What better way to start this month’s update than the terrific news from GS Yuasa, as a world leader in the manufacture and development of batteries, including for aerospace and defence, have so generously come on board as sponsor of Longbow to provide all the batteries necessary to start our jet engines !
You may appreciate that cranking over a jet engine to start it from stationary through to self sustain speed, requires a lot more power than your average car battery and in our case we have not just one but two jet engines to start, located side by side within the hull of Longbow. These are monster batteries and having taken a look at them I left it to my eldest son Tom who is always keen to show off how strong he is to lift these into the cottage workshop.
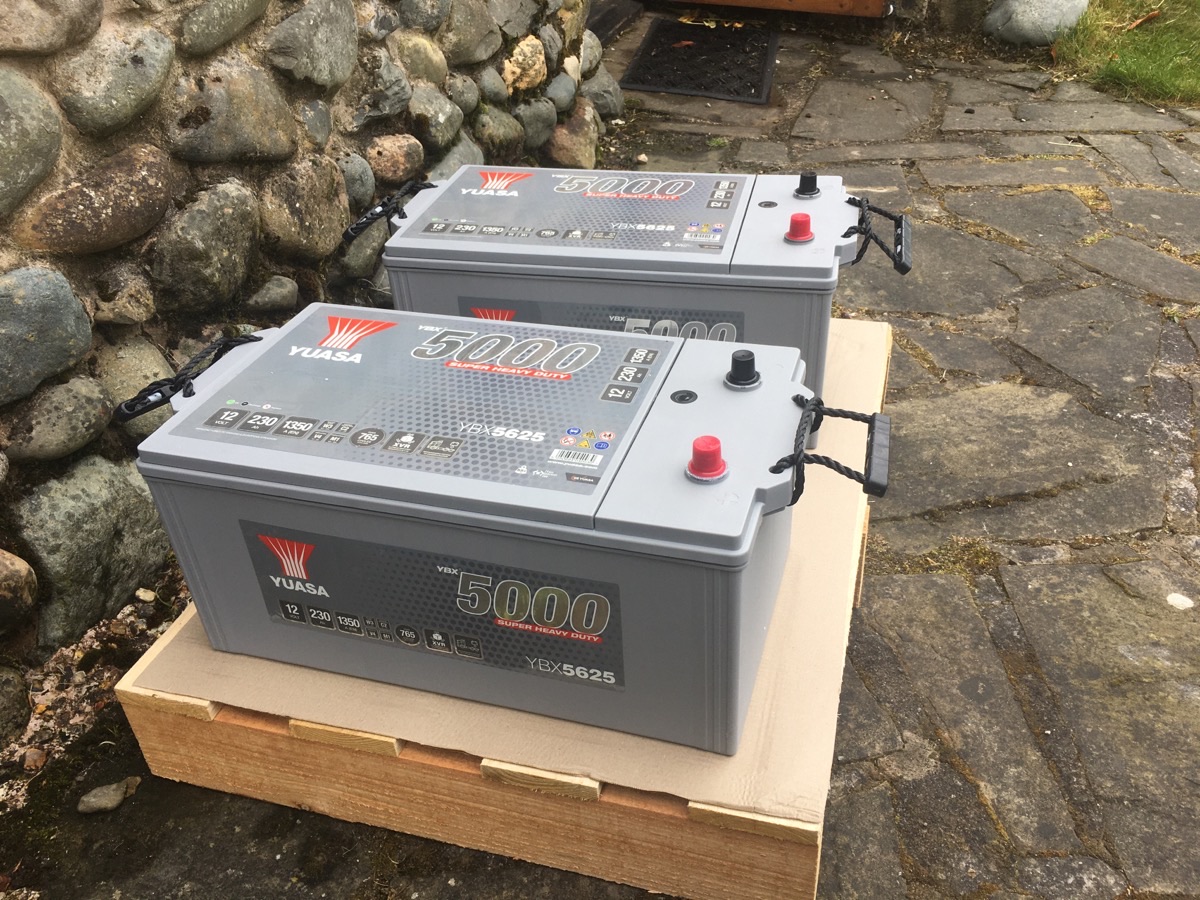
These batteries need to start not only one Rolls Royce Viper Mk. 535 turbojet engine that we are using from the military BAC Strikemaster aircraft, but immediately following one jet engine start, they then have to start the matching other jet engine within the craft. Once the support crew in a tender boat alongside Longbow have successfully started both engines using the GS Yuasa batteries within that tender boat, the crew will disconnect the electrical power cables from batteries to the jet hydroplane. The Officer of the day will upon assessment of conditions and when safe to do so, give permission for our serving military pilot, Lt. David-John Gibbs RN (DJ) to then proceed with his planned run of the craft down the lake or loch.
When that run is complete DJ will shut down Longbow to undertake her refuelling by another tender boat and crew at that end of the lake or loch. This also allows the surface of the water to settle from disturbances caused by that first run of the craft and any additional wake related to support vessels. It also allows time for a certain level debrief for that particular run and when everyone is ready the support crew at that end of the course, using another set of batteries will plug into the craft to allow DJ to re-start both of Longbow’s jet engines. The Officer of the Day will when appropriate then give the signal that it is safe for DJ to commence his return run back down the course followed by similar shut down of engines prior to slipping the craft back at base.
When undertaking an official attempt upon the Water Speed Record, runs of the craft in each direction of the linear course are required which needs to be completed within the hour. The length of inland watercourse required for such record attempts is considerable when allowing for acceleration and deceleration of the craft is taken into account for the speeds required. A certified surveyed measured distance part way along the course, which can be 1 mile apart, or these days more typically 1km apart is used to calculate the average speed obtained from both directions, thus negating any wind speed advantage that might have come into play if only a one way run was timed.
As the starter / generators on each of the jet engines require at least 24v we need two high performance GS Yuasa 12v batteries paired together to initiate an engine start. So with one set of batteries at each end of the lake or loch, plus other batteries on charge to rotate during testing of the craft, one may see that the number of high performance batteries required becomes rather significant. In these challenging times and considering the considerable cost of these high performance batteries, we must give special thanks to James Douglas and Gareth Robinson-Green of GS Yuasa who could not have been more helpful, knowledgeable and enthusiastic in providing us with all the batteries necessary to make this exciting venture happen.
Also this month Steve Buckle, Marketing Director of our sponsor Sealey Tools (Jack Sealey Ltd) kindly sent us new company signage for display upon our cottage workshop wall. This we were able to position lower down the wall than their large company banner we already had but that was often out of camera shot when taking photos of Longbow under construction.
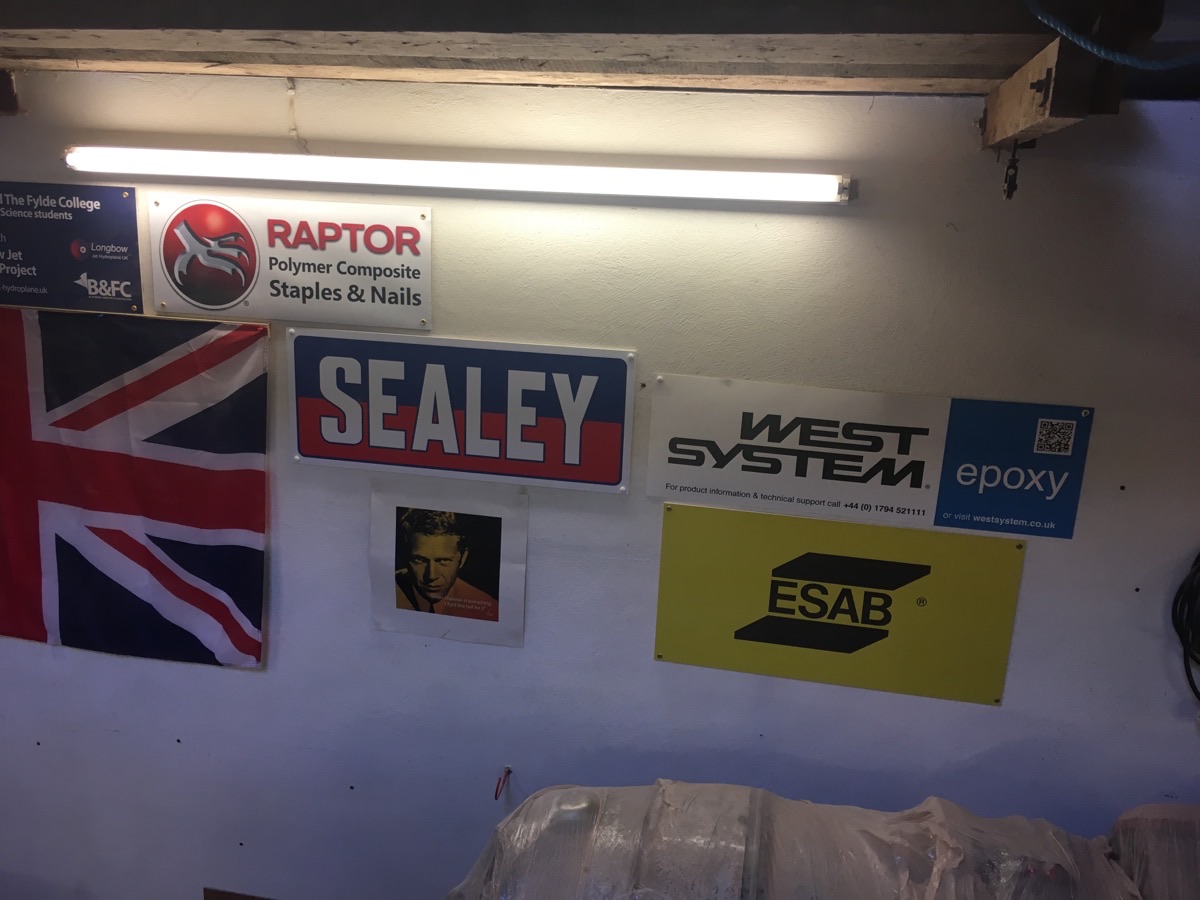
Whilst some people may say they are ‘going round the bend’ on lockdown during the pandemic, in our case during lockdown we were tasked this month with going round our own bend by forming the curved outer rails for the sponsons on either side of forward part of the craft. The rear underside of these sponsons are the surfaces upon which the forward part of the craft, as it gains speed, will rise up onto and hydroplane as a means of reducing the drag of the hull through the water. In turn this allows the available thrust of the twin jet engines to be used most effectively.
Last month we had formed the individual frames for the sponsons and so the first job to do this month was to notch out each of those frames at the correct angle to take the timber rails that define the outer shape of those sponsons.
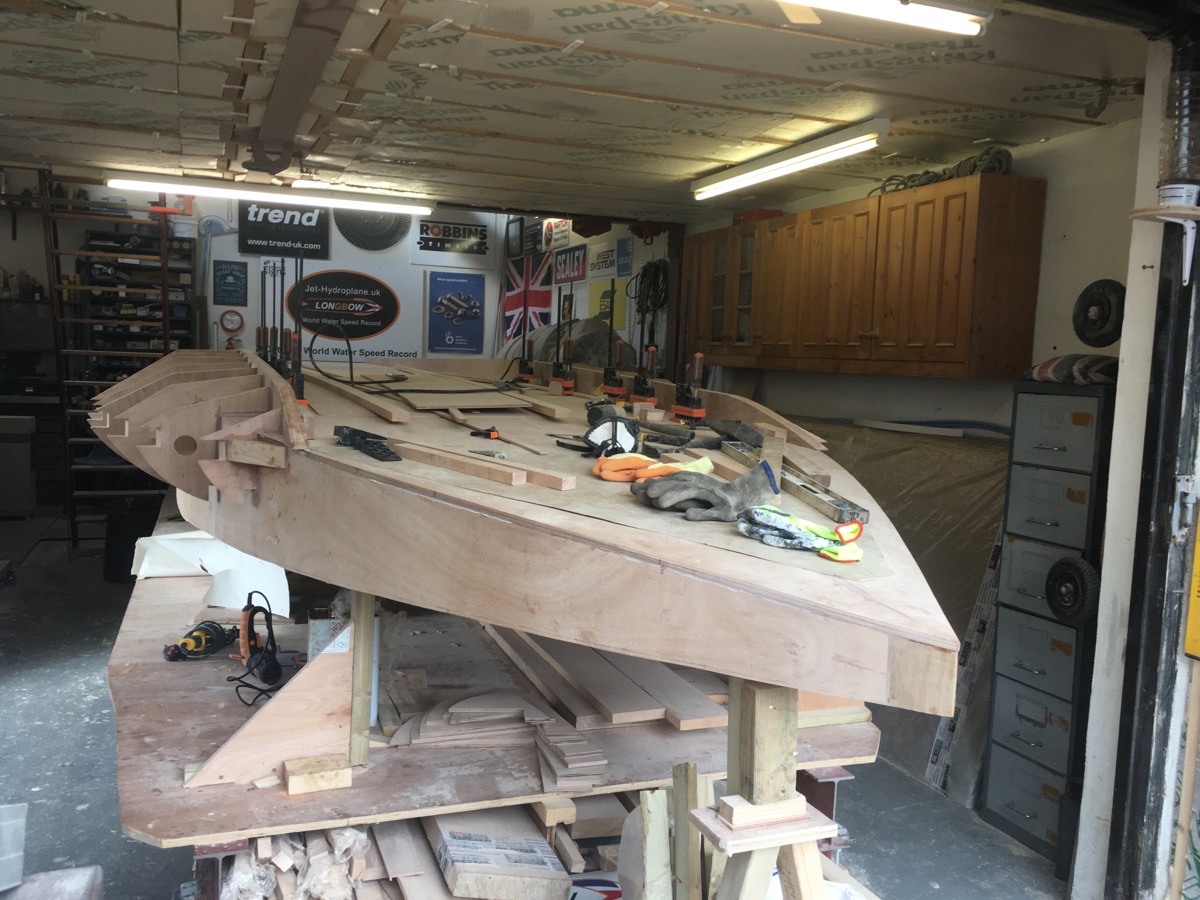
Once this was done we dug out our steam box and steam producers that we had used to form the curved bow of the hull. This would allow us to set about steaming the wood for these rails which had been so gratefully received from our sponsor Robbins Timber with again Sarah Meredith and Peter Kennedy, along with all the staff at Robbins doing so much to help us in these difficult times.
For those who remember seeing us steam the wood for the bow of Longbow you will recall that the object of the exercise with steaming wood is to soften the Lignin that forms the cell walls of the timber. Think of these cell walls rather like sugar that is rigid at normal ambient temperature but which becomes fluid at higher temperatures. If we steam the wood sufficient to bend / curve it to the required shape we are then able to maintain the grain of the timber along the length of that wood and in so doing maintain its strength as opposed to if we had cut the shape of the curve from solid stock material.
In the first instance to begin the process we put the straight lengths of wood into a plastic pipe, sealed at one end and flood that vessel with water in order to allow the relatively dry wood that went into the tube to become fully saturated throughout its length and depth over time.
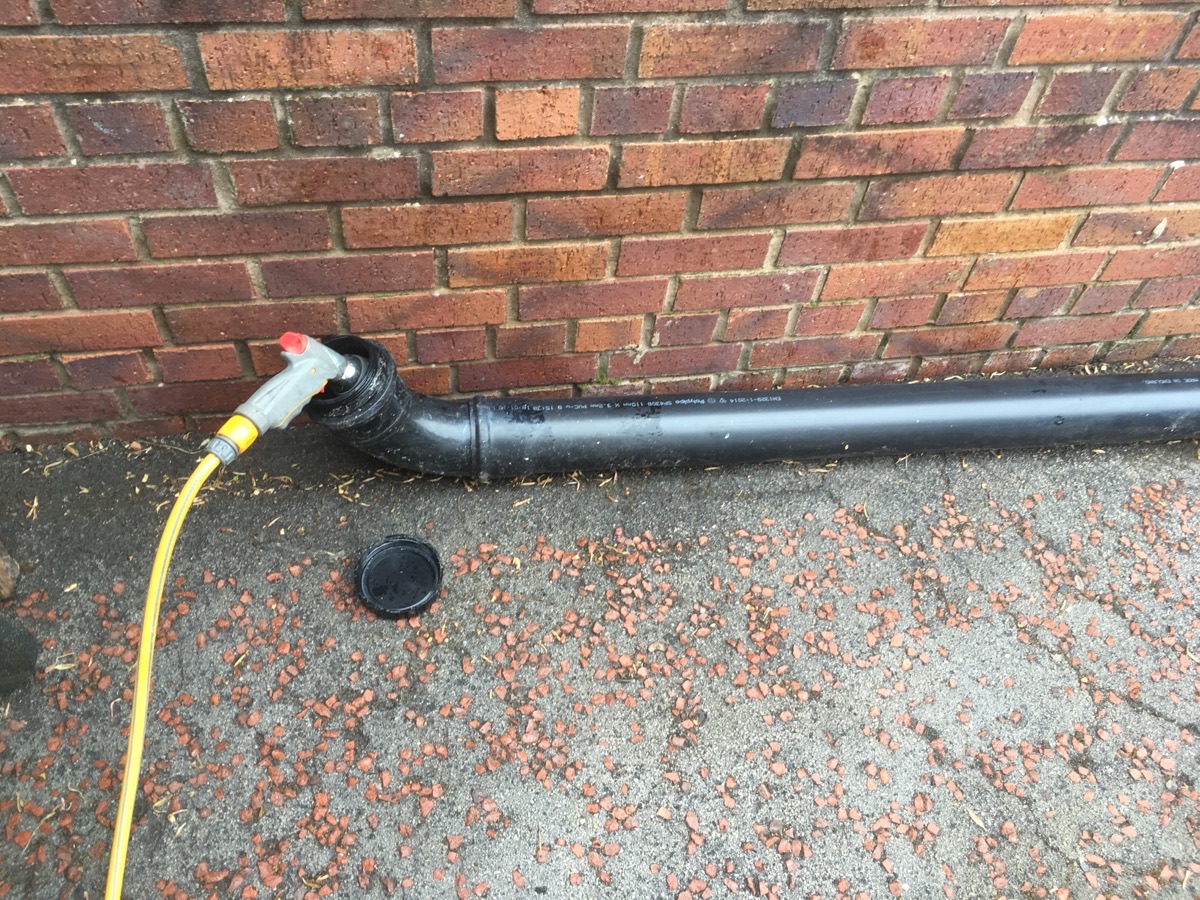
You can if you so wish attempt to steam bend wood without pre-wetting but experience suggests that works best with freshly felled timber that has a naturally high moisture content, as opposed to in our case where the wood has been kiln dried and machined to size at the sawmill.
Once the wood within our vessel has been allowed to become fully saturated for a sufficient period we remove if from that water immersion and place it into our steam box where it is supported periodically along its length by dowels that allow the steam to circulate around all the external surfaces and impregnate the wood to its core over time. The steam is introduced into the length of that box and then vents / condenses draining out of a hole at one end so as not to cause the box to pressurise and explode.
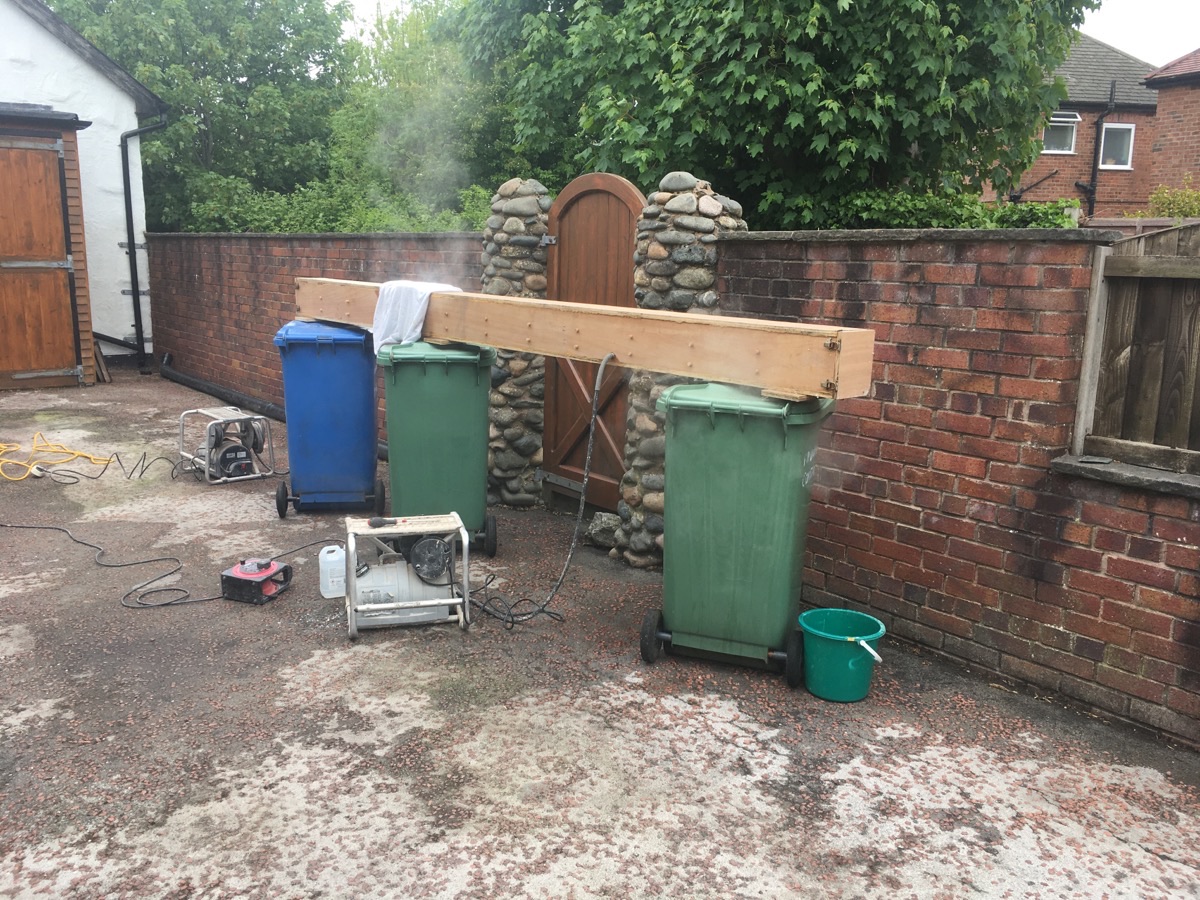
The rule of thumb for steaming timber in order to bend it is generally in the order of one inch thickness of material per hour of steaming, although we like to give it a little longer just for good measure. However if you attempt do it for too long the wood will begin to degrade often seen as becoming somewhat fibrous making it useless for our purpose so there is definitely a balance to be met in respect of steam box time.
After sufficient time has elapsed then upon removing the sections of timber from the steam box you only have a few seconds where it will remain pliable enough to clamp it into its curved position before the lignin we spoke of earlier begins to cool and the wood return to its rigid state. My wife Gill and our two sons Tom and Robert on lockdown with us were thus roped in to assist because if you have not got the wood into position and fully clamped within a few seconds, then trying to force the rapidly cooling timber into the required curve will only result in it fracturing. That in turn would require the whole process right back to the prolonged wetting of more stock timber to be repeated.
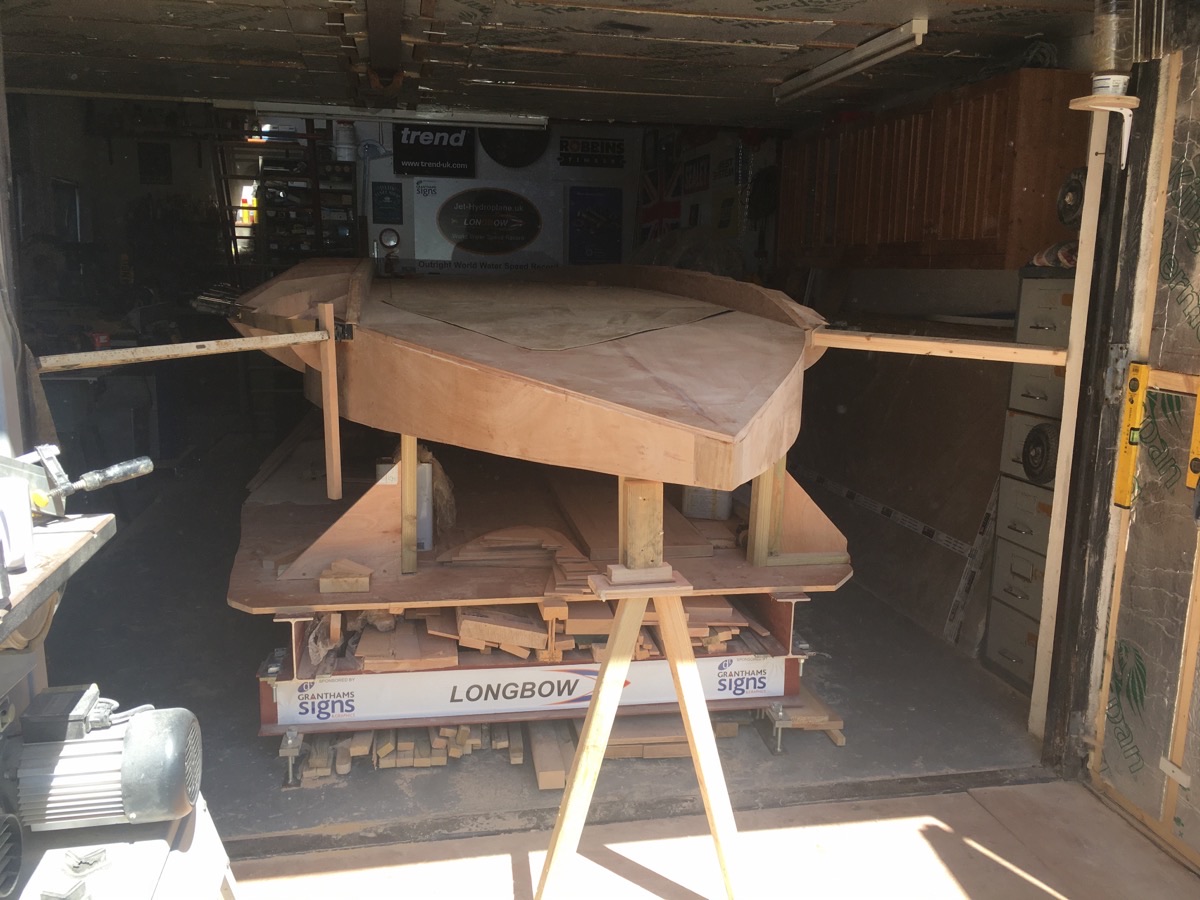
With the timber clamped into position we have to let the wooden curve fully set and its moisture content decline over days from saturated to acceptably dry, monitoring its moisture content with a Protimeter damp meter. We then remove the clamps, store the timber weighted in the direction of curve to reduce ‘spring back’ and repeat the process again for the next layers of wood.
Once we had all the pieces curved and dried back down we then set about fitting them one at a time into place using the WEST SYSTEM Epoxy and filler kindly supplied by our sponsor Wessex Resins. The following photo shows Gill being promoted to epoxy mixing specialist:
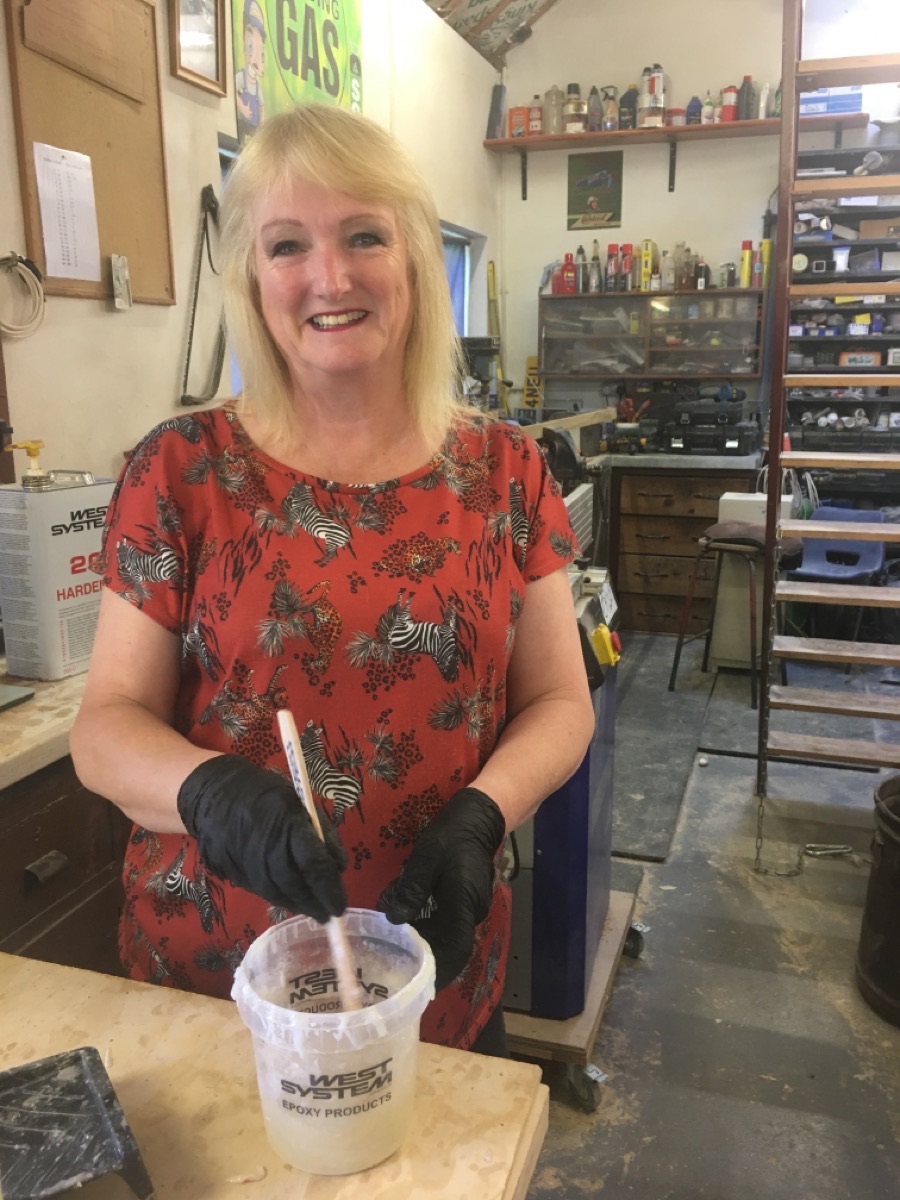
After applying the WEST SYSTEM Epoxy and filler the curved rails were held in place one layer at a time with the Sealey F clamps and left to fully cure before repeating with the additional layers.

Upon removing the clamps it was just a case of cleaning the curved sections down and with the newly formed outer rails to the sponsons in place, you can now fully appreciate the shape of the hull to Longbow coming together, bearing in mind that she is currently inverted during this stage of the build. We may be biased but we hope you agree that she is starting look sleek, fast and purposeful even standing still !
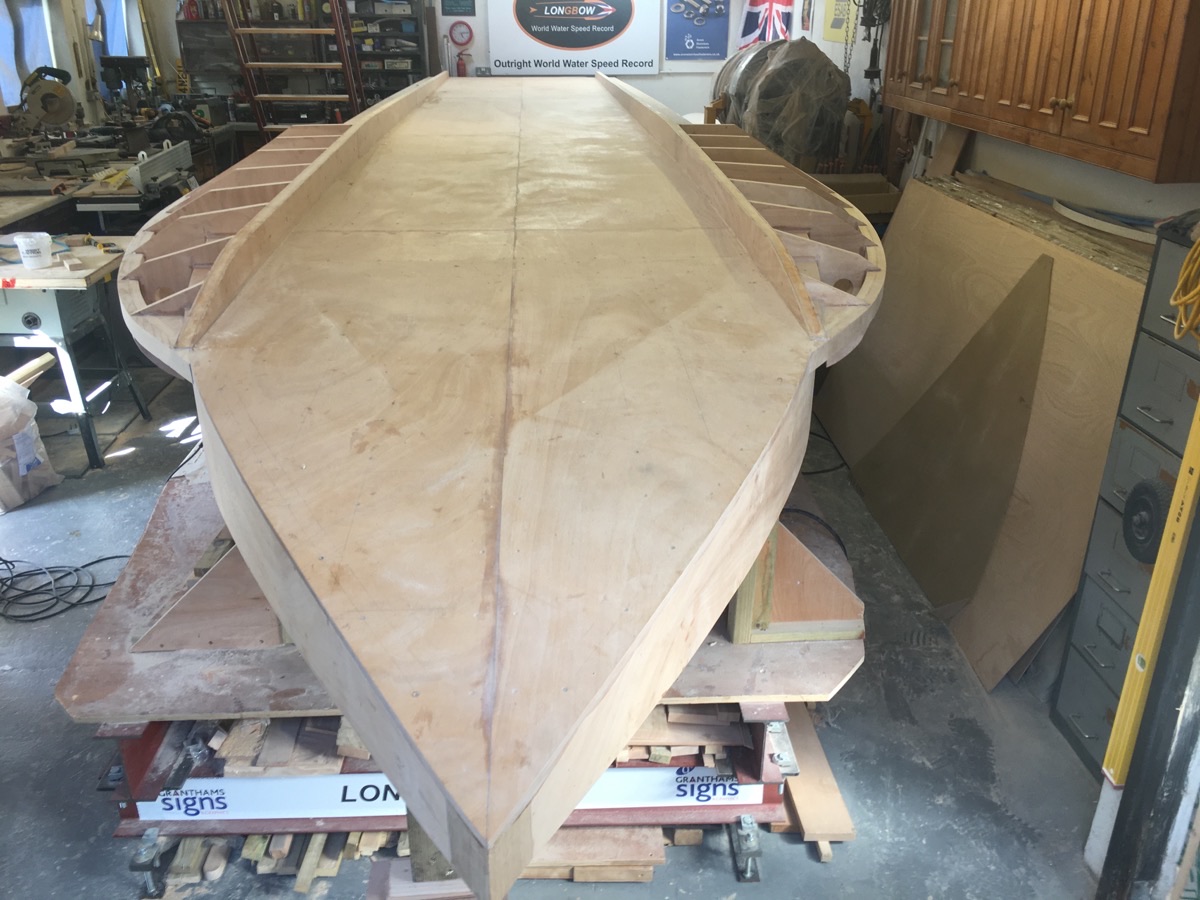
In other news our great friend Dave Warby in Australia is hoping to be back at Blowering Dam in August with his jet hydroplane Spirit of Australia 2 for further testing, as his Country begins to ease the pandemic lockdown. As we have reported previously Dave is having a ‘T‘ tail for the craft built by aircraft fabricators for him to fit upon completion, so she is going to look very different indeed on her next outing and with Dave fully fit again after his injuries we cannot wait to see both him and SOA2 back in action.
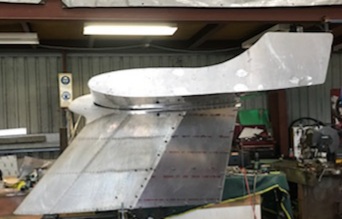
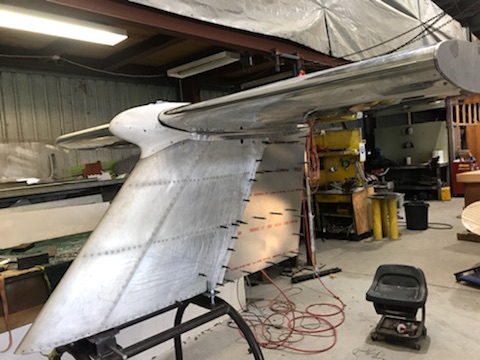
Other than me actually physically building Longbow during lockdown there is a also a lot of other work that has to be undertaken in the background in order to make the venture happen. For example this month there was also CAD drawings to be done for the transport trailer and layout drawings for the control box necessary for statically running up her jet engines under test. John Fielding our electrical engineer let us know that during his lockdown he has been doing some more of the wiring needed for those engine tests. As the build program moves on there is always the letters, emails and phone calls to both current and potential product sponsors all of which eat into my workshop build time but without which the project would not happen. As a teaser we will reveal further exciting news of product sponsorship for Longbow as a result of some of those discussions in next month’s website update.
Well that concludes this month’s news folks and once again I thank you for taking the time to pop by to catch up with our progress. If you have not already done so please ‘like’ our Facebook page. Hoping we all stay safe in these most challenging of times, if you have questions drop me an email and I will do my best to answer, perhaps even discussing your question in the following news update and please call in next month for a catch up on the exciting build of our jet hydroplane Longbow.