We all know February is the shortest month of the year but for some reason it doesn’t seem two minutes since I wrote the last update. However during that time my wife and some friends of ours have now had their first jab as part of the vaccine rollout, as the rest of us wait in line with anticipation for our turn and we hope February’s big freeze here in Blighty was the last of the sub zero temperatures until next winter.
The heavy frost here over much of February put a hold on using epoxy in the workshop for most of the month, given the minimum temperatures required for it to cure could not be met without dimming all the lights in the neighbourhood with the amount of electricity it would have required. So whilst at the end of January I had intended this month in getting the Dynel fabric embedded within the WEST SYSTEM EPOXY down on the underside of the hull, it simply would have been stupid on my part to have attempted the task under such circumstances. Colin Fletcher, Area Sales Manager for Wessex Resins and Adhesives very kindly ensured we did however remain well stocked with their products so that I can crack on with it as soon as it is warm enough to proceed:
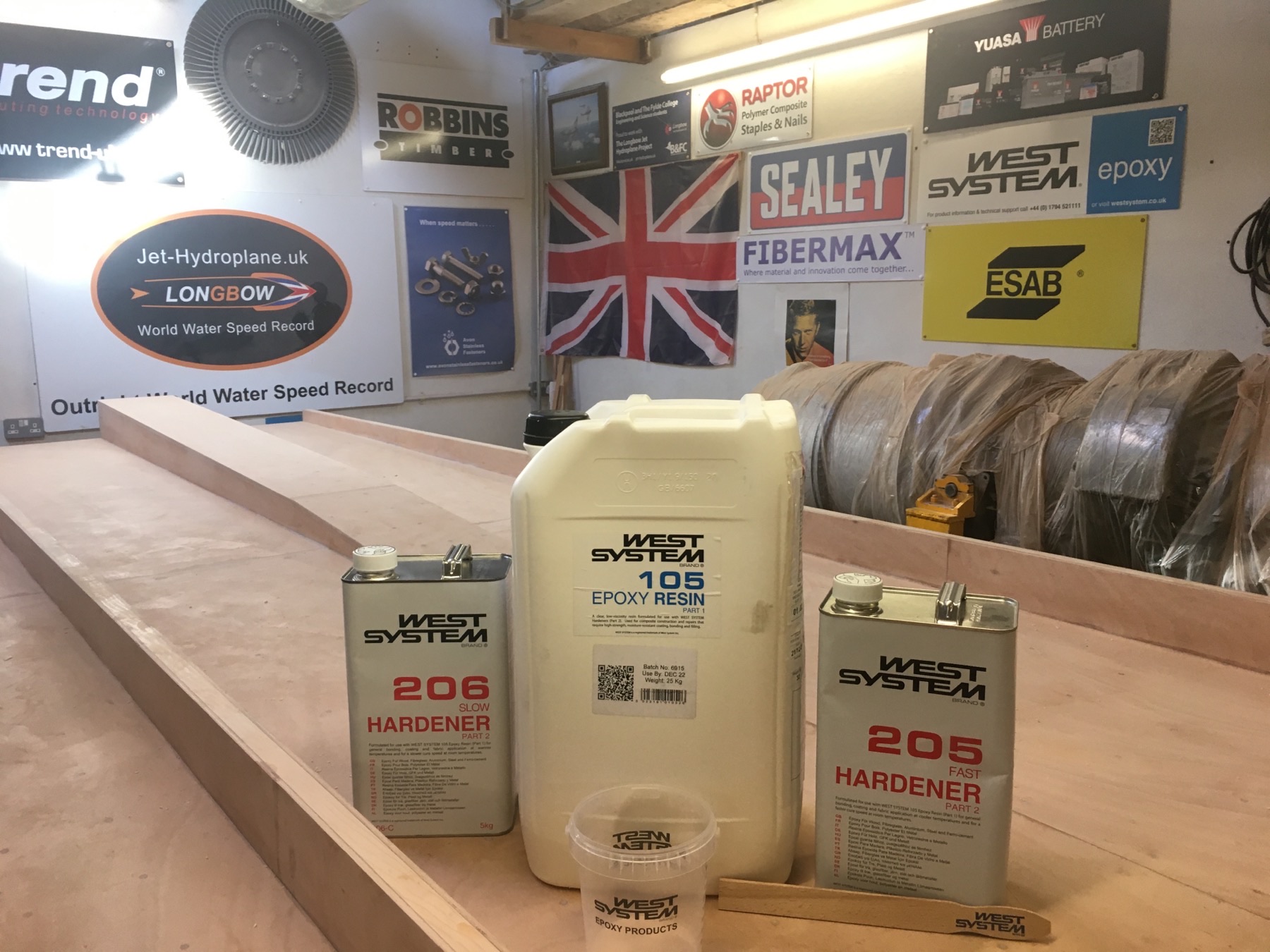
Patience is a virtue they say, so with the epoxy work on hold it was a case of waiting for the weather to pick up and in the meantime going around the upturned hull of Longbow, attending to lots of little detailing in a methodical way. Like any vehicle bodywork preparation, the more you look for imperfections, the more you will find. This being the case perhaps the cold weather halting epoxy work was something of a blessing in disguise as it allowed me to take more time sanding, picking open any air pockets in the epoxy, etc that perhaps I would otherwise have spent less time on. It is a tedious but necessary process when applied to such a large area so I won’t bore you with any more than the following photo as an illustration of what joy the winter nights have been:
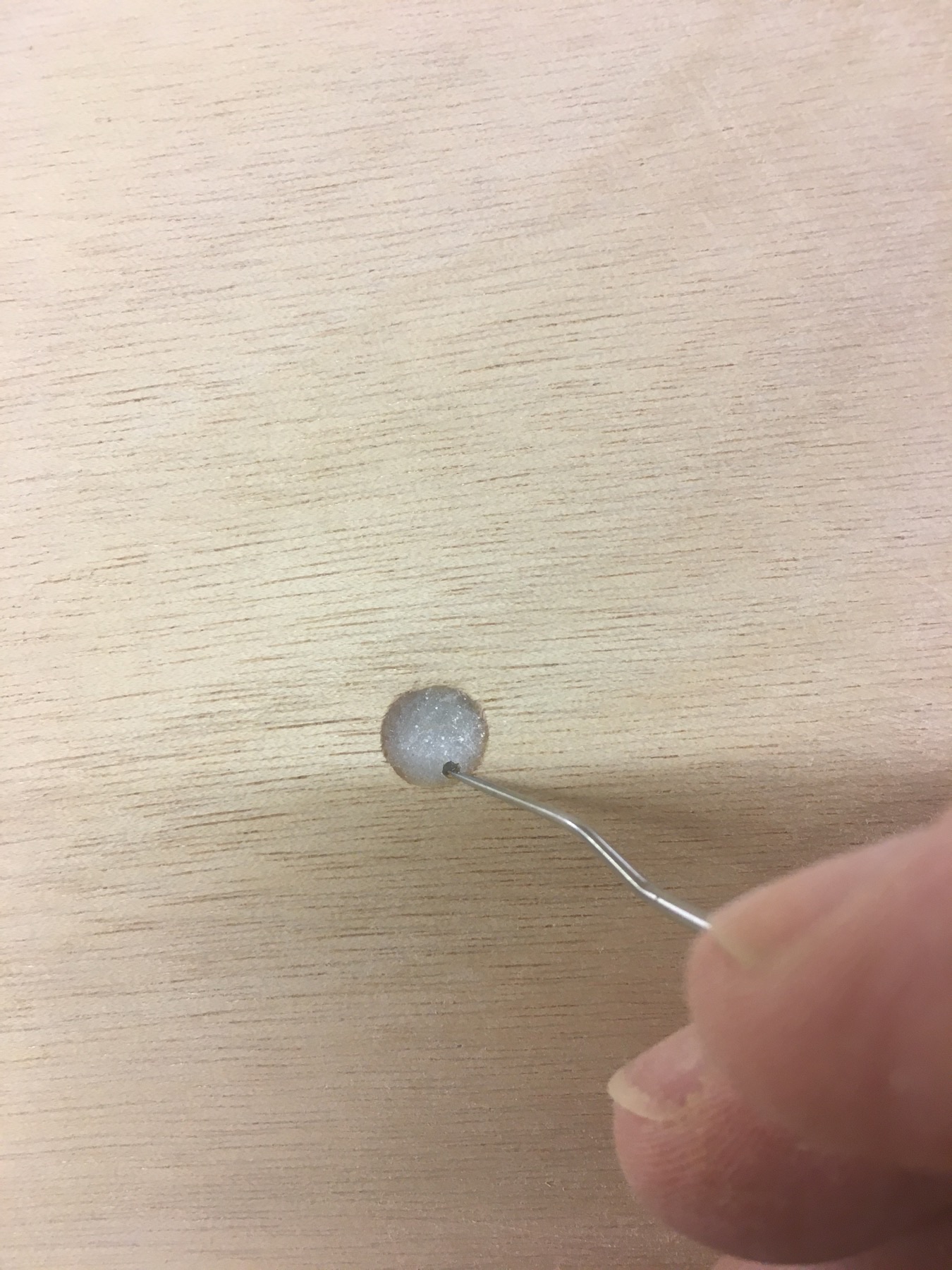
Steve Buckle of our sponsor Jack Sealey Ltd kindly ensured we had plenty of their sanding discs and additionally sent us some of their superb filler and epoxy spreading tools. Like so many people having spent a lifetime using bits of cardboard, scratch cards and whatever else I could cut up to spread filler when doing vehicle repairs, being given the correct kit to use was something of a revelation. Just a world of difference in obtaining neat results first time with minimal product waste.
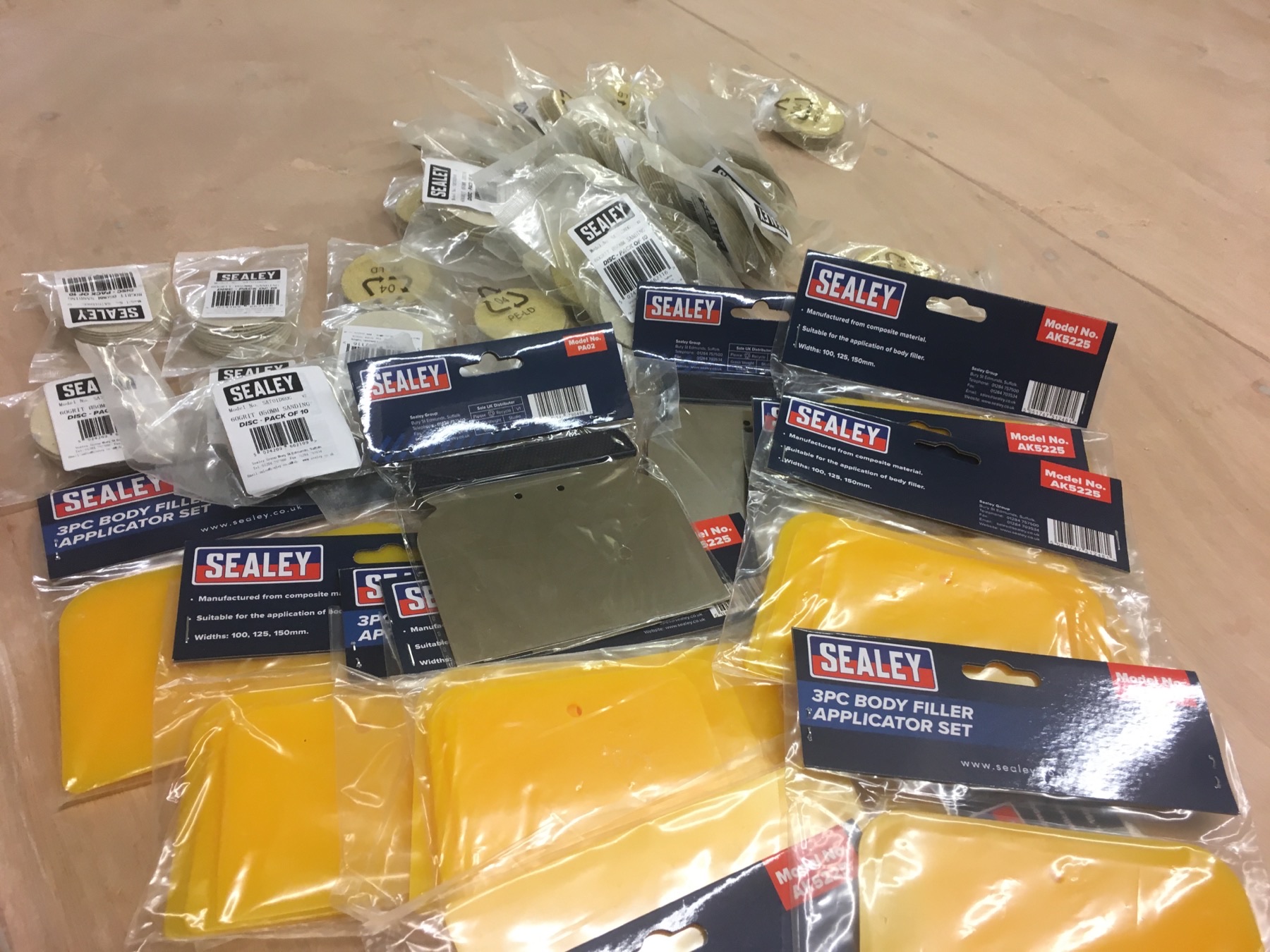
My good friend and mentor Dimitrios Apostolakis of our sponsor Fibermax Composites so very generously sent us a massive amount of their product this month by way of their own vacuum pump and everything I could wish for to start my apprenticeship in vacuum bagging and resin infusion process. At this stage I feel as though I am now the idiot ‘with all the gear and no idea’ but I am hoping Dimitrios and my good friend, composite design engineer Paul Martin will prevent me making too many stupid mistakes along the way.
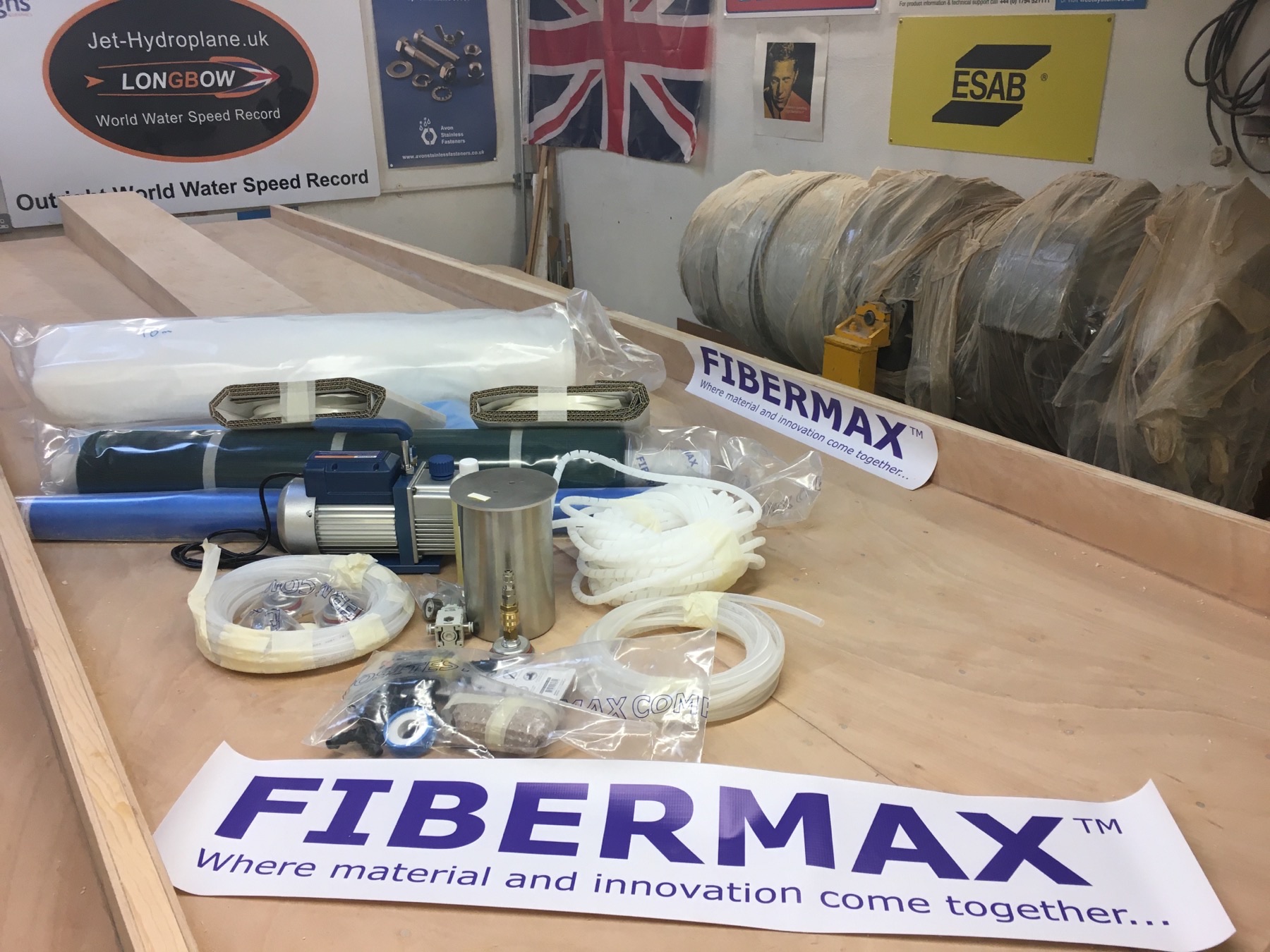
Meanwhile the apprentices at our sponsor, the WEC Group Training Academy in Darwen, have been busy completing the build of the trailer for Longbow under the guidance of their Training Manager Kris Mercer. I trust you will agree they have made a fantastic job of it and we could not be more pleased with the skill and care the apprentices have shown with the fabrication. So very well done to all involved and a special thanks also to Mark Sugden of John. W. Laycock in Keighley as sponsor for the supply of metalwork to build the trailer and Andrew Jackson along with Luke Matthews at our sponsor Peak Dynamics at Bidford on Avon, for the supply of all the trailer running gear.
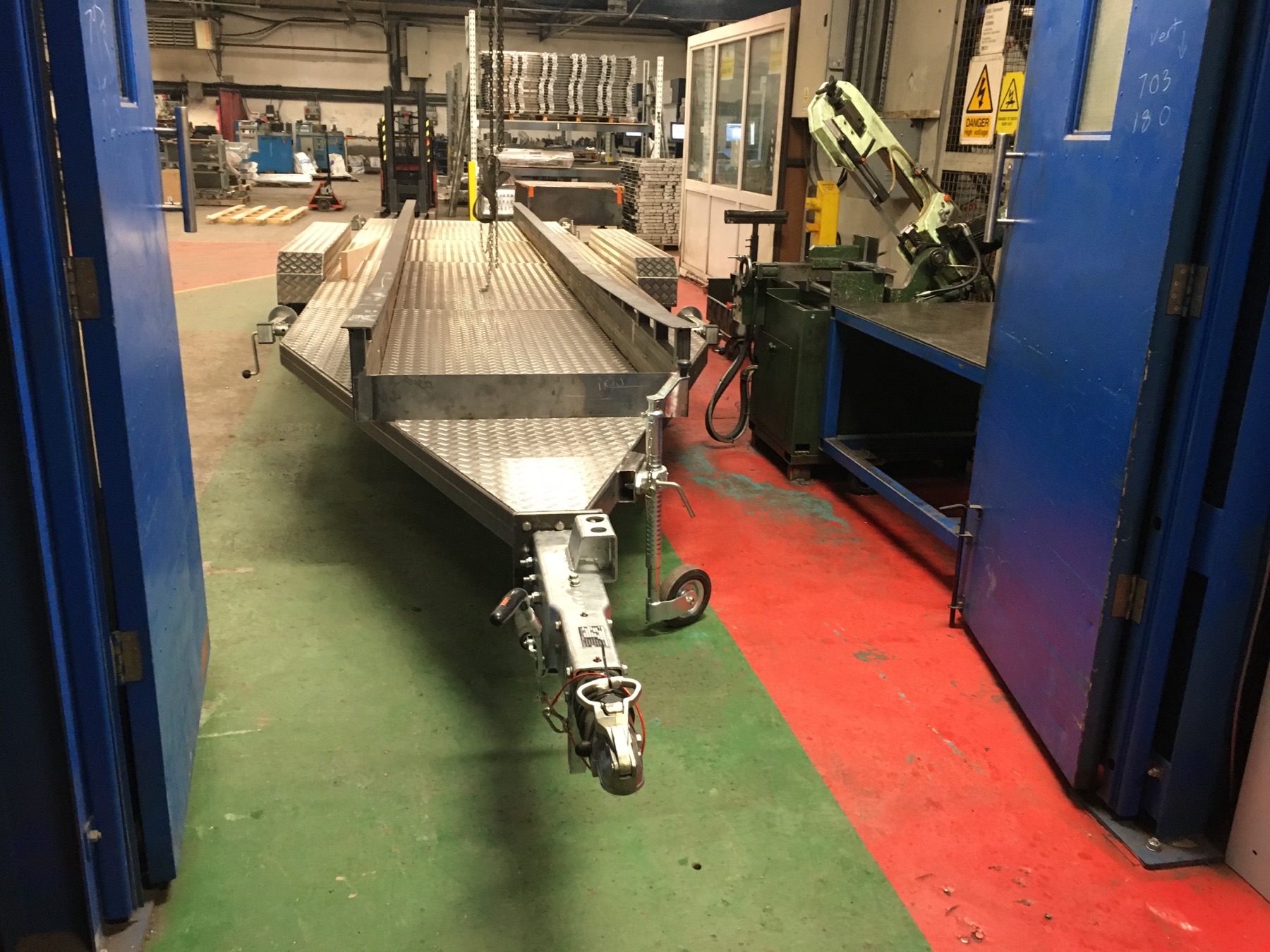
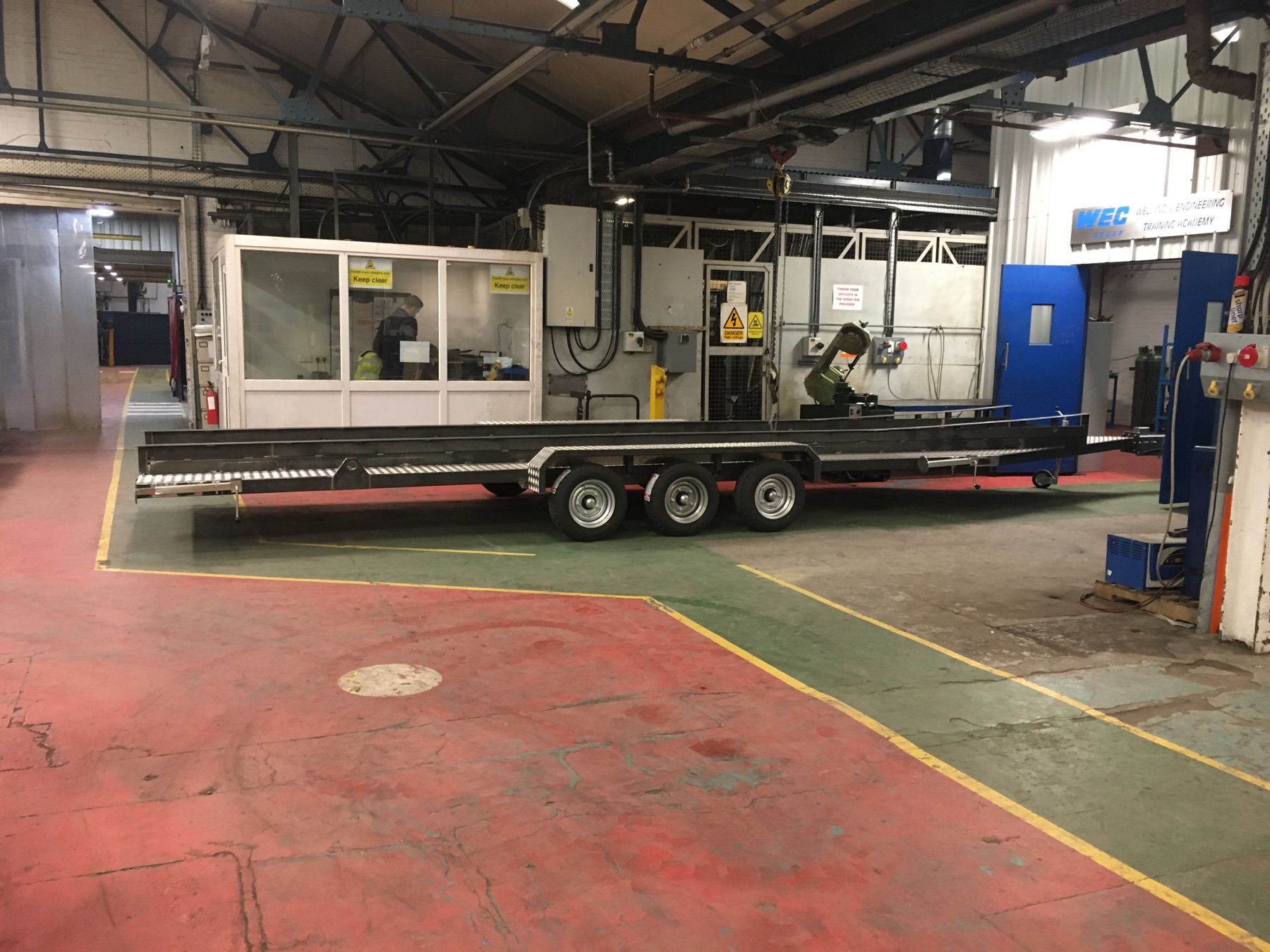
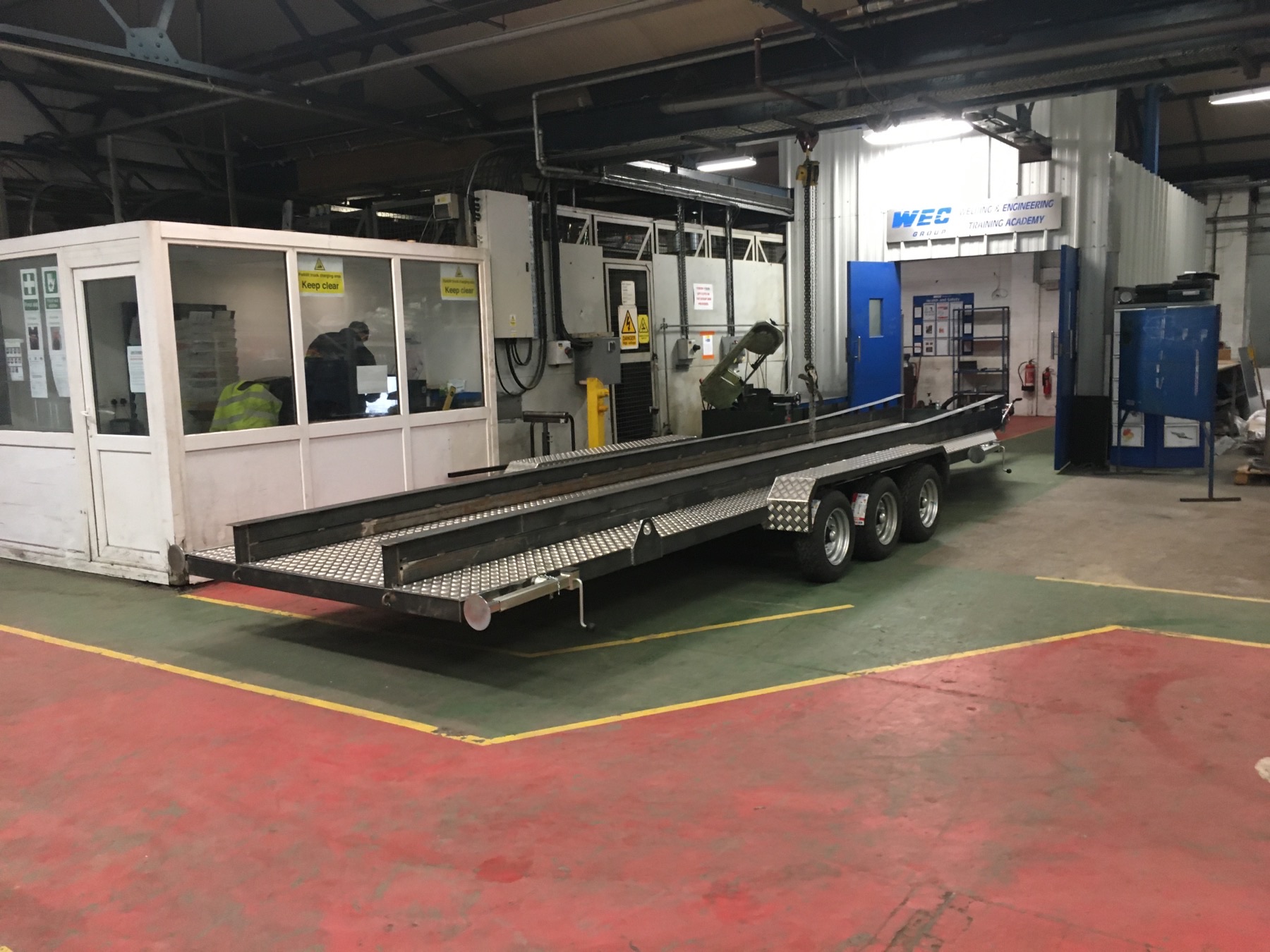
We also welcome a new sponsor to the project, ‘Right Connections’ based in Telford, who specialise in towbar wiring kits with their MD Andrew Bolton, very kindly sending us a set of detachable lights, wiring and vehicle connectors for the trailer.
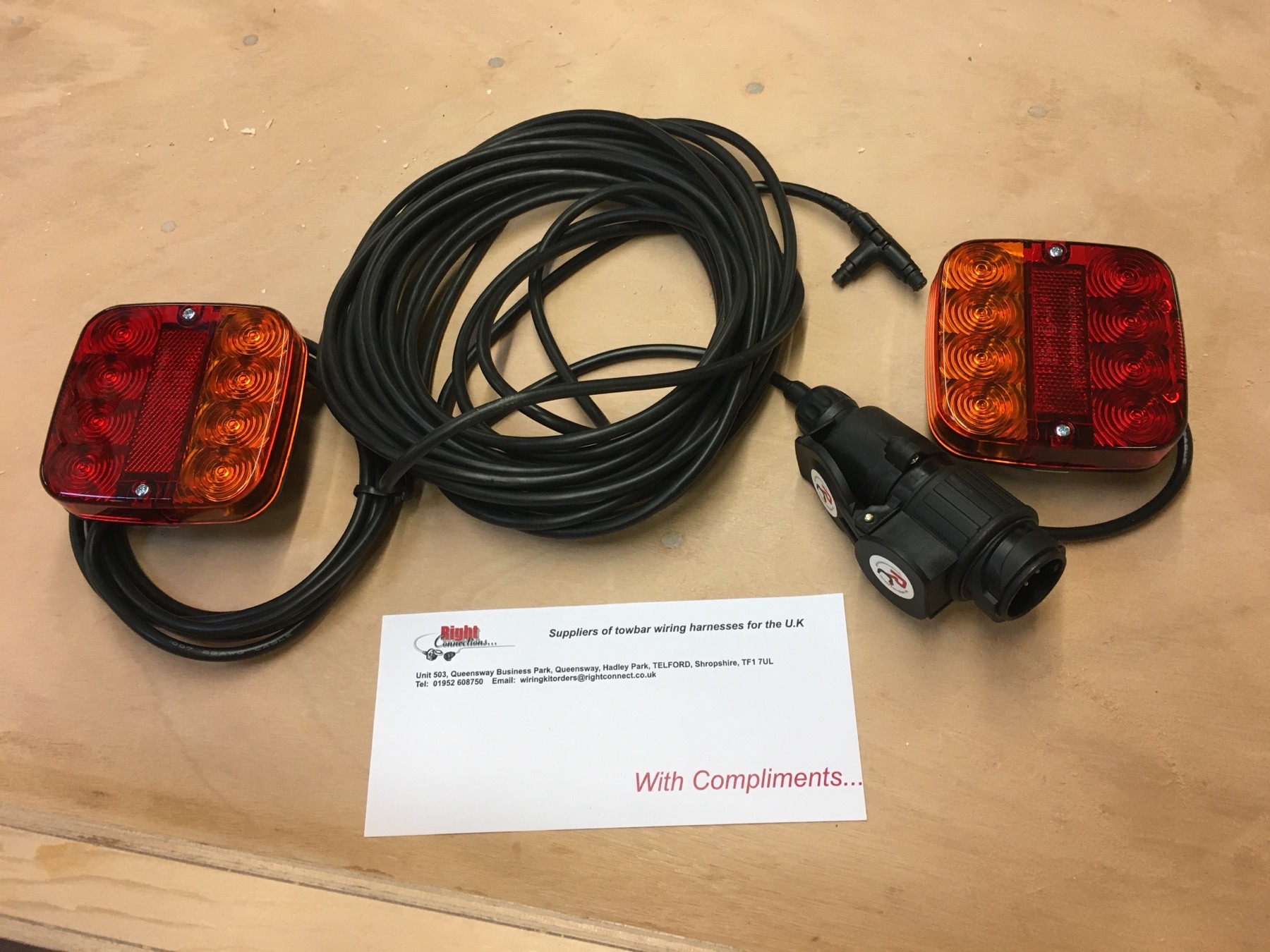
Referring back to WEC in Darwen, if you have driven through the town where they are based, then you may have noticed a beautifully impressive stainless steel Spitfire memorial and this fantastic piece of engineering was made by WEC in 2012 and upon completion, officially presented to the town on Remembrance Day in order to commemorate the local population collectively funding the building of a Spitfire during World War II to help out with the War effort.
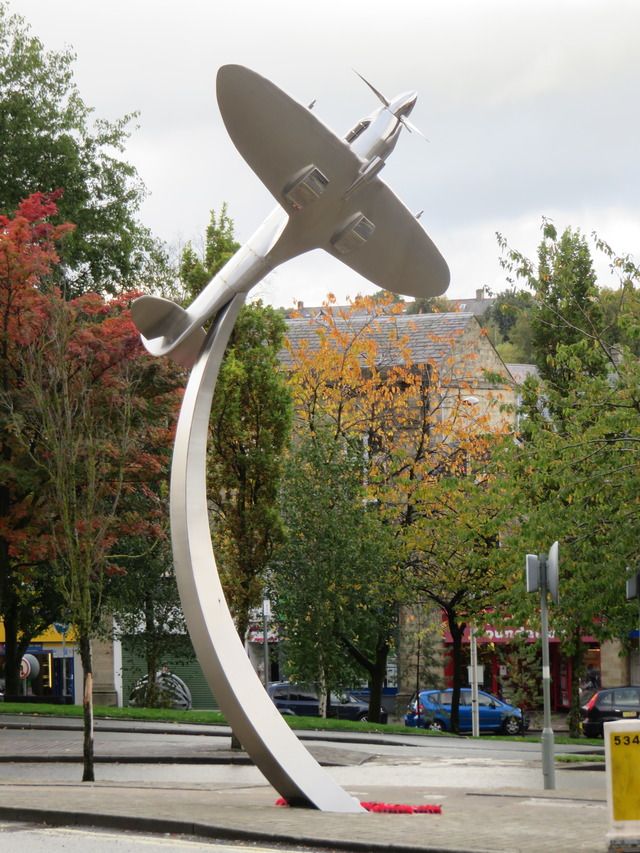
This got me thinking a little bit about the wartime military aircraft built and overhauled at Samlesbury which is only 10 miles from Darwen and how this engineering powerhouse would then go on to build Donald Campbell’s jet hydroplane Bluebird in the 1950’s. This in turn had me musing over the birth of the jet engine that also took place in this part of England that would power military aircraft throughout the world. These jet engines also powered John Cobb’s hydroplane called Crusader using a ‘centrifugal flow’ gas turbine, followed by an ‘axial flow’ gas turbine that was chosen to power Bluebird.
For those who are not too familiar with jet engines, they may wonder what I am on about when referring to centrifugal flow type engines compared to axial flow designs. As this is a website about jet hydroplanes where such craft have used both these types of engines it is perhaps worth further explanation because the differences between these two types of jet engines impacted upon the design of the craft within which they were used and indeed more widely the design of the aircraft they were originally manufactured for. This being the case and as something of a local history lesson, I hope you find the following explanation and background to these different designs of jet engine of interest.
Sir Frank Whittle, British pilot and aviation engineer is credited prior to his knighthood with inventing the turbojet engine for Britain that first ran in 1937 through the company that he had set up called Power Jets Ltd. However his engine at that stage was only a prototype and had a lot of issues to resolve if it was to run successfully in an aircraft without blowing itself and indeed the aircraft apart.
The Royal Aircraft Establishment (RAE) which in later years morphed into the Ministry of Defence (MOD) saw promise in this revolutionary engine of Whittle’s when compared to piston engines of the day but felt that Power Jets Ltd would not on its own be able to develop and produce enough reliable units. This being the case the RAE offered contracts to both Rover and Vauxhall to build and develop the design in partnership with Whittle / Power Jets. However Vauxhall declined this invitation to tender from the RAE which left Rover to accept the contract.
Once Rover were appointed by the RAE they set Frank Whittle and his company Power Jets up in a disused cotton mill that Rover owned in Barnoldswick (about 20 miles up the road from Darwen), for them to develop the engine. Unfortunately Whittle and Rover didn’t get on too well to the extent that Rover set up another jet engine factory just 13 miles away in Clitheroe, using another redundant cotton mill they owned and tried to improve Whittle’s engine without telling him.
In the meantime Whittle got in touch with Rolls Royce seeking out their knowledge on how they had made their supercharger (in effect a small turbine compressor) work so well for their Merlin piston engine that powered aircraft such as the Avro Lancaster bomber and Spitfire. The reason Whittle reached out to Rolls Royce was because the movement of air through their supercharger unit mirrored the reliability he was trying to achieve with the compressor stage of his jet engine.
With Clitheroe and Barnoldswick being so close to each other it was only a matter of time before Whittle found out that Rover were doing things at Clitheroe with his engine design without telling him. The outfall from that was a somewhat legendary meeting in 1942 bearing in mind this was in the midst of a world war, at the Swan & Royal pub / hotel at Clitheroe which you can still go for a drink and meal at once the lockdown is lifted.
At that meeting was Spencer Wilks of Rover, Frank Whittle of Power Jets, Dr Stanley Hooker of Rolls Royce and Ernest Hives also of Rolls Royce. Over a meal and a drink they all shook hands to do a deal for Rover to swap their jet engine factory at Barnoldswick plus their ‘secret’ jet engine factory they had also set up at Clitheroe, in exchange for the military tank factory Rolls Royce owned at Nottingham.
Rolls Royce shut the Clitheroe factory shortly after the handshake deal was done but they carried on producing jet engines at Barnoldswick all the way through to modern day with the site recently in the news as employees fought to prevent jet engine fan blade production being moving abroad. Out of interest you may hear Rolls Royce jet engines referred to by the letters ‘RB’ followed by numbers. For example the RB199 that powered the military combat aircraft Tornado (also built in Lancashire) and this ‘RB’ designation stands for ‘Rolls Barnoldswick’.
Anyway back to the history lesson, Whittle’s jet engine was of a ‘centrifugal flow’ compressor design. What I mean by that is air is drawn into the front of the engine by a circulating impeller which then throws that ingested air outwards and in so doing compresses the air in a similar fashion as throwing wet clothes into a spin dryer squeezes the items and water onto the sides of the drum. What should be apparent with this type of design is that the airflow entering the engine has to then change direction perpendicular to the airflow entering the engine. This is somewhat undesirable with regards to how efficient the engine compared to other designs. You may also note that the overall diameter for this type of engine has to be relatively large in comparison to the diameter of the air intake portion and the following upper sketch hopefully shows the issue.
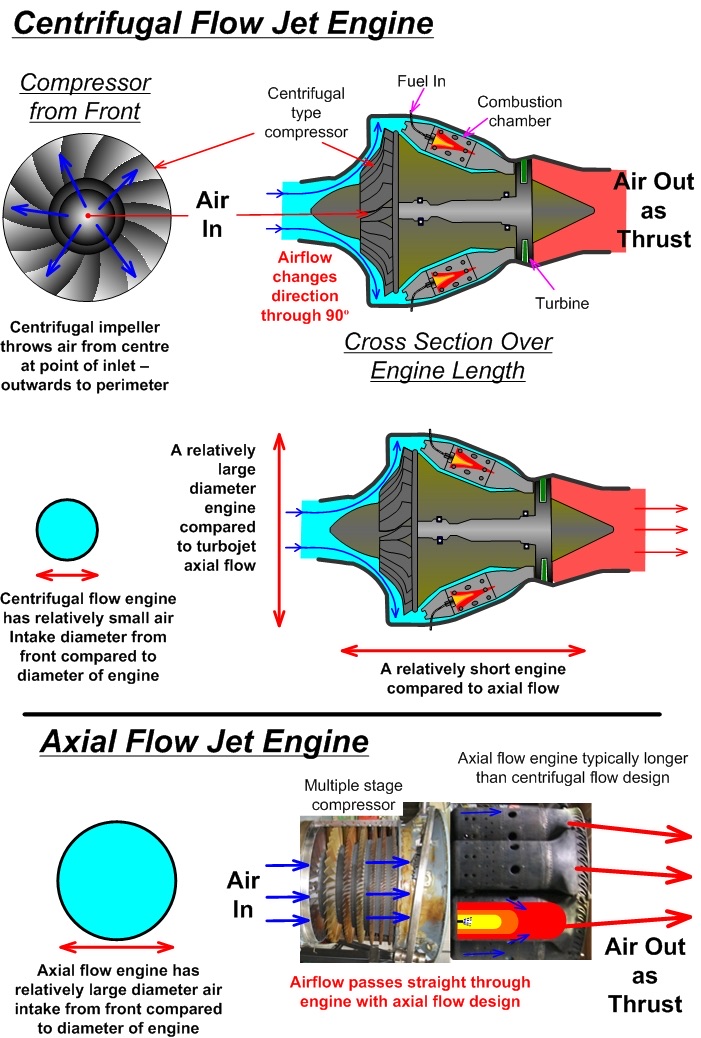
However and as the lower sketch shows the ‘centrifugal flow’ jet engine wasn’t the only game in town during this period. A different design of jet engine, one with an ‘axial flow’ compressor where air that is drawn into the engine is compressed parallel to the airflow by several rows of rotating aerofoils, interacting with static aerofoils fixed the to the compressor casing had been conceived by Alan Arnold Griffith, of the RAE as far back as 1926. For a given amount of thrust this axial flow compressor design provides greater efficiency and smaller diameter engines compared to centrifugal flow jet engines. The downside was the axial flow compressor was when compared to centrifugal flow compressor, complex and expensive to manufacture.
Whittle had actually sent his centrifugal flow design paper for a jet engine to Griffith for review in 1929 and initially the latter was sceptical of Whittle’s design ever being suitable to power an aircraft. Griffith however was later to be proved wrong about Frank’s centrifugal flow jet engine when through continued development it went on to power the first British pure thrust jet plane, an experimental proof of concept the ‘Gloster E.28/39‘ that flew at 340mph in May 1941.
After reviewing Whittle’s centrifugal flow engine concept in 1929, Griffith continued with his work on his axial flow design of jet engine. In 1937 he approached a manufacturer of steam turbines, Metropolitan Vickers (often referred to as Metrovick), who were 20 miles from Darwen at Trafford Park, Manchester, to build his axial flow jet engine for the RAE.
In 1941 Metrovick produced the first axial flow jet engine which they called the F.1 and which had a 9 stage axial flow compressor, annular combustion chamber and two stage (twin wheel) power turbine. This was tested in the bomb bay of an Avro Lancaster aircraft and proved Griffith’s thoughts that his axial flow design would be more powerful than the thrust Whittle’s centrifugal flow engines were producing at that time.
The F.1 design was rapidly modified to the F.2 and that was tested again in a Lancaster bomber but this time with the jet engine positioned where the rear gun turret would normally be and the jet engine air intake being located on top of the fuselage.
F2.2 and F2.3 versions followed to further address reliability problems. Then in something of a milestone the thrust of the engine was modified sufficient to raise the static thrust from 2700 lbs to 4000 lbs and this latest F.2/4 version which was named the ‘Beryl’ after the gem stone, then went into multiple unit production by Metrovick.
The Saunders-Roe SR.A/1 flying boat that first flew in 1947 used twin Metrovick F2./4 Beryl axial flow jet engines and the following video shows it being demonstrated even flying inverted:
In 1947 Metrovick also received an order to replace one of the three Packard petrol engines in a Motor Gun Boat MGB 2009 with one of their F.2 type engines modified so the central shaft of the engine drove a gearbox which in turn drove one of the water immersed propellers making it the first gas turbine powered boat in the world.
This new jet age in post war Britain did not go unnoticed by those seeking to challenge the Outright Water Speed Record. The high performance hydroplanes of this period were reaching the limits of water immersed propeller propulsion by way of just how fast they could spin the propeller, cavitations and preventing the propeller from disintegrating under load.
Sir Malcolm Campbell MBE in 1947 was loaned a centrifugal flow de Havilland ‘Goblin’ jet engine producing 3000 lbs of static thrust to convert his Bluebird K4 hydroplane from piston engine water immersed propeller, to pure thrust jet engine. However it only went to show that dropping a jet engine into a hull meant for a piston engine was not a route to success.
In 1951 the design for John Cobb’s Crusader purpose built jet hydroplane was being finalised with the aim to better the Outright World Water Speed Record of 178mph at that time. Their choice of pure thrust jet engine was a centrifugal flow de Havilland Ghost which was a scaled up version of the Goblin, to power the craft even though the Metrovick Beryl axial flow jet engine was in production by that time.
The Ghost engine produced around 5000 lbs of static thrust, weighed just over 2000 lbs and had an engine diameter of 53 inches whilst being 129 inches long. Such a large diameter engine dictated a large diameter hull to carry it and correspondingly the thrust line of the engine being large in diameter was relatively high in relation to the surface of the water when the craft was hydroplaning at speed. The following photos show just how large the Ghost centrifugal flow jet engine was compared to an Orpheus axial flow engine yet both engines delivered similar amounts of thrust:
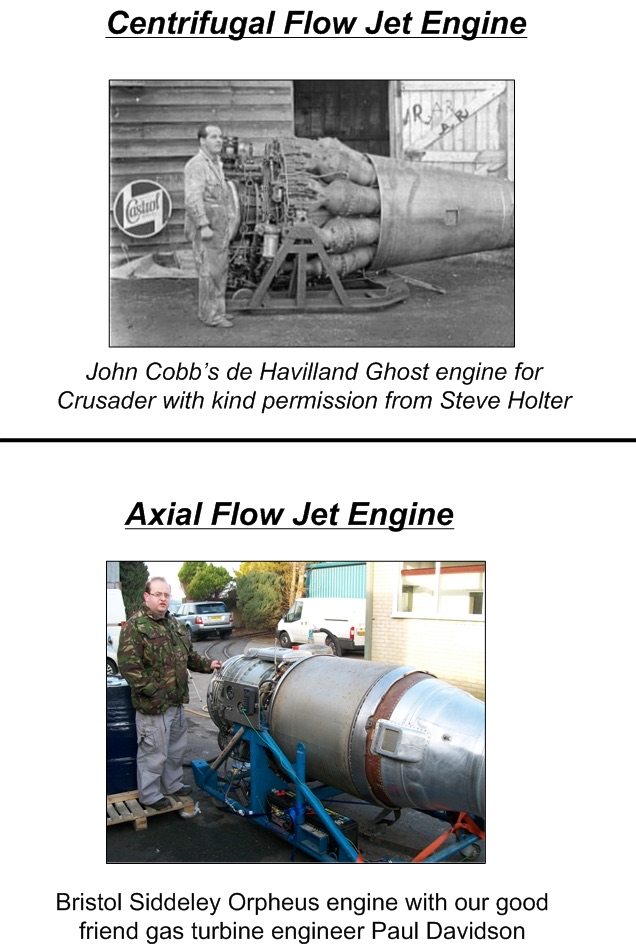
Unfortunately Cobb was to be tragically killed the following year whilst driving Crusader when the craft came to grief for a number of reasons on Loch Ness.
During 1953 Bluebird’s designers opted for the Metrovick F.2/4 Beryl axial flow jet engine to power the craft. This engine with its thrust of 4000 lbs, weight of 1750 lbs and diameter of only 36 inches allowed the jet engine to be located much lower in the hull compared to the centrifugal flow Ghost engine in Crusader. This in turn brought the thrust line of Bluebird considerably closer to the surface of the water than Crusader and in so doing enhanced the stability of the craft. The photos below show the difference between models of Crusader and Bluebird with both craft at the same scale illustrating how much wider crusader had to be to accommodate the Ghost centrifugal compressor flow engine compared to the axial flow Beryl jet engine, in addition to showing the rear of each craft again illustrating the height of the jet pipe from the water (carpet for the model) in each case:
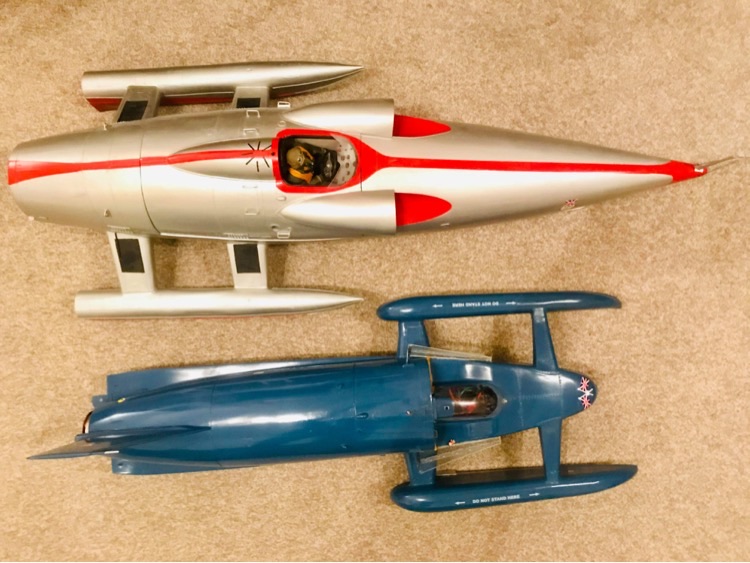
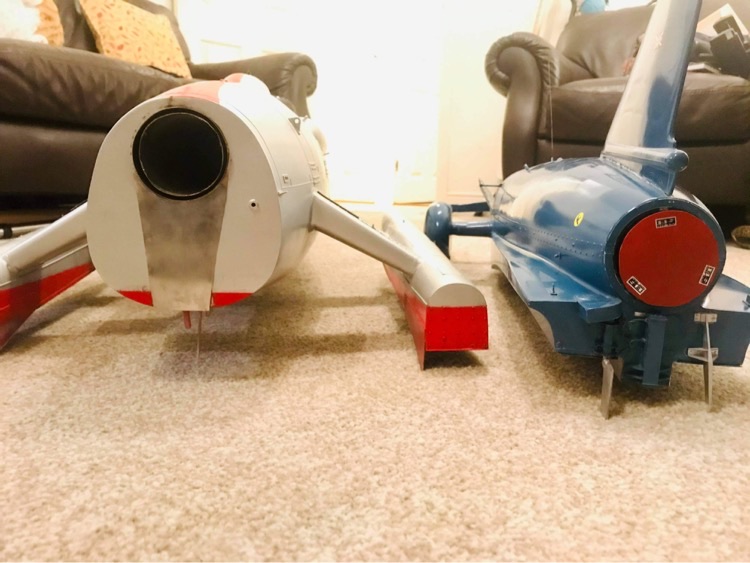
With kind permission of Rich Marsh
Bluebird went on to win seven Outright World Water Speed Records with a highest recorded one way pass using the Beryl axial flow engine of 286mph in 1956.
So we have the birth of jet engines, the birth of Bluebird and the birth of the engine that powered Bluebird to all her records, all within 40 miles of the factory that has just made the trailer and is building other parts for our jet hydroplane Longbow. Call me sentimental or just mental but for me personally I think all of that local heritage has a very nice feel to it and ties in very nicely with Longbow.
In 1966 Bluebird had her trusty Beryl jet engine that she had won all her records with replaced on Donald Campbell’s instruction with a more modern for the time but still axial flow, Mk 701 Bristol Siddely Orpheus jet engine from the Folland Gnat aircraft, producing only around 500 lbs more thrust than the Beryl but weighing several hundred pounds less.
That conversion from Beryl to Orpheus jet engine to try and push Bluebird beyond 300mph was in my view a complete disaster from start to finish irrespective of it ending with Campbell being killed.
Perhaps I am somewhat biased given my late mother’s name was Beryl but for me personally Bluebird was designed around the Metrovick axial flow F.2/4 Beryl turbojet, that is the engine she won all her records with, Campbell and his team had all the happy times and success with and in my humble opinion was of a format that she looked and ran her best with.
It is perhaps in conclusion worth noting that despite Campbell swapping out the 4000 lb thrust Beryl for a more powerful engine to chase 300mph, Ken Warby MBE and his jet hydroplane Spirit of Australia a few years after Campbell was killed, broke the 300mph barrier by a considerable margin. He did so using a Westinghouse J34 axial flow turbojet producing only 3,400 lbs of static thrust, which was well below the thrust from Campbell’s Beryl jet engine, the later installed Orpheus and Cobb’s Ghost engine.
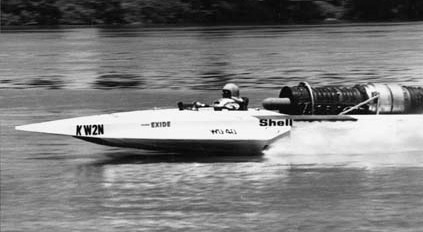
If anything is therefore to be learnt it is that stability and design of the jet hydroplane are far more important than the need for the most powerful engine you can get hold of, if you wanted to chase this ultimate record and live to tell the tale.
Well on that sobering note, that is all for this month folks and thank you for dropping by to read the update. Please tell your family and friends about our little venture and if I have not bored you too much, do call in next month for another catch up. In the meantime stay safe and if you have not done so already a like on our Facebook page will help you keep tabs on the project.