Welcome to the first Longbow update of 2021 and no I am sorry the boat didn’t get finished over Christmas so I am afraid you will have to put up with more of my odd sense of humour and appalling grammar over the coming year as the build continues. So as you pull up a chair, have a brew and read my ramblings I hope if nothing else that I can make you chuckle at all the mistakes I inevitably make along the way and tell me under your breath that you would be doing this in so many other ways but you cannot help but look forward to the next instalment at each month end.
For me a lot of time has been spent in January on vacuuming and I don’t mean cleaning the layers of sanding dust in the workshop. What I am referring to is starting to get my head around a skill set that I have never done before but am going to have to learn and that is vacuum bagging for some of the tasks that lie ahead with the building of our jet hydroplane.
My only experience with vacuum bagging to date has been shoving clothes that the family are never going to wear again but refuse to throw out, into a plastic bag then attaching the Hoover and sucking all the air out until the package is reduced to half its size, before tossing it into the loft never to be seen again. What I have to start learning is applying the same principle of using a vacuum to compress WEST SYSTEM EPOXY from our Sponsor Wessex Resins and specialist materials such as carbon fibre together to make composite elements of the build.
Fortunately I am not just having to rely on YouTube videos for guidance as I have my good friends composite design engineer Paul Martin who worked for a time at McLaren and has been such a help to Rosco McGlashan with his land speed record car Aussie Invader 5R aiming for 1000mph, in addition to my other good friend Dimitrios Apostolakis of our sponsor Fibermax Composites who are providing the specialists fabrics and a great deal of supportive products.
The principle goes back to my school days where I remember the earth’s atmosphere is heavy and pushes down on us and everything else at sea level with a force of around 14 pounds per square inch (psi). That may not seem like much and indeed we don’t notice it as we are accustomed to it from birth but over a square foot that is a force of 2,016 lbs which is getting on for an imperial ton. That force is so much more than you are ever going to achieve with workshop clamps or weights and what is more it is a completely even pressure across the surface being held down rather than a pinched point load of say where you fix a clamp compared to the surrounding area.
In reality apparently you would be very lucky to see a vacuum bag pull down to 14psi and more likely anything between 6-12.5 psi is typical but even so that remains a considerable amount of compressive force. Another advantage of vacuum bagging is it allows you to control excess adhesive in the laminate resulting in higher fibre to resin ratios, which in turn I am told produces higher strength to weight ratios in addition to reducing build costs.
So first on the list in my vacuum bagging apprenticeship was to source a suitable vacuum pump given plugging the bag into the Hoover just won’t cut it for the tasks that lie ahead. After much discussion with Dimitrios and Paul we decided upon a rotary vane oil bath lubricated vacuum pump of industrial quality would be required and very kindly Chris Platt, Technical Manager for Becker UK Ltd offered to provide one of their superb pumps as a new product sponsor for the Project.
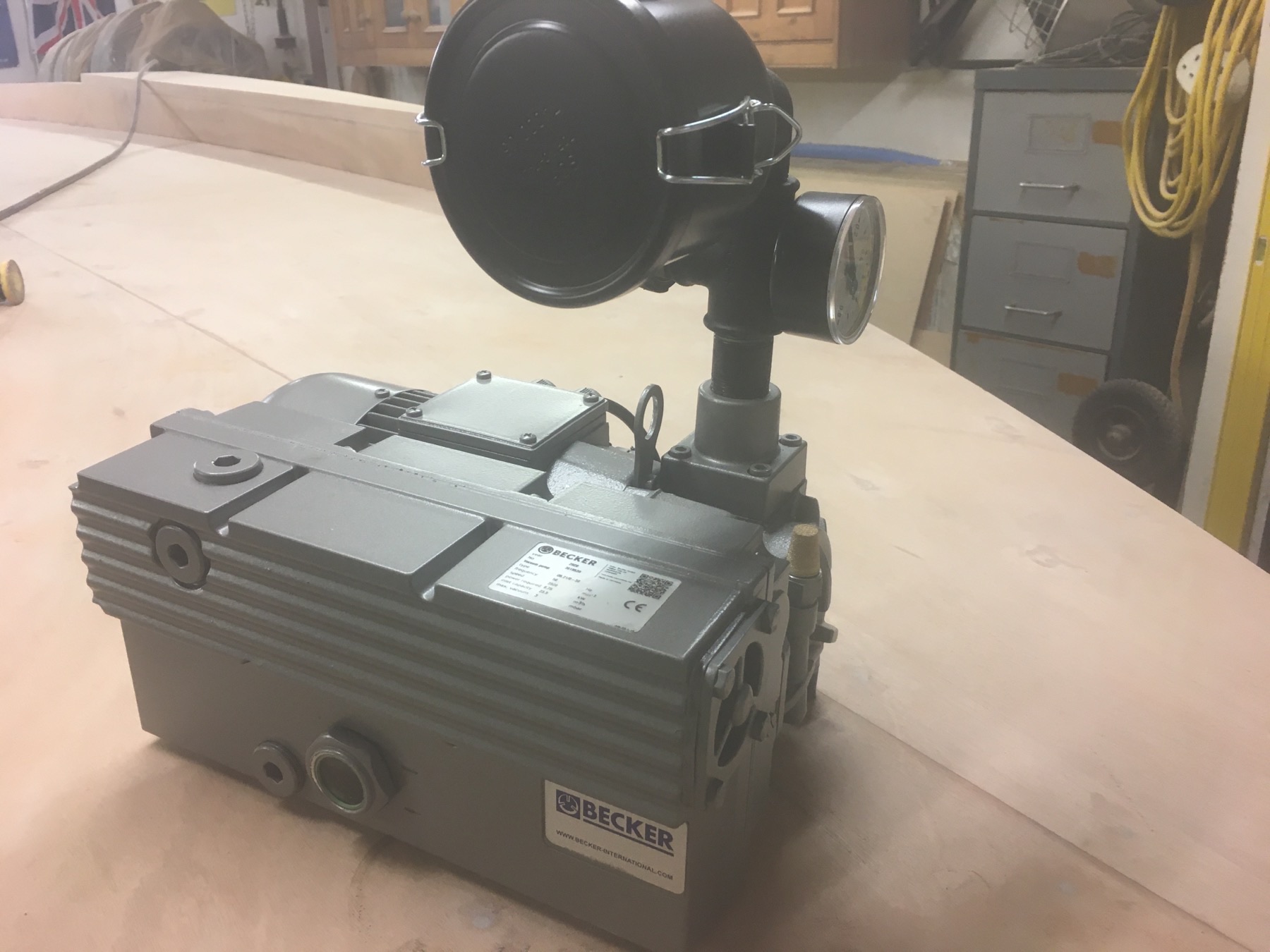
Now the vacuum pump has arrived (and what a superb well made piece of kit it is) we are just awaiting some vacuum consumable product and associated equipment from Dimitrios at Fibermax Composites in Greece to also arrive and we can experiment on forming some sample sections before applying the process on certain elements of Longbow. As this will be our first delivery from the company based in Greece since Britain left the EU we are nervously hoping there will be no undue hold ups with the shipping of sponsorship product but will just have to wait and see.
Referring back to mentioning Rosco’s land speed record car and forever linked to it we are also sad to report that the highly skilled and charismatic design engineer John Ackroyd (Ackers to those who knew him well) sadly passed away this month and our sincere condolences go out to his family at this difficult time. John had been working to assist Rosco with the design of the car and its wheels capable of running to 1000mph for many years up until his health began to fail. ‘Ackers’ was trained at Saunders Roe as a design engineer and lived on the Isle of White but was renowned for cycling all over the UK to attend meetings. He also was design engineer for the British land speed car Thrust 2 and Richard Branson’s round the world balloon project and if you want to know more about this brilliant engineer his book ‘Jet Blast and the Hand of Fate‘ is a fantastic read for all record breaking enthusiasts.
Whilst we are discussing land speed vehicles it was not unexpected to see the Bloodhound land speed record car up for sale for a second time having previously been sold in 2018 after going into administration.
https://www.topgear.com/car-news/bloodhound-sale-again
Again it is down to money apparently failing to find a further financial sponsor to stump up the vast amounts of cash being sought to further develop the car. Probably not the runabout for popping to the shops in but as you can only do so on your own during lockdown, the single seat in the vehicle should not be an issue, though the lack of mirrors, poor turning circle and economy figures might put some people off.
Although Bloodhound might be struggling for sponsors our little venture with Longbow is fortunately having no such problems despite the global pandemic. Not only have Becker UK come on board this month but also we are pleased to announce the world famous Shepherds of Windermere who’s boating roots date back to the 1890’s have become a sponsor of Longbow after Darren Grundy, their Managing Director heard about the project. Darren has been so enthusiastic about his Company assisting us and their support, expertise, knowledge and experience out on the water when it comes to running our jet hydroplane will be invaluable in the times ahead.
This month Bill Dawe got in touch with me on behalf of our sponsor RS Components and has asked us to do a series of articles / videos of the Longbow jet hydroplane venture for their DesignSpark experience. For those that are not familiar with DesignSpark the following link gives an introduction:
https://www.rs-online.com/designspark/home
I am not sure how we will get on with doing presentations but have promised Bill we will give it a go and I will let you know when there is something on there from the Project which in the first instance is likely to be an introduction of what the venture is all about.
Referring to last month’s update the feedback regarding the section on jet engines that I tried to convey in my typical ham fisted way was surprisingly very well received, so just as a little addition to that hopefully you may find the following a further helpful illustration of what was discussed and in particular the graph therein showing no pressure increase across the burner can section of the engine as the fuel / air mixture ignites. The eagle eyed amongst you may smile at one of the annotations.
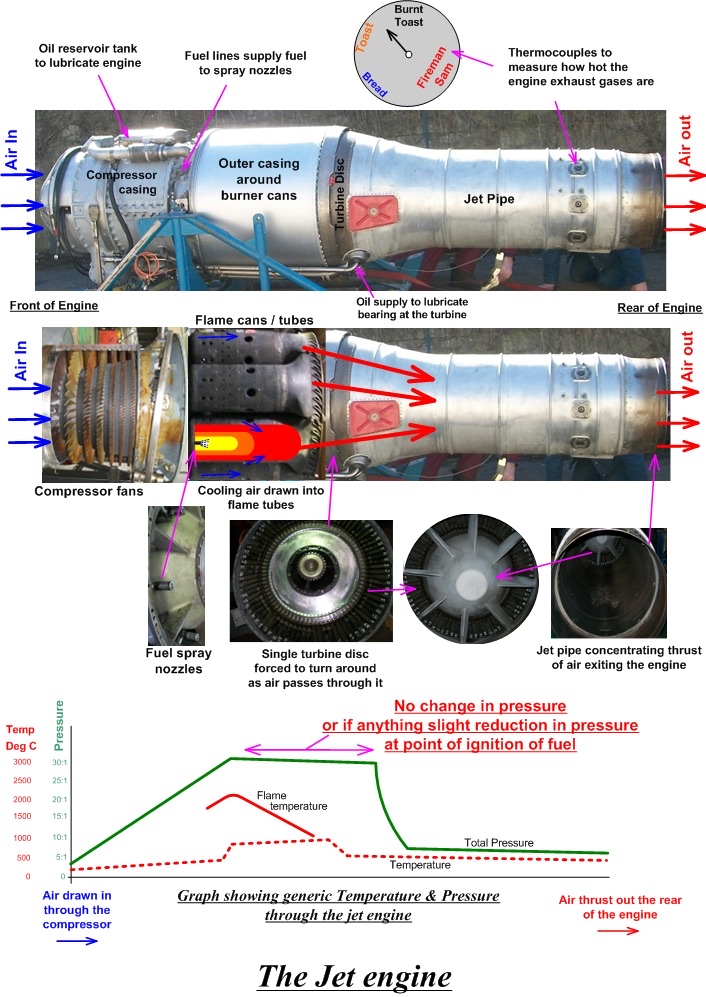
Our good friend and mentor Dave Warby reports that this month they did an exhibition show for one of their sponsors which is always nice to give something back to those that have supported the project where you can and Dave says their next set of tests with the jet hydroplane Spirit of Australia II will be at Taree towards the end of March.
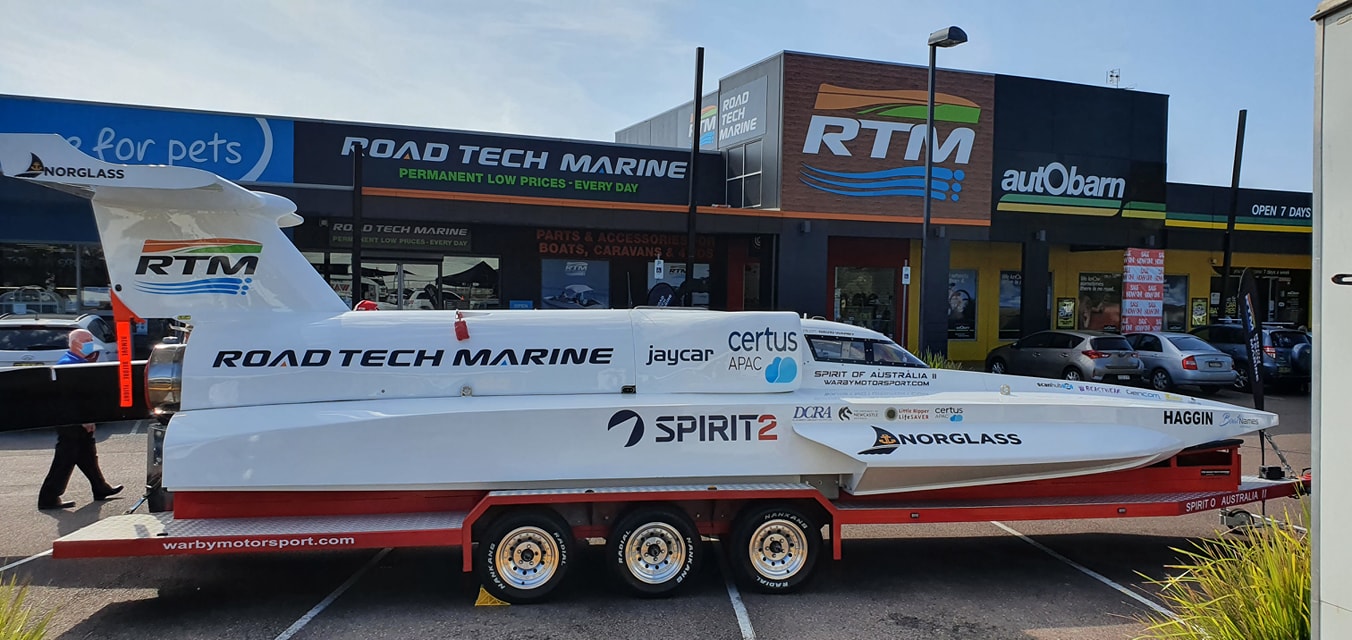
We are all looking forward to seeing them back out on the water running this awesome craft and will report back on how they get on in due course.
Back with the build of Longbow it has been something of a slow month whilst I await getting all the kit together to begin practicing vacuum bagging composite laminations which I wanted to try on parts of the planing shoes before I Dynel the whole underside of the boat. Or conversely the folk who know me well may conclude that it was freezing in the workshop despite the heater and I was too lazy to get off my butt for the first half of the month being laid on the settee next to the open fire, left over Christmas goodies and a new toy poodle pup called Ruby that is a bundle of fun to add to the other dogs in this madhouse.
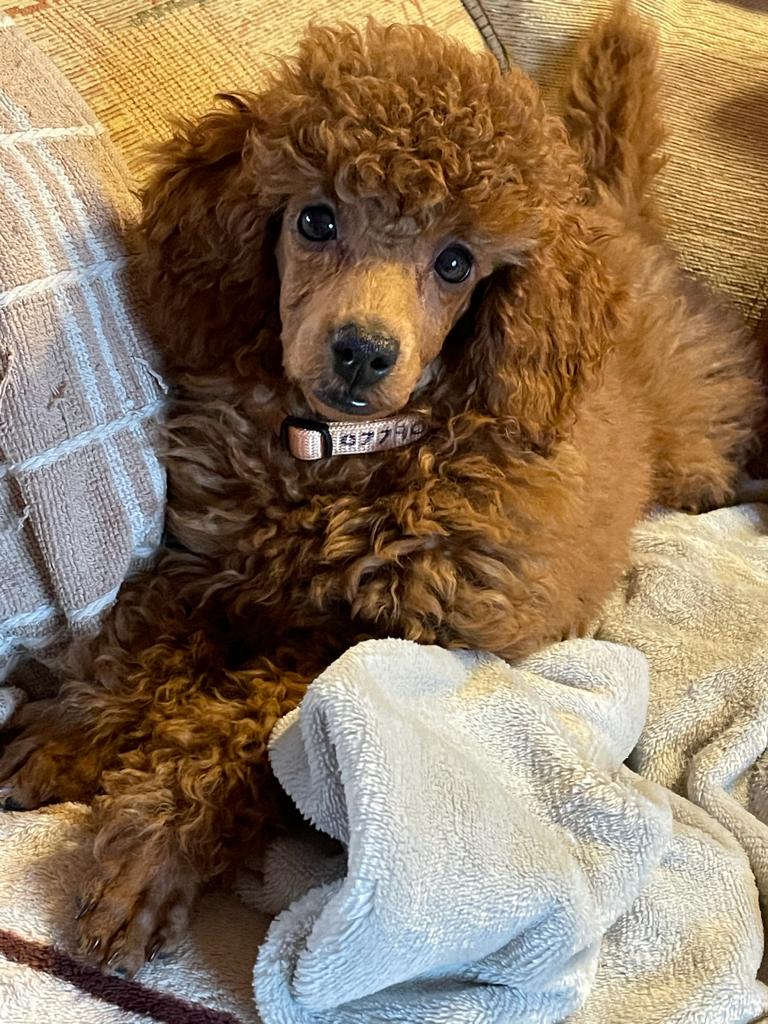
Anyway by mid January I was gaining too much lockdown lumber so it was back to the build and the next task was to fit the plywood to the rear planing shoe running surfaces as a flat sheet, in order to protect the vertical joints of the timber laminations that make up the bulk of the planing wedge. There are two angles to the planing shoe so this was a scarf joint at each end to form on the forward section.
Once that was done the Lloyds registered marine plywood kindly supplied by our sponsor Robbins Timber could then be fixed using the WEST SYSTEM EPOXY and 403 microfibre filler supplied by our sponsor Wessex Resins.
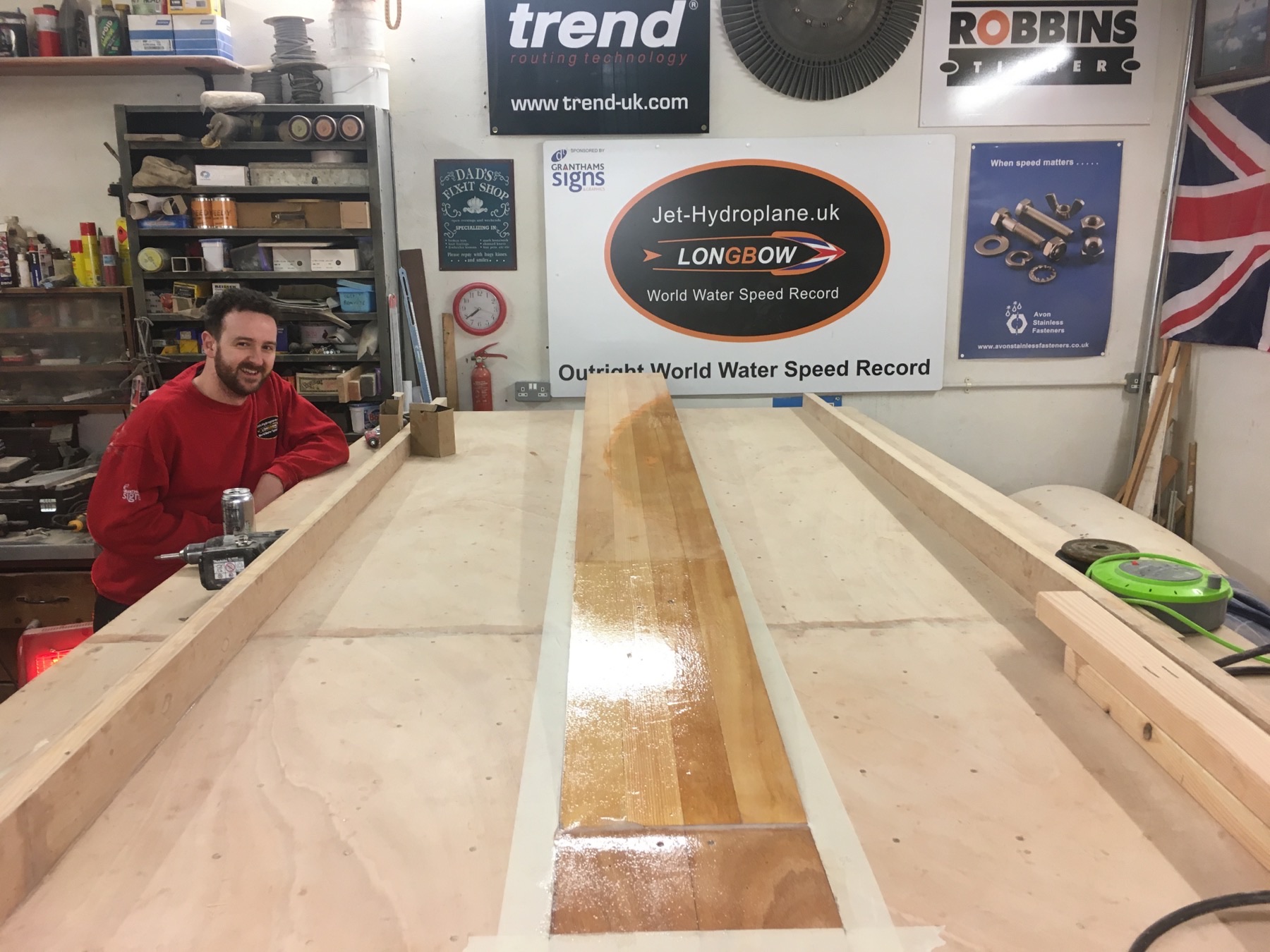
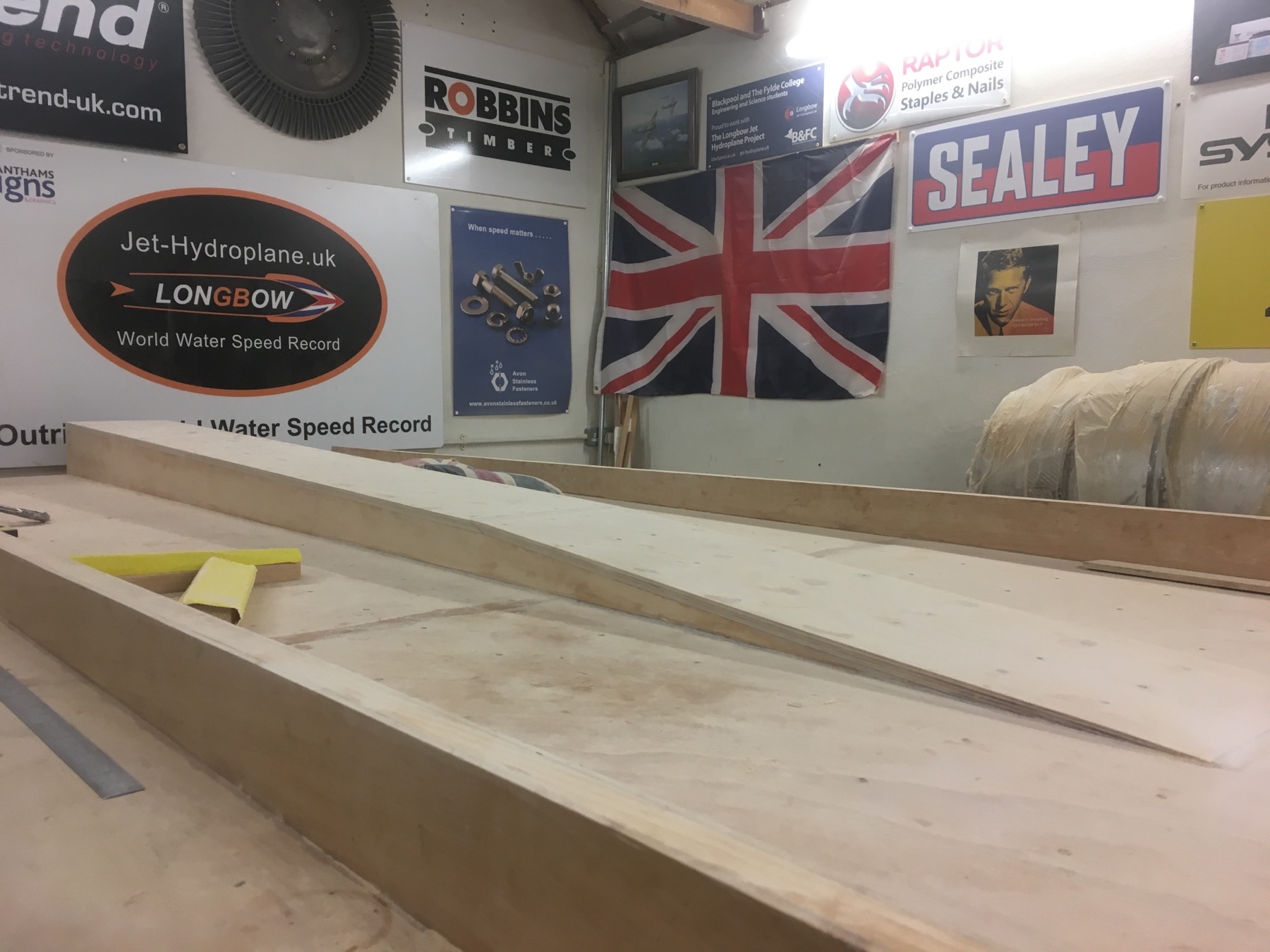
The next task after that was to apply the same epoxy and filler to all the screw heads and Raptor composite nail fixings which made the upturned hull of Longbow look more like a bad case of chicken pox.
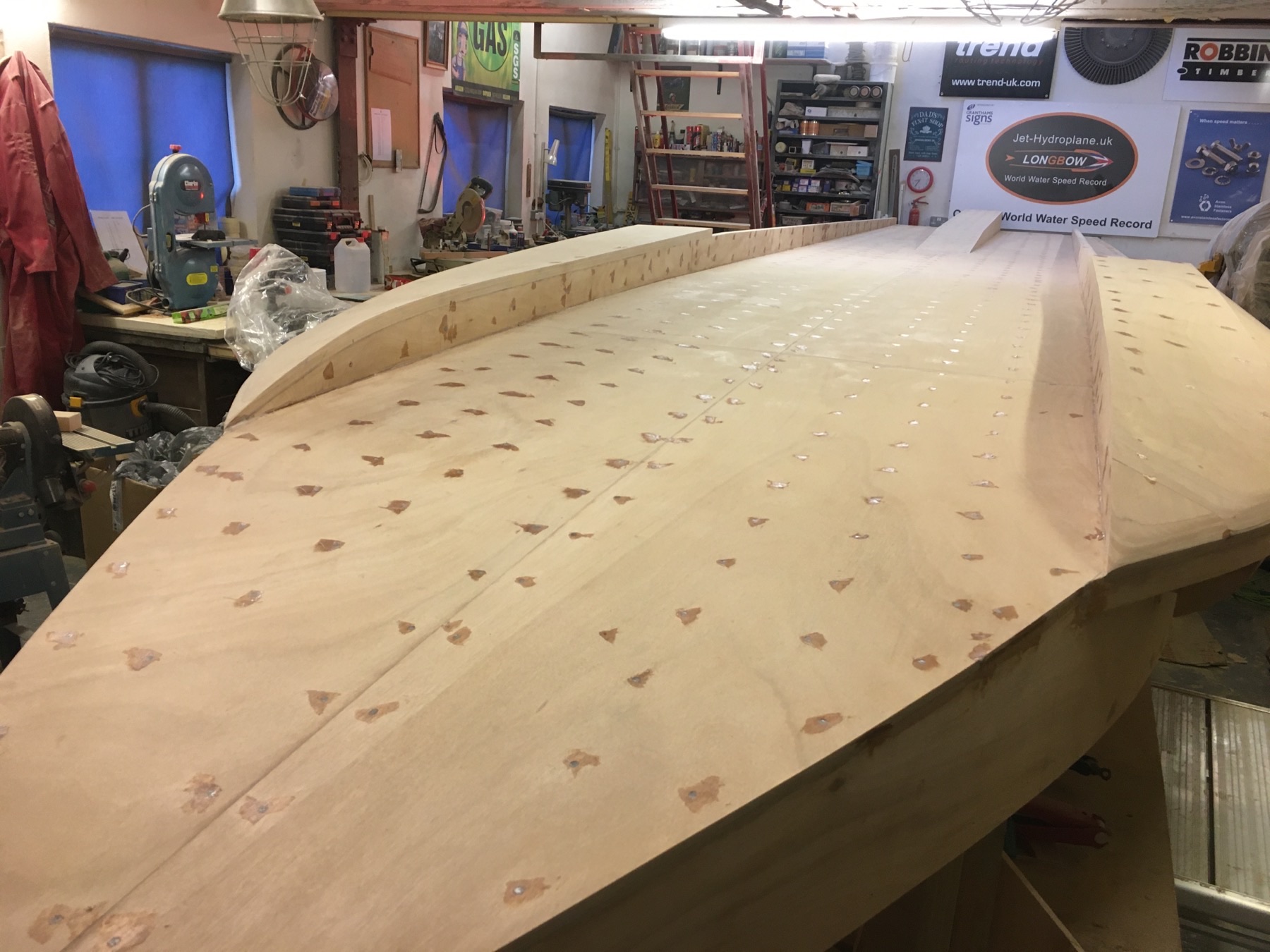
There are literally hundreds of fixing points on the hull to fill and sand down and a great little tool for this has been our sponsor Sealey Tools 50mm mini orbital sander from Steve Buckle.
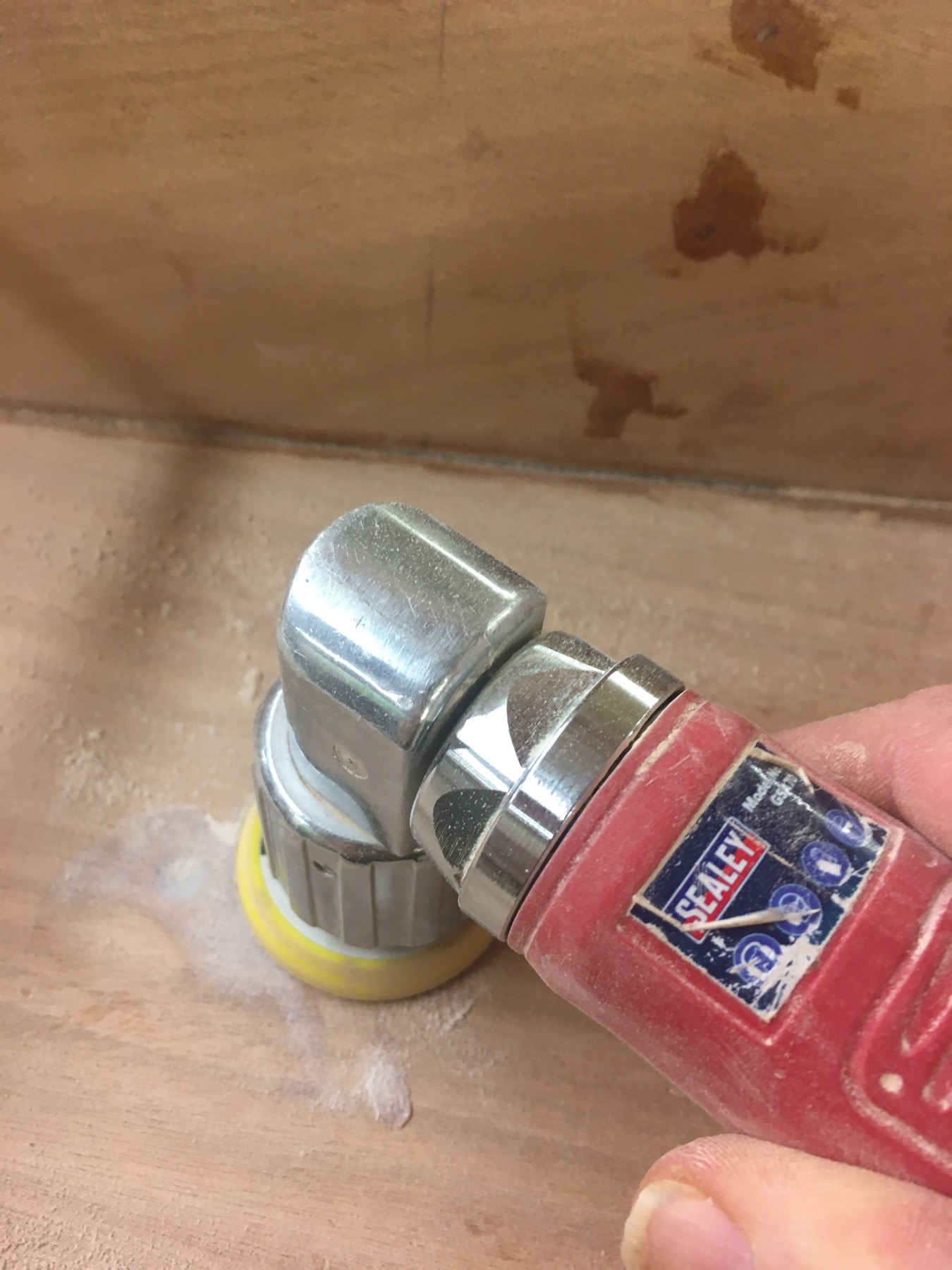
I was also very thankful to Darren Spinage of our sponsor Trend Machinery & Cutting Tools Ltd for sending us their fantastic Air Stealth Lite Pro masks and Air Mask Pro full face mask to keep all the dust out of my lungs which I cannot recommend highly enough.
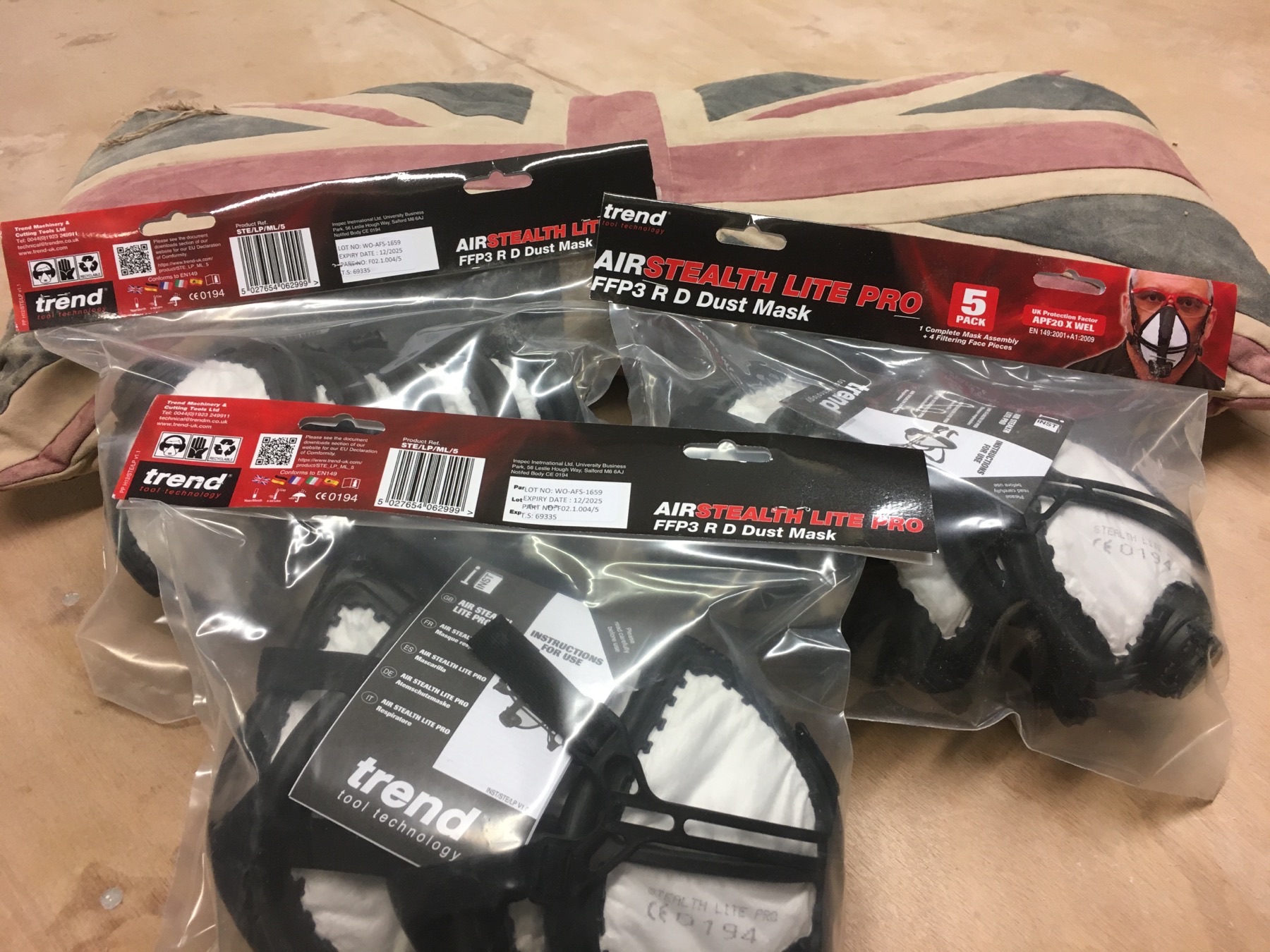
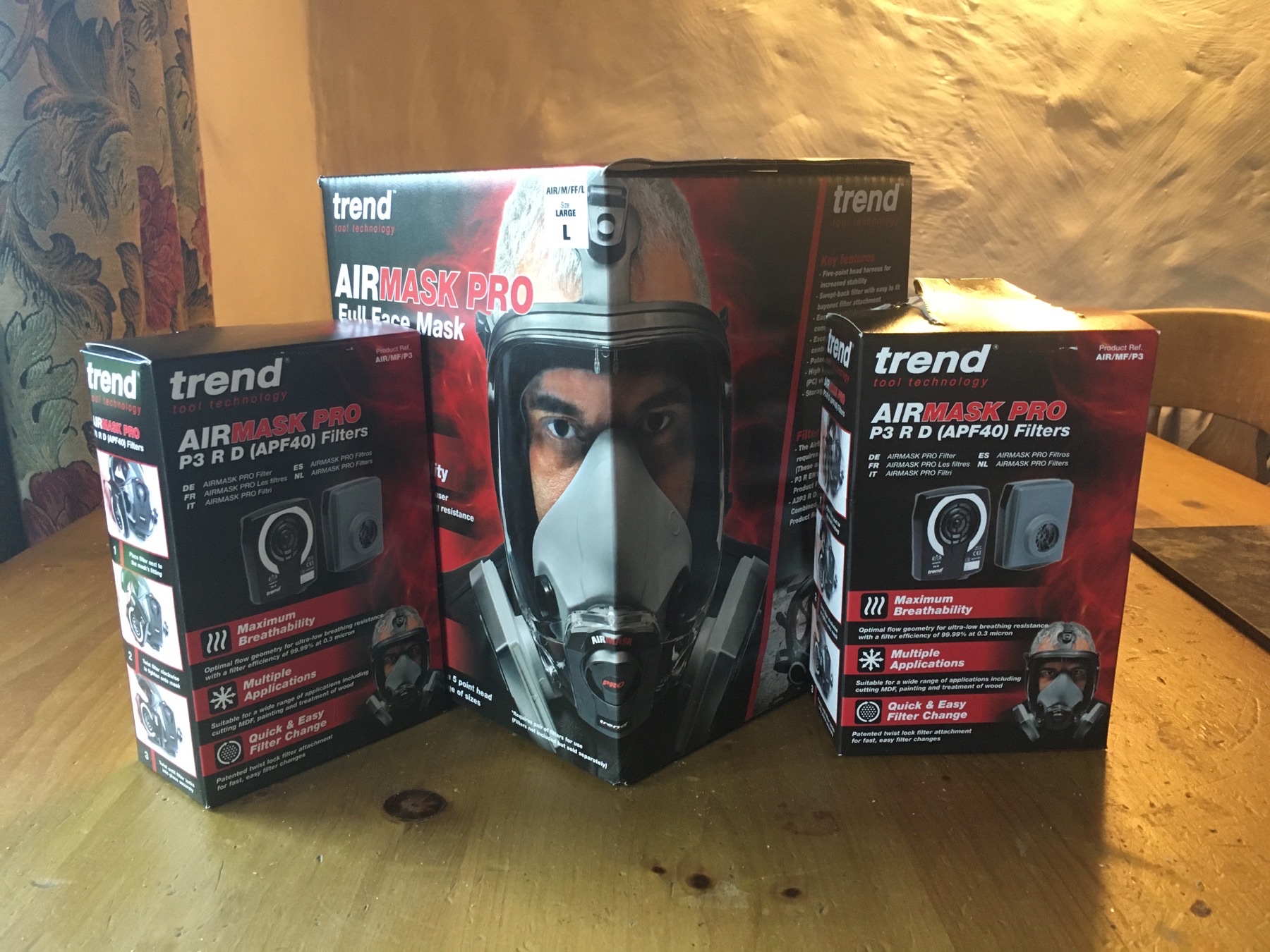
Well that is it for this month folks and thank you for dropping by to read the update. Please tell your family and friends about our little venture and if I have not bored you too much do call in next month to see if I have pulled my finger out enough to justify your approval. In the meantime stay safe and if you have not done so already a like on our Facebook page will help you keep tabs on the project.