This month marked the 50 year anniversary since astronauts first bounced around on the moon but our good friend Dave Warby in Australia found out that gravity back here on earth, can still mess you up pretty good when he took a tumble in the workshop attending to odd jobs on his jet hydroplane Spirit of Australia 2. Dave didn’t have far to fall to get knocked out with a broken arm in two places and looking like he had done twelve rounds with Mike Tyson. Feeling pretty sorry for himself Dave needed a bit of cheering up whilst he is recovering and in typical Aussie style his team mates made him laugh in their own way with the following photo which we also thought was pretty funny.
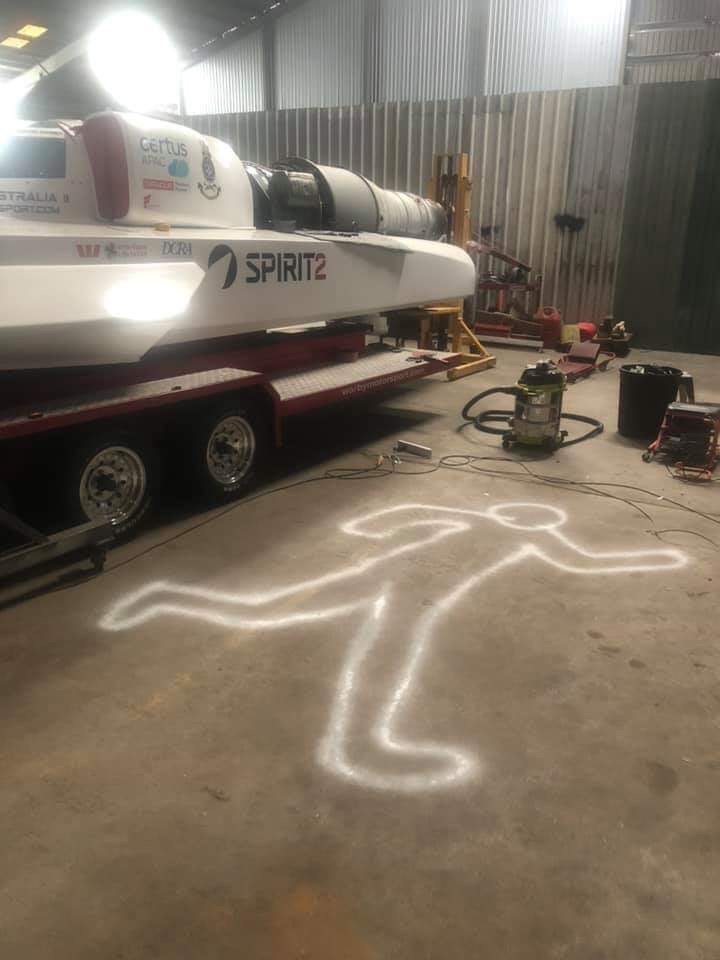
On a more serious note a routine inspection of the Orpheus jet engine that Dave had been using during tests of their boat, revealed the turbine disc was not giving of its best. That disc is the last fan wheel on the jet engine, that the hot gases of combustion pass through on their way out the back and consequentially it gets a hard life and can suffer over time.
Luckily Dave has a complete spare engine so his team swapped that over in the boat whilst they scratched their heads over where they would get a replacement turbine disc for an engine that went out of production many years ago. Dave might now be sporting a right shiner of a black eye but he could still spot an Orpheus turbine disc a mile away; well in fact 10,000 miles away when he saw I had one on the back wall of my workshop we are building our jet hydroplane Longbow in. So it would be just a case of promising us a crate of Fosters and us sending him my Orpheus disc right?
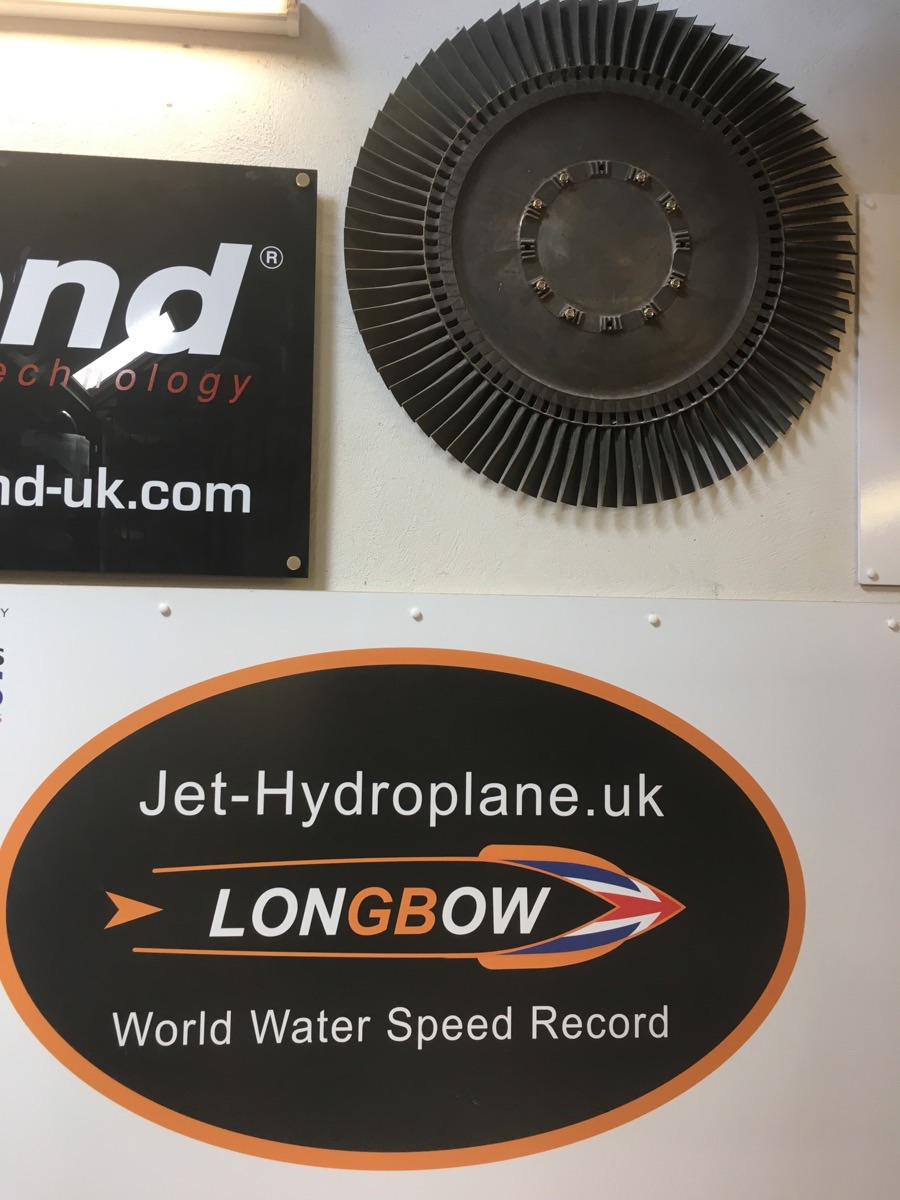
Well no as it happens because unfortunately the number of blades on an Orpheus turbine disc vary from one model to another. Dave’s Orpheus being from a Fiat G91 aircraft in Italy has 125 blades, whilst the one I had on my wall in the workshop relates to a British Folland Gnat, so only has around 79 blades the last time I counted. That and other differences between the two engines gives the G91 version in the region of 500 lbs more thrust than the one used in the Gnat, which the latter some readers may remember was the RAF Red Arrows display aircraft before it was superseded by the Hawk they currently fly.
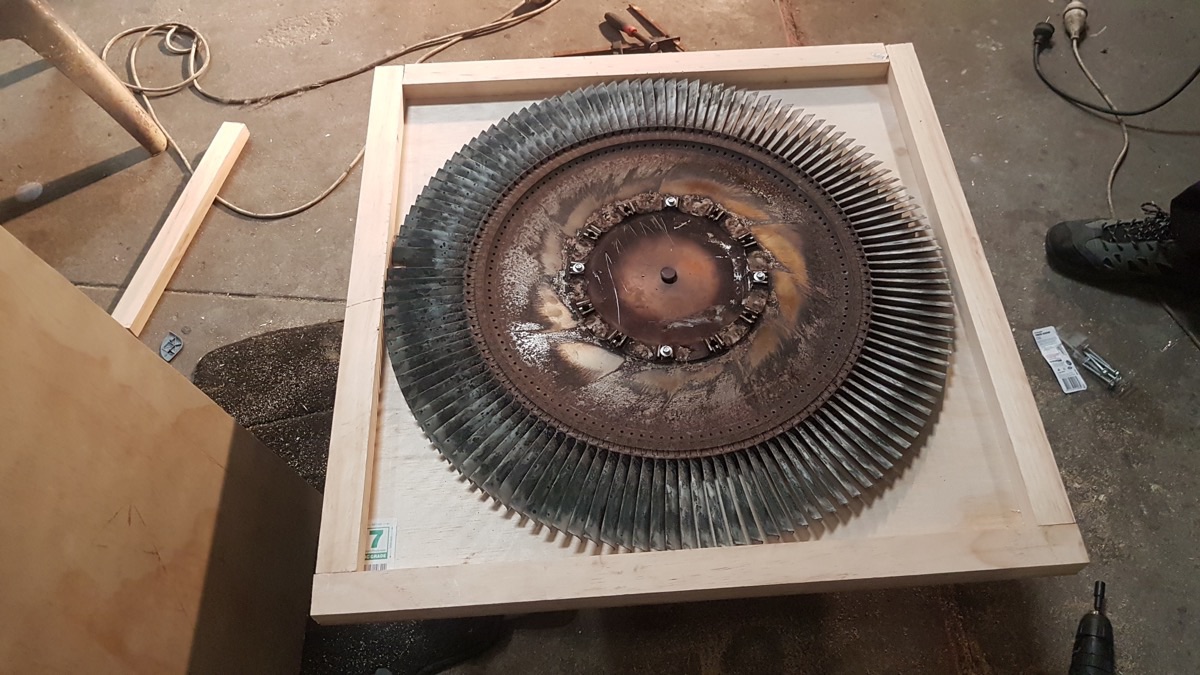
So if the Orpheus disc I had would not match Dave’s we both scratched our heads as to where we were going to find him a replacement. Dave could not find one in Australia and even ended up looking for one as far as Sweden. However as luck would have it, I managed to track one down within a sectioned engine owned by the North East Aircraft Museum here in the UK which is currently on loan to Hartlepool College Aerospace faculty.
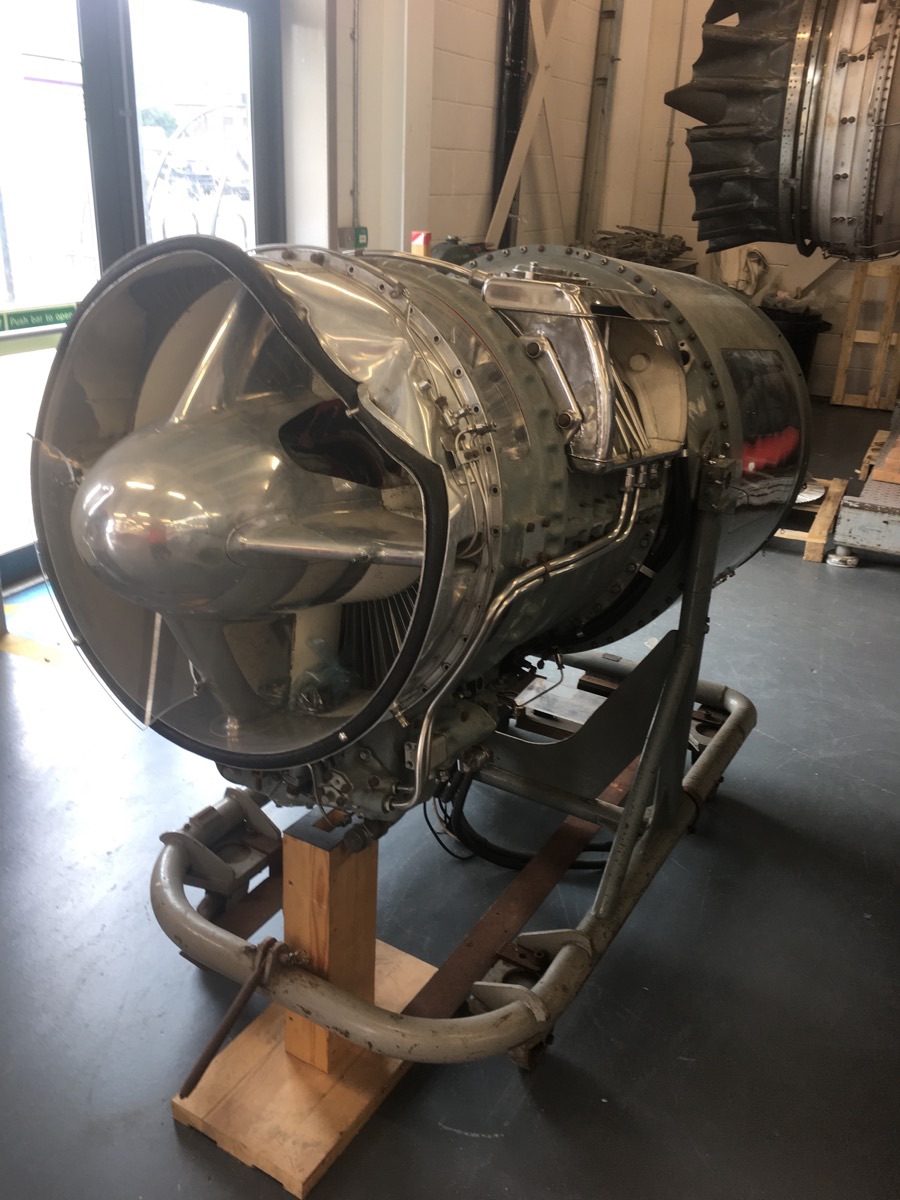
David Charles curator of the Museum and John Applegarth senior lecturer at Hartlepool College, could not have been more helpful with our request. So whilst Dave’s team packed up their Orpheus wheel in Australia to send to us, Fred and I had a day out popping up to Hartlepool from Wyre to pick up the Museum’s one.
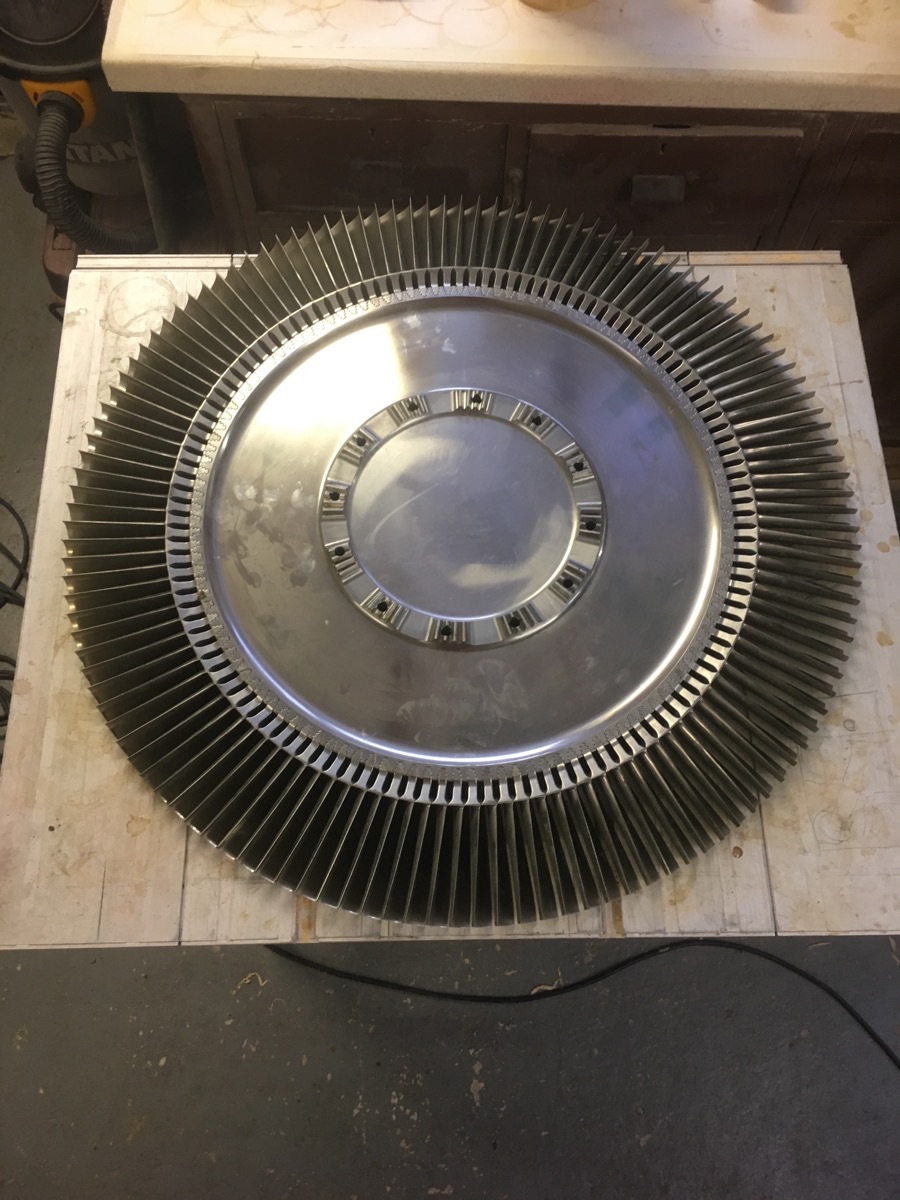
As you can see by the photos this turbine wheel from the Museum / College looks like it has never been run and was comparative to Dave’s in immaculate condition. So once his wheel arrives in the UK, we will be sending the Museum one over to Australia where hopefully it will be in use for Dave’s attempt upon his father’s Record and the Museum / College here gets Dave’s wheel to go in their static display sectioned Orpheus, with some special history to it having been run in a jet hydroplane.
The other good thing that came out of this exchange was some of John’s aeronautical students at Hartlepool hopefully becoming involved with our jet hydroplane Longbow in conjunction with the students of Blackpool & Fylde College, given the excitement in the project and it being an inspiration for our young engineers of tomorrow.
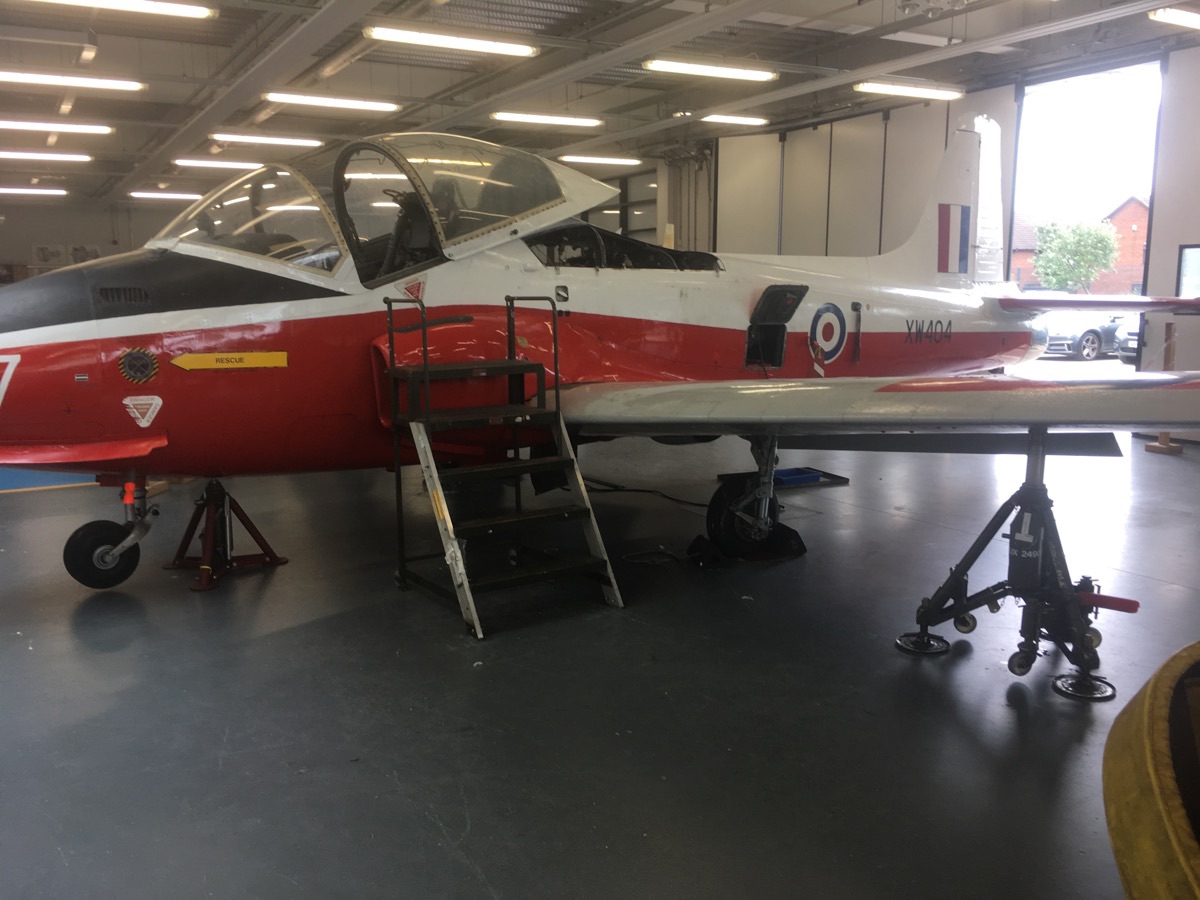
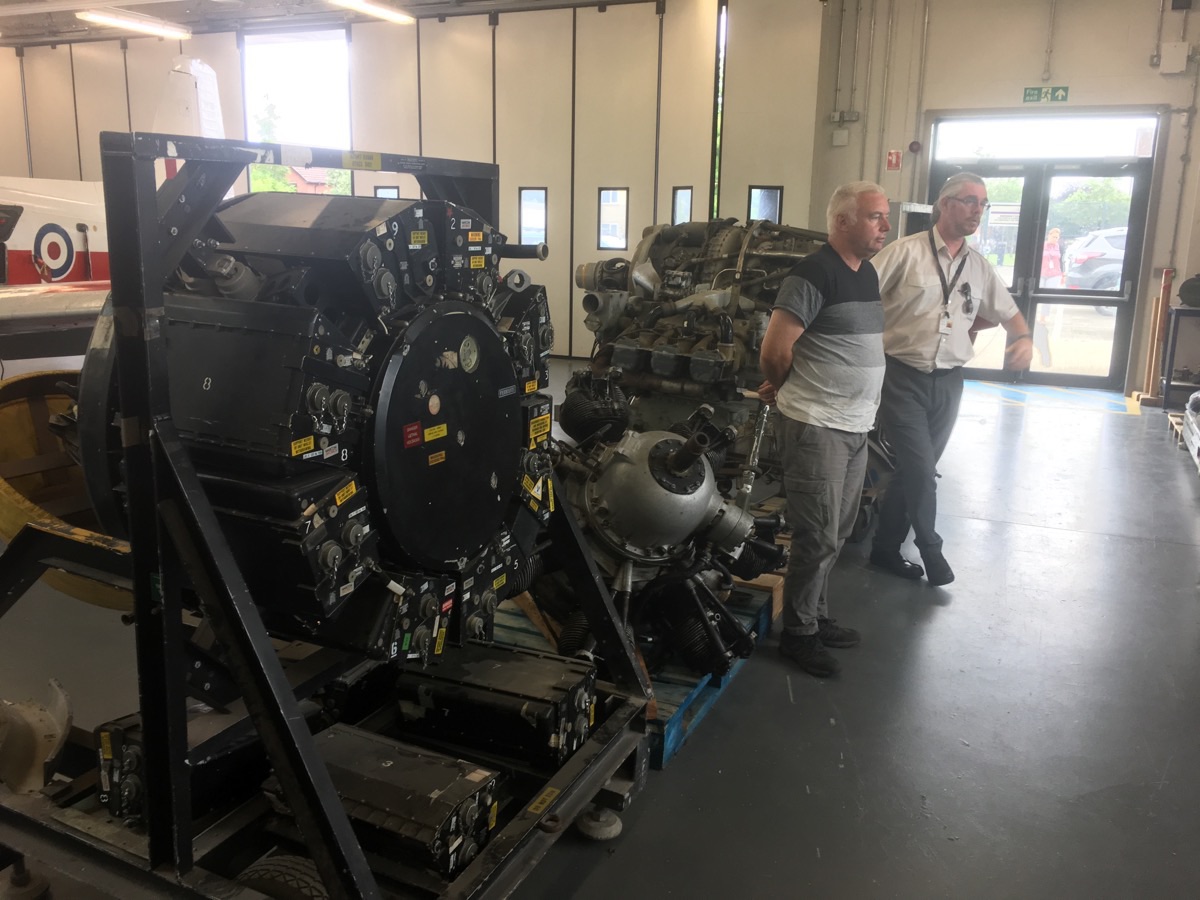
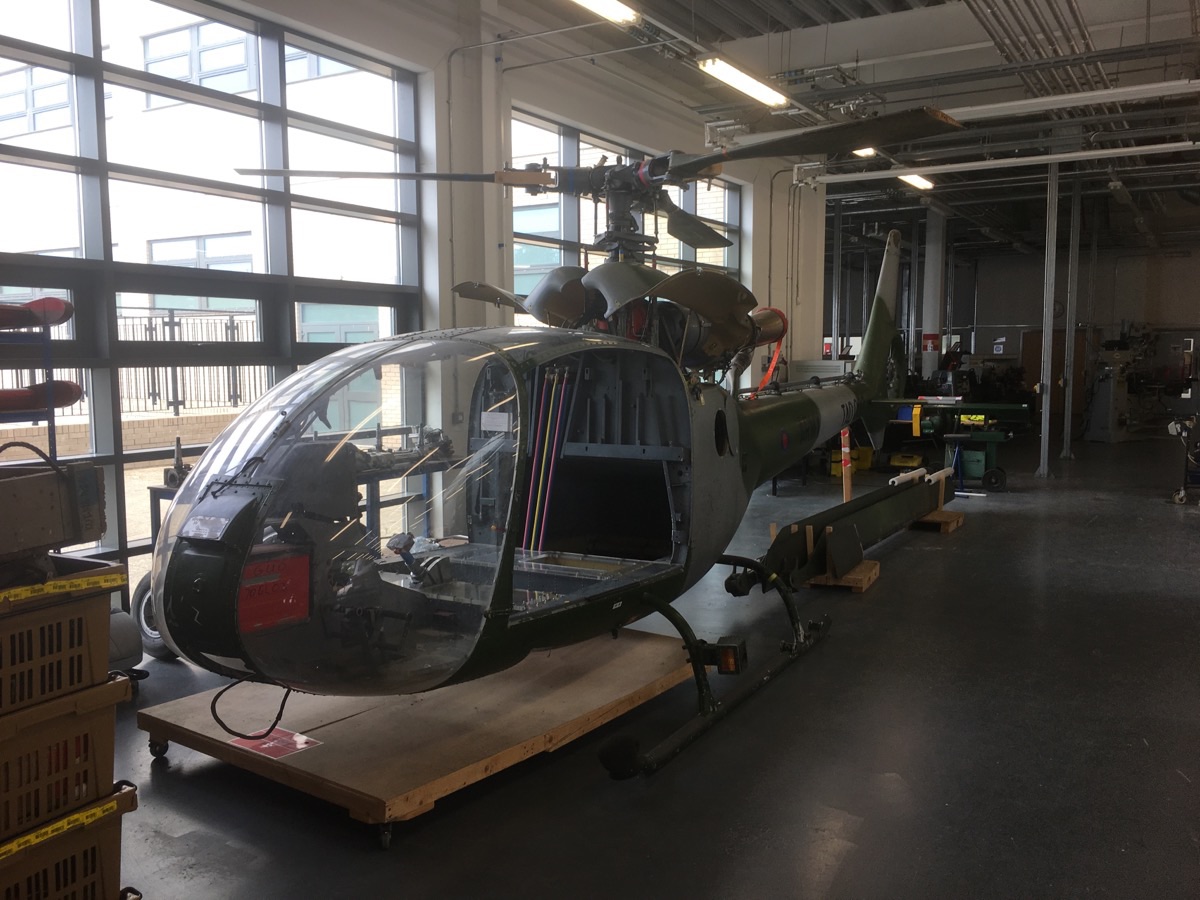
Continuing that theme it was nice to have one of the motorsport students from Blackpool & Fylde College, Bethany, visit us where she not only learnt about making joints on the hull of our jet hydroplane Longbow, using the West System Epoxy supplied by Wessex Resins, one of our product sponsors but also had a go at welding aluminium using the AC / DC Tig machine supplied by ESAB, another of our product sponsors as shown below:
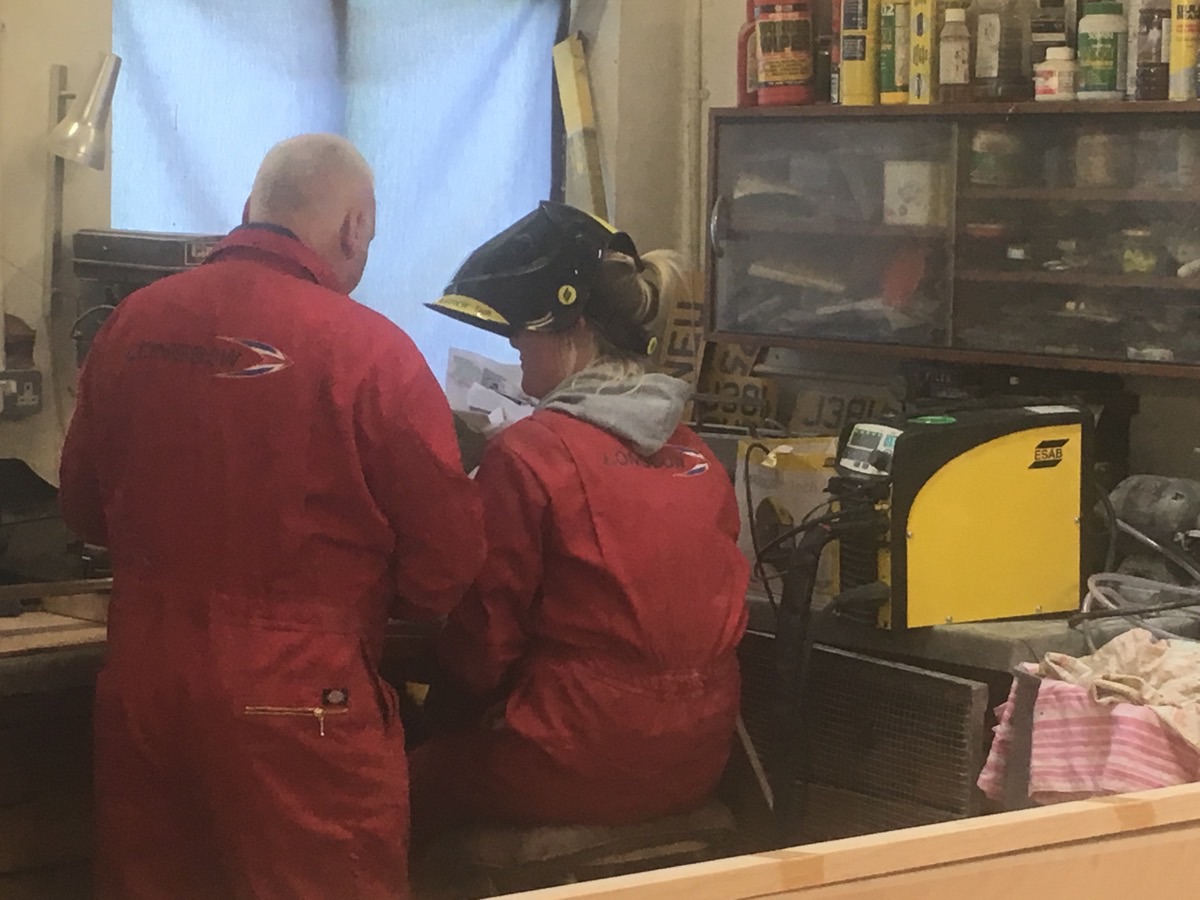
Acquiring some parts for Longbow and everything that goes along with getting her twin jet engines to run in this specific application, as opposed to in the aircraft presents a few challenges along the way. Some things are more easy to source than others such as we managed to find and purchase some electrical fuel pumps specifically designed to feed the mechanical pumps on each of the Viper jet engines going into the craft.
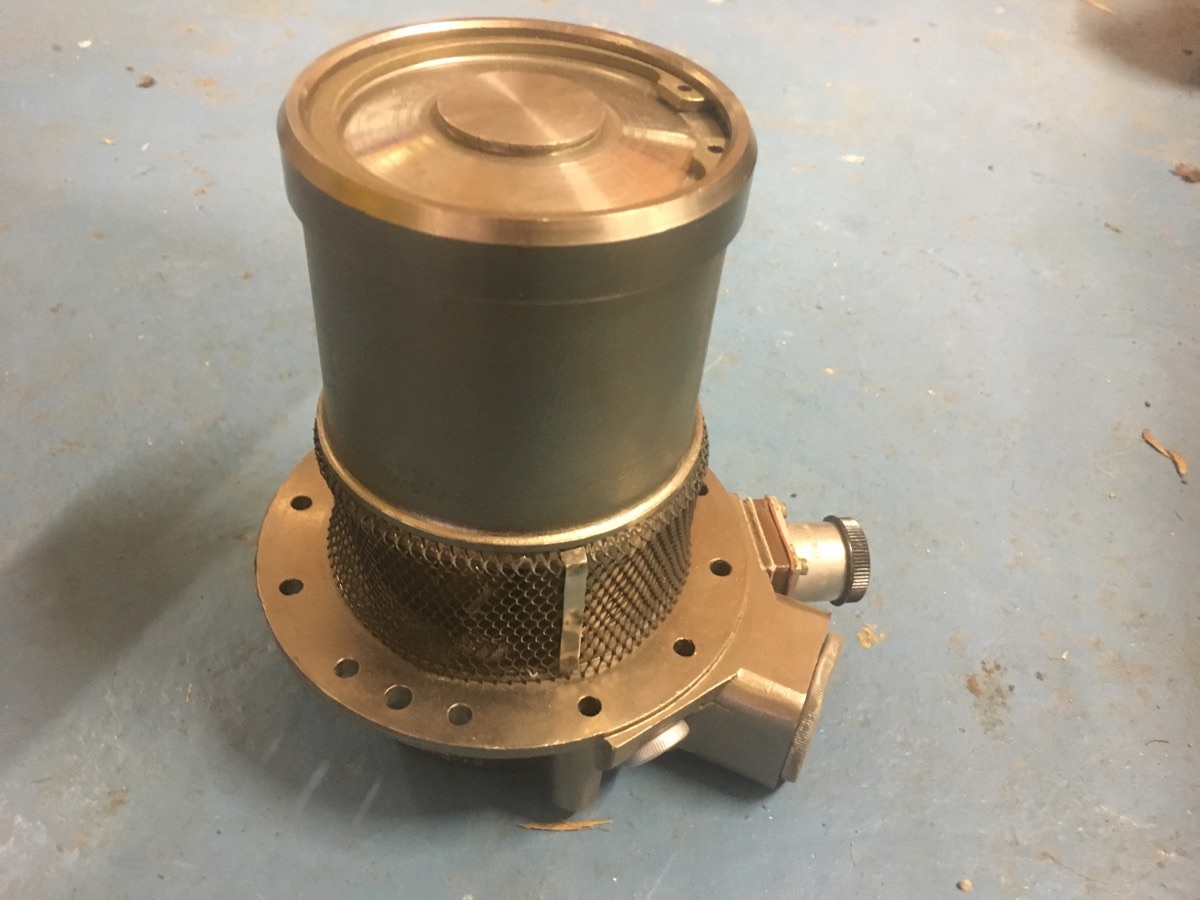
Other parts which you might not think would be any trouble to get hold of can end up really tripping you up and be difficult to obtain such as the leads that supply the electrical current between igniter units and the igniter plugs of the twin jet engines. There are two igniter plugs on each engine so with twin engines in Longbow that was a minimum of four igniter leads we required. The ends of those leads have to have metal gland ends with connections that are not metric but UNF thread to match the threads on the igniter plugs and they also needed ceramic isolators at either end. That ceramic isolator has to fit just right down the igniter plug connection otherwise there will be a lethal dose of electricity going astray which is the last thing we need in the middle of a lake, let alone the workshop.
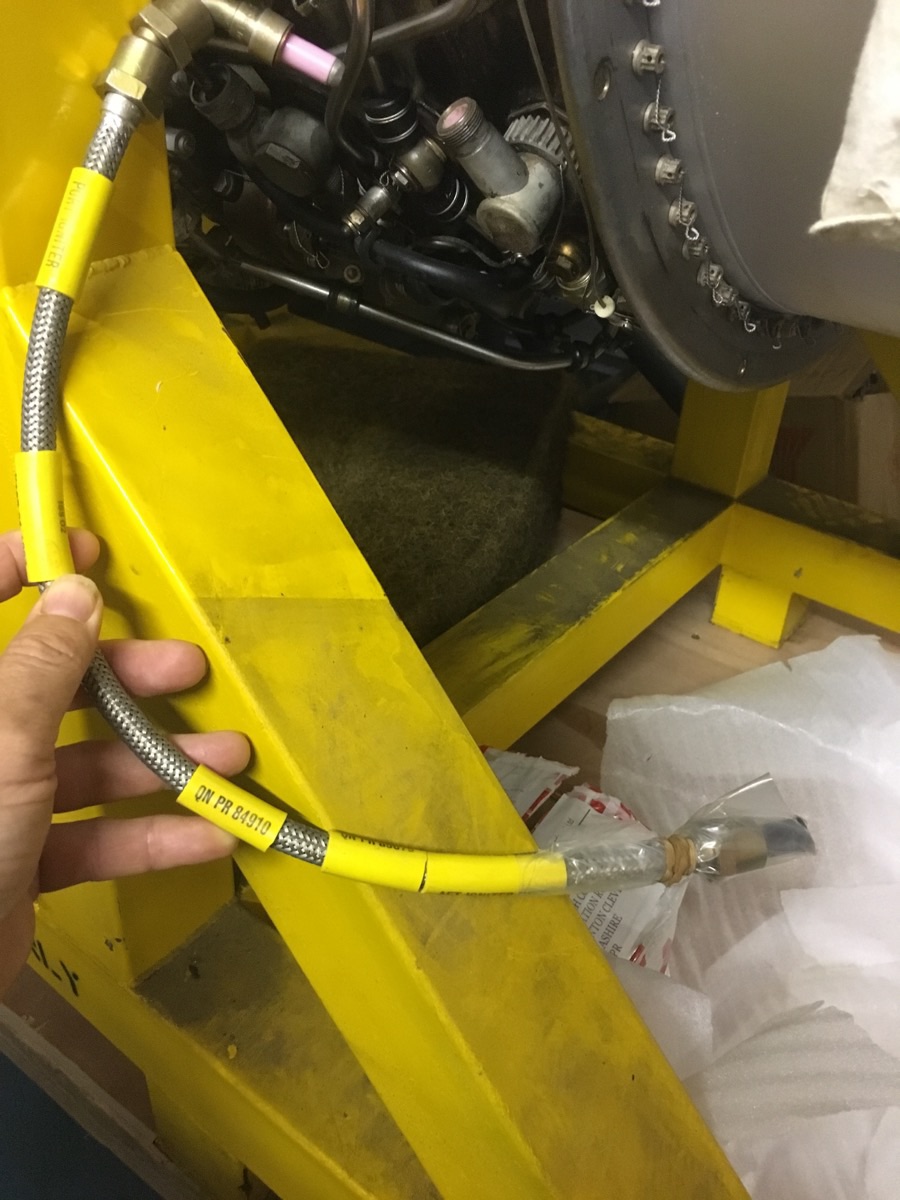
We struggled to find anything off the shelf but a very short igniter lead as shown above from the aircraft the engines had come from and even made enquires as far as the USA where a company offered to make us a set which they would normally charge out at around $1000 dollars for each lead plus shipping and import duty / vat.
Just as we were beginning to despair, Craig Baines of Task-Pro in Aberdeen, who’s company services industrial gas turbines, came to our aid. Craig saw the marketing opportunity to come on board with the venture and also a bunch of guys trying their best on limited resources trying to build the fastest boat in the world and so very kindly took pity on us by way of helping us out with this issue.
The following photos show one of their employees, Stuart McLaren of Task-Pro, making up a special set of long igniter leads for the twin Viper jet engines in Longbow, complete with the correct ceramic insulated metal gland ends. They have also kindly provided all the necessary igniter boxes too that match those leads, along with an assurance that if we need any future spares we need look no further. We were simply bowled over by Craig’s and his workforce enthusiasm to assist us making the venture happen and we cannot thank them enough for coming on board.
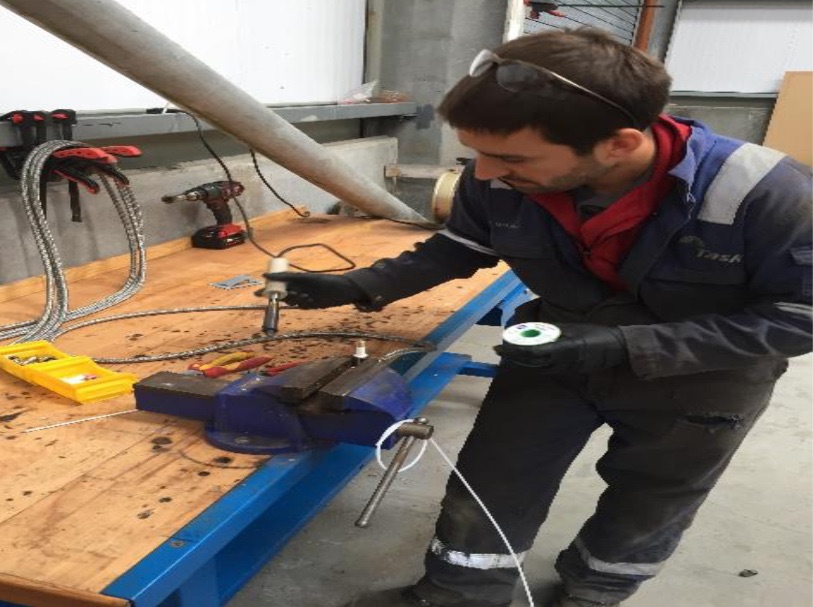
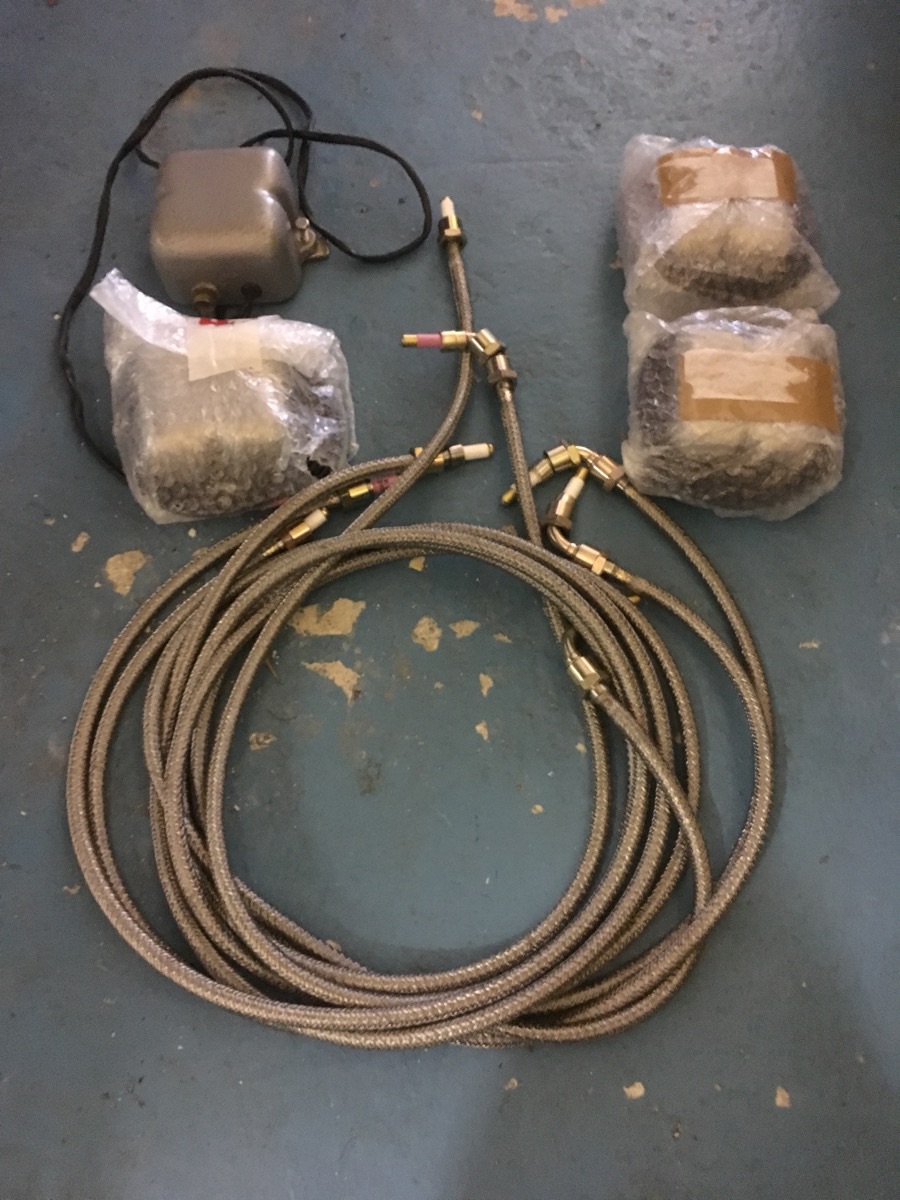
Back with the building of the hull for Longbow, this month saw us start to form the structure and curve the frames for the barrel back shape of the hull. This might not look much in the photos but it was actually quite a complicated time consuming exercise to shape. The top of the hull diminishes in height with each frame, the sides of the hull are coming in with each frame and the main stringers are also curving in with each frame but not at the same rate as the outside of the hull, so nothing is constant as a reference.
In order to form the curves of barrel back, this was at its most acute made from solid white oak, suitably prepared, as shown in the photograph below, that was fixed into place using West System G/Flex 650, which is a special grade of epoxy for difficult to bond woods.
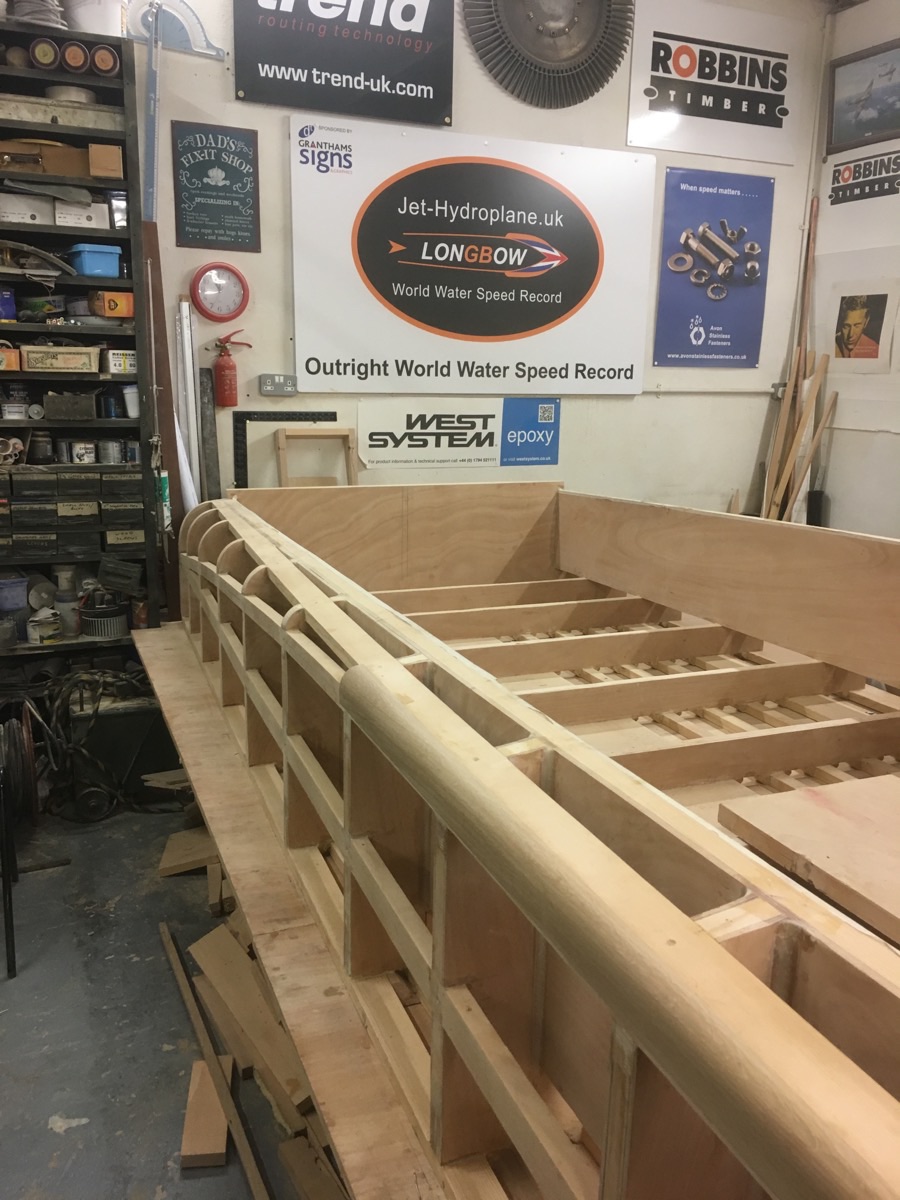
As the curve begins to open up, thin sheets of marine grade sheet ply will then be laminated into place on to the curved frames from where the white oak finishes, back towards the transom, until sufficient thickness is obtained. The white oak and thin grade plywood being so very generously provided by Robbins Timber, another of our product sponsors. Moving to the front of the hull additional laminations of Sitka Spruce also went into the top frame this month.
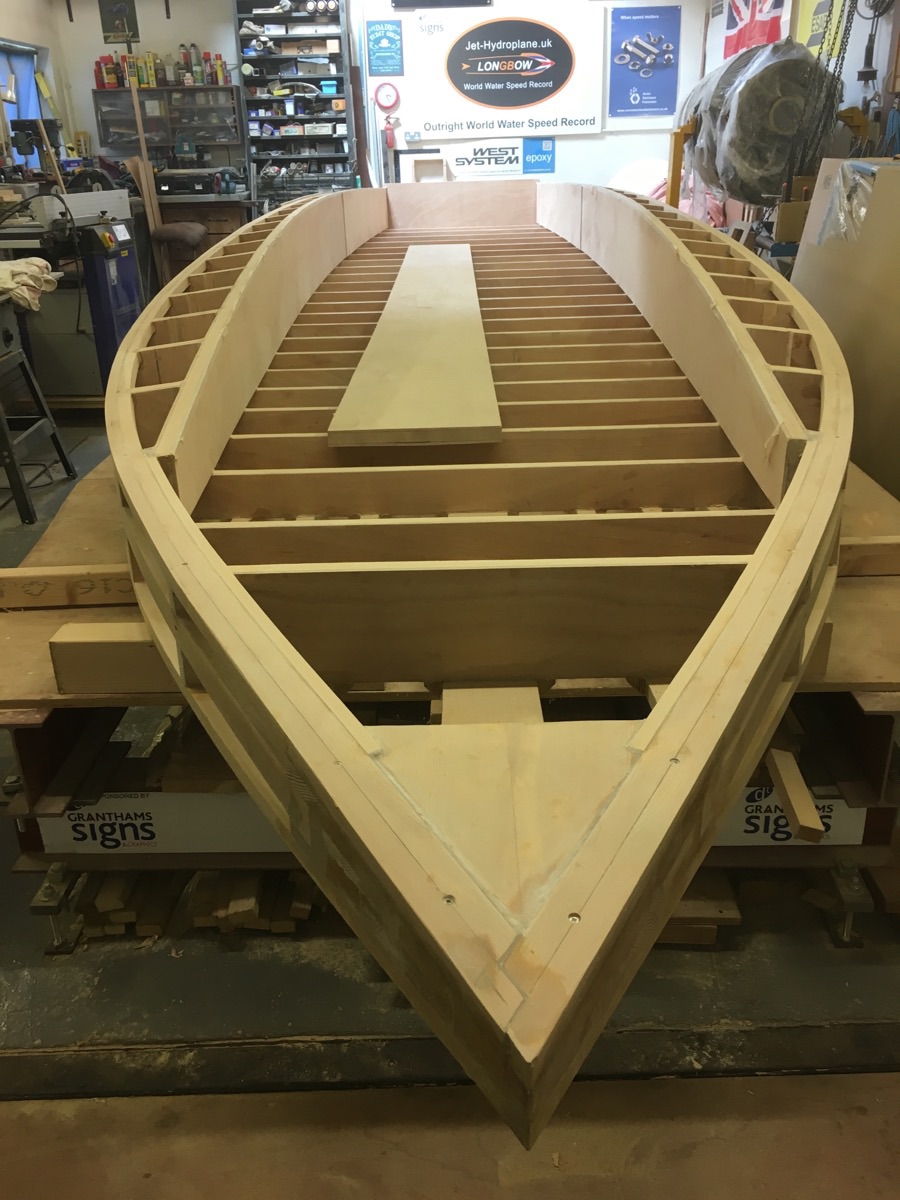
As the next job now is to take the hull back outside, sit her down and turn her back over again, so we can begin to start looking at skinning the underside of the hull of Longbow; we thought that given it will be a while before she is the right way up again, we would take the opportunity to put the driver capsule buck into the hull and sling over one of the pair of Viper 535 jet engines, for a trial fit. We are having a purpose made engine lift fabricated at time of writing this diary update which we will report upon next month so apologies for the makeshift hoist we had to rig up as shown in the following photo.
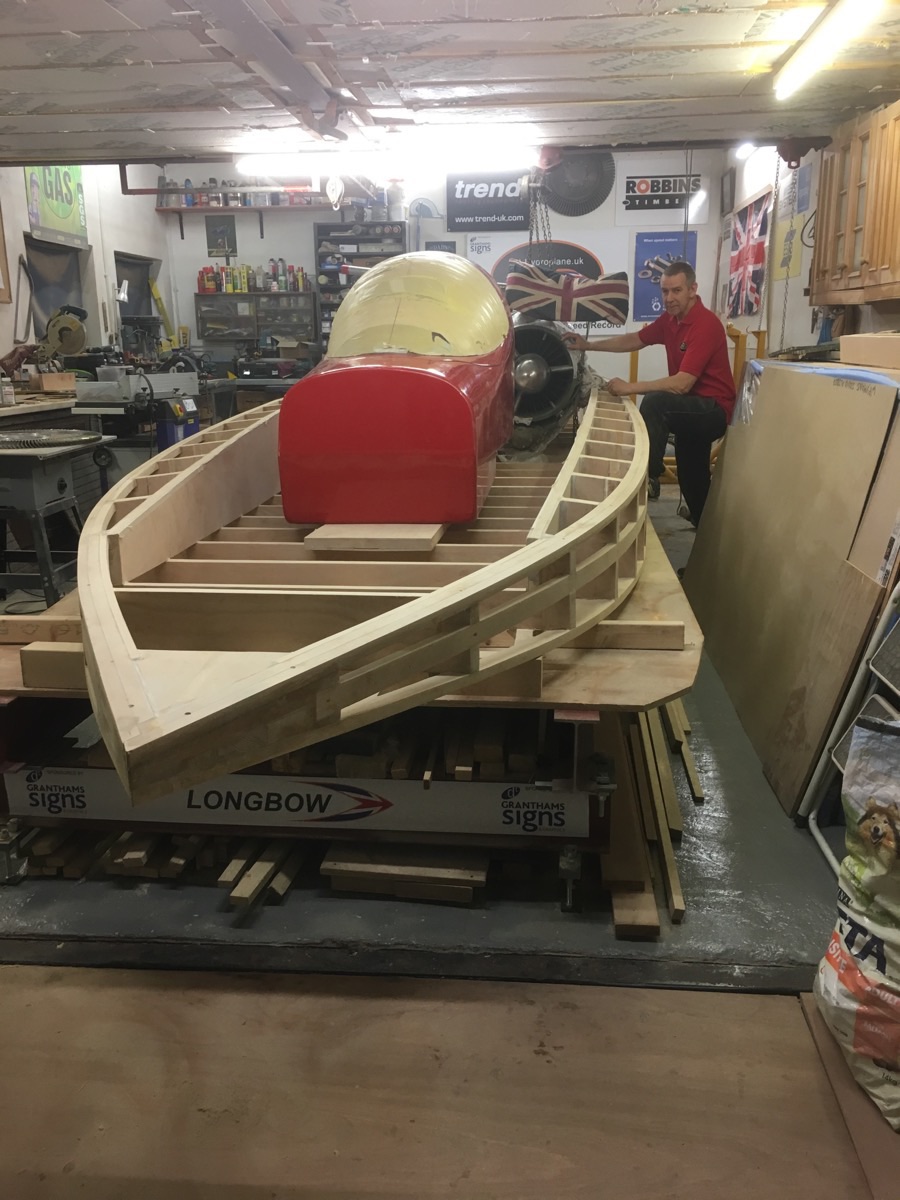
We hope our good friend Dave Warby makes a speedy recovery after his operation to mend the broken bones from his workshop tumble. All being well he will be match fit for when they return to Blowering Dam in Australia, at the end of next month to undertake the next round of tests with Spirit of Australia II. As always we wish him and his team, calm dry weather during those tests and every success.
That is all for this month folks, thank you for tuning in and please spread the word about our exciting venture, with student participation under STEM, to attempt the Outright World Water Speed Record for Britain. Liking our Facebook page helps you stay in touch to follow our progress, with the updates being issued towards the end of every month to keep up with each stage of the build of our jet hydroplane Longbow.