This month’s update should really be titled ‘no pressure’ as it begins with reference to an online discussion with a nice chap who has been following the building of our jet hydroplane Longbow and in particular our recent exchange regarding how her jet engines work. The comment from him was that the jet engine is basically like a piston engine followed by the comment that it is a process of ‘suck, squeeze bang blow’ which here in Blackpool can have several meanings on a night out but in this case it referred to an engine where you set fire to fuel and the resultant increase in pressure blows out the back of the engine thereby giving you thrust. To which I said there is no increase in pressure with a jet engine, it doesn’t work the same as a piston engine. His reply was well there is obviously no piston in a jet engine but the principle is the same.
As there are quite a few ‘petrol heads’ that are following the venture I thought the above may well be a common misconception of how our jet engines work so the following in hopefully relatively simple terms is my stab at an explanation of why a jet engine does not work in the way a petrol or indeed a diesel engine performs that my good friend described above.
So let’s start with a photo of a jet engine in this case a Bristol Siddeley Orpheus the same as Donald Campbell used on his last attempt with his jet hydroplane Bluebird and in this case one that I overhauled for the Bluebird replica K777. The bit where the air goes in is on the left and the bit where it comes back out is hopefully at the other end. If it comes back out of the front then it’s a case of ‘Houston we have a problem’.
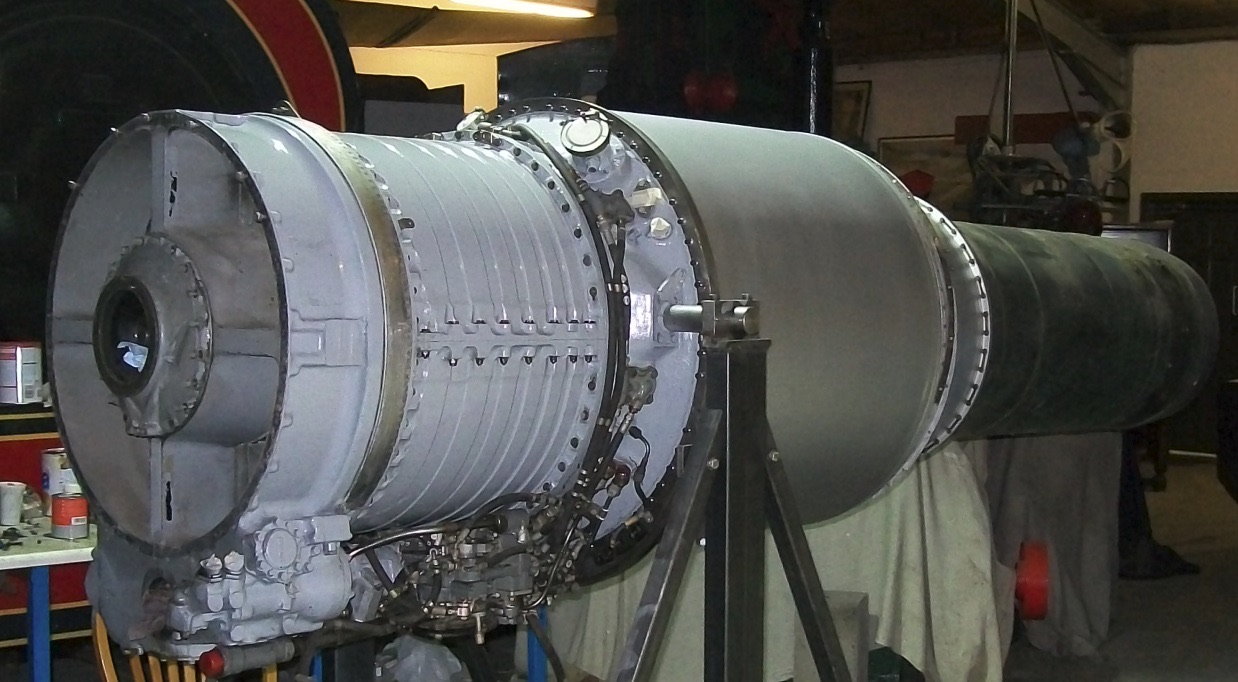
So let’s take the jet pipe off the end and rotate the engine vertically so the front is now at the bottom of the photo.
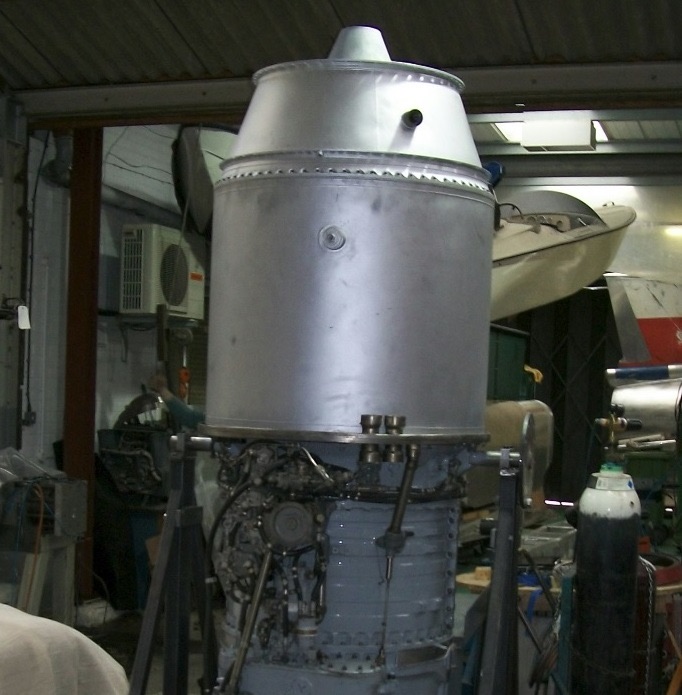
Now with the aid of a spanner and a few swear words we can take one half of the engine casing off and as you can see in the next photo, what that reveals at the front of the jet engine is the compressor which in our case is basically several wheels with blades around the outside fixed onto a common shaft. If you spin the central shaft all the compressor wheels turn in the same direction and the blades on those wheels are shaped to move air from the outside deeper into the engine.
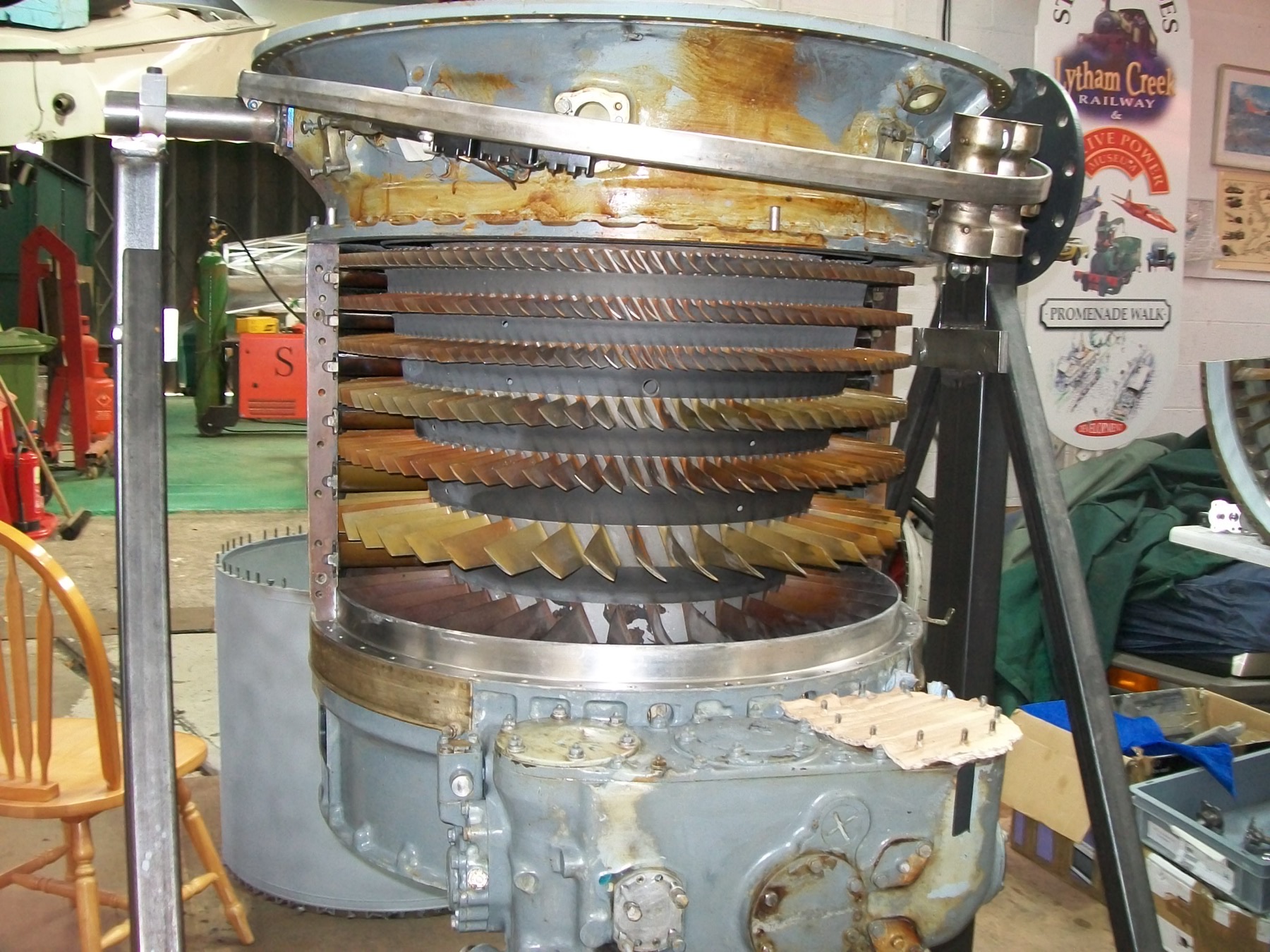
The air that is being blown along the tube by the fan (compressor) on the front of the engine, is then directed around the outside of several metal cans. So let’s take the next bit of the engine outer casing off and have a look at those cans.
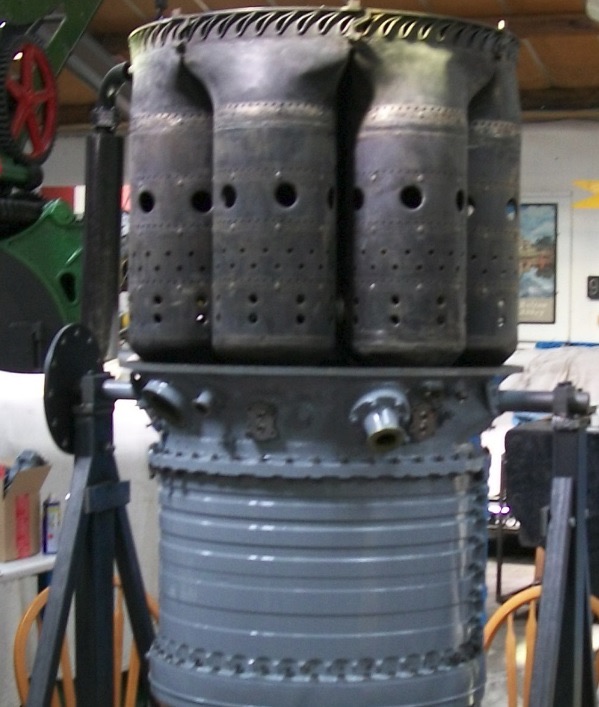
As you can see each of those cans have lots of holes around their sides and this allows the air that the fan (compressor) on the front of the engine has blown in, to be pushed to the inside of each of those cans.
Just for a moment let’s take these cans off and have a look at what is at the front end of the inside of each of those cans.
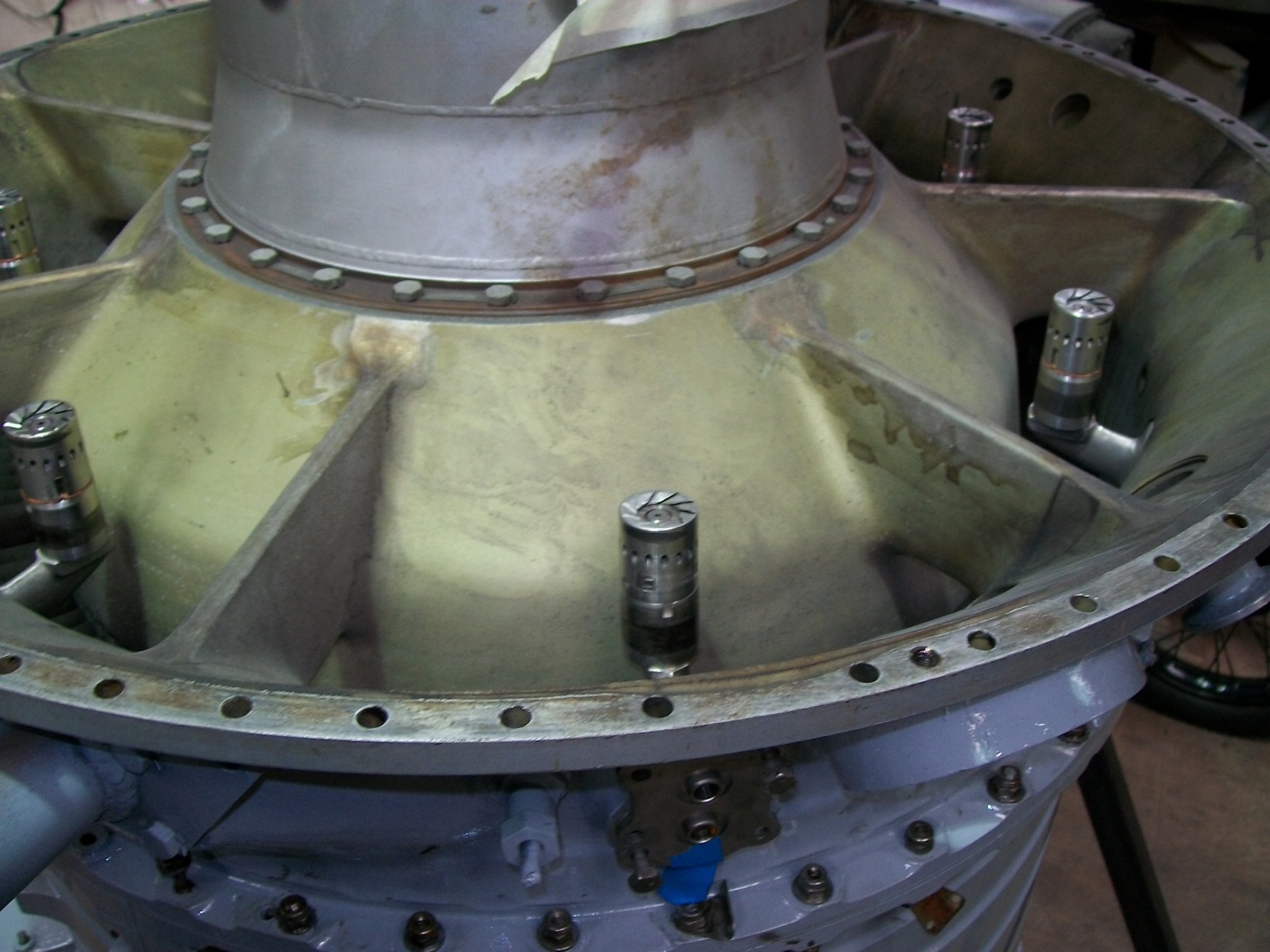
What you have here is a spray nozzle at the end of a fuel line. The fuel line is connected to the fuel pump which in turn is connected to the fuel tank that is so very expensive to fill given this engine is drinking around 45 gallons in four minutes of run time. Anyway back to the nozzle in the photo this nozzle sprays the fuel out into the can in a fine mist such that it mixes with the air in the can. This combination is set alight by a spark provided by electrics outside of the engine. Once this fuel mixture is lit and air mixed with fuel keeps coming the engine has a constant fire raging within each of those cans so the electrical spark that provided that initial combustion can be turned off and the engine just carries on working and drinking fuel and air. At full chat this engine is consuming around 83 lbs of air per second, that equates to around a 30 cubic metres of air per second so not the place to stand in front of counting your loose change in your hand.
Now here is the point of difference between a petrol / diesel engine and a jet engine and what I was referring to in my opening comment of ‘no pressure’. In a petrol /engine the combustion of the fuel is within a closed cylinder at point of fuel ignition which increases the pressure in the cylinder and forces the piston down the bore. However in our jet engine the combustion cans are not a closed cylinder at all, they have holes in their sides as previously described to let air in and at the rear of the cans they have further holes to let the hot air from combustion out the back. Because the cans are therefore not a closed void during combustion there is no increase in pressure.
What you get as a result of the combustion of jet fuel and air is a massive increase in volume and so the speed of air through the jet engine increases dramatically as it passes out the rear of the engine. It is this increase in volume of the air that transfers into speed of the air exiting the rear of the engine that provides the thrust from the jet engine to move an airplane or in our case a jet hydroplane along.
As this accelerated air rushes out of the back of the engine it also has to pass through another wheel with blades on it that is called the turbine wheel, or some refer to it as the ‘hot wheel’ because of the hot gases passing through it. So let’s have a look at that wheel on this engine.
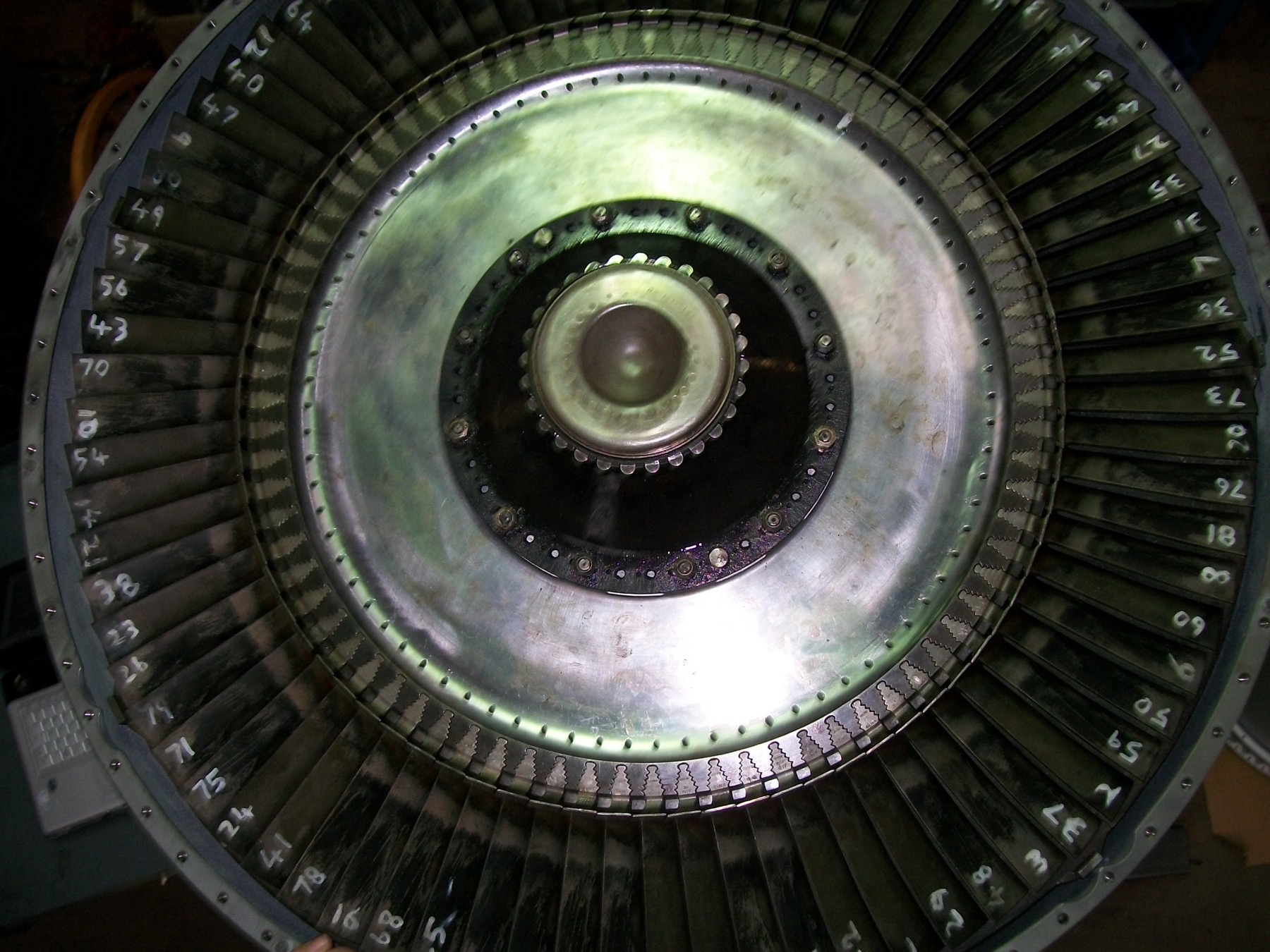
As the hot expanding gases rush past the blades in this wheel, it forces the wheel to turn around and as the wheel in this case is connected to the same shaft as the fan (compressor) on the front of the engine, the quicker this turbine wheel rotates, then the quicker the fan on the front of the engine rotates and consequentially the more air is drawn into the engine.
Of note one of the problems the jet engine has to deal with is the temperature of the flame inside the cans. This is not your Christmas candle hot, it is 2000ºC hot and unfortunately for our engine that is way above the melting point of the metal the cans are made of. That is to say they will no longer be a can in the region of 1350ºC. this being the case our flame within the can cannot be allowed to touch the sides of the can or indeed come out of the back of the can because it is so hot it would also melt the blades of the turbine wheel if that happened.
Luckily there is a lot more air passing through the engine than is actually used up by the flame and hence the excess air is used to surround our flame inside each can. This excess air acts as a thermal barrier between the flame and the metalwork of the combustion can, in addition to also cooling the gases emerging out the rear of the combustion can sufficiently to a low enough temperature to not melt the turbine blades as they pass through it and on their merry way out of the jet pipe.
From the above one will appreciate that the quicker the engine revolves the more cooling air is passing through the jet engine and hence why the engine operates most efficiently at 100% of its operating speed. At the other end of the scale the most hazardous time for the engine is upon start up when the amount of air being drawn in by the fan (compressor) at the front of the engine wouldn’t take the skin off a rice pudding. Hence with so little amount of cooling air provided the temperatures seen within the jet pipe and engine will be at their greatest. Note to self it is therefore critical the temperatures of the engine at start up are monitored carefully to ensure they remain within limits.
The temperature of the hot gases created by the jet engine are typically only measured by thermocouples within the jet pipe which is downstream and outside of the working parts of the engine itself. Whilst such temperature measurement is a critical aid to monitoring the condition of the engine, measuring the temperature in the jet pipe only, can lead to a false indication of engine condition and it is something to be aware of when manually starting these older jet engines as it can cause the unwary operator to make mistakes and damage the engine. This risk is reduced on more modern engines by the electronics used to monitor and manage the engine. Typically refereed to as Full Authority Digital Engine (or Electronics) Control (FADEC) this box of tricks prevents the pilot or operator from asking the engine to do things outside of its operating limits, including how it is started.
I hope the above has not confused you too much and helped you understand a little more about the engines powering out jet hydroplane Longbow.
Following feedback I realised that part of my explanation around jet engines may appear somewhat ambiguous to the lay person. In particular my comment ‘Because the cans are therefore not a closed void during combustion there is no increase in pressure.’ could be misinterpreted as me saying there is zero pressure.
To put this more clearly, I thought I would add some comments from my good friend Robin Snipe, who is a fully qualified gas turbine engineer and President at S&S Turbines Ltd.
There is 0-pressure rise from the inlet of a combustor to its outlet. In fact there is slight pressure loss. However, immediately upstream of the combustor, across the compressor outlet diffuser, there is a distinct pressure increase, as kinetic energy (gas velocity.) is converted to potential energy. (Pressure.) So, If you look at only the combustor, and not the combustor module, there is a slight pressure loss. Across the whole module, including the compressor diffuser, there most certainly is a pressure increase.
Also, keep in mind that the outlet area of the compressor (Not including the diffuser.) is significantly smaller than the first stage turbine nozzle area.(Or turbine inlet.) If the combustor did not add any heat, the pressure drop across the combustor module would be very high indeed, and of course the engine would not operate. (Perpetual motion.) The added heat, causes the gasses to expand, keeping the total pressure loss across the combustor as close to “0” as possible, effectively allowing the turbine to run, as the total area leaving the combustor module is bigger that the total area entering the module. Across a whole turbine engine, of course there is a pressure rise, it all depends on where you measure those pressures! If you look at P0 (Atmospheric.), P1 (Inlet duct.), or P2 (Inlet of compressor.), it is always lower than P7 (Jet pipe pressure.), otherwise the engine would not develop any net effective thrust! Pilots call often call this P2/P5 pressure ratio, and is the holy grail as to how an engine is making thrust. Same in industrial units, only the terminology may be changed. The sole function of any turbine or jet engine, is to act as an air pump. Take atmospheric air and accelerate it. How it is used is up to the end client.
I trust that the above clarifies any confusion with the technical followers of our readership which I may have unintentionally caused.
Back with the build of the hull you may recall that we finished last month at the point of getting one of the sponson shoe laminations on and the additional nose section of that sponson put into place. This month my eldest son Tom, my wife Gill and myself were able to complete the laminations on that sponson using marine grade timber very kindly supplied by Richard Bagnall, Managing Director of Robbins Timber.
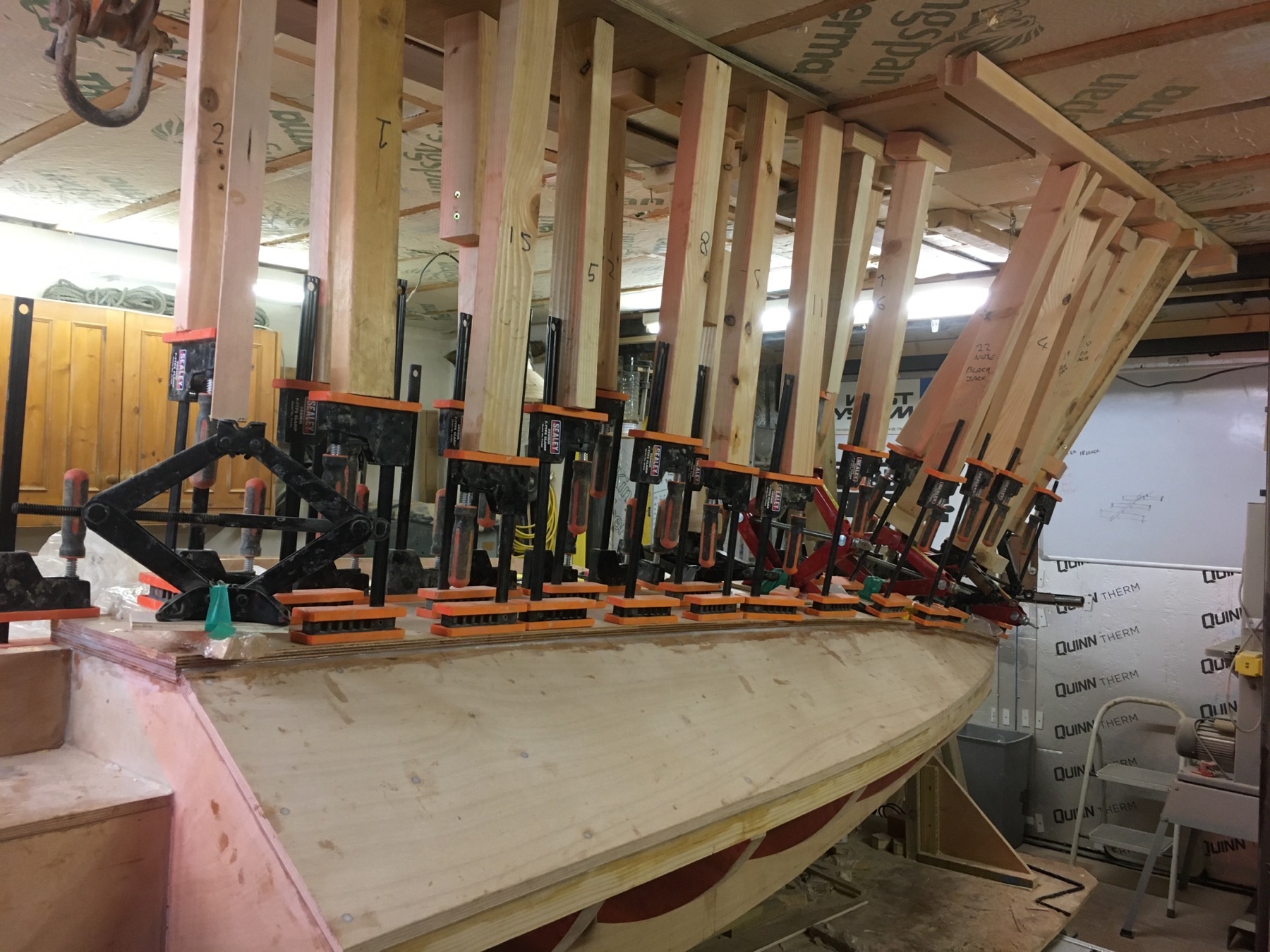
Once that side was done we could then move onto the matching sponson on the other side. Again this was a stepped process of getting one layer of plywood into place, then the additional nose section scarfed into position, followed by the other laminations. This all being held into place using the clamps supplied by our sponsor Sealey Tools. The whole fixing process being totally reliant upon the WEST SYSTEM Epoxy and WEST SYSTEM 403 Microfibre Filler very gratefully supplied through Colin Fletcher of our sponsor Wessex Resins.
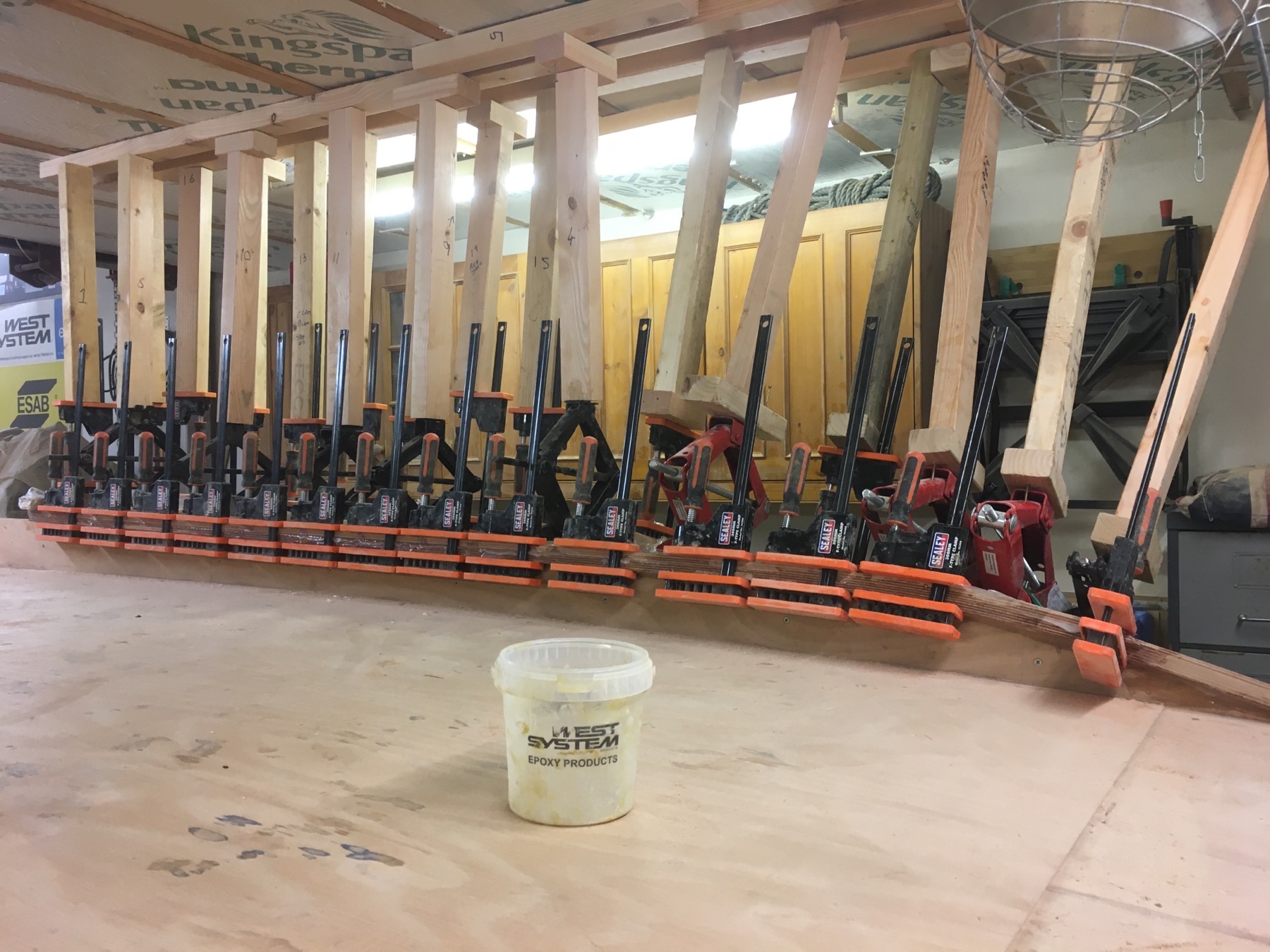
Once each stage of the epoxy fix had cured, the temporary fixings could be removed and the area cleaned up before the next layer could be added in a repeat of the process. It sounds an easy two minute job when you write it out in a sentence like that but in reality there was an awful lot of work in teasing everything to sit right, corkscrew curve the plywood, shape the nose of the sponsons and trim the wastage followed by lots of hand planing and sanding to get the desired sponson and their planing shoe shapes but we got there in the end.
This month also saw the arrival of product from our terrific sponsor FIBREMAX COMPOSITES with our utmost thanks going out to Dimitrios Apostolakis and Elizabeth Lioliou of Fibremax for their superb assistance with the venture by way of sending us rolls of both carbon fibre fabric and peel ply fabric.
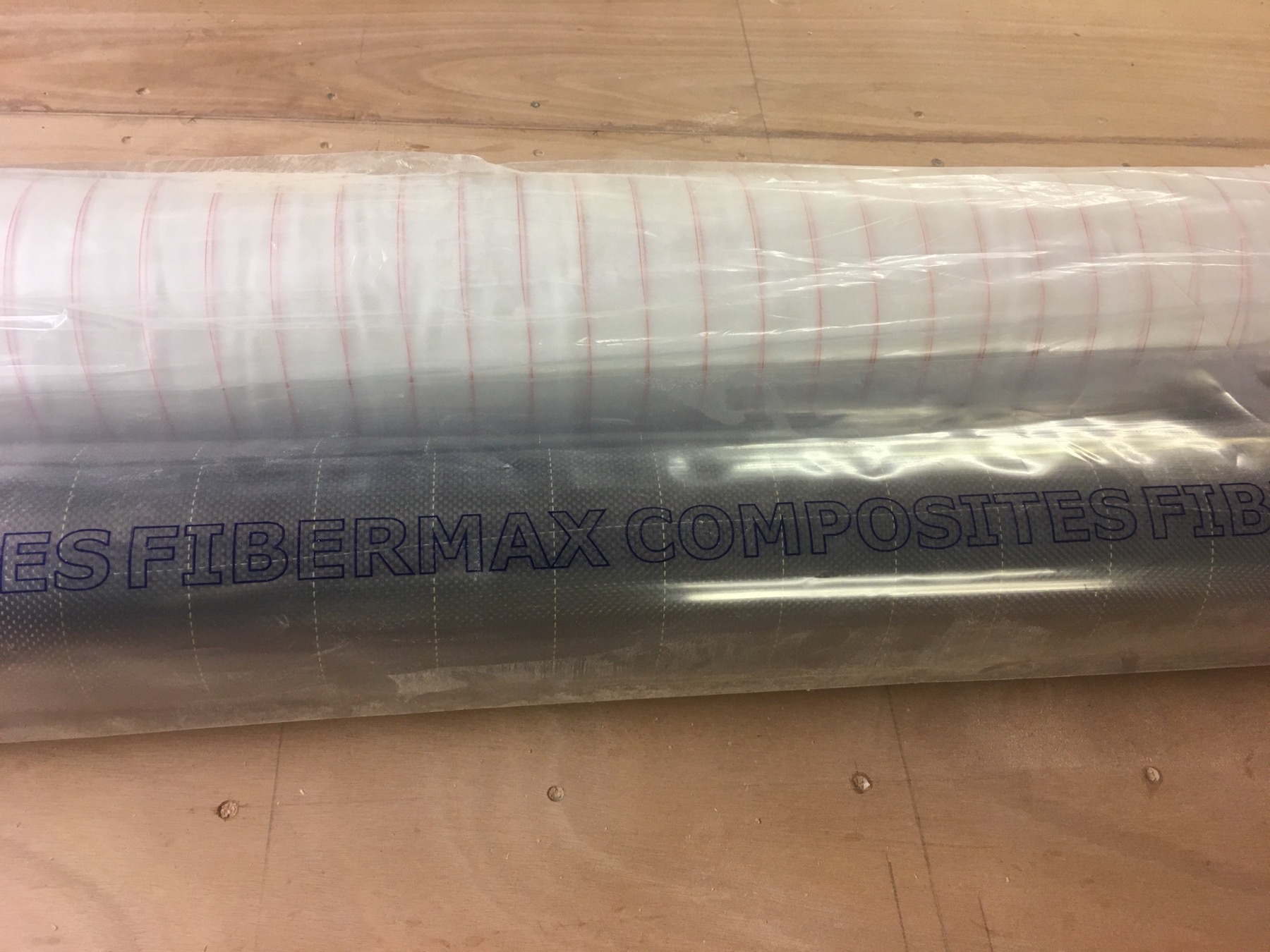
The peel ply will be laid over the carbon and Dynel areas and allows Amine blush to form on the fabric of the peel ply, rather than on the outer face of the epoxy. This will thankfully eliminate the need for scouring and washing the surface of the epoxy over the entire underside of the hull sponsons and rear planing wedge to remove the inevitable Amine blush.
After we had completed the sponsons section described previously we could then move on to getting the laminated rear planing shoe fixed into position, again using the WEST SYSTEM Epoxy and filler from Wessex Resins. I forgot to take any photos of the wedge being clamped down so I only have the before and after images to show as follows.
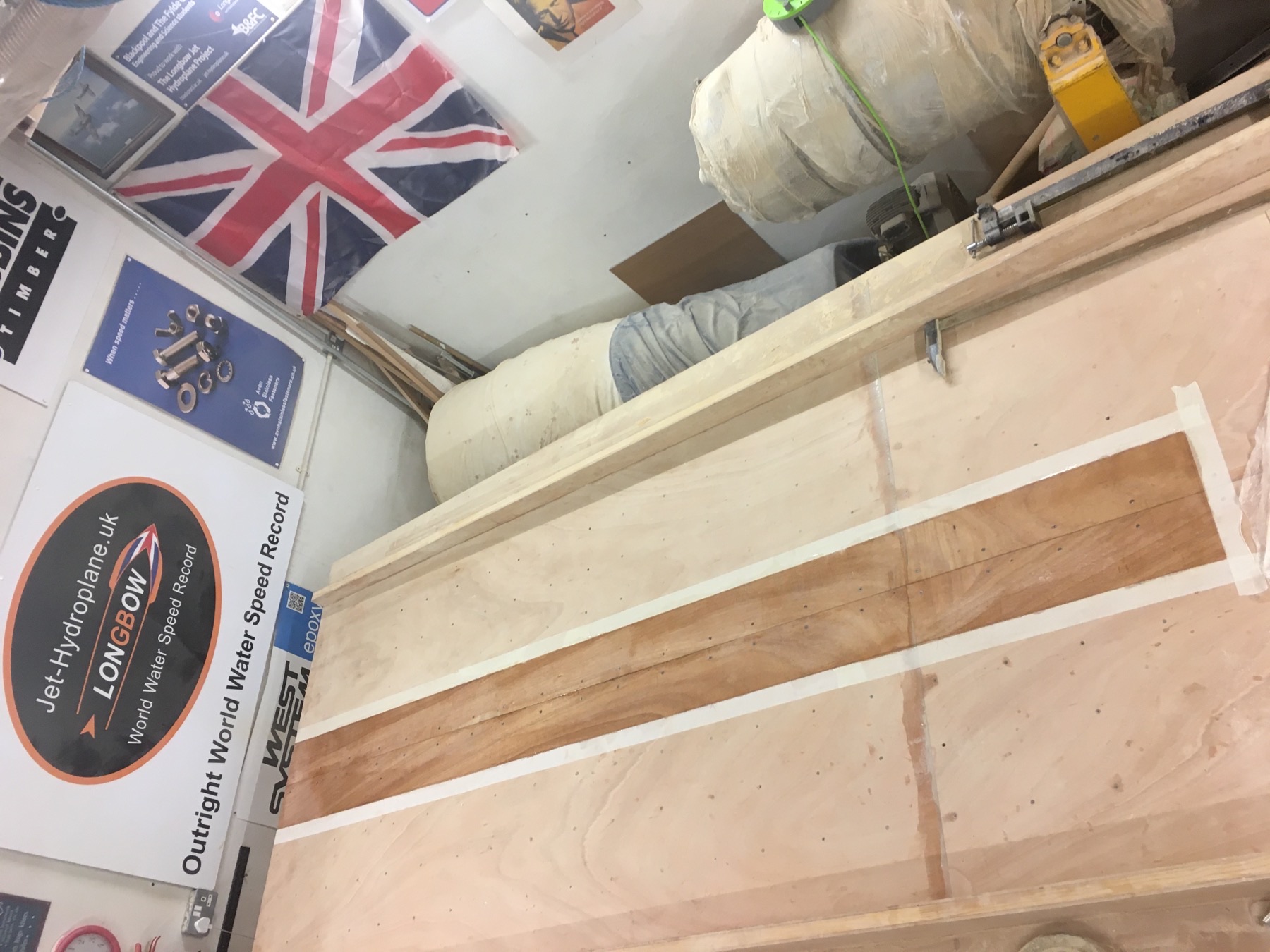
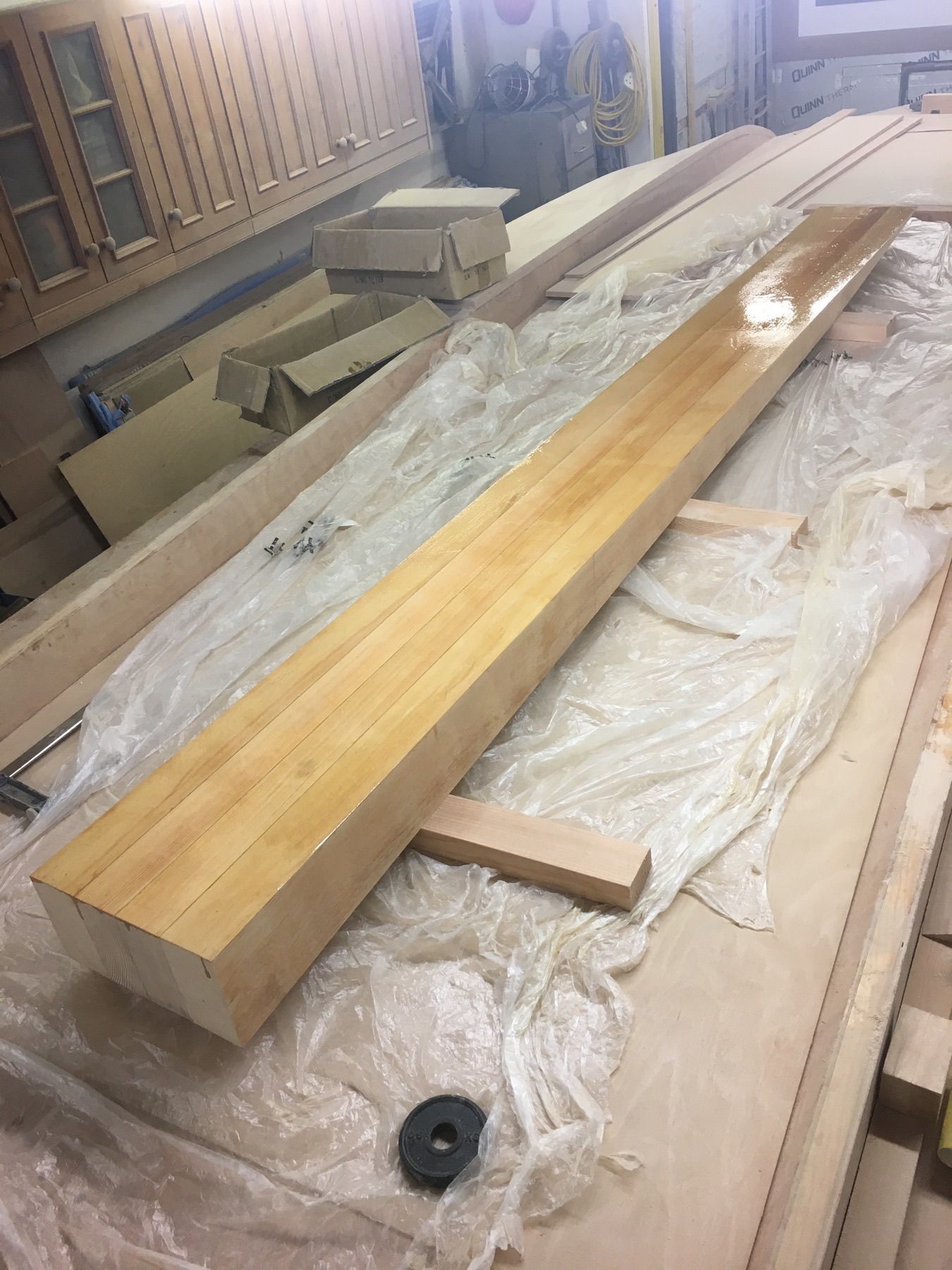
The next task will be to cover the rear planing wedge riding surface with a laminate of Robbins marine plywood so as to protect the vertical joints of the timber shoe laminations. Once that is done we can then move on to filling the hundreds of screw holes with epoxy, smoothing out the scarf joints, inevitable lumps and bumps of the underside of the hull before we can move on to the next stage of laying the carbon and Dynel fabrics to the underside of the hull. I am filled with trepidation about doing this as it is a very large area to undertake and put right if it goes badly but fortunately my good friend Dave Warby over in Australia has given me good advice as always to avoid some of the pitfalls.
What you can now hopefully appreciate is the shape of the underside of Longbow and for me this is a very poignant stage of the build to finish the year with and what a very challenging year for all of us the world over it has been. I look forward to turning the hull over onto her new trailer (being built by our great sponsor WEC Group) within the beginnings of 2021 and then we can move on to the exciting bits of fitting her twin jet engines into place.
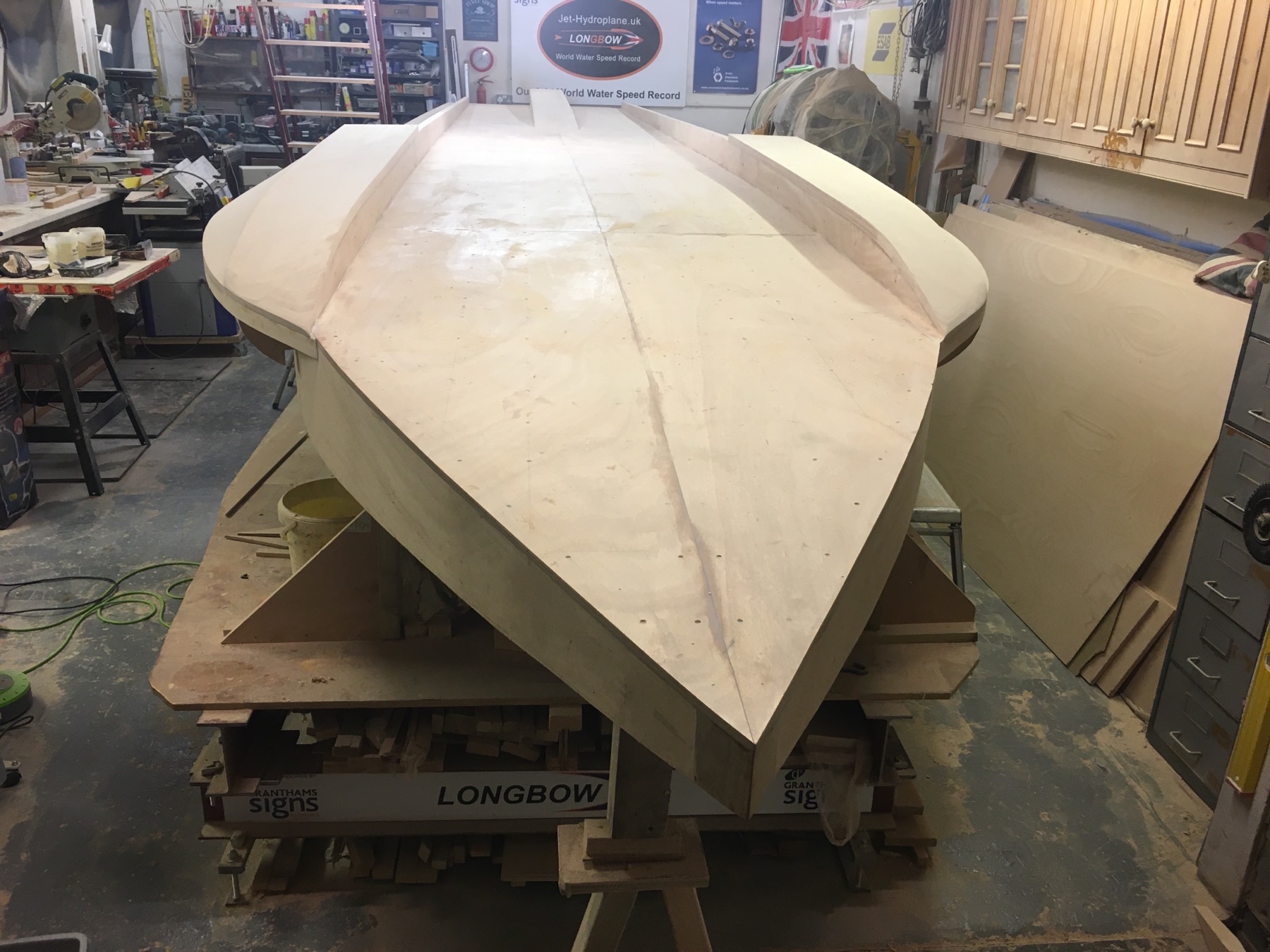
As we close this traumatic year my sincerest thanks goes out to all of our sponsors for continuing to support the project during this time. I know some businesses have really struggled to keep their staff and their companies running due to the impact of the pandemic in addition to all the challenges with Brexit upon us, so to continue to help us with the supply of product throughout this terrible and protracted period will not have been easy and I am so very humbled by the kindness and generosity of your continued support in making this fantastic venture happen for without you the project would not be making the fantastic progress it has and continues to make.
For those who have tuned in each month to read my twaddle I thank you all for putting up with my appalling style of writing and terrible grammar. I wish you all a safe Merry Christmas and very much a Happy New Year with hopefully at some point in 2021 a return to normality and to good times ahead. Also to my very dear friend Dave Warby, his partner Lesa and their team good luck with your further testing of SOAII next February and every success with your attempt on taking the Outright World Water Speed Record from your old man and living legend Ken. If anyone deserves it Dave it is you.
Thank you for tuning in to this close of year diary update and please stop by towards the end of January next year to see how we are getting on with the build of our jet hydroplane, Longbow.