Here in Britain we have come to expect wind and rain for most of the year but when I think of Australia, it conjures sweltering prolonged sunny days. That being the case it came as something of a surprise to see our good friend Dave Warby and his team struggling down under with stormy weather as they undertook their latest testing of his jet hydroplane Spirit of Australia II relatively local to him on the Manning River, Taree, New South Wales.
Dave was hoping to take the boat down the river at speeds knocking on the door of 200mph in order to see how their latest rudder with revised steering was behaving prior to making the prolonged trip to Blowering Dam (where his father Ken Warby MBE set the current Outright World Water Speed Record of 317mph). However the awful weather at Taree whipped up the surface of the river with white horses so badly, that they were lucky to manage around half that speed but it was testament to the strength of her timber hull that she coped so well with such poor conditions.
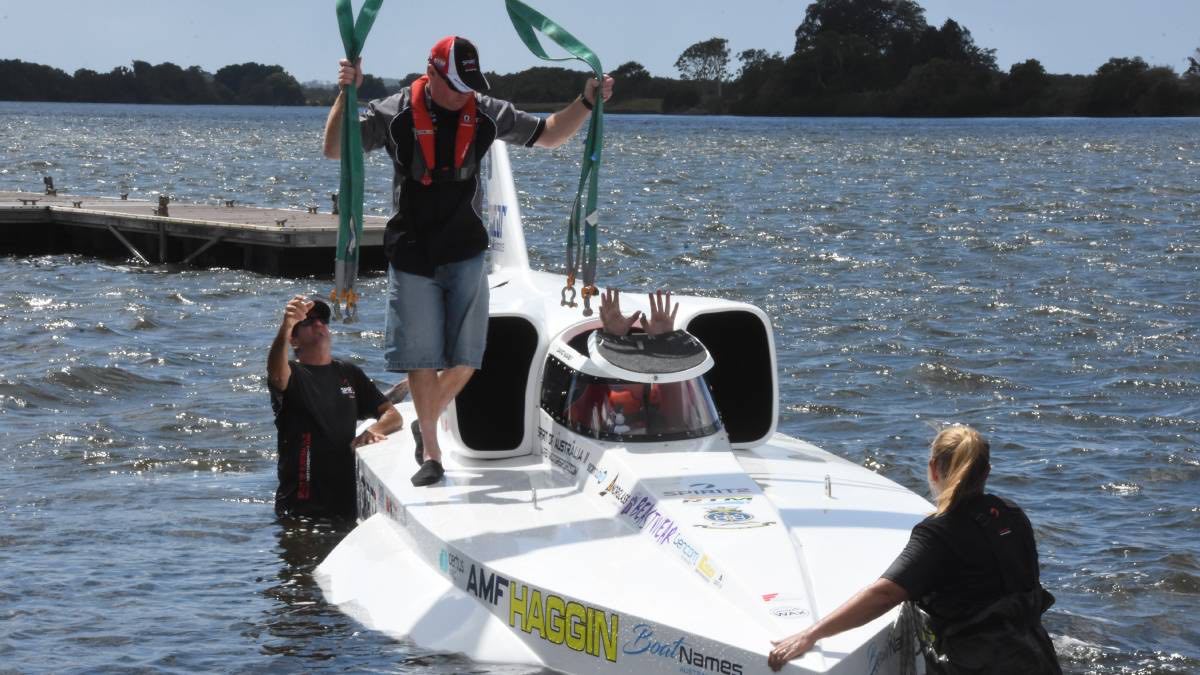
Courtesy of Dave Warby
That as they say is the nature of record breaking being at the mercy of the weather but it was a shame given their jet hydroplane is now equipped with technology that allows people to live stream and travel along with Dave in real time during these tests. Undaunted Dave and his team have been granted permission to return to the Manning River, Taree at the end of this month for further tests.
Back in the UK it was nice to see the multi million pound Bloodhound Land Speed Record car re-launched, after being bought by Ian Warhurst and his Company Grafton, who are taking the Project forward. They are apparently retaining Wing Commander Andy Green as driver and the Eurofighter engines on loan from the British Government. The aim being to still run the car in South Africa.
All that is a far cry from our little cottage workshop tucked away on the Fylde Coast, where family friends come together after work to build our jet hydroplane Longbow, chasing our good friend Dave Warby to have the fastest boat in the world.
We might not have the big bucks or the latest military high tech Government supplied jet engines that Bloodhound has but nevertheless we have fun, talk rubbish, have plenty of brews being part of that great tradition of pottering in the garage building something we have set our heart upon completing and having a go at this most challenging of speed records. If we can manage to just even come close to emulating in the boat world, what Burt Monroe managed to do from his shed on his motorcycle, made famous by the film ‘The World’s Fastest Indian‘ then that will do for us.
We hope that our little venture is something people sat at home can relate to and have a chuckle at, as we dare to build our jet hydroplane Longbow in a home workshop situation, then test her methodically and carefully to see if she can be developed into an Outright World Water Speed Record contender.
In the past few months we have spoken about what a joy wood is to work with as nature’s own composite material, to build the hull of Longbow. Since the discussion to date upon timber within our previous diary updates appears to have been very well received by those who kindly wrote in, particularly those in education, we thought that we should perhaps this month, harp on a bit about some of the risks of degradation to timber that anyone has to be mindful of when building with wood. Apologies if the following information bores you when all you want to read about is jet hydroplanes but you never know, it might just be something you don’t mind learning a little bit about after all.
If you think about it, life on earth is dependent upon plants growing and from our school days we remember that they do this by taking up carbon dioxide along with water in the presence of sunlight. However left unchecked plant growth would consume all the earth’s carbon dioxide and we would not be able to move for vegetation. Mother nature steps in to control this situation by way of providing fungi and insects that will devour plant material, be it dead or alive, cleverly putting back carbon dioxide into the atmosphere through respiration during this process.
So whilst building the hull of Longbow in wood we have to ensure there is no risk of fungal decay occurring, or it being eaten by those pesky insects, we also have to be mindful of it being damaged by certain chemicals, or effected by sap stains and mould growth.
It is therefore important that we can recognise different wood boring insects because some insects such as pin hole / shot hole beetle will emerge from the wood when the tree is recently felled and will not re-infest as the wood is dried down for use, hence no control treatment is required. Other wood boring insects however will happily carry on eating the wooden structure, until there is nothing left to consume.
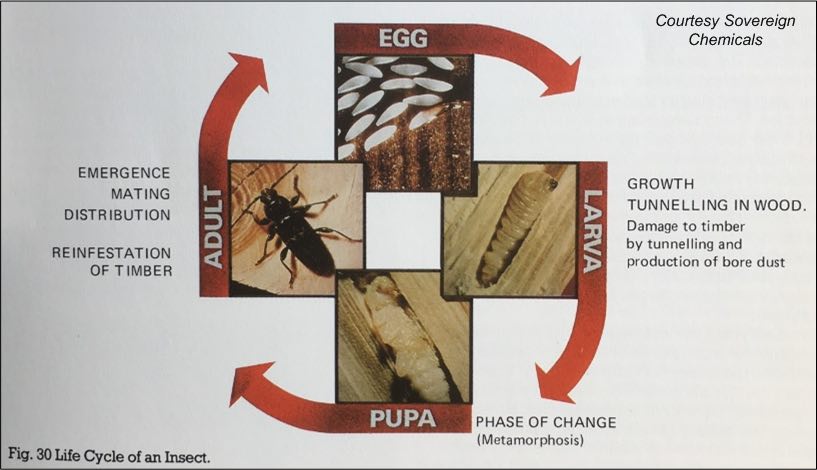
Some wood boring insects are very fussy about what they feast on, such as House Longhorn beetle who will only eat softwoods, whilst other species such as Deathwatch beetle will only tuck into hardwoods.
A bit of trivia for you here is Deathwatch beetle got its name from being heard dining out on prison timbers during the middle of the night, when a condemned person would be watched by prison wardens on their last night, prior to execution. I kind of like to think they were eating the wooden gallows to the point of collapse in order give the poor soul half a chance but anyway there are also those insects which are far less fussy on what they dine out on such as common furniture beetle (often referred to as woodworm), who will happily munch through both softwoods and hardwoods.
There are wood borers such as weevil, that can only digest damp decaying wood (and hence if present are an indication of rot), whilst others such as Lyctus which will only eat timber with a high starch content, so those will not re-infest wood as that starch content naturally depletes over time.
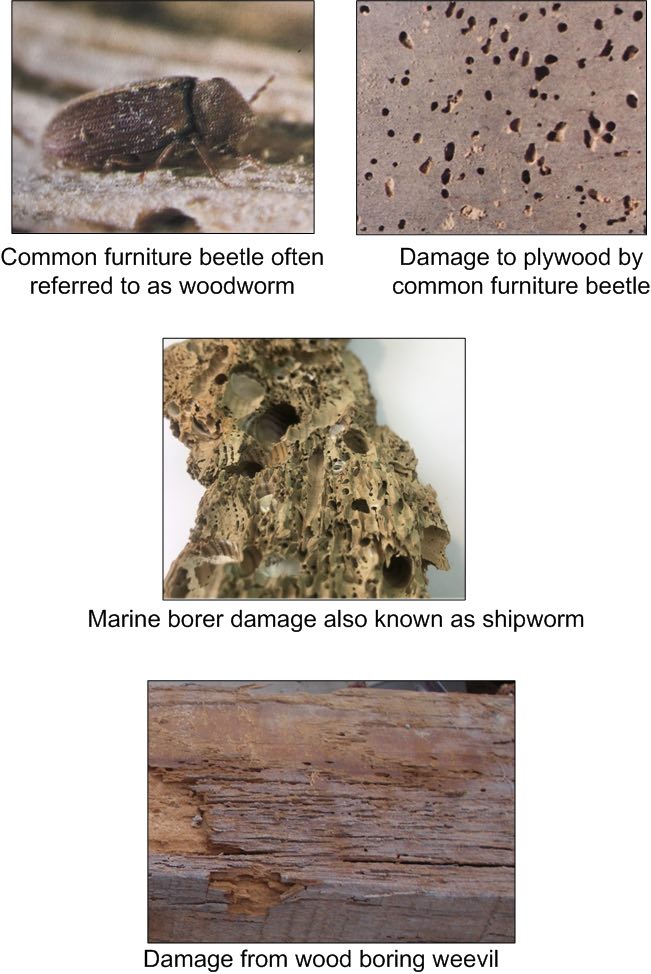
Sometimes chemicals may assist as a control measure for ongoing wood boring insect attack but also freezing and heating will usually (at least for insects native to the UK), dispatch them. So before binning that picture frame peppered with woodworm, you might want to try popping it in a sealed bag next to the ice cream over night, stressing sealed bag unless you fancy that rum and crunchy raisin flavour you don’t remember buying!
Moving on to fungi and their relationship with wood, sap stain for example, often occurs in the ray tissue (cells of wood orientated from bark to centre) during seasoning. Whilst this fungus does not effect the strength of the wood, since it will not attack the cell walls and cease to be active once the wood moisture content drops below 30% during seasoning, it is often rejected by the end user due to it being unsightly.
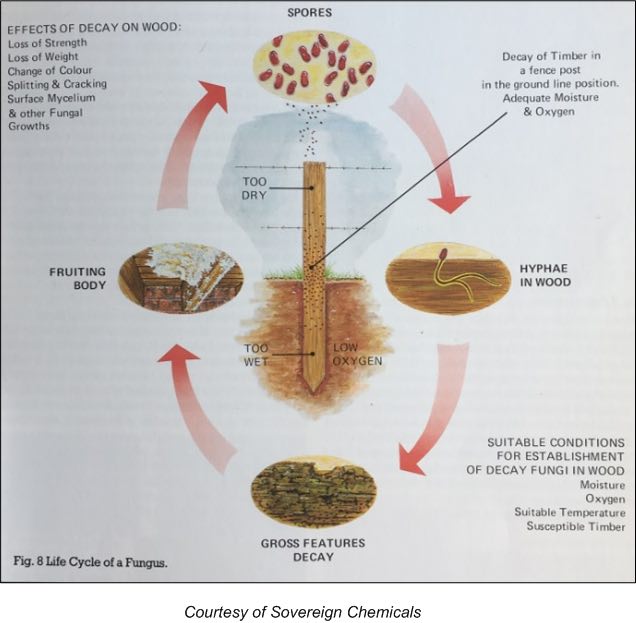
Brown rots are the result of fungi that digest the cellulose and hemicellulose of the wood but leave most of the lignin (which if you remember we discussed last month) behind such that they can consume about 65% of the timber by weight. Characteristics of these rots are the wood becoming darker in colour, hence the term brown rot, typically accompanied by cuboidal cracking across the grain and being able to be crumbled in the hand where the infection has been severe.
White rots on the other hand will readily consume not only the cellulose and hemicellulose but also the lignin and therefore eventually devour the entire wood. During this process the wood becomes lighter in colour, hence the name white rot, along with it looking like it has broken down into fibres with no cross grain cracking that you would otherwise see in a brown rot.
Except for one particular form of brown rot, called dry rot, all the other species of brown and white rots (of which there are many) are collectively referred to as wet rots. The name dry rot often strikes fear into home owners because unlike wet rots, the dry rot fungal strands are very invasive having a love of dark dank concealed places and will readily grow through soils, hardcore, weak mortar beds of masonry, beneath solid floors etc, in search of more wood to devour.
Once a building becomes infected with the fungal strands of dry rot, it cannot be easily removed without rebuilding the structure. Because of this it can be very difficult to kill off completely, at least within the short term and hence may remain dormant for many years, then become active once more should conditions become favourable for it once more.
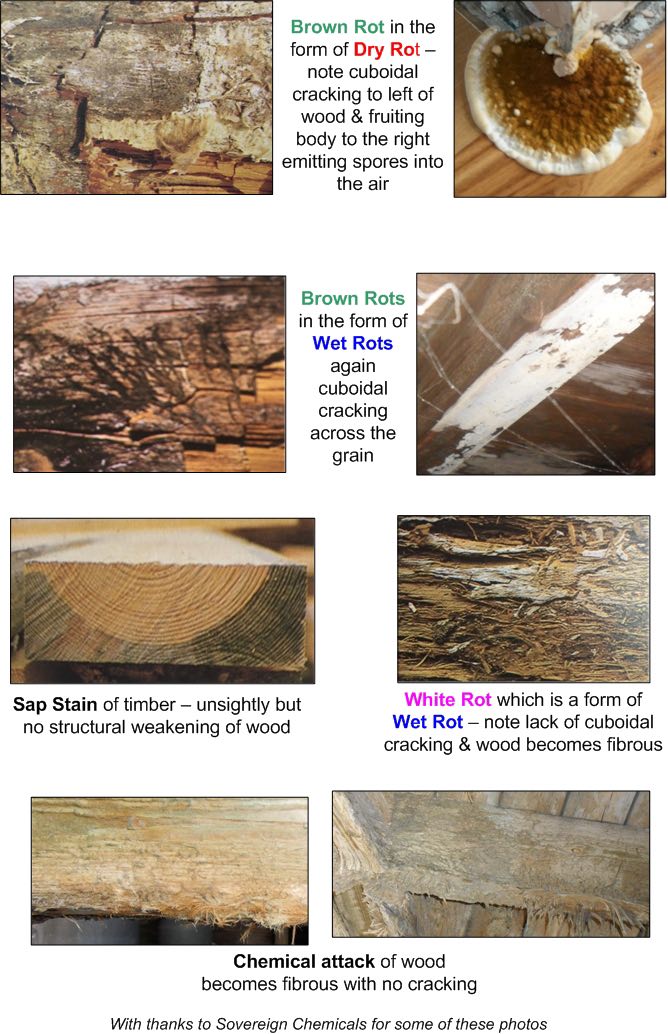
The spores of wet and dry rots are in the air all the time and are about 1/100mm long if you fancy measuring one. Both dry and wet rots require wood as a food source, oxygen, a certain temperature range and importantly some degree of moisture to germinate and flourish. Wood will initiate decays at around 28% moisture content but can sustain it down to around 20-22% once commenced. Keeping wood below this threshold moisture content is therefore essential if risk of decay is to be avoided and also bringing the moisture content down to below this level will stop further growth of the fungus leading to it dying out over time.
The term ‘dry rot’ is somewhat misleading since moisture is still required for a dry rot infection to both commence and to be sustained, thriving best at around the 30-40% moisture content. Wet rots on the other hand as one would expect do better at higher moisture contents of around 45-60%. Both wet and dry rots have an optimum temperature for growth of 20-22ºC but sustained exposure to higher temperatures at or above 40ºC will usually kill them off.
Chemicals that are strong acidic or caustic can severely attack wood and cause it to swell and become fibrous. On the whole softwoods are surprisingly more resistant to chemical attack than hardwoods but both have been known to suffer attack through exposure to aggressive chemicals.
Anyway school lesson over and back to the build, this month we were treated by Darren Spinage, of Trend Machinery & Cutting Tools Ltd, one of our product sponsors, to some of their superb pieces of kit in support of our venture. From breathing masks, to saw blades, countersink drills and router bits, Trend really have done us proud and we are so lucky to have them on board given their products really are the best you can get.
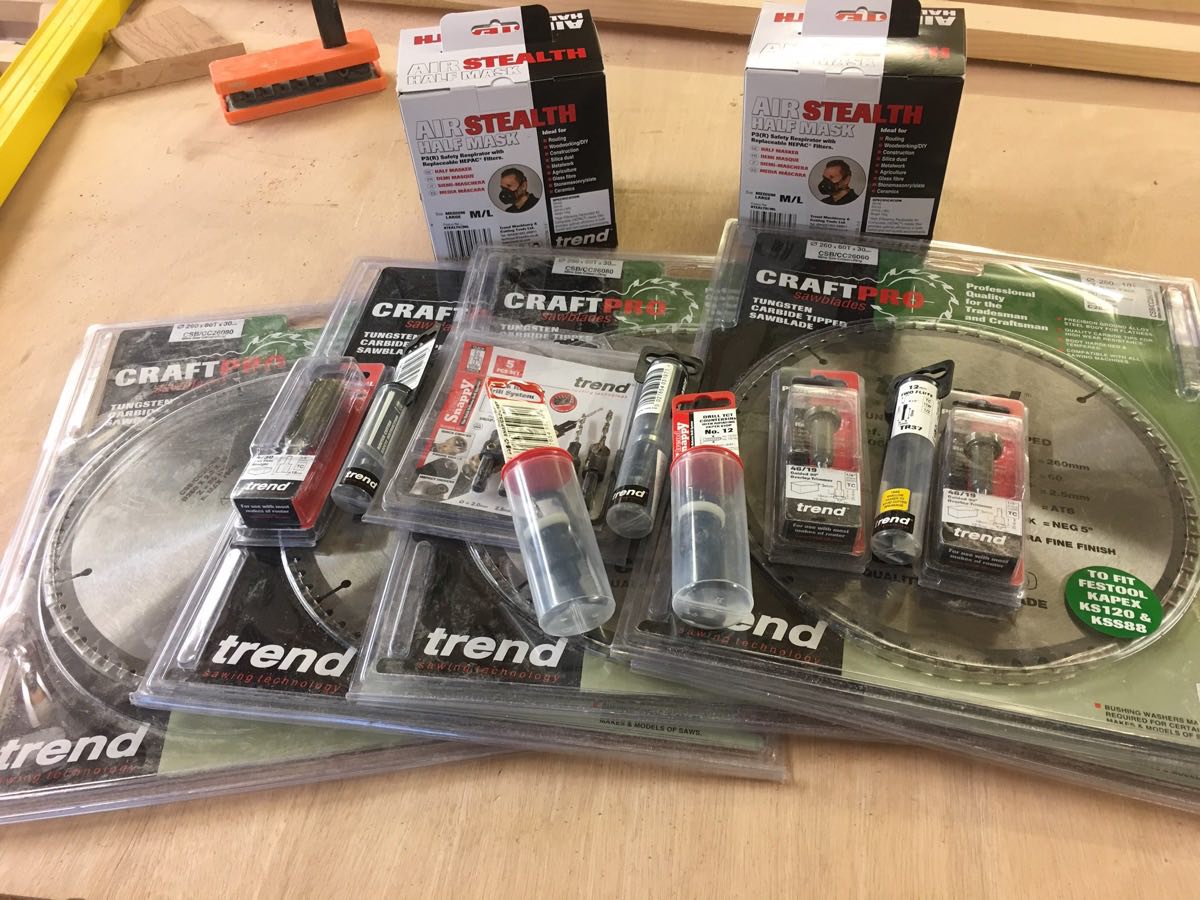
Likewise Frank Canfield, Managing Director of Avon Stainless Fasteners, has been so very generous in supplying us all the marine grade stainless steel fixings for the hull of our jet hydroplane Longbow. Anything we have specified to date by way of screws, nuts bolts washers, etc his Company have gone out of their way to provide and get it delivered to us as fast as possible.
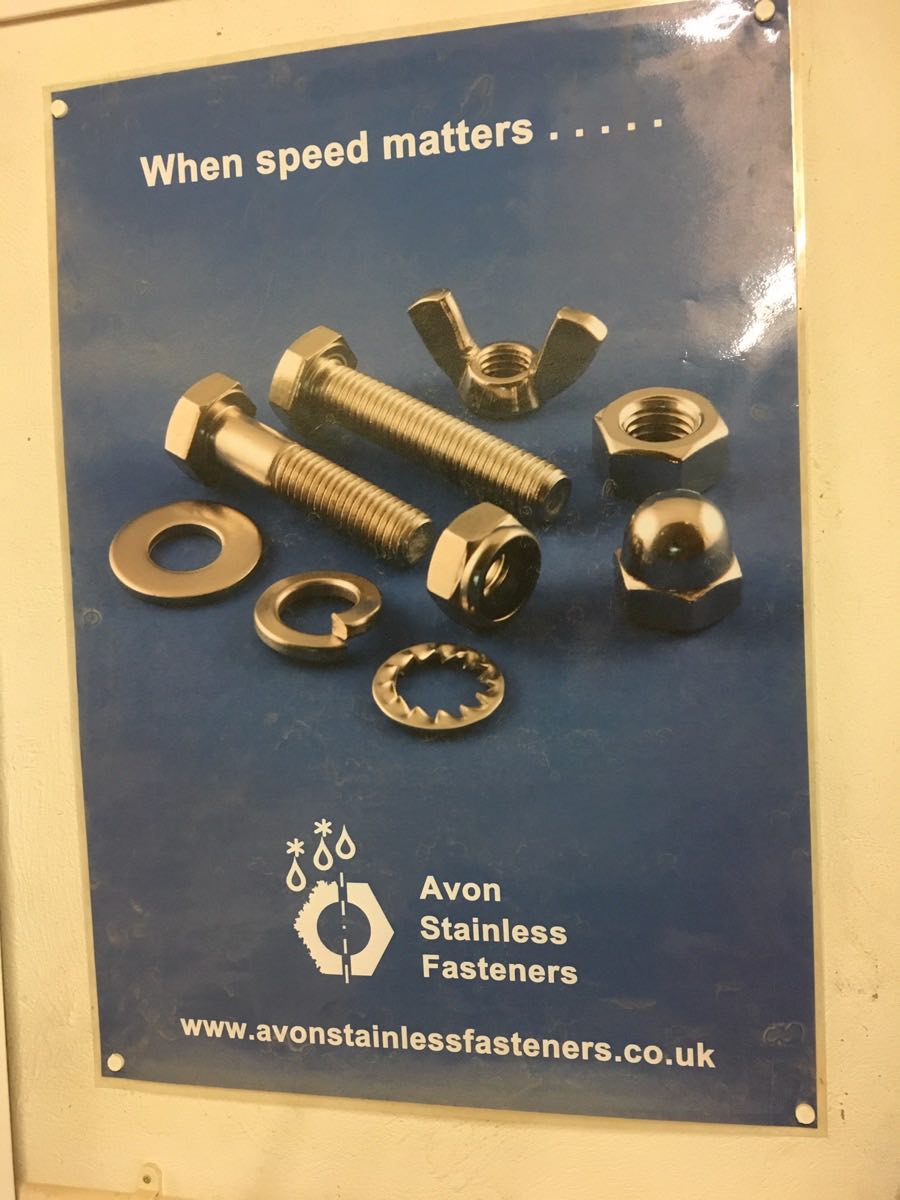
You may recall from last month’s diary update that we showed you how we had traditionally steam bent the sections of timber generously supplied by Robbins that were required to date in forming the hull. Once we were satisfied by sample metering over time that these wooden sections had dried down to an acceptable level after steaming, they could then be laminated using the West System Epoxy System kindly supplied by Wessex Resins, shown as follows.
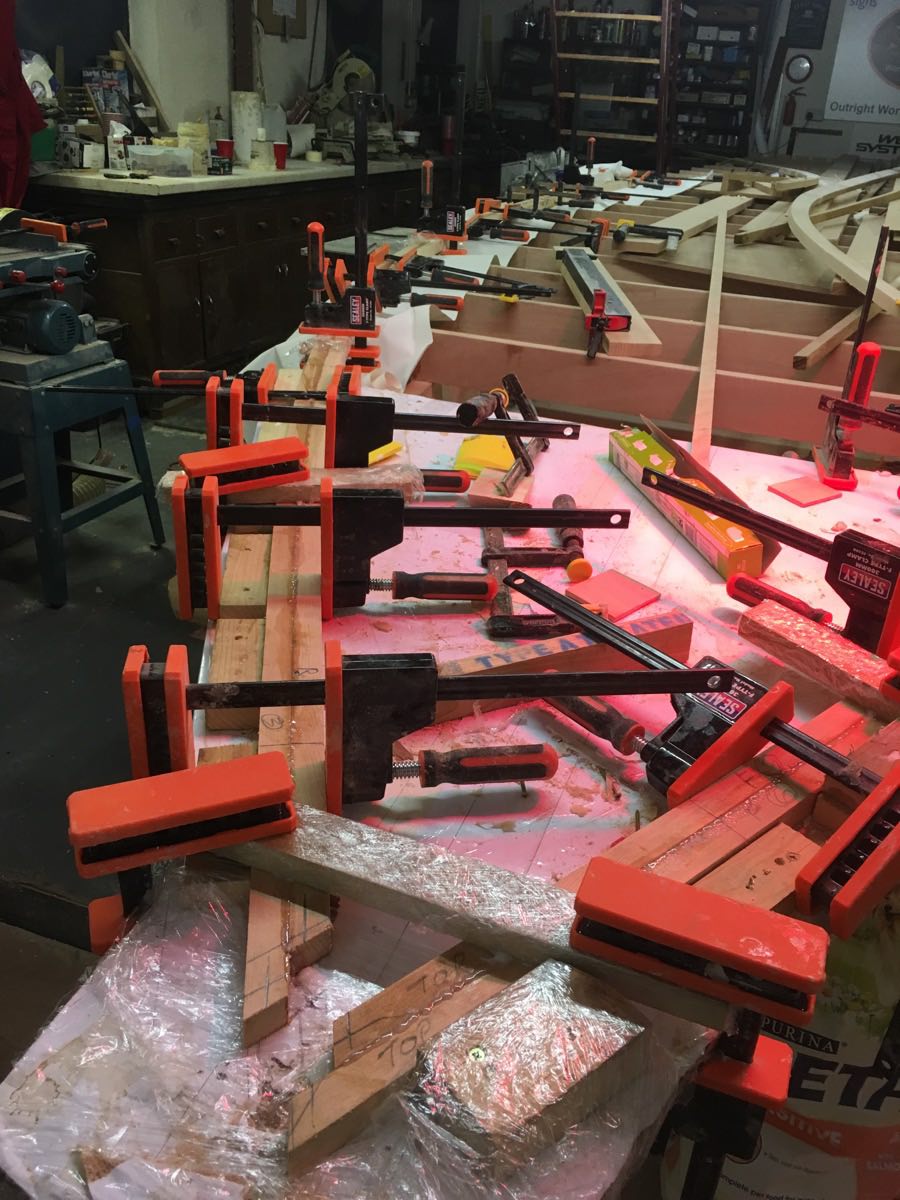
Once this phase was complete it allowed us to set the keel in place with screws and epoxy then, to make a start on setting out the longitudinal battens that will run alongside the keel from bow to transom. If you are new to visiting the website what you are looking at is the hull of Longbow being built upside down at this stage:
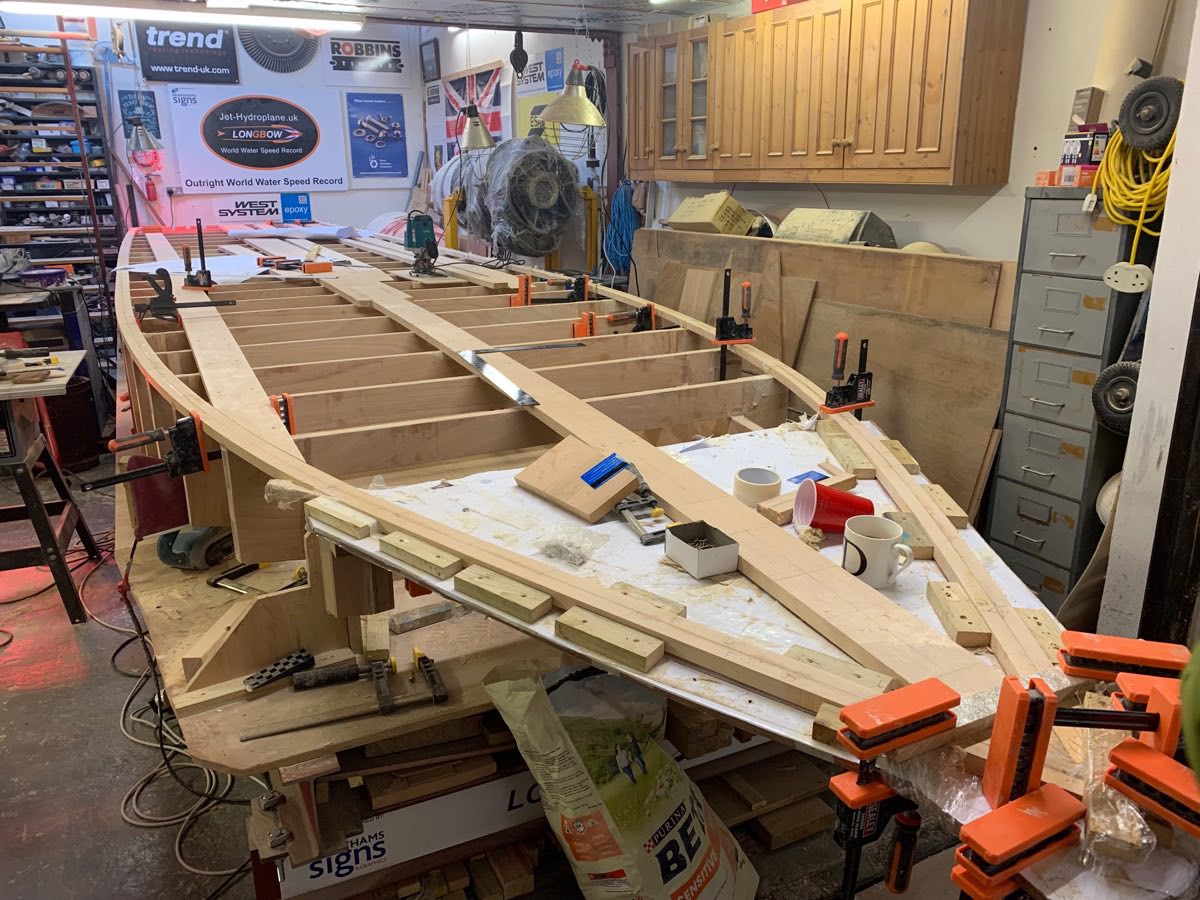
The outer rails and keel really start to define the shape of the hull of Longbow and it was great to see her starting to come together as a defined shape. We would show you more but having set aside a good deal of this month’s update to discuss issues that we have to be mindful of when constructing a wooden hull, we have decided to leave it there until next month to reveal the next stage of the build. We hope that next time you see a piece of furniture with woodworm in it, or are replacing that rotten gate, perhaps you will remember reading about these issues on here.
In next month’s update we intend to report back on our good friend Dave Warby and his team in Australia, with how they progress with their latest round of tests at Taree of their jet hydroplane Spirit of Australia II, for which we wish them better weather this time around.
Thank you for tuning in as the nights get lighter with the clocks changing and spring is finally here in the UK. If we have not bored you too much with wittering on about wood, then please drop by next month to see how we got on with the next stage of the build.