Yes here it is at last, our first diary update for 2020 having skipped doing one for January whilst we had an extended break as a result of waiting upon material arriving to continue with the build of our jet hydroplane Longbow. Thank you to those who wrote in asking when our next update would be and hence it was nice to know that the Project has built up quite a following over the last year with the updates apparently being well received both here within the UK and abroad.
For those that may think goodness why did we not plan so as to not run out of material you have to remember that Longbow’s hull is primarily being constructed out of wood. That being the case as we approached the Christmas holidays we knew our families quite rightly would be wanting our time over that period so we would be banned from working on the boat and also our sponsor Robbins Timber would be closing for the same period.
As the next task of the build required ordering some long lengths of machined timber, then had we put the order in with Robbins Timber prior to the holidays there was a good chance that timber would have begun to twist or warp during the seasonal break, even if appropriately stacked which would (as opposed to wood) render it useless. Accordingly our view was that it just wasn’t worth the risk. Picking things up in the New Year, Robbins Timber very kindly sent us some superb quality machined stock towards the end of January for the next phase of the build, which was to form the side skirts / fences for the air trap beneath the hull.
What do we mean by air trap? As my good friend renowned aeronautical engineer and former H1 Unlimited Hydroplane Chief Engineer Doug Ford explained “it was learnt that a very large amount of lift can be generated on the lower surface of a ramp with side skirts, oriented at some angle of attack and placed very close to a surface, for example either land or water. This effect, which is known as “ram effect”, “ram wing”, or “surface effect” generates its lift on the lower surface rather than the upper surface like a conventional airplane wing. Further, it generates much more lift than the increase due to what is known as “ground effect” which can increase the effectiveness of the wings on aircraft when close to the ground”.
So in our case the side skirts or fences to form the air trap beneath the hull of Longbow are made of long lengths of laminated timber running on the bottom of the hull, commencing towards the bow and tapering off towards the transom. Due to the size of the hull we cannot form the fences for the air trap in one length of timber so the first job was to scarf joint the lengths of stock machined rectangular timber together, that would then form the core of these air trap fences. This was done using a finger joint router cutter from our sponsor Trend Machinery and Cutting Tools as shown in the photos below:
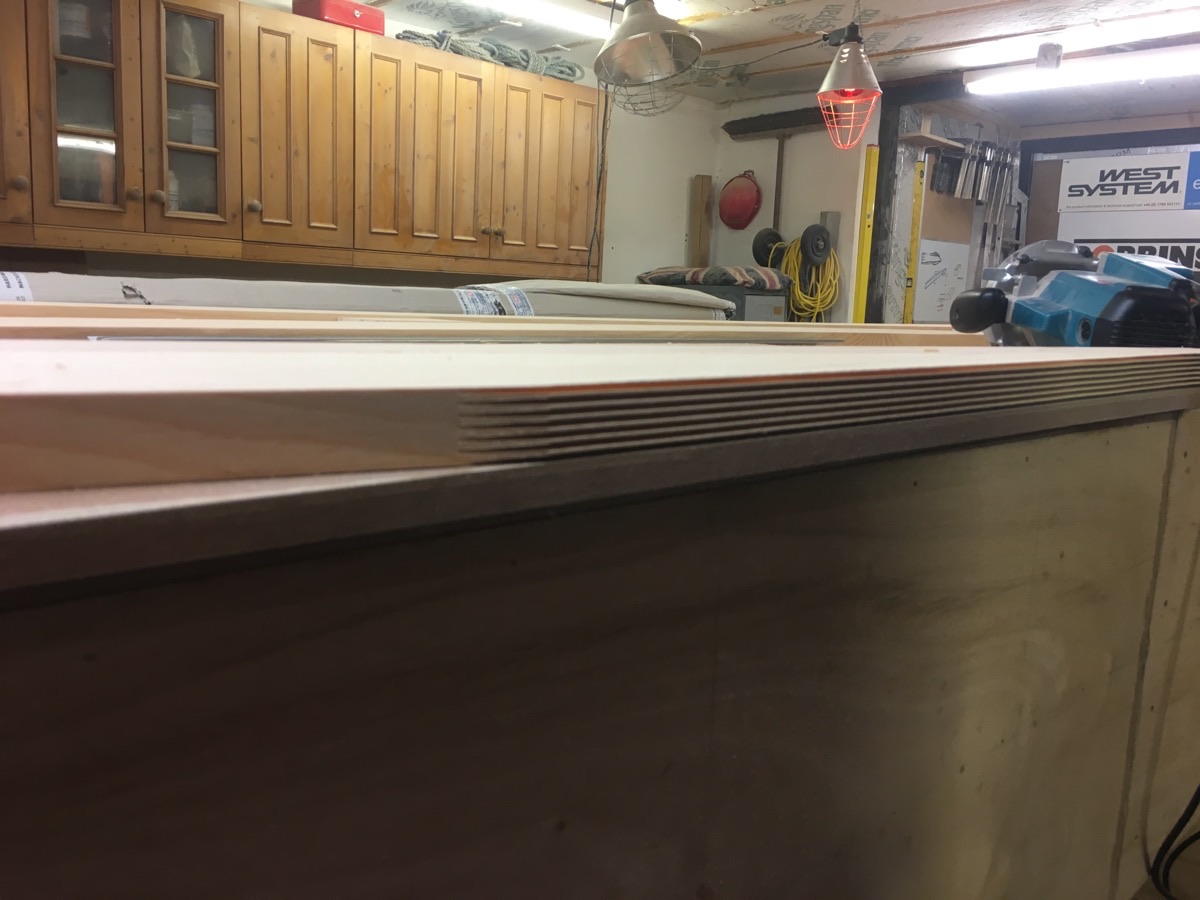
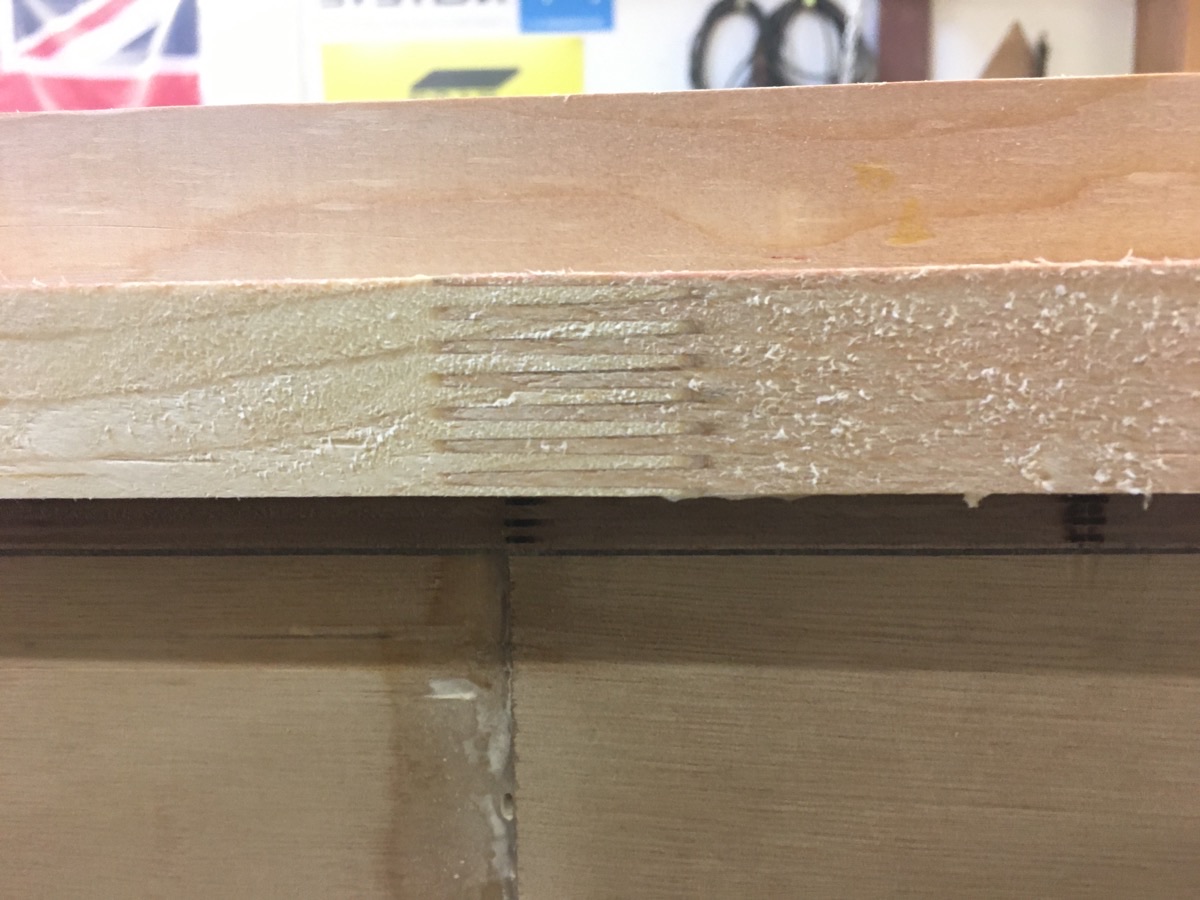
Once we were satisfied with the interlocking finger scarf joints they were permanently fused together using West System Epoxy from our sponsor Wessex Resins. Now we had the right lengths of timber to form the fences of the air trap, the next job on the list was to transfer from the drawings of Longbow onto a template made from sections of plywood screwed together in order to follow the contour of the underside of the hull and also to form the correct profile of the fences themselves.
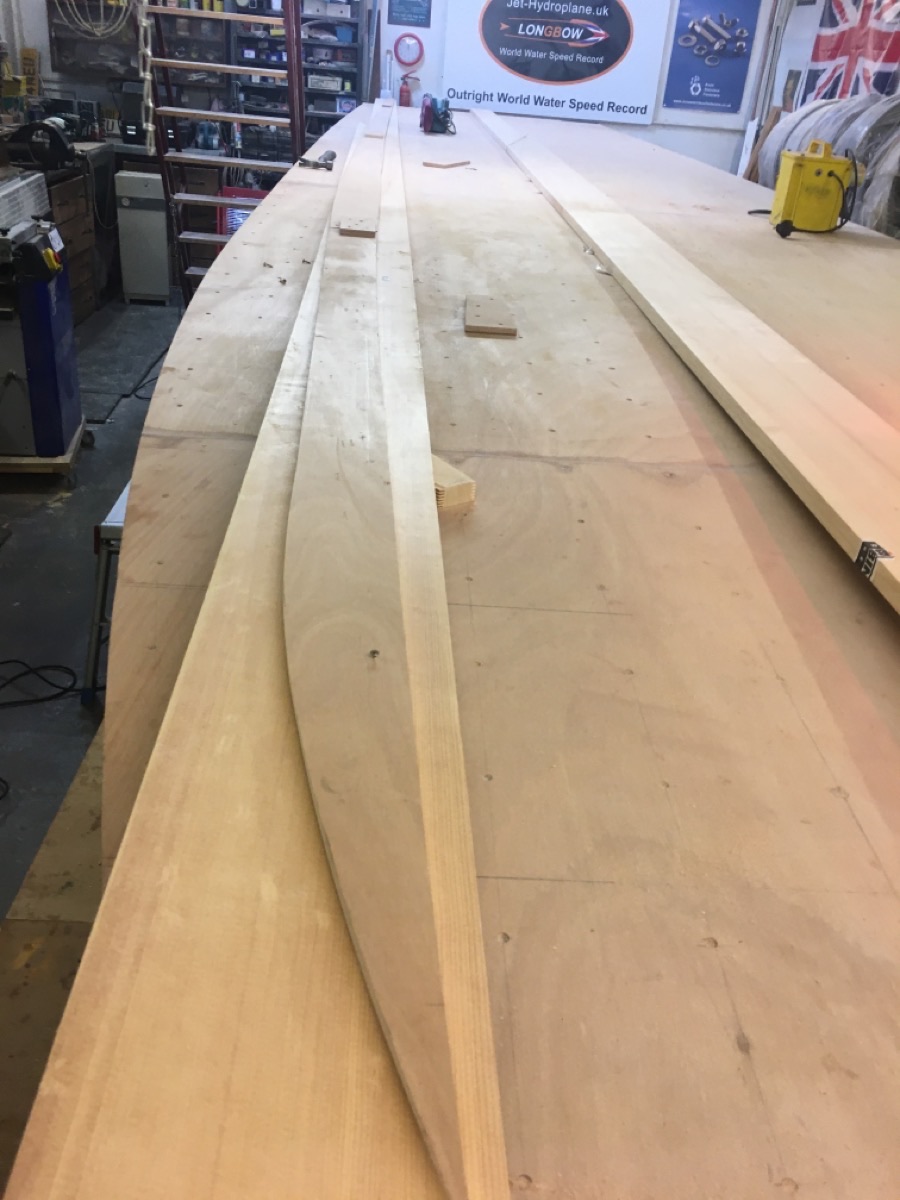
Once that was done we could then transfer the pattern onto the core scarf jointed timber lengths and cut them to shape. From the photos it may appear that the depth of the timber is not that great but it actually required a stock width of over 200mm to form the necessary shape due to the upward curvature of the hull towards the bow. Or just to confuse you the downward shape of the bow with the hull currently inverted.
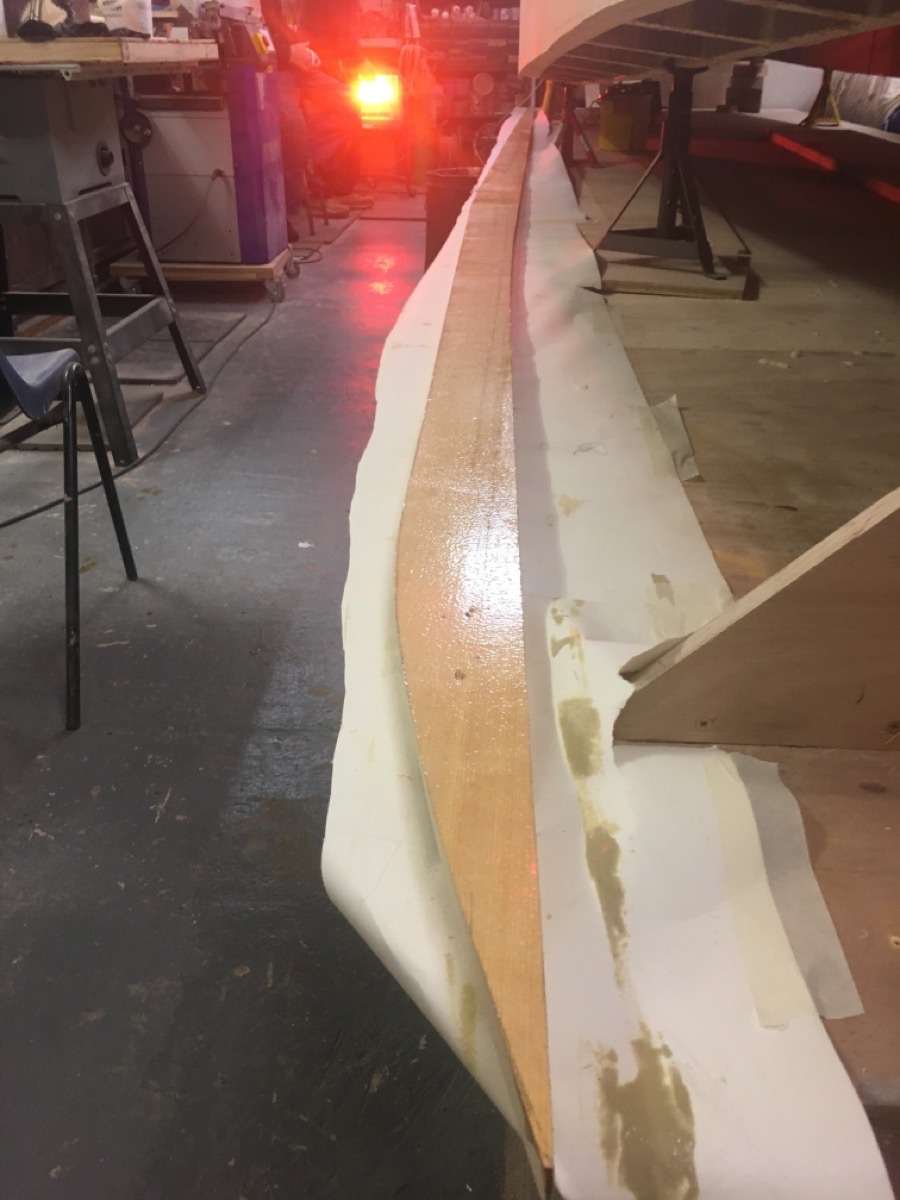
Having got the core shape and lengths correct ensuring that both left and right (or port and starboard if you are being nautical) fences to the air trap were perfectly matched, the next task was to stabilise them by lamination in order to resist any warping / twisting etc of the core timber in service. This being achieved using strips of marine grade plywood provided by Robbins Timber and again using the West System Epoxy. To hold that sandwich together whilst the epoxy cured we used Raptor composite nails in addition to weights and clamps as necessary which can be seen in the following photos:
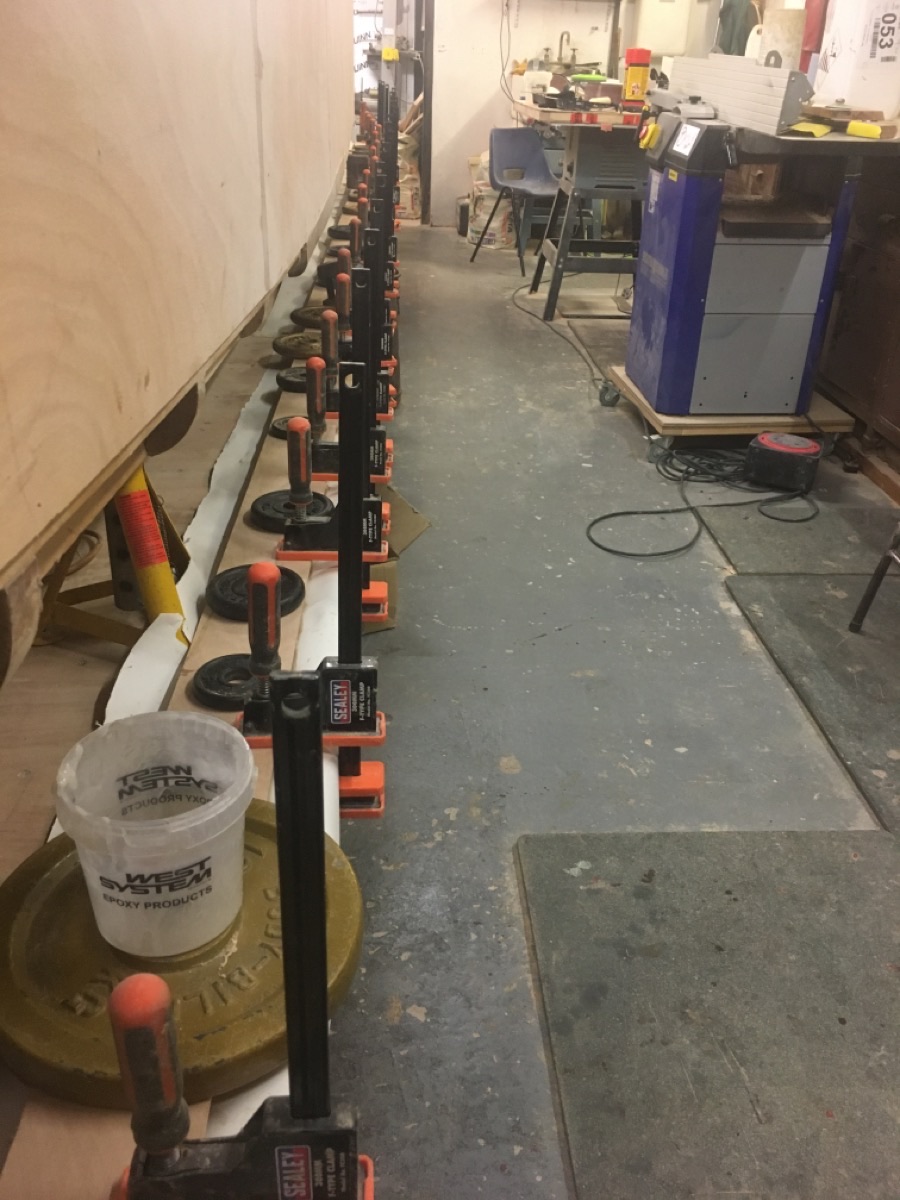
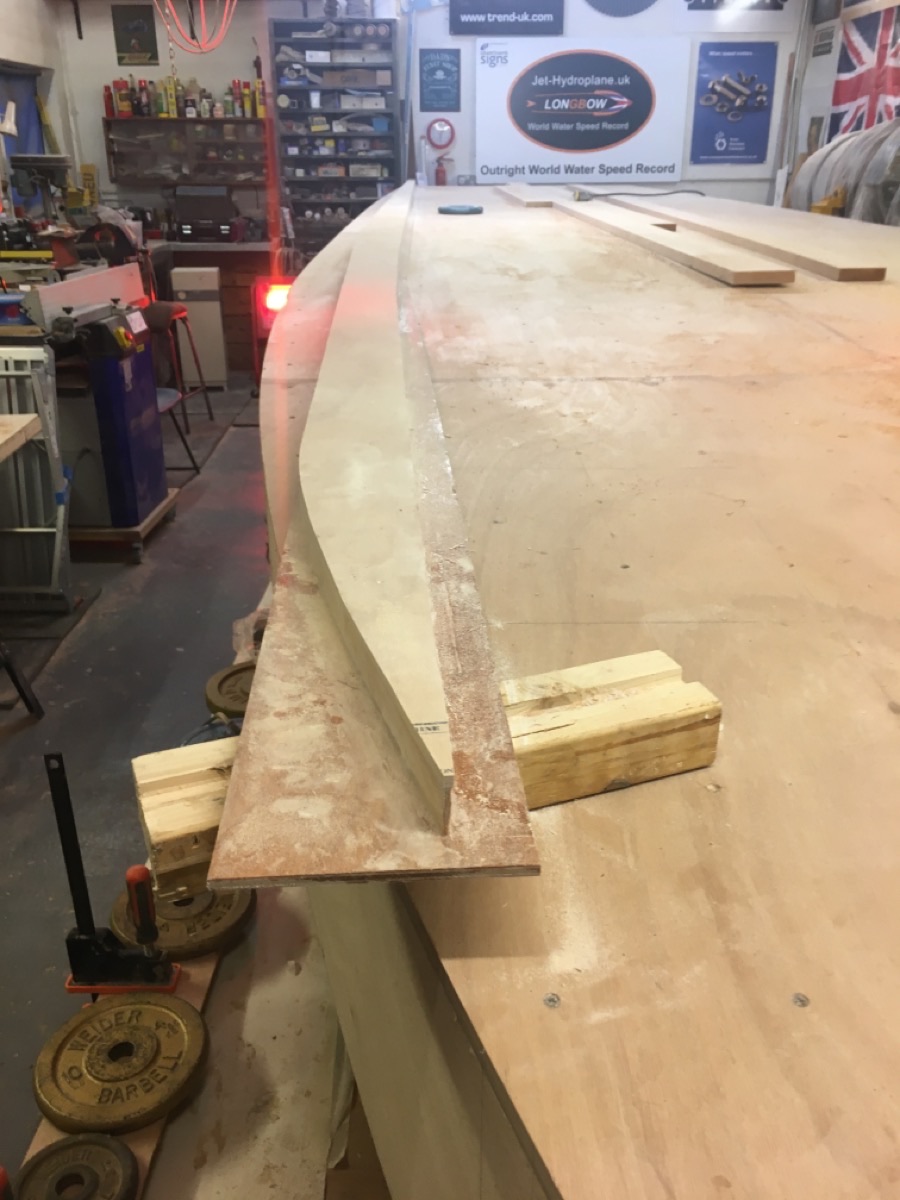
Once the epoxy was cured the plywood laminations were then trimmed to the same profile as the core timber using a Trend guided trimmer bit:
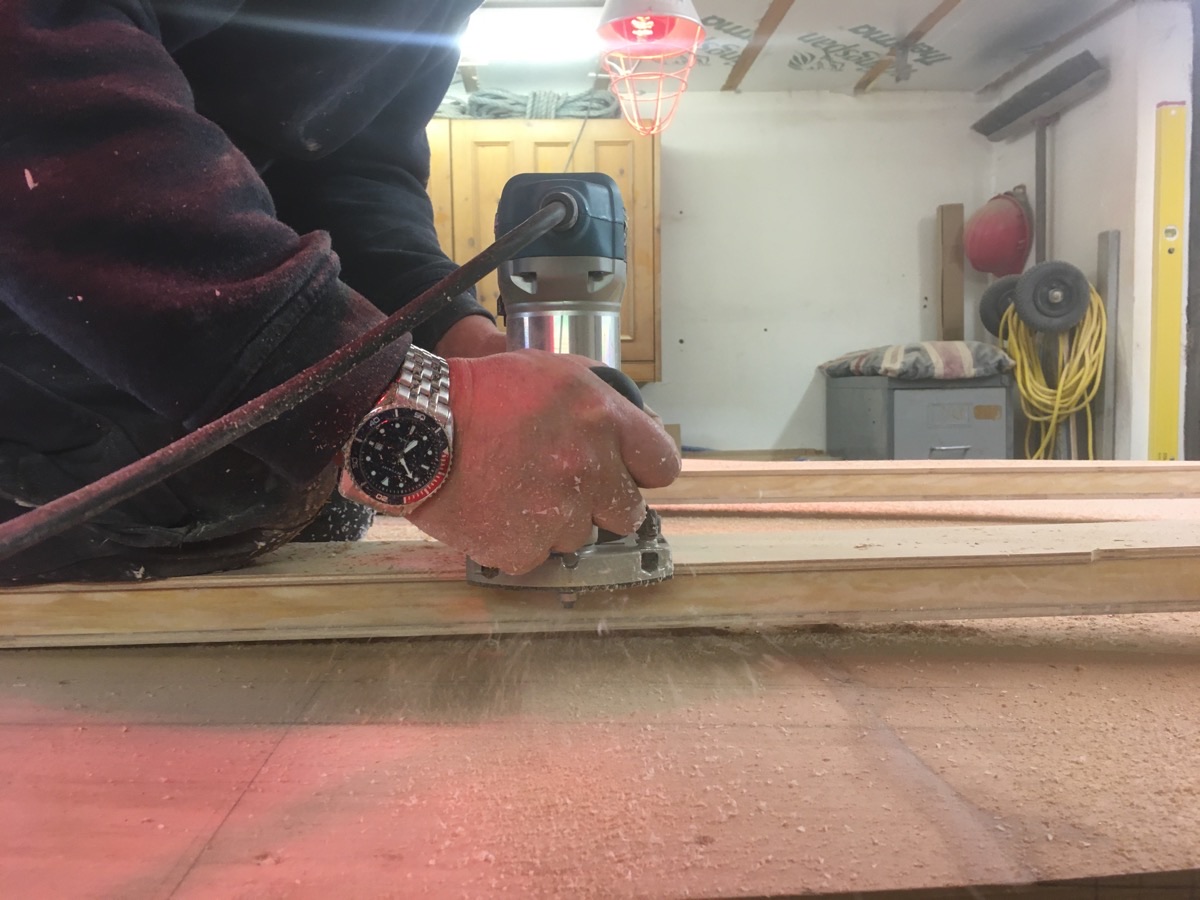
After a final sanding and check to ensure both left and right air trap fences were still matched we then attached the fences vertically into place on the bottom of the hull using a combination of stainless steel screws from our sponsor Avon Stainless Fasteners and again West System Epoxy from Wessex Resins. A little tool that we cannot recommend highly enough for getting screws into awkward places is this angle driver from Trend which they very kindly sent us to relieve a lot of swearing and scraped knuckles:
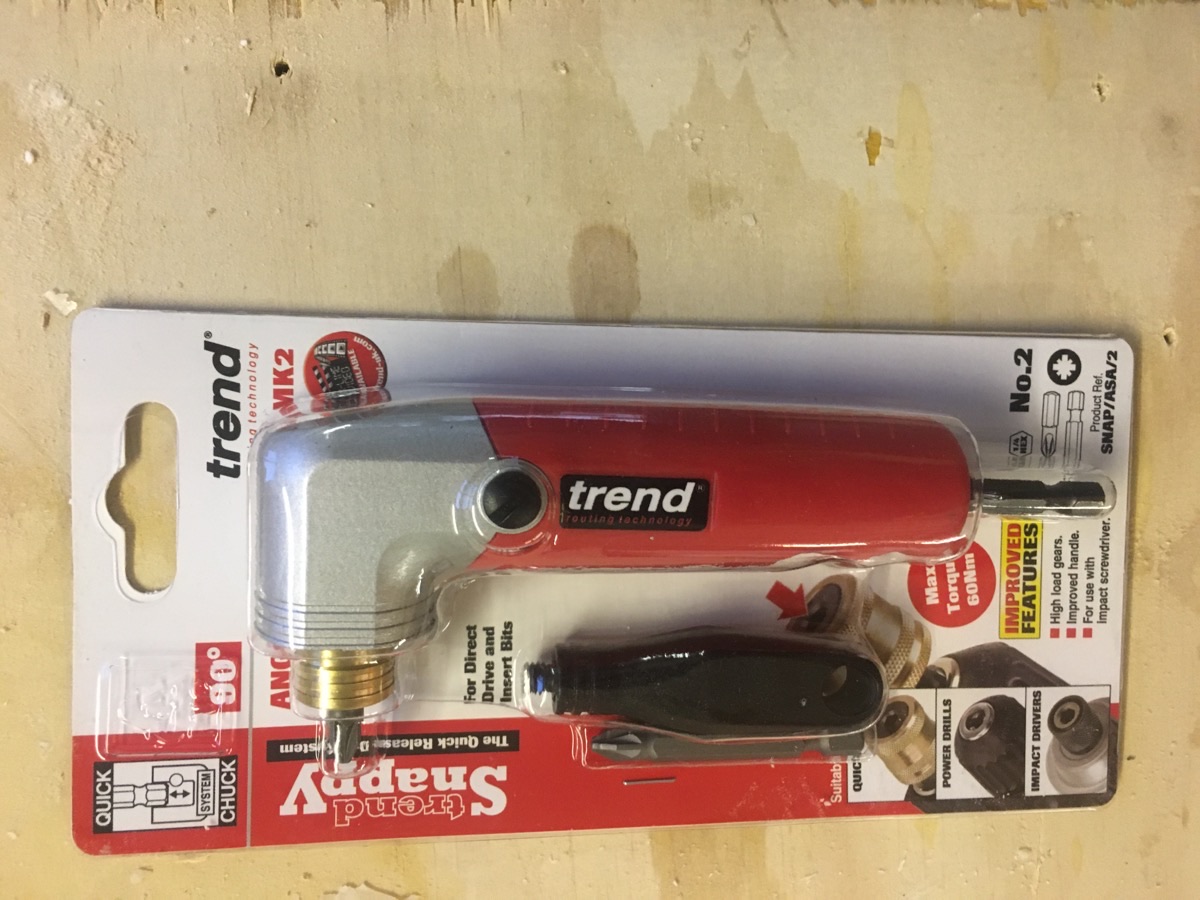
With everything in place and the epoxy cured we then gave the air trap fences a light sanding down to remove handling marks and it was great to see them completed and forming an integral part of the hull:
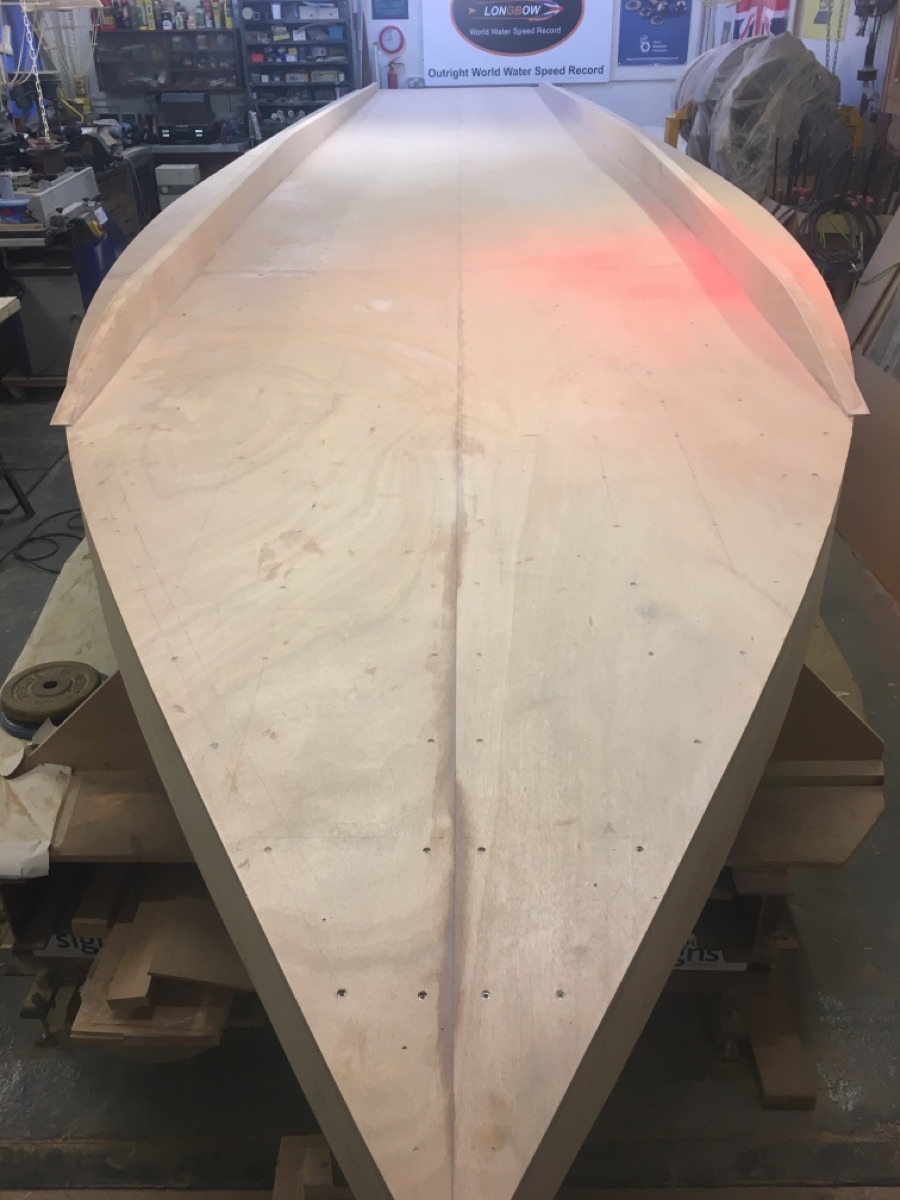
It is always nice to have the sponsors come and visit the Project to see how we are getting along, make them a brew and show where their products are being used in the building of Longbow. As such it was great to have Colin Fletcher of Wessex Resins drop by on his way home to Scotland from a show in the Midlands and bring us some new West System Epoxy pumps to ensure the resin and hardener are combined in the appropriate ratios.
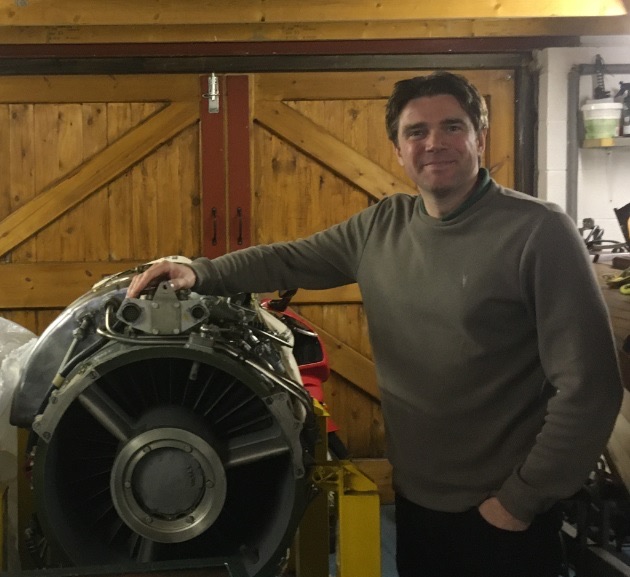
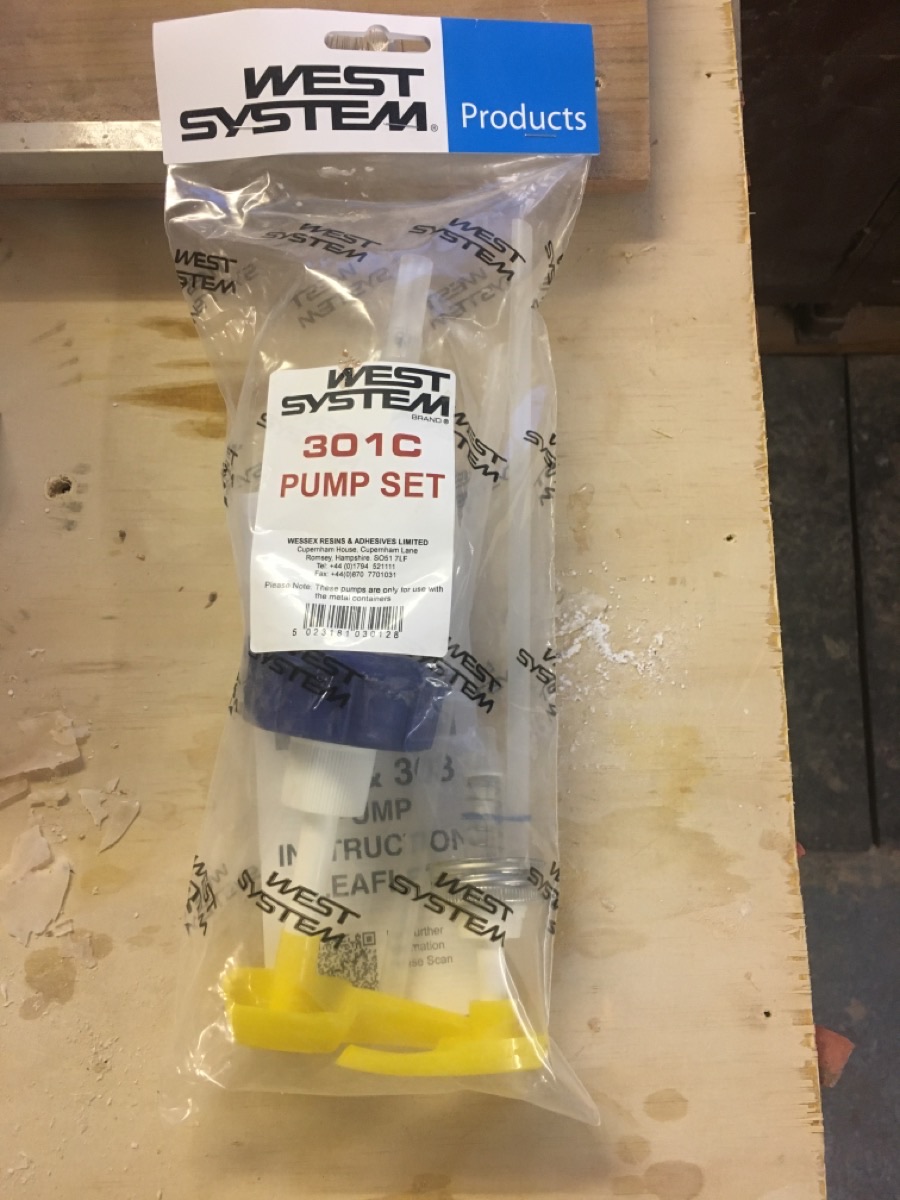
This month we also met up again with model boat enthusiast Rich Marsh who had acquired a partially constructed model of John Cobb’s Crusader jet hydroplane from expert model maker Ernie Lazenby. Rich told us that this lovely model was originally commenced by a third party as balsa wood planked hull to which Ernie added carbon fibre and epoxy to strengthen the hull in addition to revising the low speed steering by including a secondary rudder to the transom (not present on the full sized craft) which lifts clear of the water when the model is running at speed. I had the good fortune to meet Ernie at Pier Cottage, Coniston many years ago and see some of his other working models of Outright World Water Speed Record craft including Slo-Mo-Shun IV, the Bluebird boats (both propeller and jet powered), in addition to Spirit of Australia.
The following photo show Rich’s models of Bluebird K7 and the partially complete Crusader both at the same 1/8th scale (which illustrates a number of points, not least of which is how much larger Crusader was than Bluebird K7).
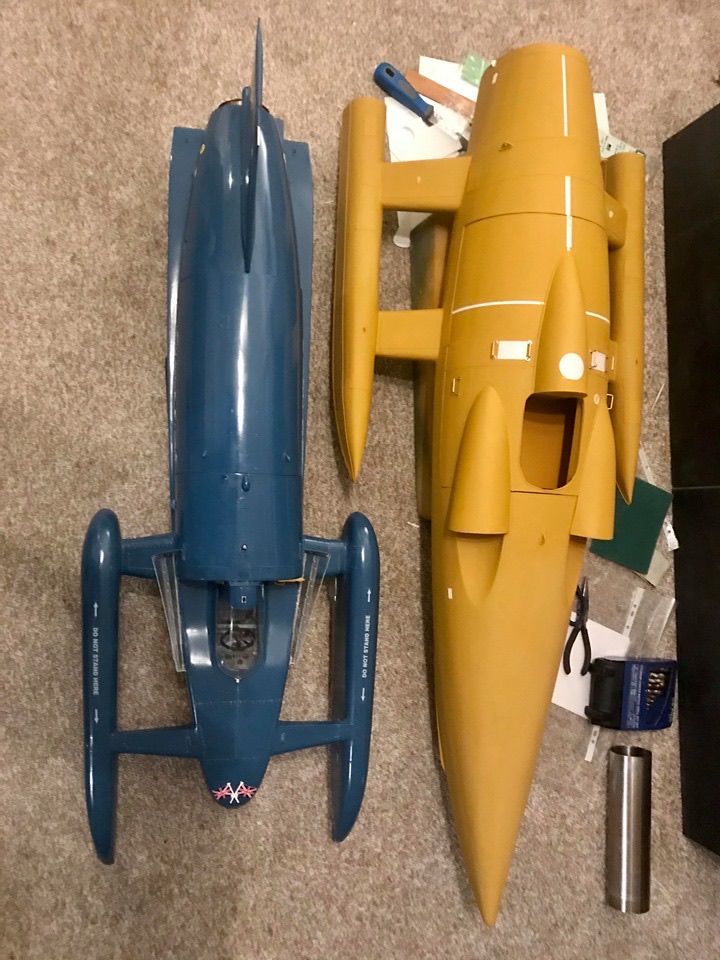
A link to a recent YouTube video of Rich running the model of Crusader at a model boating pool in Southport is given below although as you may see the boat was struggling to perform and steer with the wind on that particular day.
The model itself is currently driven by a Leopard 2000KV brushless motor connected to a 3 blade propeller rather than mirroring the pure thrust jet the full sized Crusader was built with. Rich is considering converting the model to run a gas turbine and if he does we will report back on the results.
The rudder for Crusader on the full sized boat was located at the rear of the front planing shoe whereas upon Bluebird K7 the rudder was located at the transom. Discussion upon the location of the rudder to Crusader can be found in the books ‘The Last Crusader’ by Barry Stobart-Hook and the soon to be released ‘Quiet Giants’ by Steve Holter.
Crusader was the first purpose built pure thrust jet hydroplane (the earlier Blue bird K4 having been converted from propeller to pure thrust) and was constructed in 1952 using a large diameter centrifugal compressor Ghost turbojet manufactured by de Havilland, developing 5000 lbs of static thrust for the de Havilland Venom and Comet aircraft. Following the destruction of Crusader where John Cobb was killed on Loch Ness whilst driving it, Bluebird K7 was then built in 1955, designed for the much smaller diameter axial flow compressor of the F.2/4 Beryl turbojet manufactured by Metropolitan-Vickers developing 4000 lbs of static thrust, primarily for the Saunders Roe SR.A1 flying boat.
Of note as the Ghost engine was a much larger diameter than the Beryl, the line of thrust for Crusader was consequentially significantly higher from the waterline than Bluebird K7 when the craft was running at speed which was an undesirable feature with regards to stability.
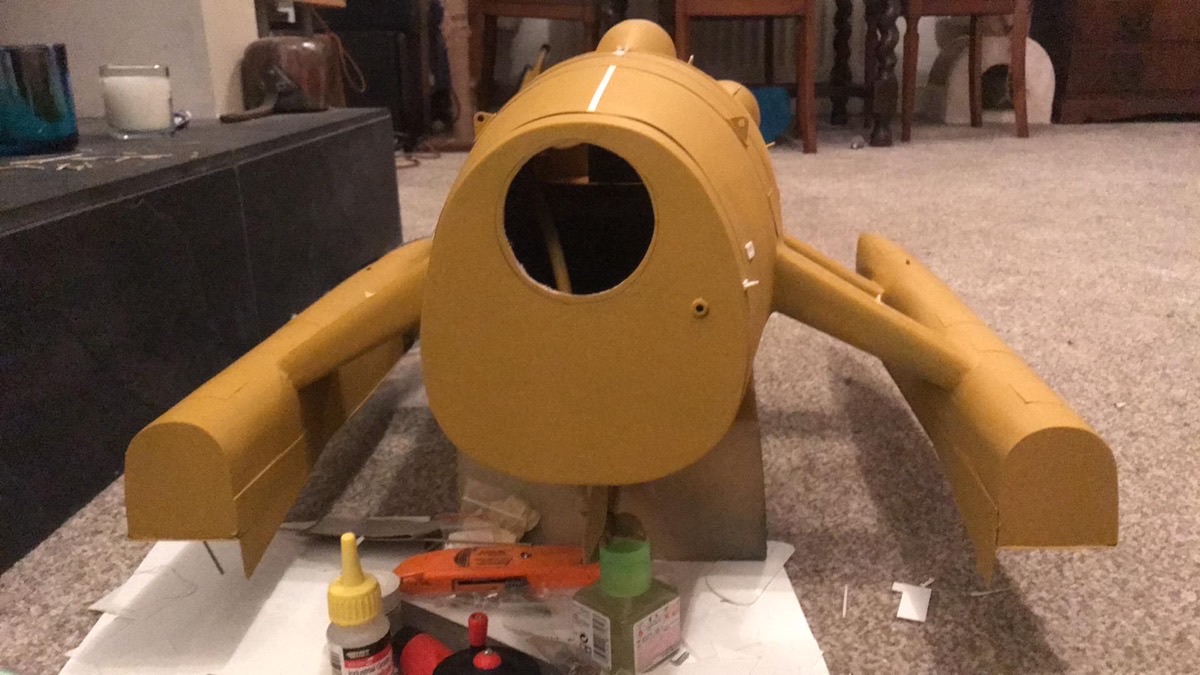
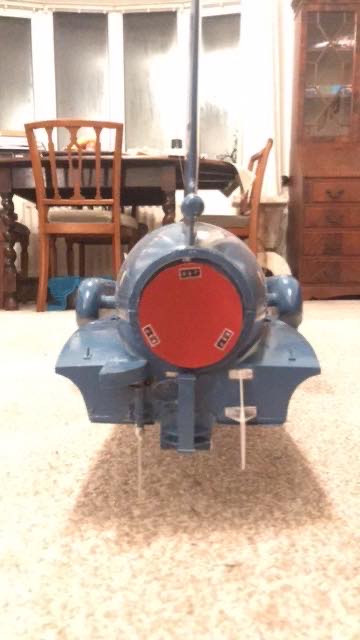
However on a more positive note the design of Crusader desirably had the centre of pressure considerably more towards the aft of the boat than was able to be achieved with the design of Bluebird K7.
In order to reduce hydrodynamic drag of the hull passing through the water, both Crusader and Bluebird K7 when at speed were designed to rise up out of the water to ride upon three points occupying only a few square inches. One of these points is under the main hull and the other two are beneath outrigger floats on either side of the craft. In the case of Bluebird K7 those outrigger floats are to the front of the boat and in the case of Crusader they are located to the rear of the boat. As a result the third riding point that is beneath the hull to Bluebird K7 is at the transom whereas the third riding point that was beneath the hull of Crusader was located to the forward part of the craft as shown in the following photos:
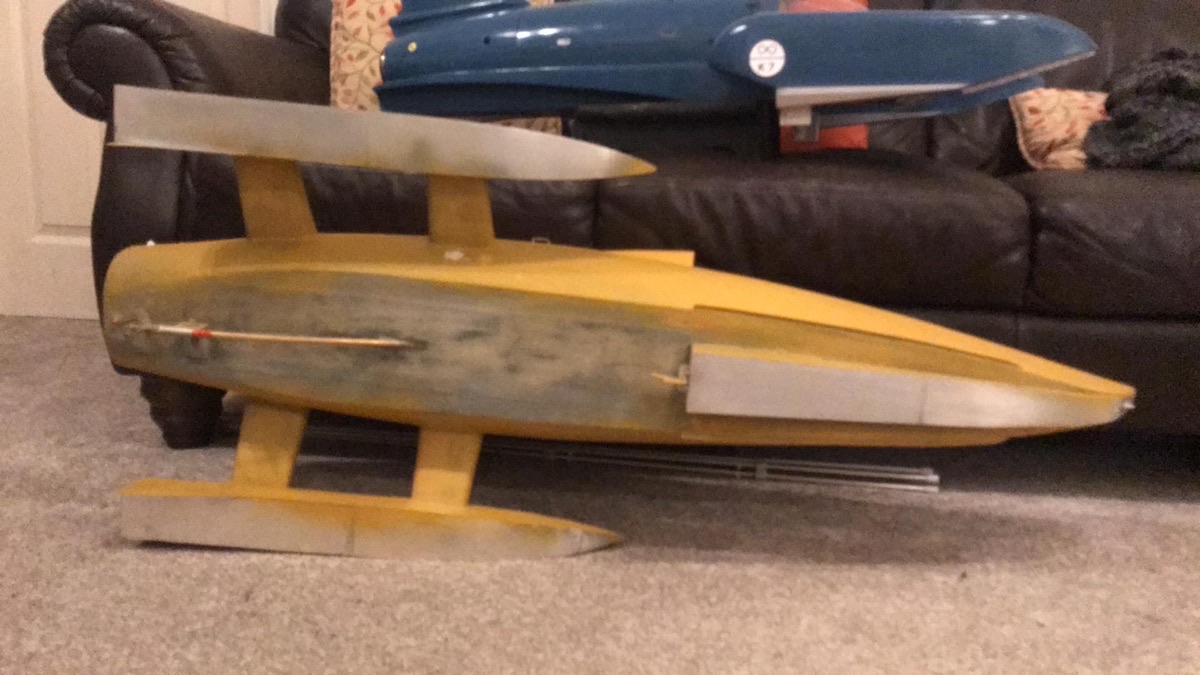
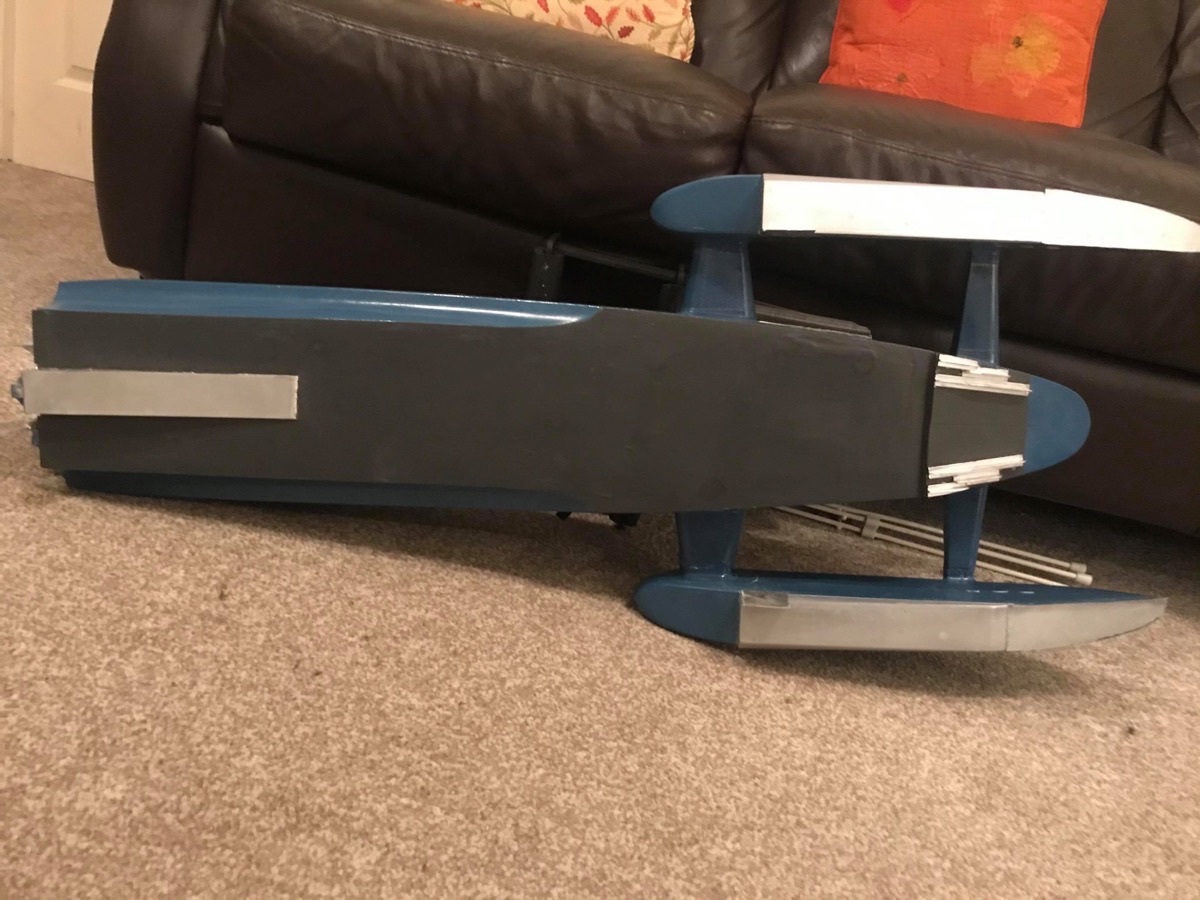
Crusader and Bluebird K7 are outrigger surface riding hydroplanes that have no air trap beneath the hull and were designed by engineers as their solution for travelling at high speed upon water. In the world of hydroplanes both historically and currently surface riding outrigger designs are relatively rare when compared to the vast majority of air trapping hulls. Air trapping hydroplanes are built on a very solid and proven foundation of thousands of hydroplane racers developing their craft over decades with a proven similar format that works across a considerable speed range. Indeed both the current and previous fastest boats in the world were built by people who had a vast amount of experience actually out on the water racing their designs and their choice was to use air trapping hulls with great success.
Comparatively engineer designed surface riding outrigger hydroplanes Crusader, Bluebird K7 and the other outrigger craft that attempted the Record, US Discovery II, were all craft that were themselves individually unique, all had major problems in one form or another despite encouraging model tests and all those ventures ended with crashes with resultant fatalities in every case.
It is all very well suggesting large heavy very powerful gas turbines in a surface riding outrigger jet hydroplane would in theory produce a craft that had a speed way above the existing Outright World Water Speed Record but one has to remember the craft has to work across a wide speed range to get there and whatever you design somebody has to sit in it and drive it at the end of the day, (or you just make a very big radio controlled model), there is a limit to how fast you can go when airflow around the hull begins to disturb the water surface and drivers of outrigger surface riding jet hydroplanes reported being unable to see due to eyeball oscillation. The current record holder Ken Warby MBE and his son David in both their air trapping jet hydroplanes report no such vision disturbance issues.
The danger with treating the Outright World Water Speed Record as just an engineering problem is that unlike the cars running in the desert on a known flat surface clear of debris for the land speed record; the jet hydroplane has no suspension, you are dealing with floating debris on or just beneath the surface in addition to waterfowl resting or in flight all of which can impact the craft; there are waves, ripples, wash and swell to constantly alter that lake surface one is running upon and to be compliant with rules for such records you are dragging rudders and fins through water that is 800 times more dense than air, the drag of which is going up at the square of the speed.
It is these types of issues along with the destructive nature of water bursting open voids upon impact that has given the Outright World Water Speed Record the reputation of being the most dangerous sport in the world. If you don’t treat it with respect it will bite, kill you and just for good measure take you to the bottom of the lake. That being the case would you rather put your life in the hands of a unique unproven engineered outrigger surface riding design and cross your fingers the engineers got their sums right, or sit in an air trapping hull that is a development of decades of high speed racing in hydroplanes across many classes, with the past two fastest boats in the world both being that type of craft and keeping their drivers alive…….?
For us the decision was a ‘no brainer’ and hence why Longbow is an air trapping hull of a proven format that with good fortune and development there is optimism for high speed running within the speed range she was designed for.
Finally on a personal note my great niece Delilah was born this week to my nephew and motorbike racing nut Phil and his wife Chloe. This is where you all go aaaw bless whereas Phil is wondering where you can buy ear defenders for babies when running jet hydroplanes?
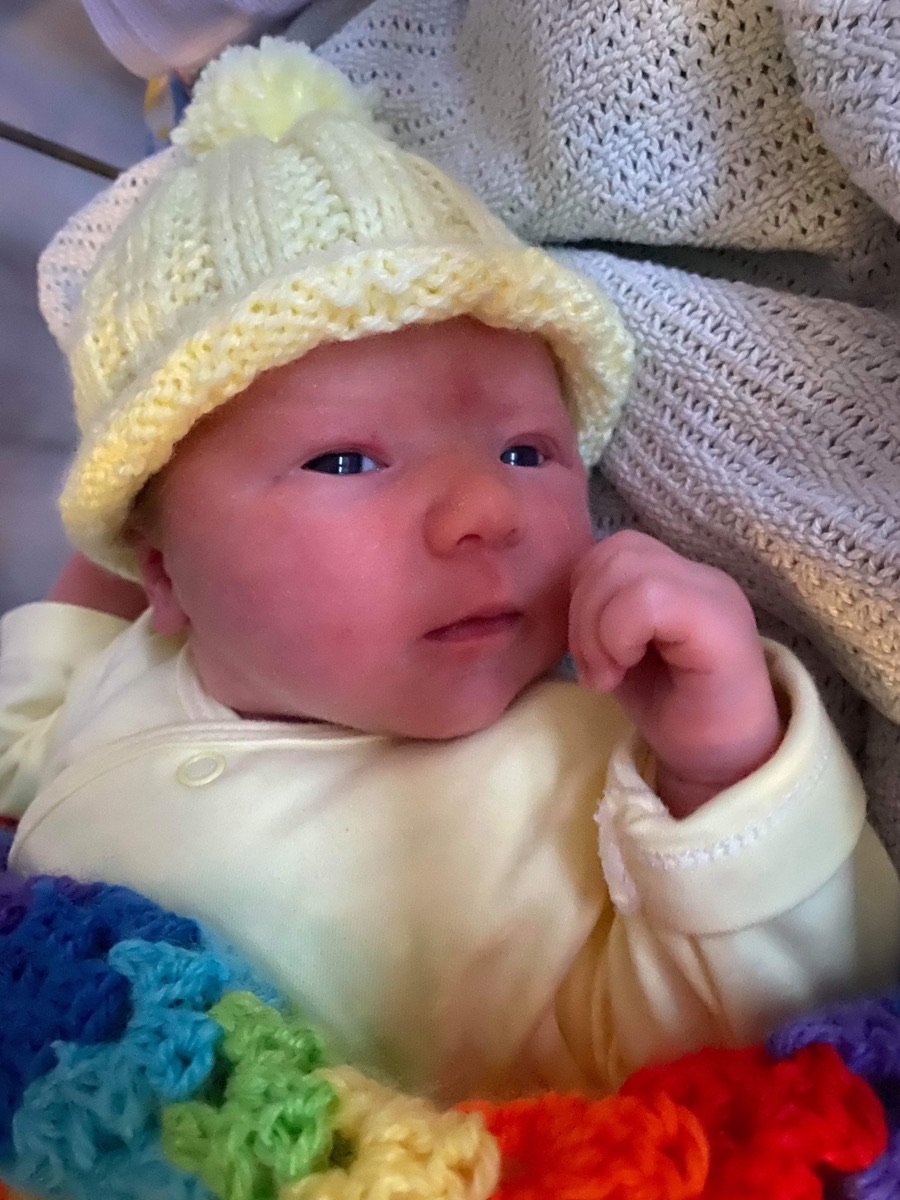
On that happy news we are done for this month folks. Thank you for all the kind words and support as the build continues of this exciting project of building our jet hydroplane Longbow. Please drop by again at the end of March for the next instalment of the venture and in the meantime if you have not done so already and are into social media, take a moment to like our Facebook page.