Welcome to this month’s update which has been a little eventful, so where should we begin? In the first instance probably with a lesson learnt of not to just assume something without checking it yourself first. In our case that applied to the two jet pipes, one for each of the engines within Longbow.
In order to obtain the best performance for the engines in the aircraft they are derived from, the thrust that is produced out from the rear of the engine, passes directly into a circular metal pipe that in the case of our engines reduces in diameter. This has the effect of rather like putting your thumb partially over the end of a hose pipe to obtain a more powerful water flow.
In order to achieve this as simply as possible there is a short intermediate section of jet pipe around a couple of feet long that has a large diameter end connecting to the rear of the engine and then reduces in diameter to connect to the rest of the longer jet pipe length.
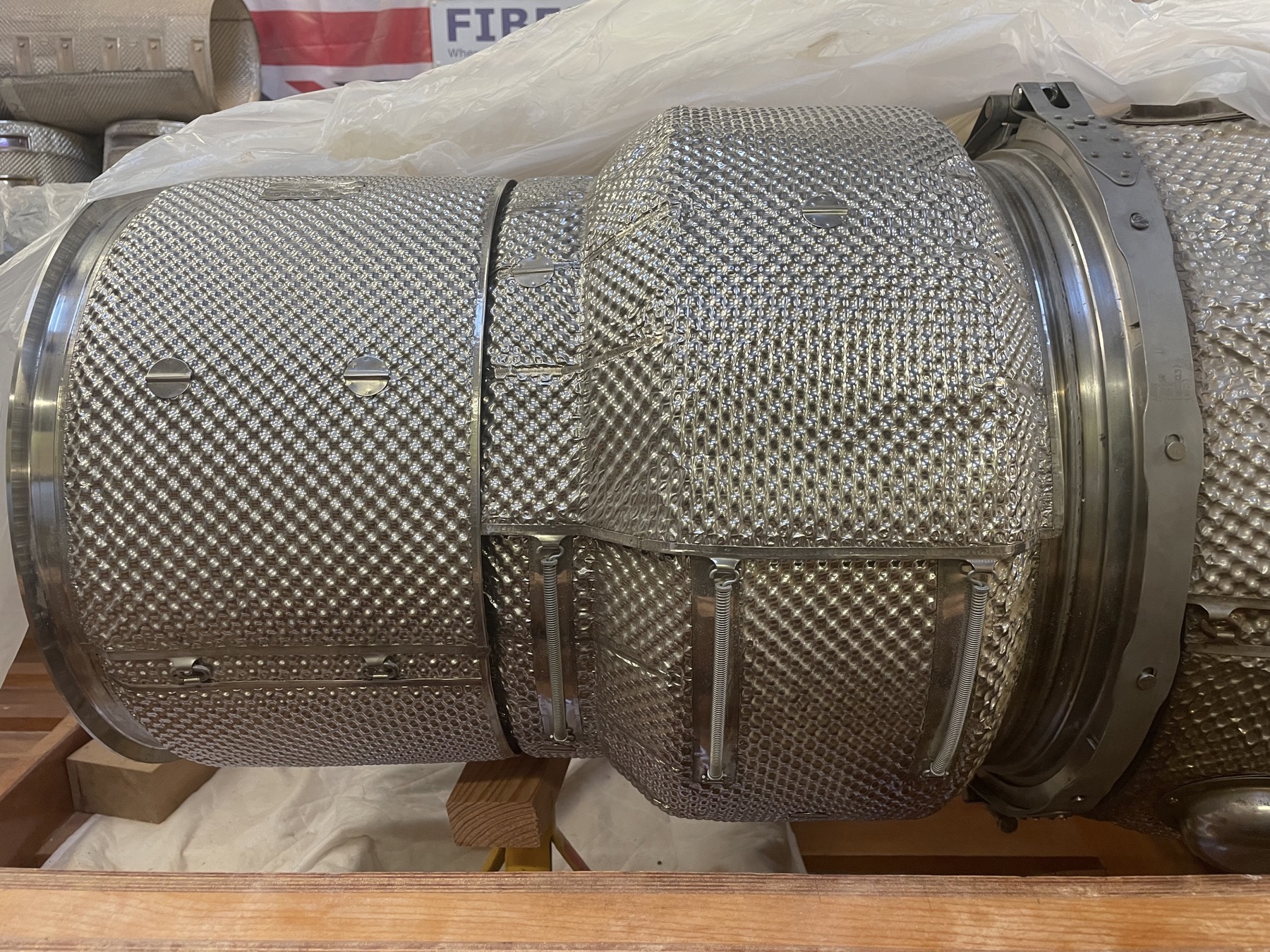
Both of these connections, one to the main engine and one to the rest of the jet pipe, are achieved by a circular metal strap with an internal ‘V’ shaped groove that acts to hold two flanges together on the respective mating surfaces. Tension to the clamps is achieved by tightening a couple of bolts with specially shaped spacers and nuts.
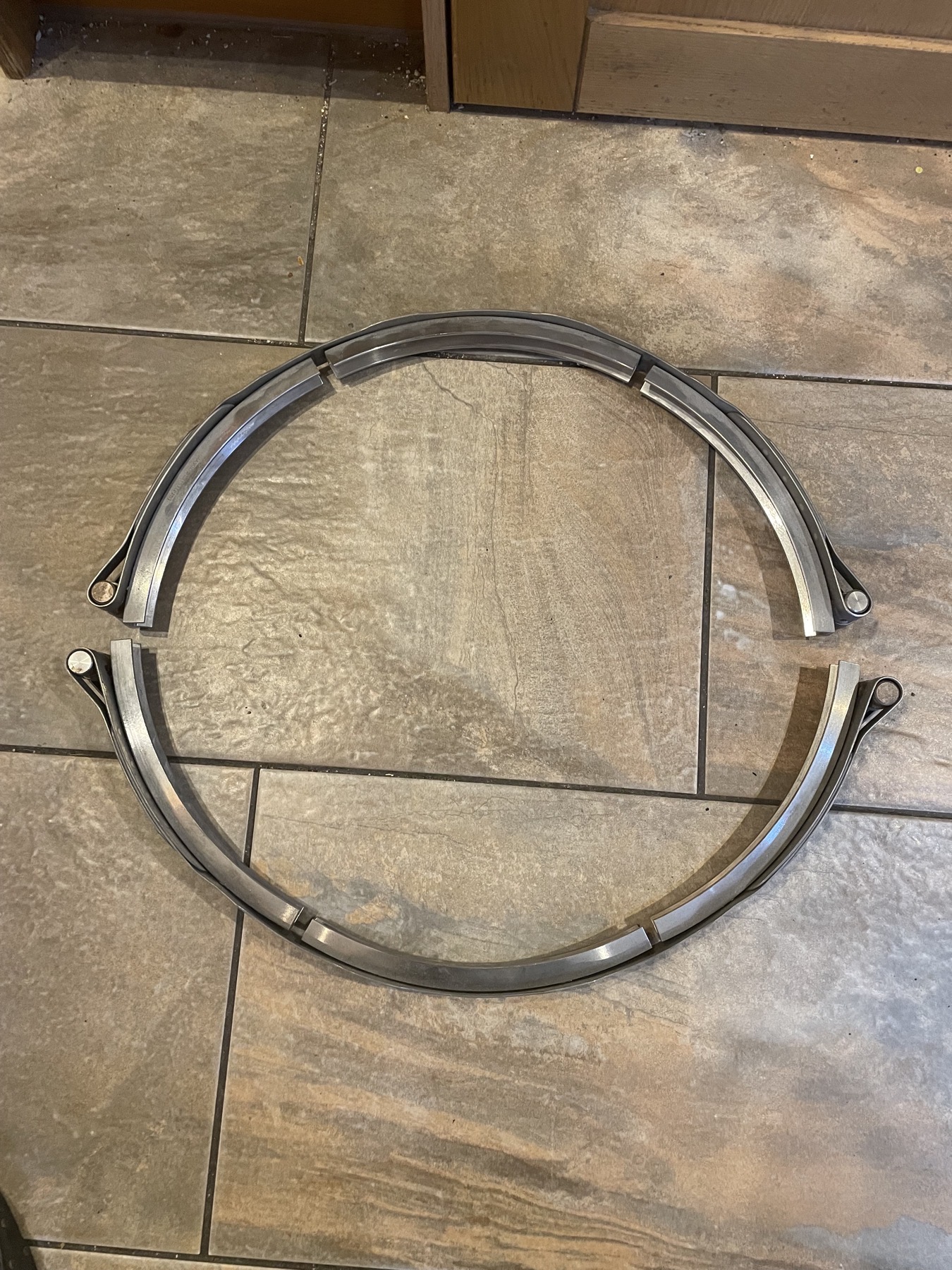
All of this assembly is called a ‘Marman’ type clamp and is often lighter than a bolted flange connection, where with the latter the flanges would have to be more substantial to accommodate the many bolts around the pipe circumference to obtain a gas tight seal. Marman clamps are used extensively in aircraft pipe connections and even in space vehicles. For example where stages of a booster rocket are held together by Marman clamps until explosive bolts holding the clamps together are purposely detonated at the appropriate time in order to allow separation of the various rocket stages.
Anyway back with Longbow when we purchased the engines, the intermediate section of jet pipes, final stages of jet pipes and respective Marman clamps to fasten everything together all of this had been what is termed as ‘new old stock’ and heavily packaged in various anti corrosion wrappings, plastic bags and timber crates. As things were needed I unpacked each item so initially the intermediate section of jet pipes and their respective large diameter Marman clamps to attach them to the rear of each of the engines. Next was to retrieve and unpack the smaller diameter Marman clamps required to attach the other end of the intermediate jet pipe section to the final stage of jet pipe.
As I searched about in our stores where we keep all the engine bits there were only two circular packaged parts left but when I started to unwrap them, it was one of those ‘Houston we have a problem’ moments.
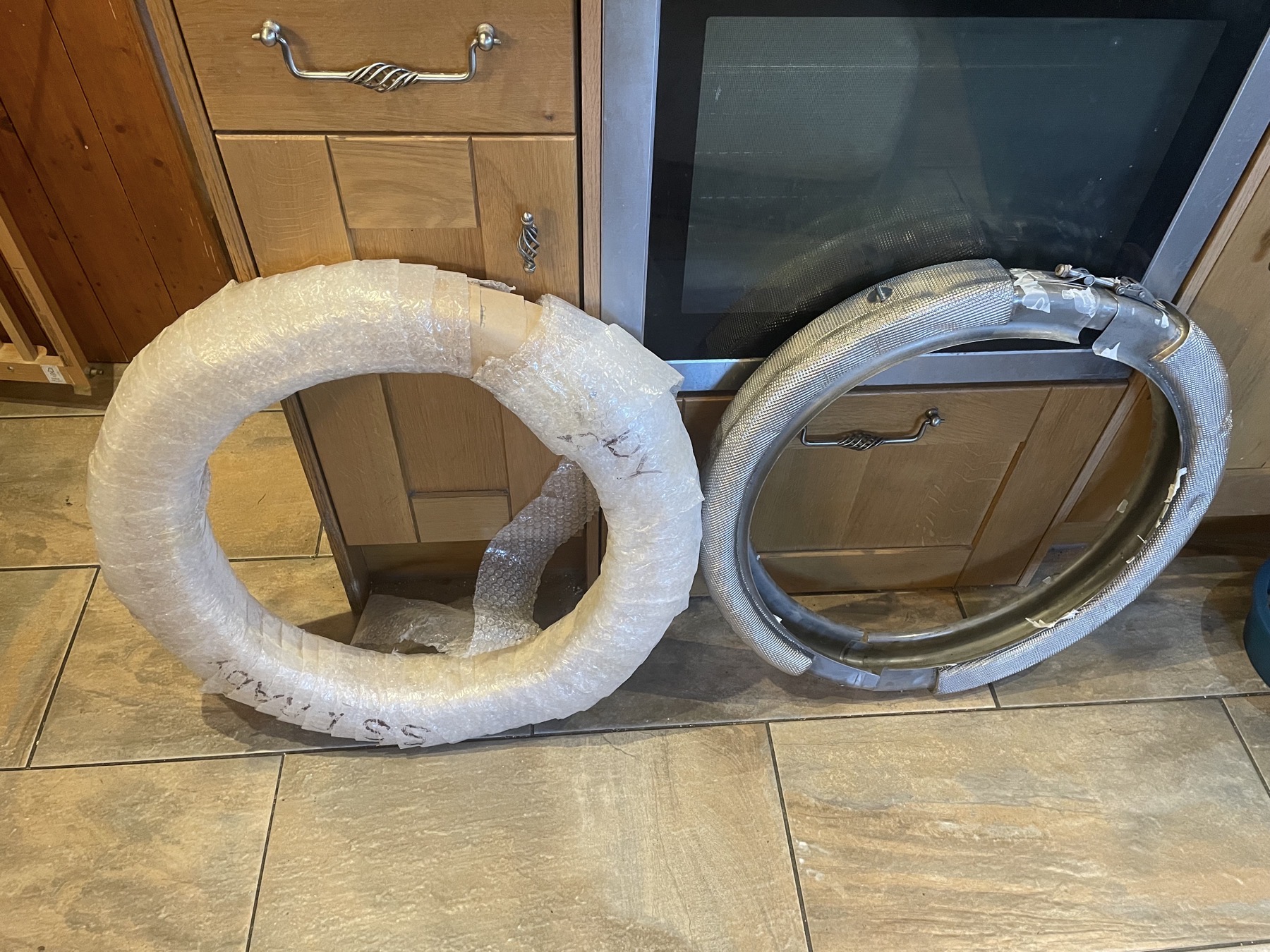
What were supposed to be the smaller diameter Marman clamps turned out instead to be only the heat shields that go over the Marman clamps. Now there are only about twenty Strikemaster aircraft still flying worldwide that these engines were originally meant for. Consequentially the operators of those few historic aircraft quite rightly want to retain parts for their own use. A series of phone calls and emails managed to get us one of the correct Marman clamps for one engine but I was still short of one Marman clamp for the other.
The clamp itself is a more complicated thing to replicate than you might think given the inner V sections have to be machined just right in half a dozen sections and they are then housed via their respective locating pins into the outer clamp band.
The Strikemaster aircraft is essentially an armed version of the Jet Provost aircraft and not surprisingly for that armed role the Strikemaster was fitted with a more powerful jet engine so it could fly faster. As a plan B, further phone calls and emails sourced us a Marman clamp from the Jet Provost aircraft. The ‘V’ shaped groove on the inside of the Marman clamp was thankfully the same profile but the diameter of the clamp was somewhat smaller than the one we needed for our engines derived from the Strikemaster aircraft. This reflecting the less powerful engine in the Jet Provost compared to the Strikemaster. It was close but unfortunately no cigar.
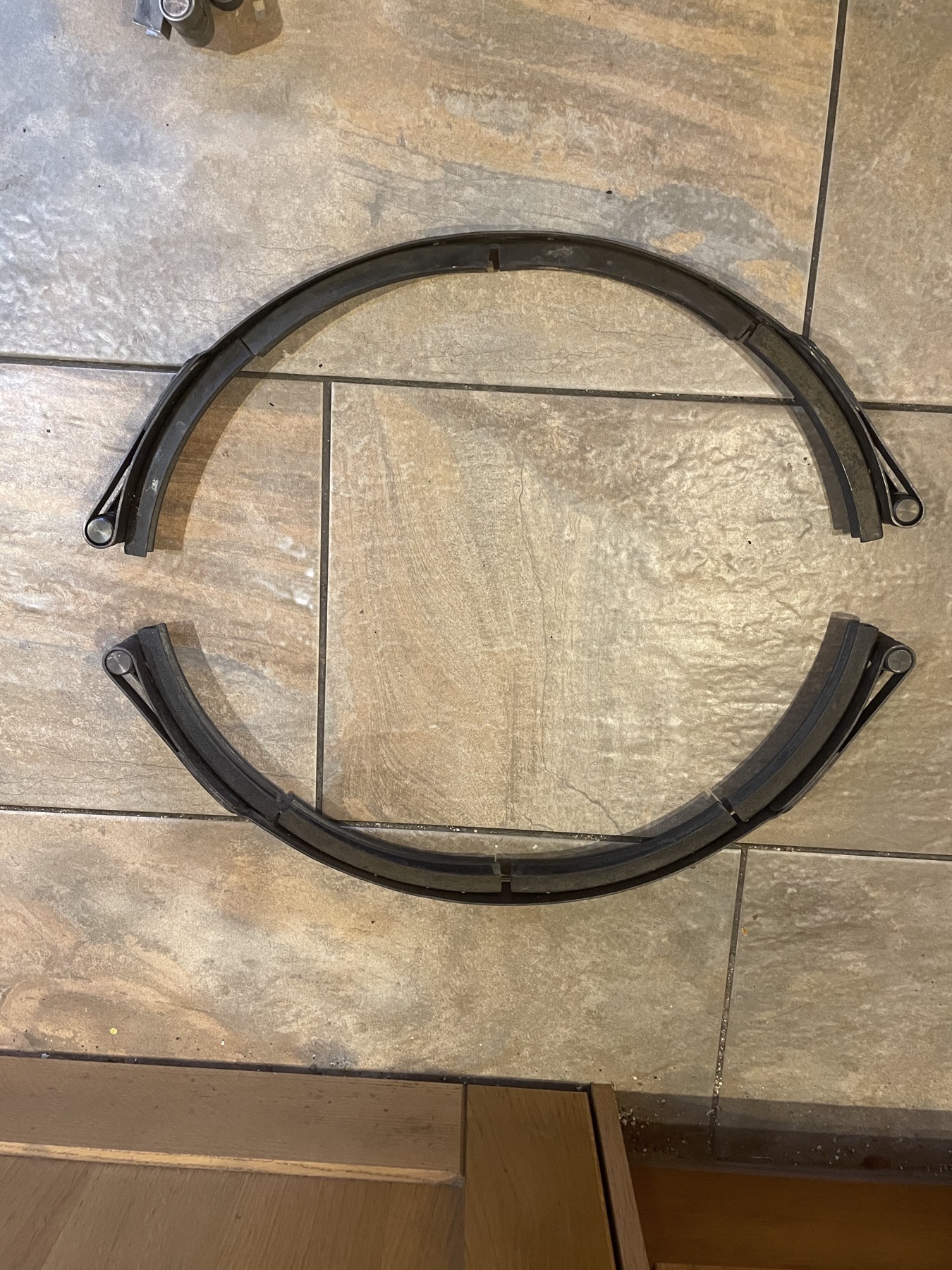
More phone calls and emails as far as Australia and New Zealand on the hunt for the correct Marman clamp eventually found us a Strikemaster aircraft with no engine but which still had its jet pipe within it. Excitedly I said yes please and a few days later grabbed the delivery box off the courier only to find the Marman clamp that had been recovered and sent to us was the one relating to the larger diameter end of the intermediate jet pipe!
I did think about cutting that clamp down to the correct size but the band is not a plain steel and so that would have required metallurgy analysis before we could attempt to weld it back together to the correct diameter which wasn’t going to be a two minute job.
More phone calls and emails on the basis that the smaller diameter Marman clamp should be there if the rest of the jet pipe assembly was and so please at any cost could they go back and have another look. Sometime later we got the call that yes the very clamp we needed was indeed there, it was just going to be difficult to reach being buried deep within the bowels of the aircraft fuselage. It was as you might imagine with huge relief that several days later our Willy Wonka parcel with gold ticket arrived by way of the correct Marman clamp we required!
Happy days at last and I could finally turn my attention back to getting on with the building of Longbow once more.
The final two sections of sponson tops on the port side of the hull were the next on the list of jobs to complete. Room in the cottage workshop to this side of the boat is somewhat limited and you can see in the following photos the series of ‘Heath Robinson’ timber props and scissor jacks required to get this task completed. We even utilised a heavy filled metal storage cabinet as that was easier than trying to drag it out of the way being full of those vintage car parts and stock metal off cuts I am probably never going to use but ‘keep just in case’.
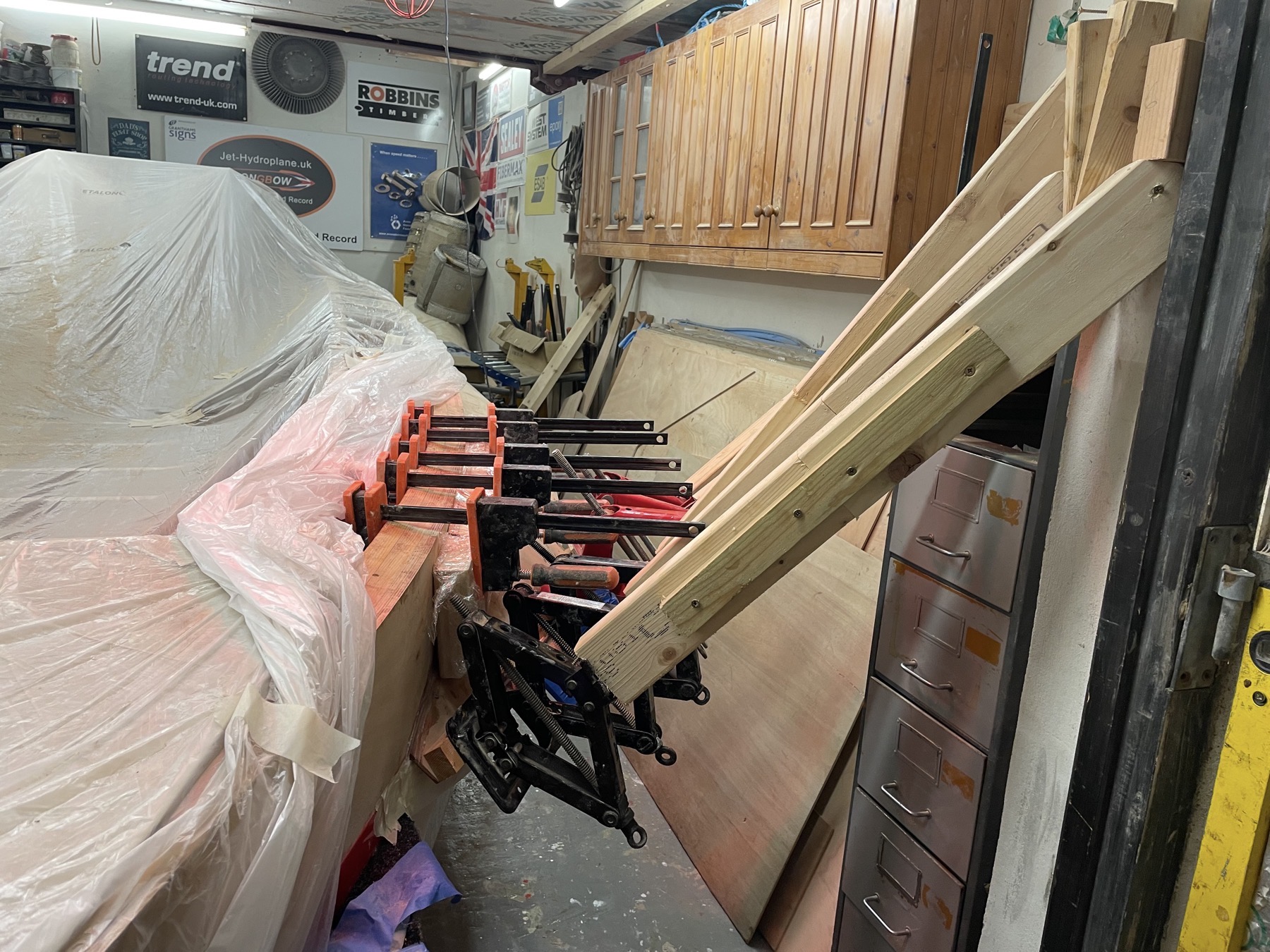
Anyway it all worked out rather well and thankfully all the sponson tops are now fixed into place other than some of the screw holes need filling and surfaces to be cleaned up. Many thanks with this task to our terrific sponsors Robbins Timber, WEST SYSTEM EPOXY from Wessex Resins and screws from Avon Stainless Marine.
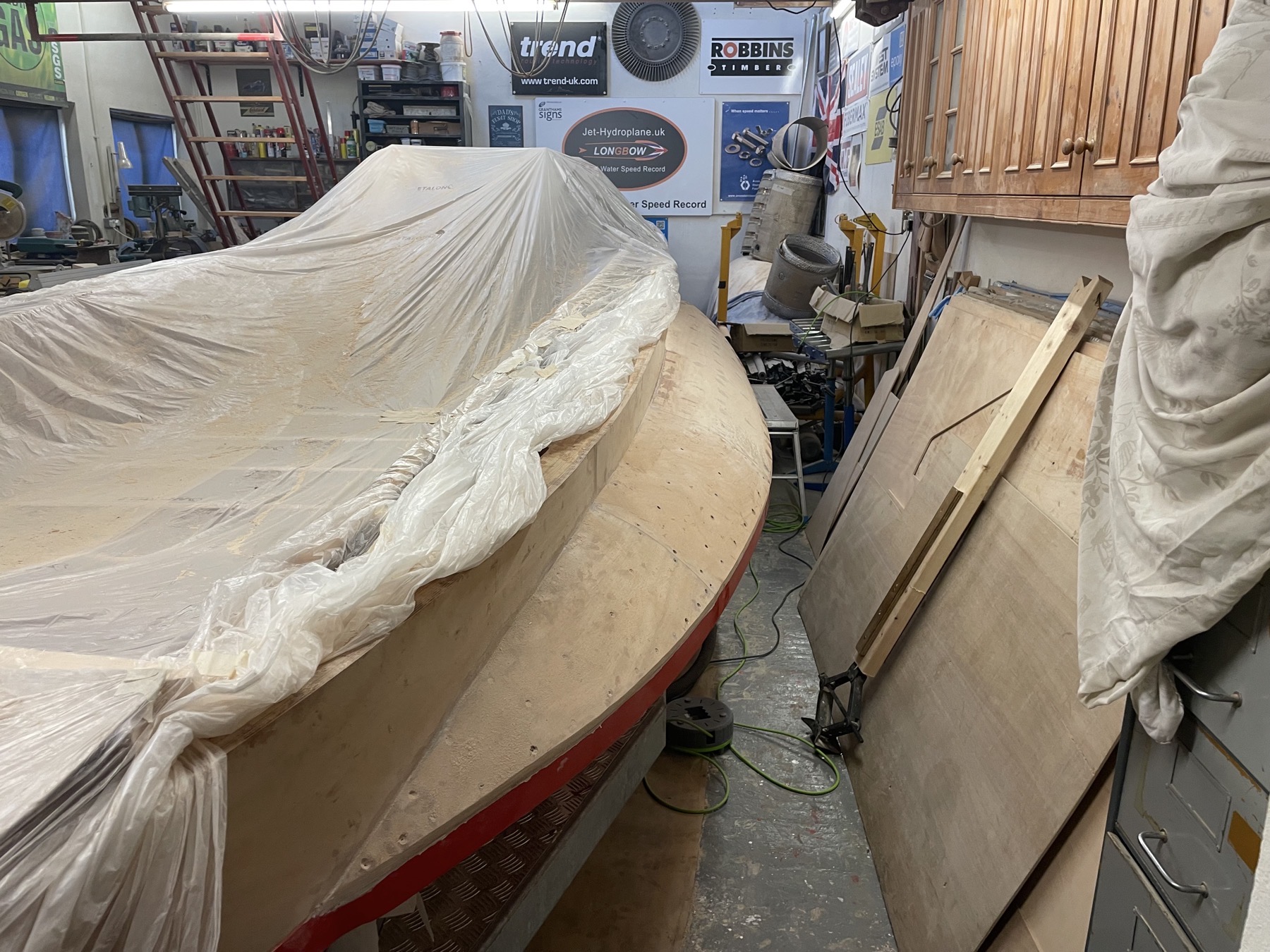
Lastly and for those that have kindly been asking how our newborn second granddaughter Annabelle is getting on, the update is she remains on a feeding tube, has a hole in the heart and of more concern, a very rare condition of chromosome 17 additions. At this stage we do not know how all of that is going to pan out but both of her parents are having genetic tests the results of which may or may not impact upon their siblings and their other child. They do say life is like a box of chocolates but whatever the outcome I am sure Annabelle will not be short of love and attention from all of our family and friends.
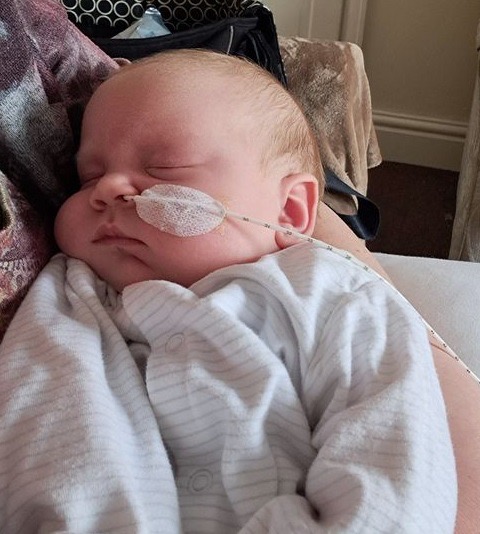
Well that is all for this month folks and I hope I haven’t bored you too much. Please drop by towards the end of next moth for our next update of building our jet hydroplane Longbow.