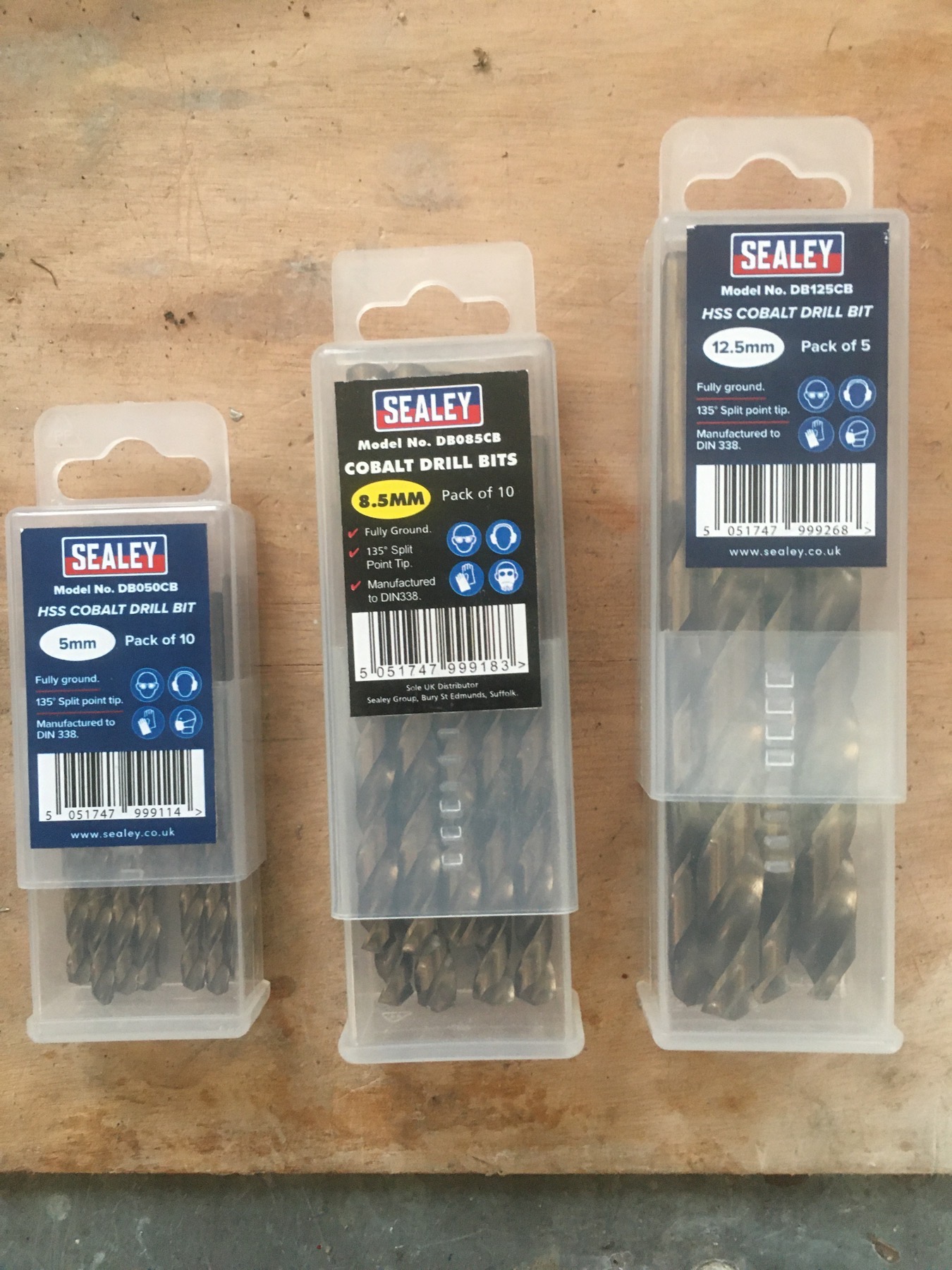
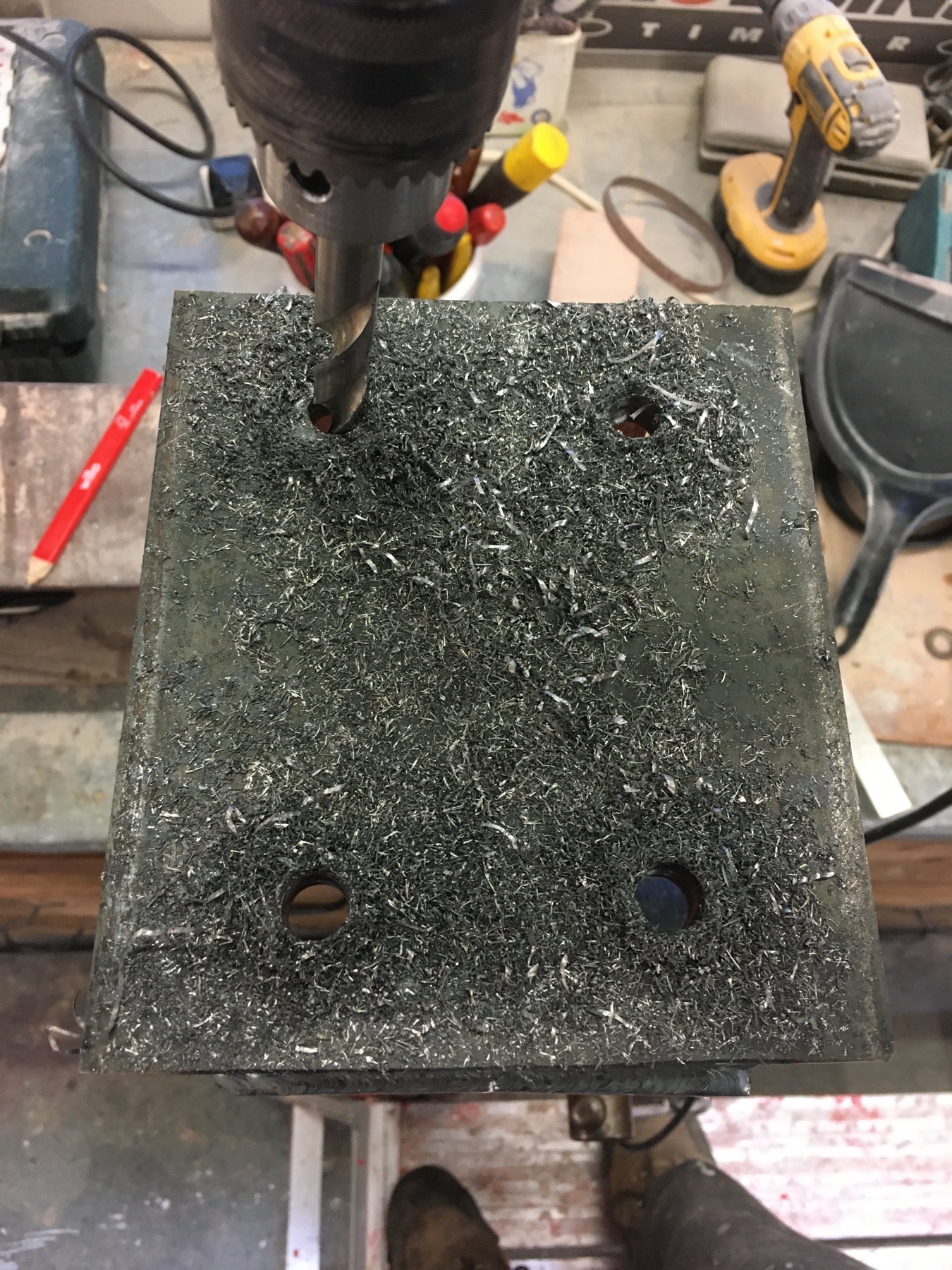
I was also able to upcycle the various nuts, bolts, washers and base plates previously used for Longbow’s build table, by cutting them down to the right size for the various gantry joints throughout.
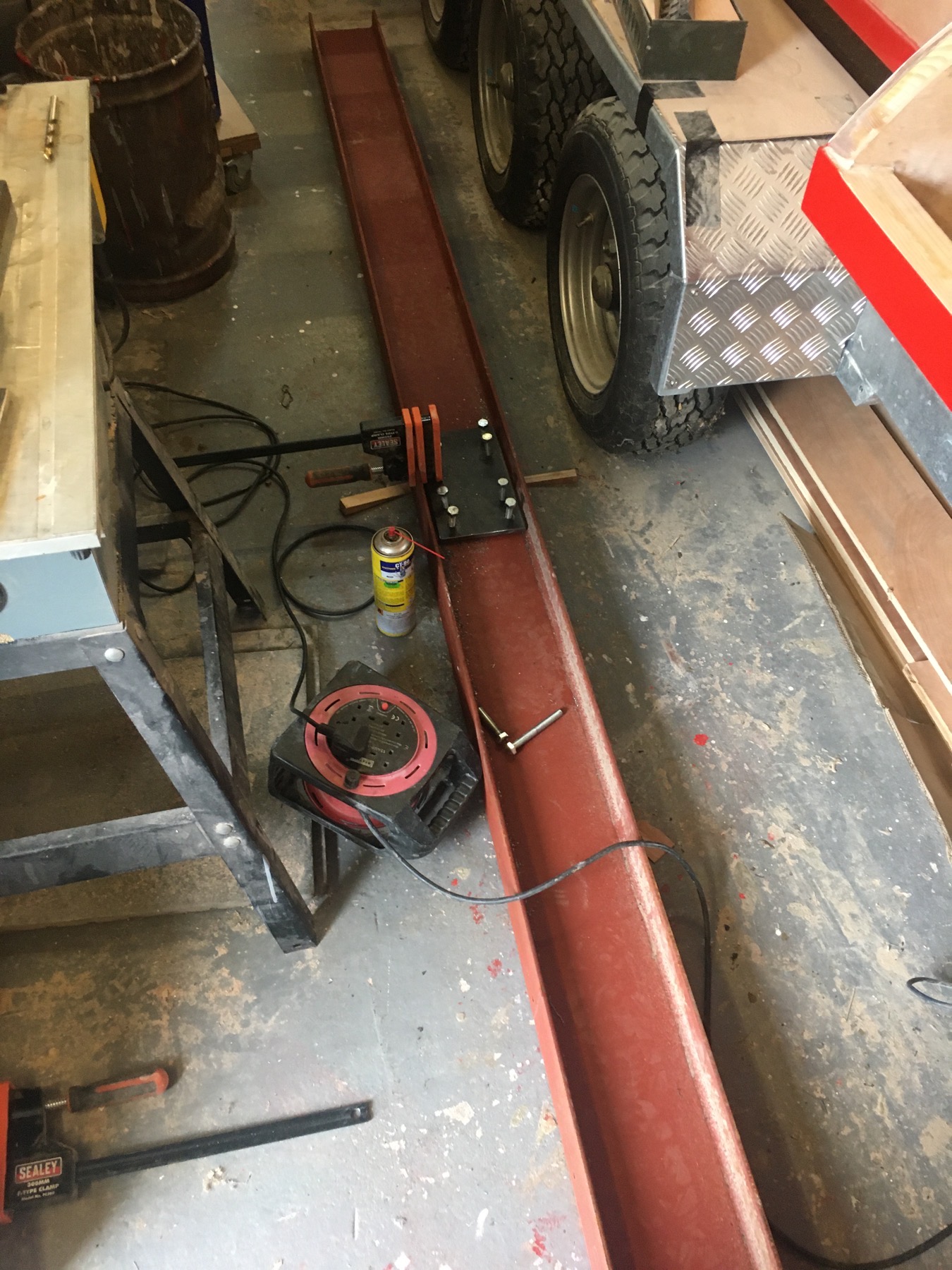
With all of that done it was time to call in the labour debt with my children / their respective partners to help get it all assembled. Fortunately from a relatively young age I have handled plenty of structural steel with my father and on various building sites, so it wasn’t my first rodeo with getting heavy steel up in the air without a crane or scaffolding and here is a flashback to the years before the grey hair set in.
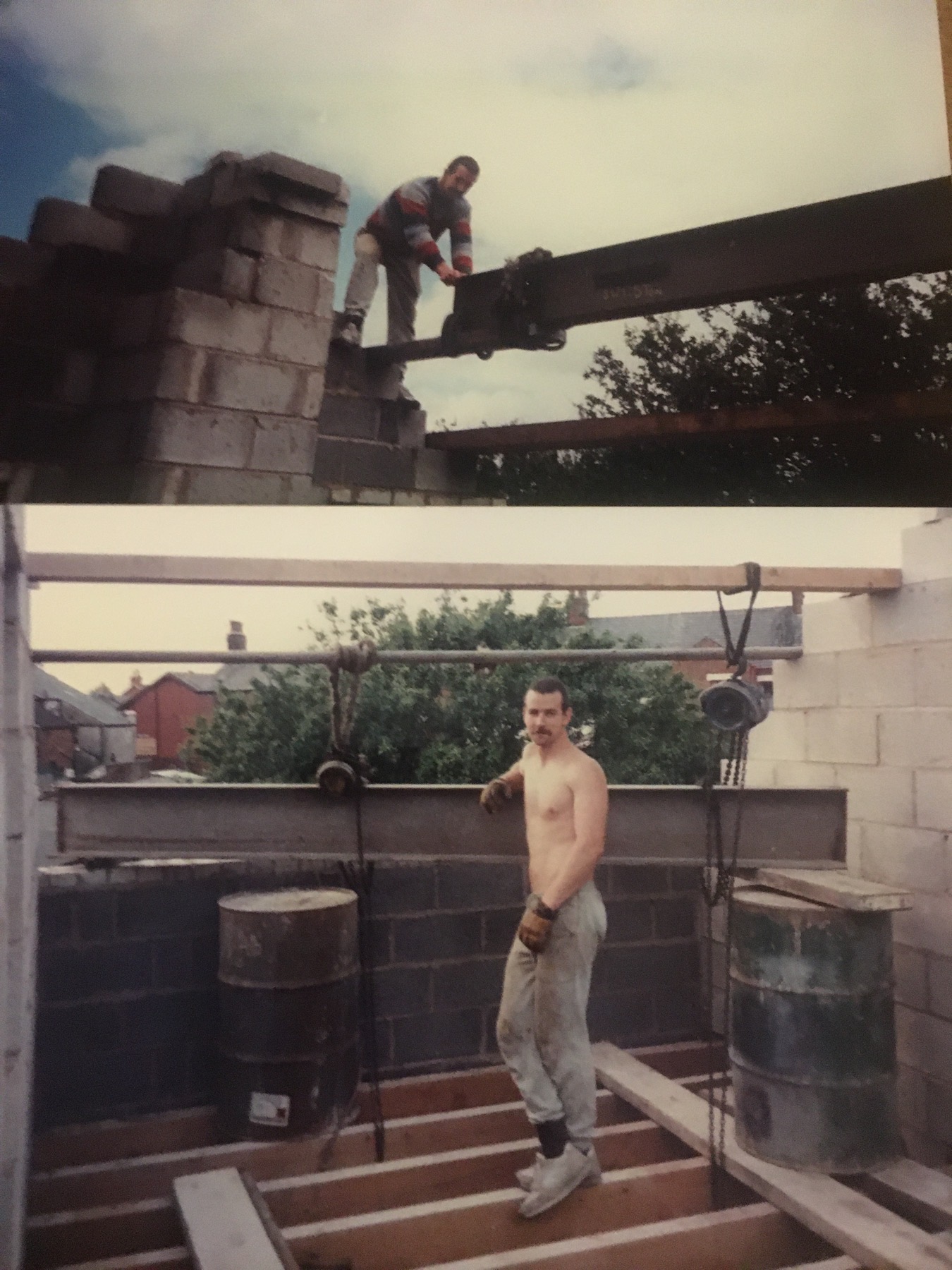
For the kids however it was something of a steep learning curve, rather like an outward bound team building exercise but with me drilling into them not to get in the way of structural steel if it starts to go anywhere you don’t want it to. So with Robert, one of my son’s hanging on to a section of steel beam on a rope through the cottage bedroom window, the rest of us took our places on the ground or balancing on the garden wall and up it all went very smoothly.
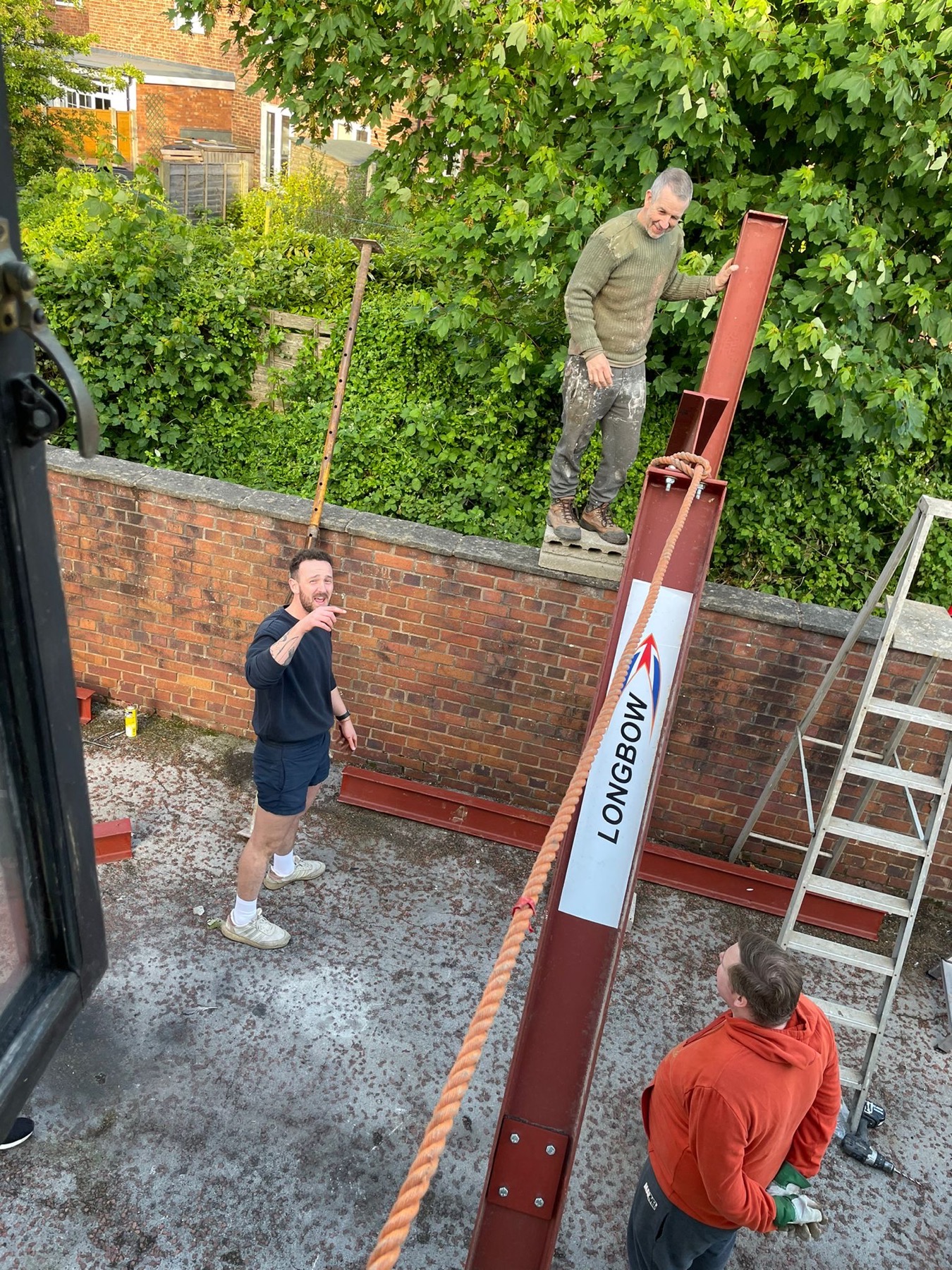
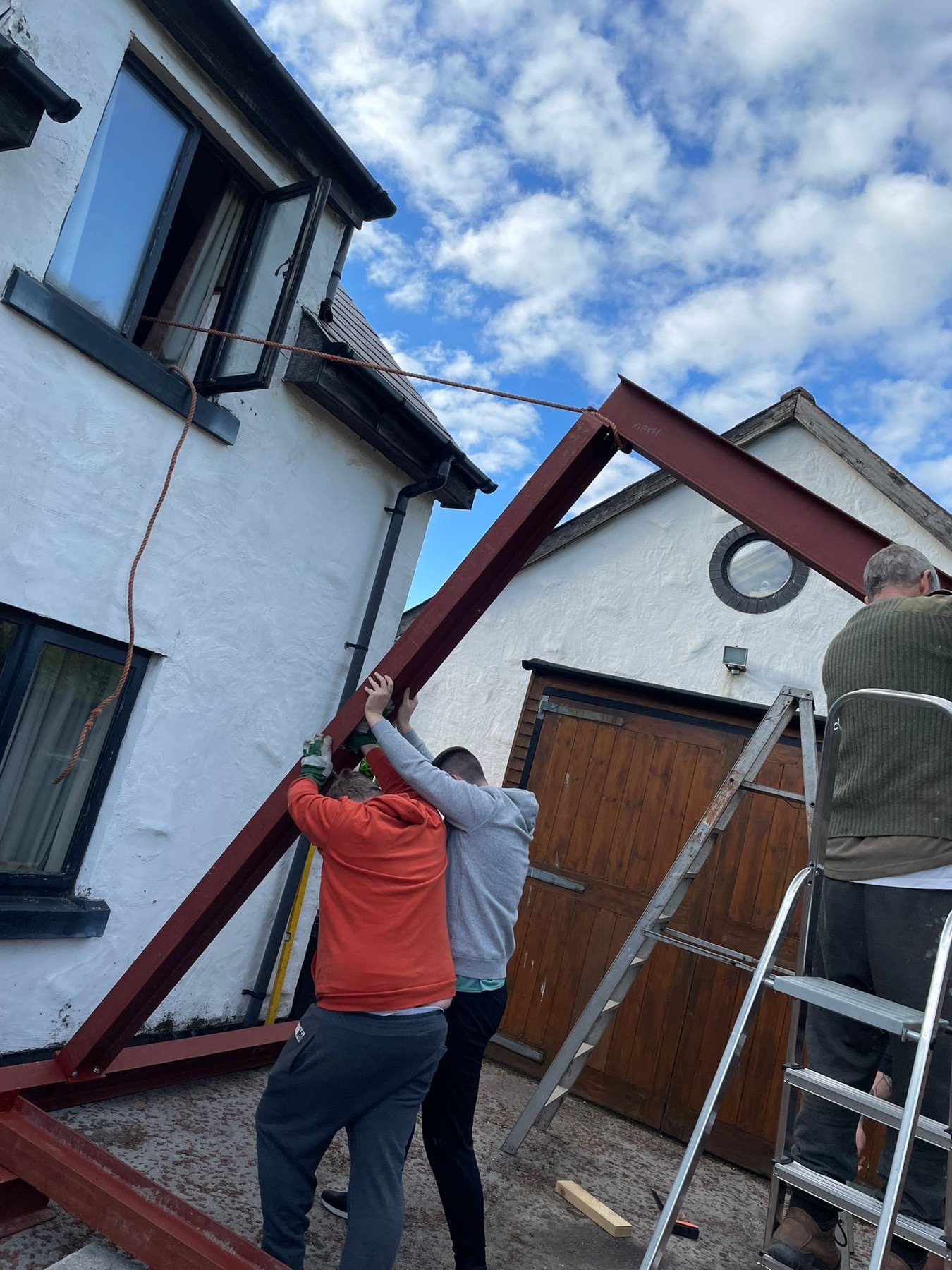
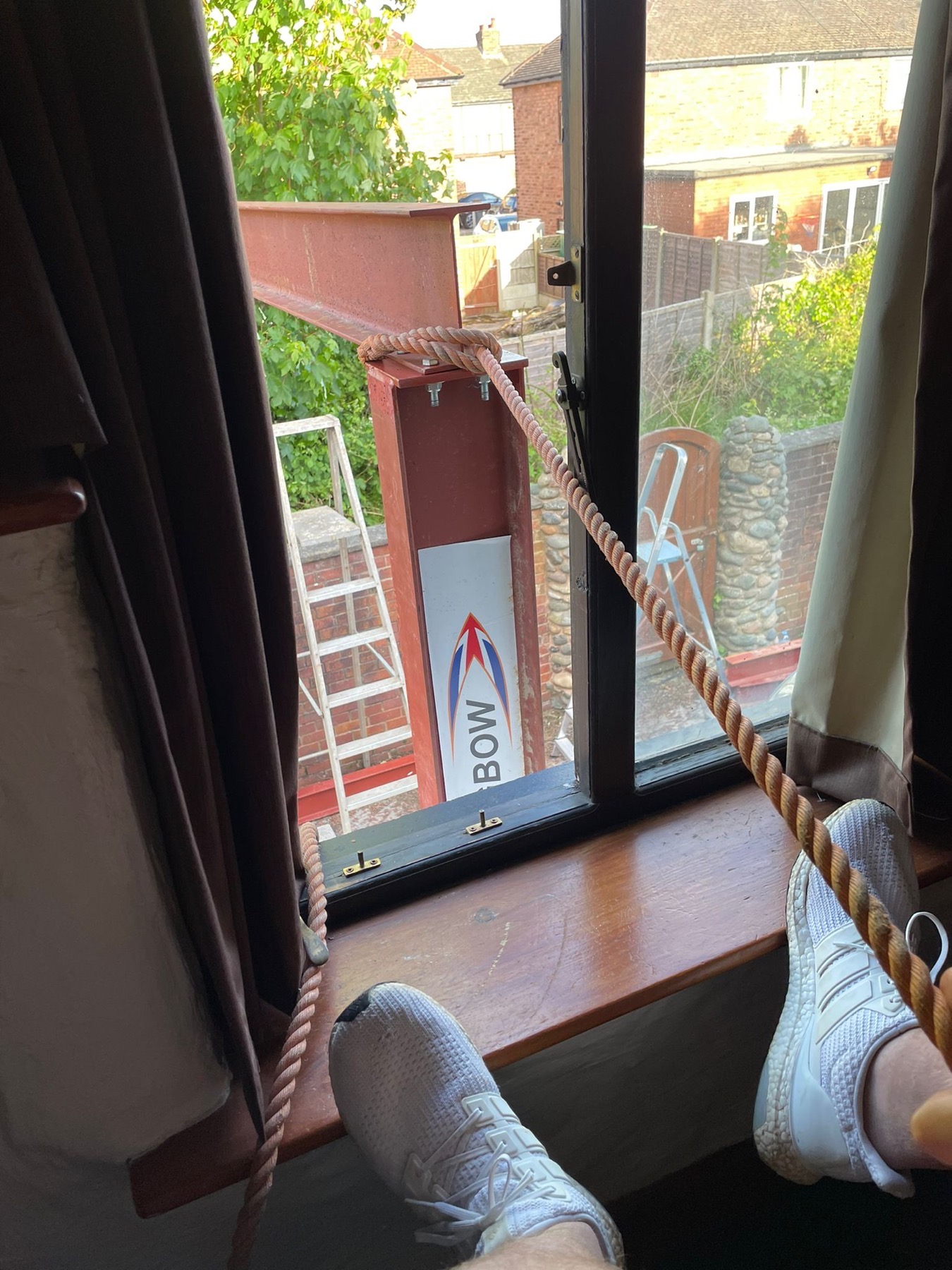
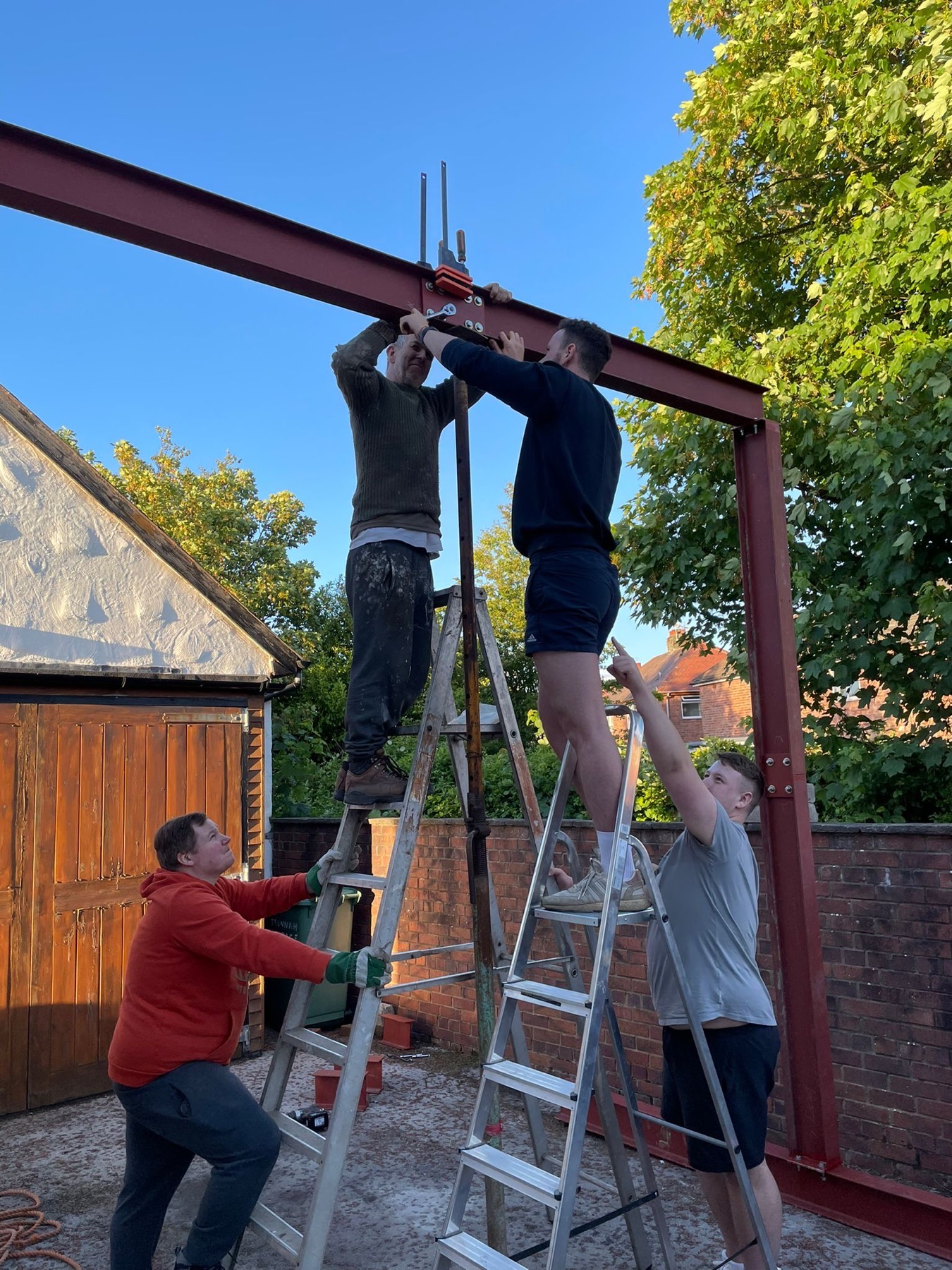
In order to ensure the whole structure remains stable the gantry is ground anchored into the driveway, with restraining straps bolted to the surrounding walls and steel wire rope rigging under tension to take any flex out of it. I then added the brilliant geared beam trolley from our sponsor Sealey and to that my old faithful chain block.
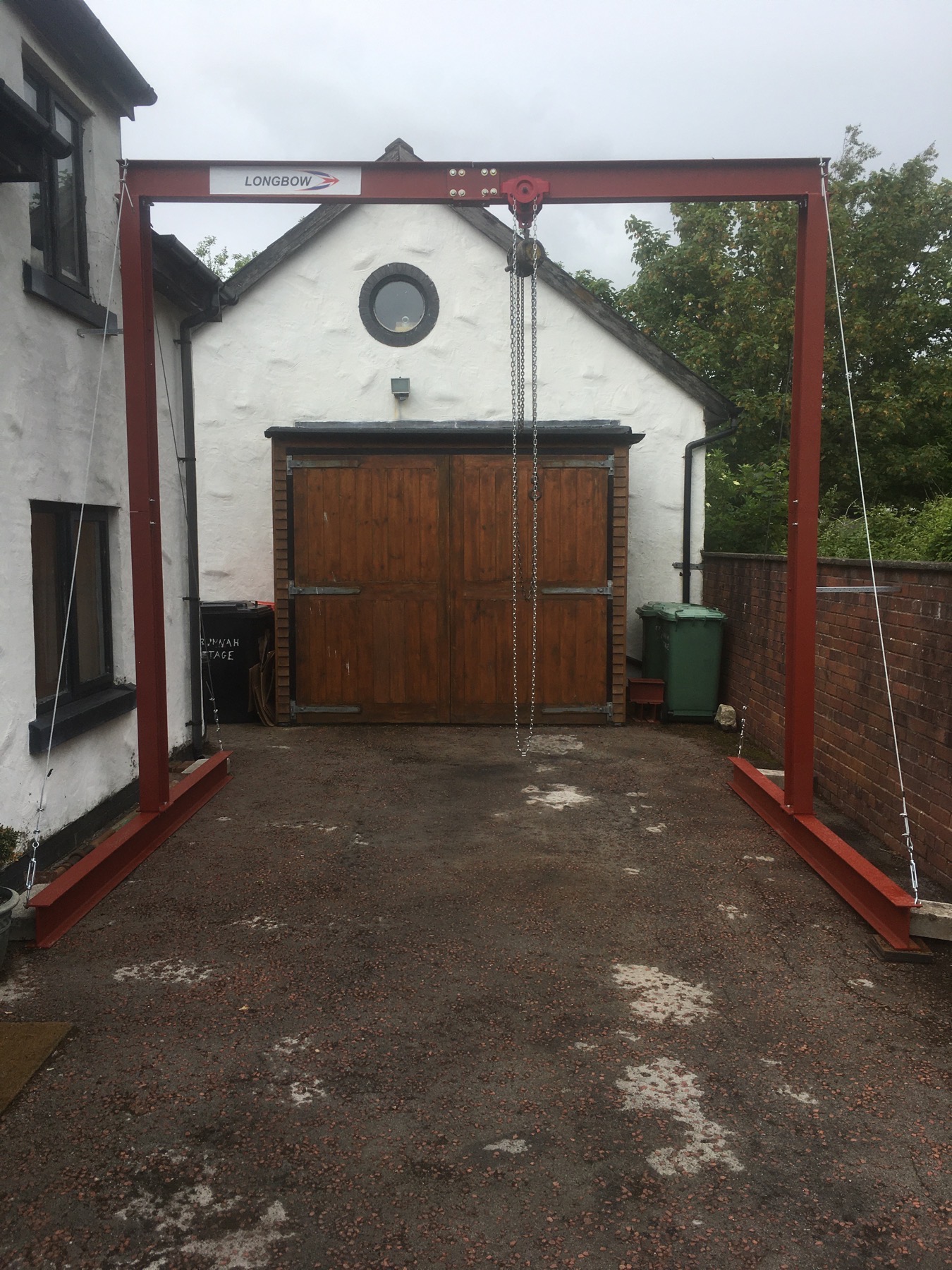
For those of you that have followed the venture for some time, you may recall I had previously designed a jet engine lifting rig and our sponsor Britlift had kindly fabricated it for us, with a selection of rigging for its use kindly supplied by our sponsor LES – Lifting Equipment Store.
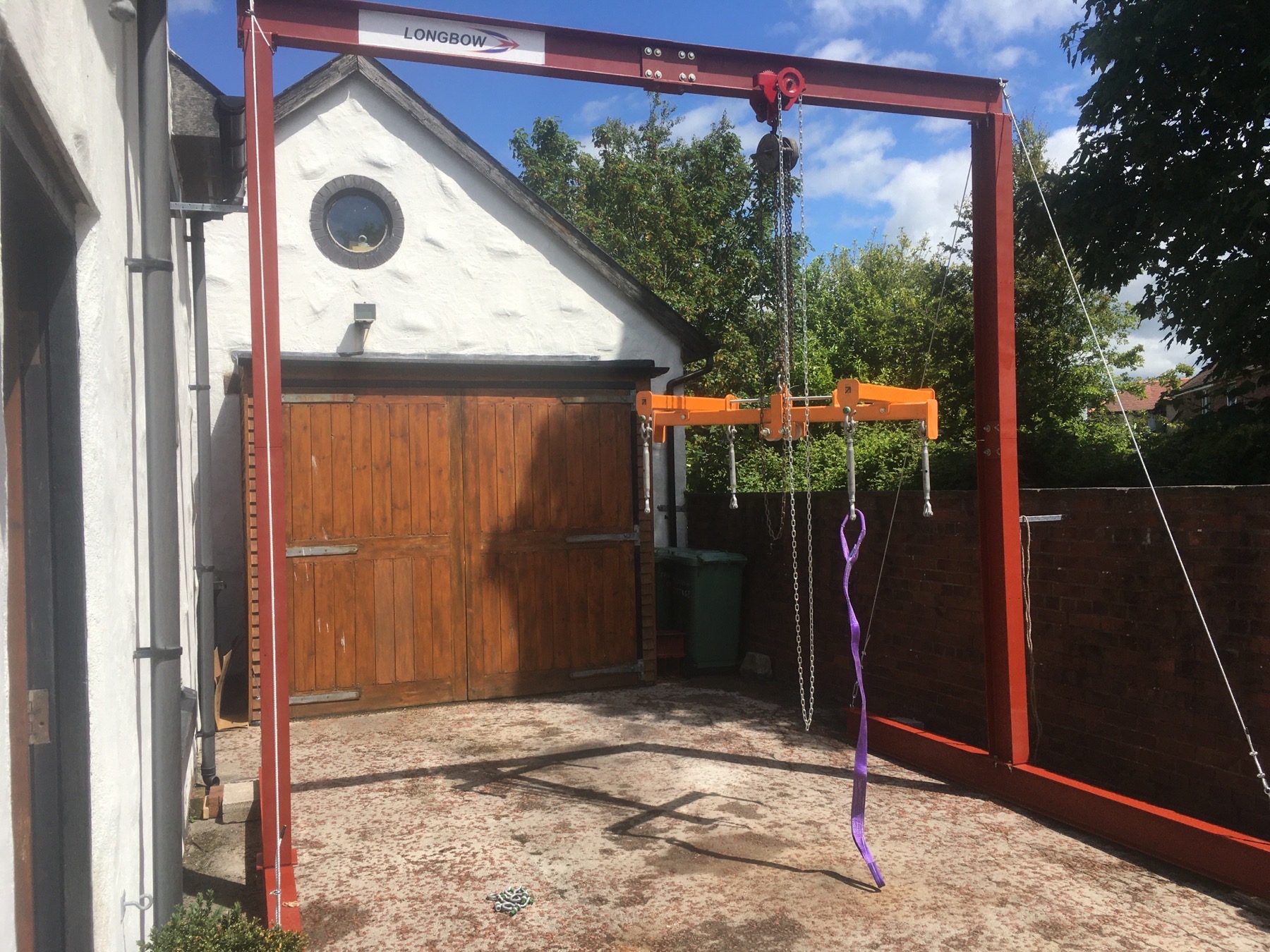
All we needed now was to move one of our jet engines out of storage to beneath our new gantry and see if the whole set up would work. Time to bring in my two son’s Robert and Tom again.
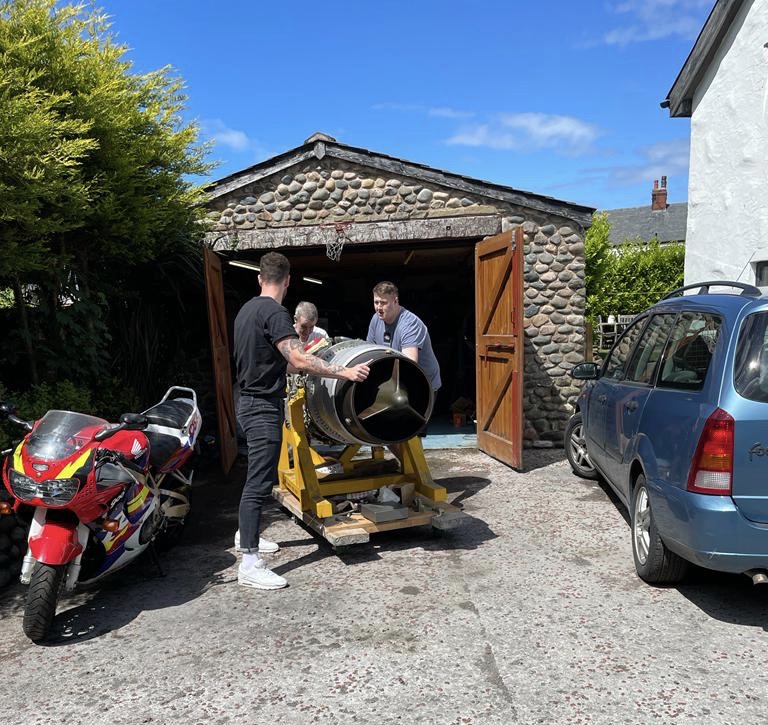
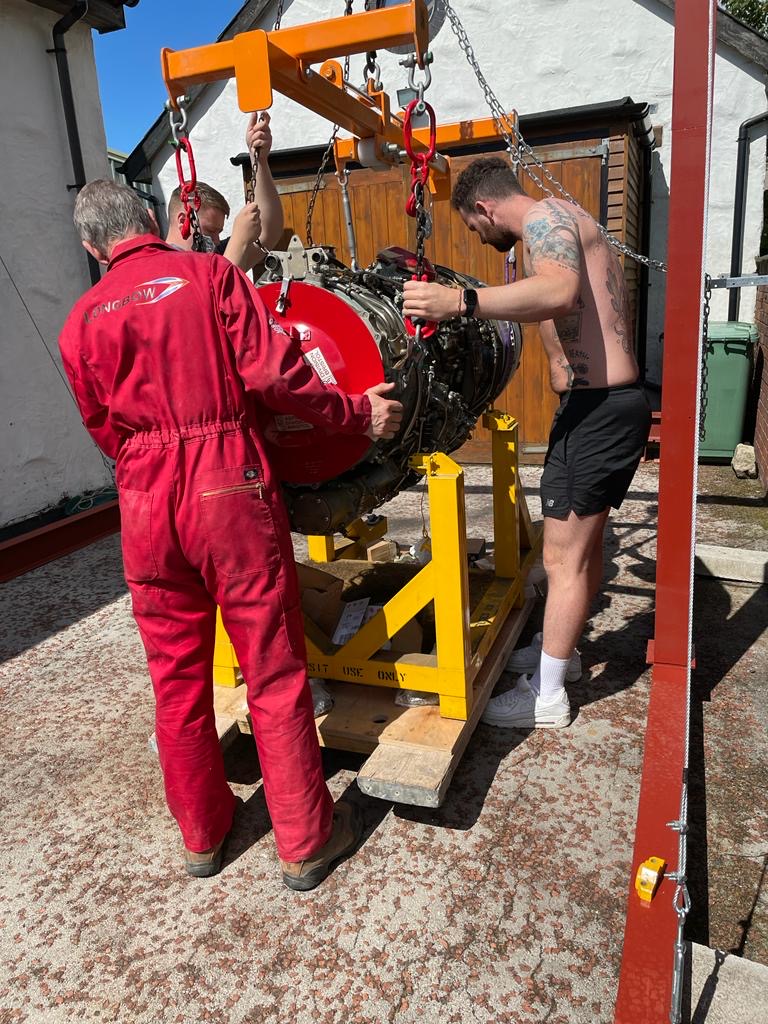
A little playing around with the threaded balance point adjuster on the lifting frame and we were good to go:
I am not so sure just how much my long suffering wife Gill appreciates the new steel feature on the driveway even if it is only a temporary structure. They do say marriage is all about making memories together though I am not so sure I am giving her the memories she quite envisaged when she said ‘I do’ all those years ago. I suggested she could use the structure for some hanging flower baskets, a swing seat now summer is coming, or maybe it might help if the kids or grandchildren take up gymnastics. Whatever she decides I am sure she will get used to it being there after a while……
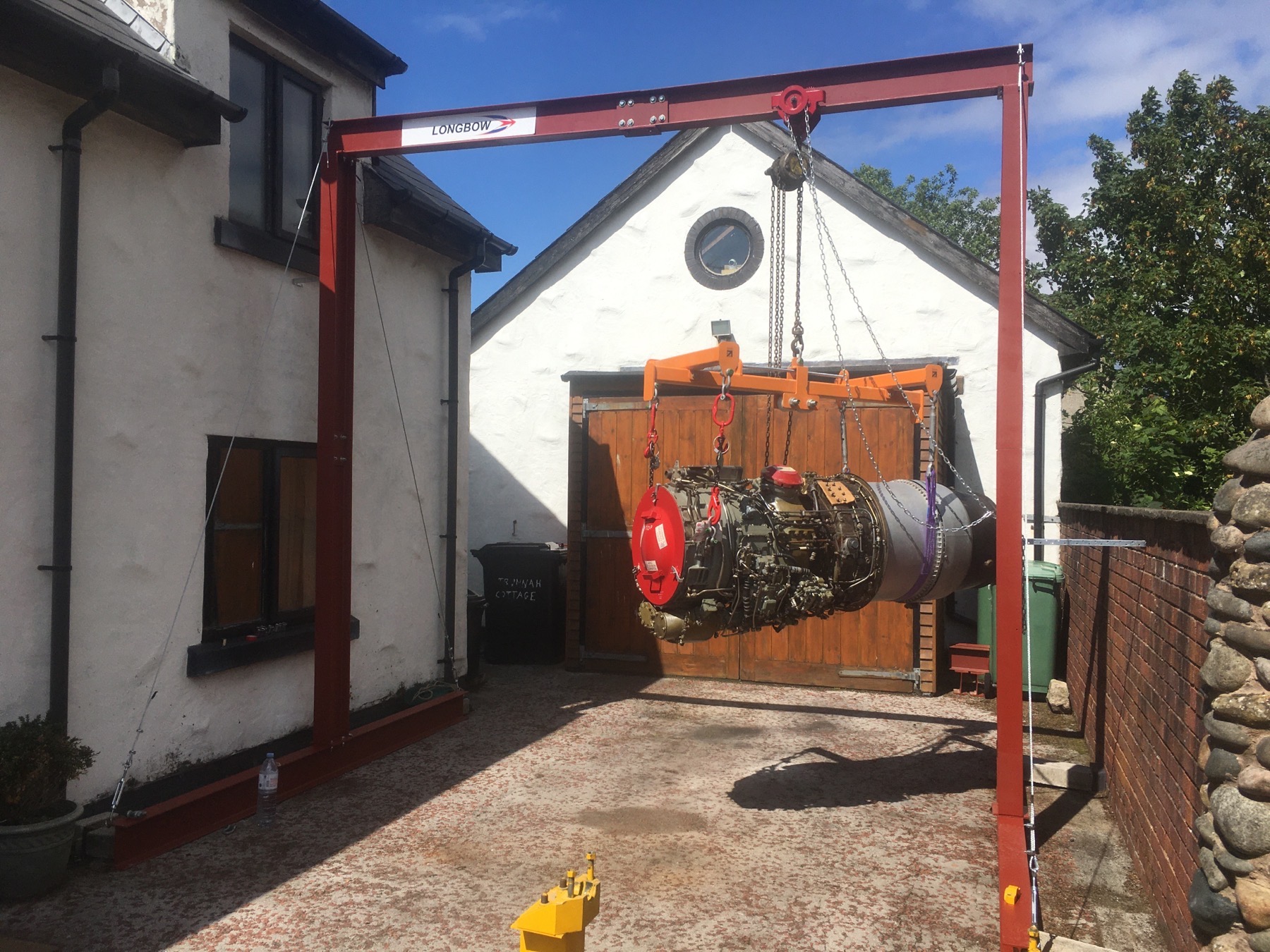
In all seriousness it is great to see our children learning to handle the jet engines and they tell me that they can now see the venture all coming together as we start to move onto the more exciting phases of the build.
In a world of fast moving technology I feel it is easy to forget the basics of simply building a fast boat by traditional methods based upon what has been proven to work over many decades. There is no need to reinvent the wheel or be overwhelmed by mind boggling stupidly expensive highly complex engineering, when common sense and experience will get you where you need to be.
Perhaps I am something of a dinosaur in that it leaves me cold when a vehicle has to be running a software program / autopilot in order for it to remain stable as it runs down the course. Has the spirit of record breaking come to the point where we must put the craft down the lake several times by remote control without a driver to check it is safe before letting a person sit in it to claim a record?
Pick up your hand tools and make what you want a reality. If it looks right then it probably is right and if it doesn’t work as you want it to, scratch your head, ask for help when needed and fix the problem.
With Longbow there are no computer programs for her design, no fancy graphics or simulations of twenty different versions that end up never getting built. Hell I don’t even know if she will float until I put her in the water. There is no trading on the history of previous British water speed record attempts, or using education in hydroplanes as a money spinning marketing ploy. There are no fat cat salaries for us to retire upon, or charging silly money for swanky after dinner speeches waffling about ‘The Challenge’ to line our own pockets. There is no asking the public or industry for millions of pounds to build something for a one off event lasting just a few seconds through a speed trap that will go straight into a museum. Surely those millions of pounds would be better off spent helping to staff a hospital or fixing the holes in our roads, just anything that was more good use than self indulgence? you will not find any ‘doing it for Britain’ rubbish whilst discretely making a living from it with sponsorship money here.
I am just a guy in a cottage workshop building in his spare time something different and fun with my own hands and a love of overcoming any hurdles in the way of making it happen. I am anything but wealthy and the venture is all at a personal total loss both time wise and financially but what else is there to do before I end up in my 70’s and through hubris fail to admit I am too old and no longer mentally sharp enough to start and most importantly to see through to completion such a project.
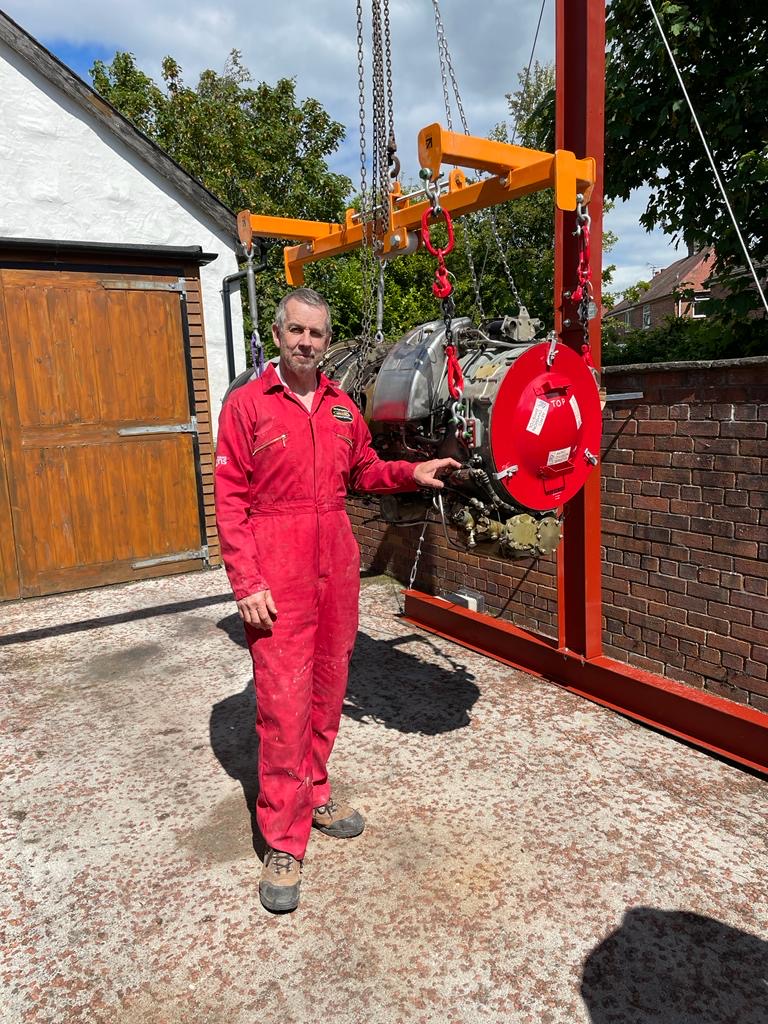
Irrespective of any water speed records I am simply designing and building a jet hydroplane that with good fortune under the watchful eye of my dear pal and mentor Dave Warby (who has a similar outlook to me) will hopefully float, get onto the plane and go reasonably quick again and again and again for the public to enjoy as a sight and sound experience. Something that anyone, in any country in the world following this little project may think, yes I can relate to that, it’s a cool thing to do and it’s just using tools to hand in any home workshop.
So on we go; build the boat, this jet hydroplane called Longbow and see how we get on.
I hope you enjoy reading my monthly diary updates of the little venture. It’s a bit of fun and yes there are periods of just hard graft as with any project but hopefully it will all be worth it to see her run as a pure thrust jet hydroplane upon Coniston Water in the Lake District again and again as we develop her.
Stay well folks and see you at the end of June for the next instalment.